La continua riduzione della dimensione dei dispositivi medici sta riportando in auge il processo di microstampaggio a iniezione. Tre mercati ad alto volume stanno creando una domanda crescente di componenti microstampati:
- Con l’invecchiamento della popolazione, aumentano i problemi associati alla degenerazione maculare, al glaucoma e alla cataratta. Queste procedure richiedono parti e dispositivi a parete sottile e superficie a elevata finitura per migliorare il comfort del paziente.
- La chirurgia mininvasiva richiede dispositivi di precisione che possano viaggiare attraverso o all’estremità di un filo guida.
- I dispositivi di monitoraggio del glucosio per la gestione del diabete e i meccanismi di pompaggio, gli aghi e le cannule senz’ago sono molto richiesti e anch’essi devono avere pareti sottili per il comfort del paziente.
Secondo un recente rapporto di Research and Markets, il mercato globale del microstampaggio dovrebbe passare da 904 milioni di dollari nel 2020 a 1,6 miliardi di dollari entro il 2025, con un tasso di crescita annuale composto (CAGR) dell’11,8%. In questo articolo, pubblicato a pag. 36 della rivista Plastix di maggio 2023, si cercherà di fare un po’ di chiarezza sul concetto di microstampaggio, sulle sfide che pone e sulle soluzioni tecnologiche disponibili.
Cos’è il microstampaggio a iniezione?
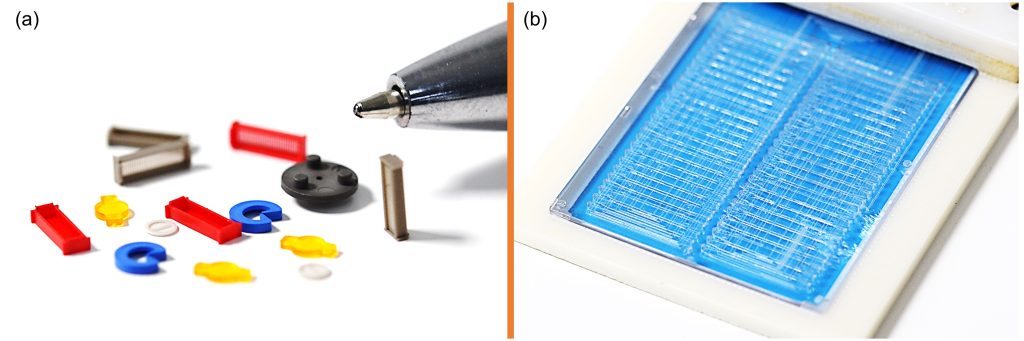
La definizione precisa di un pezzo microstampato è ancora controversa. Per essere definito micro, un pezzo deve presentare una o più delle seguenti caratteristiche:
- pesa meno di 1 g o è una frazione di un granulo (figura 1a);
- è una parte con regioni microstrutturate o, più specificamente, con pareti di spessore inferiore a 300 μm. Il dispositivo microfluidico riportato in figura 1b presenta decine di canali larghi soli 150 μm.
- è un pezzo di microprecisione, cioè un pezzo che può avere qualsiasi dimensione, ma con tolleranze nell’ordine dei micrometri, o più precisamente tra 1 e 5 μm.
Per avere un’idea delle dimensioni di cui stiamo parlando si consideri che lo spessore di un capello è di circa 75 μm.
Il microstampaggio non è semplicemente l’applicazione del processo convenzionale di stampaggio a iniezione alla produzione di pezzi molto piccoli. Il passaggio dal livello macro a quello micro comporta numerose considerazioni, dalla progettazione dei componenti alla lavorazione dello stampo, fino alla scelta dei sistemi di stampaggio e assemblaggio.
Con tolleranze inferiori ai 10 μm, per validare il processo produttivo con Cpk = 1,33 è necessario lavorare su tutti i sottoprocessi che possono influire sulla precisione. La pratica industriale mostra che i tre fattori più critici sono: la progettazione e la lavorazione dello stampo; la valutazione della ripetibilità e della riproducibilità degli strumenti di misura; la precisione del sistema di stampaggio a iniezione. Un contributo minore può essere dato dalla variabilità del materiale polimerico e del processo di essiccazione.
Lo stampo
Anche il peso di ciascun fattore può variare a seconda del componente da stampare ed è importante considerare l’errore percentuale di tolleranza in ogni singola fase del processo. In particolare, si consiglia di costruire lo stampo con un errore inferiore al 20% della tolleranza per lasciare l’80% alle altre variabili indicate e mantenere una buona finestra di processo. Per esempio, con tolleranze sul microcomponente di ±10 μm, le tolleranze delle lavorazioni dello stampo devono essere di ±2 μm. È chiaro, quindi, come la capacità di realizzare microstampi sia il principale fattore abilitante e rappresenti la barriera da superare per l’ingresso in questo mercato.
Per realizzare “feature” micrometriche (ad es.: cave da 30 μm, o perni con diametro di 50 μm) e sfiati adeguati (ad es. sul fondo di una cavità per microaghi), è necessario disporre di tecnologie di lavorazione per asportazione con precisione submicrometrica: la combinazione di fresatura ultraprecisa e micro-EDM permette di ottenere la maggior parte delle geometrie richieste direttamente su stampi in acciaio. Perni e anime devono essere vincolati a entrambe le estremità e questo è possibile solo se si garantisce un allineamento estremamente preciso in fase di chiusura e la corretta termostatazione dello stampo.
Gli stampi presentano dimensioni molto ridotte (figura 2) e si caratterizzano per il fatto di avere solitamente: un sistema di centraggio su inserti liberi di ruotare, un sistema di riscaldamento elettrico (il circuito di raffreddamento è necessario solo per componenti macro con superfici microstrutturate) e una configurazione che permette all’ugello del cilindro d’iniezione di arrivare direttamente sul piano di partizione, per minimizzare il volume dei canali d’alimentazione.
I parametri di stampaggio
Nel corso del processo di microstampaggio, le criticità maggiori sono rappresentate dalla replicazione delle microfeature e dalla preservazione della loro integrità durante l’estrazione. Gli spessori estremamente ridotti impongono un raffreddamento immediato del fuso polimerico. Per garantire la completa replicazione della geometria della cavità, la temperatura dello stampo e la velocità d’iniezione devono essere impostate a valori molto superiori rispetto a quelli utilizzati nello stampaggio convenzionale. La temperatura elevata dello stampo non va comunque a pesare sul tempo ciclo, dato che per questi spessori il tempo di raffreddamento è comunque vincolato dalla fase di plastificazione.
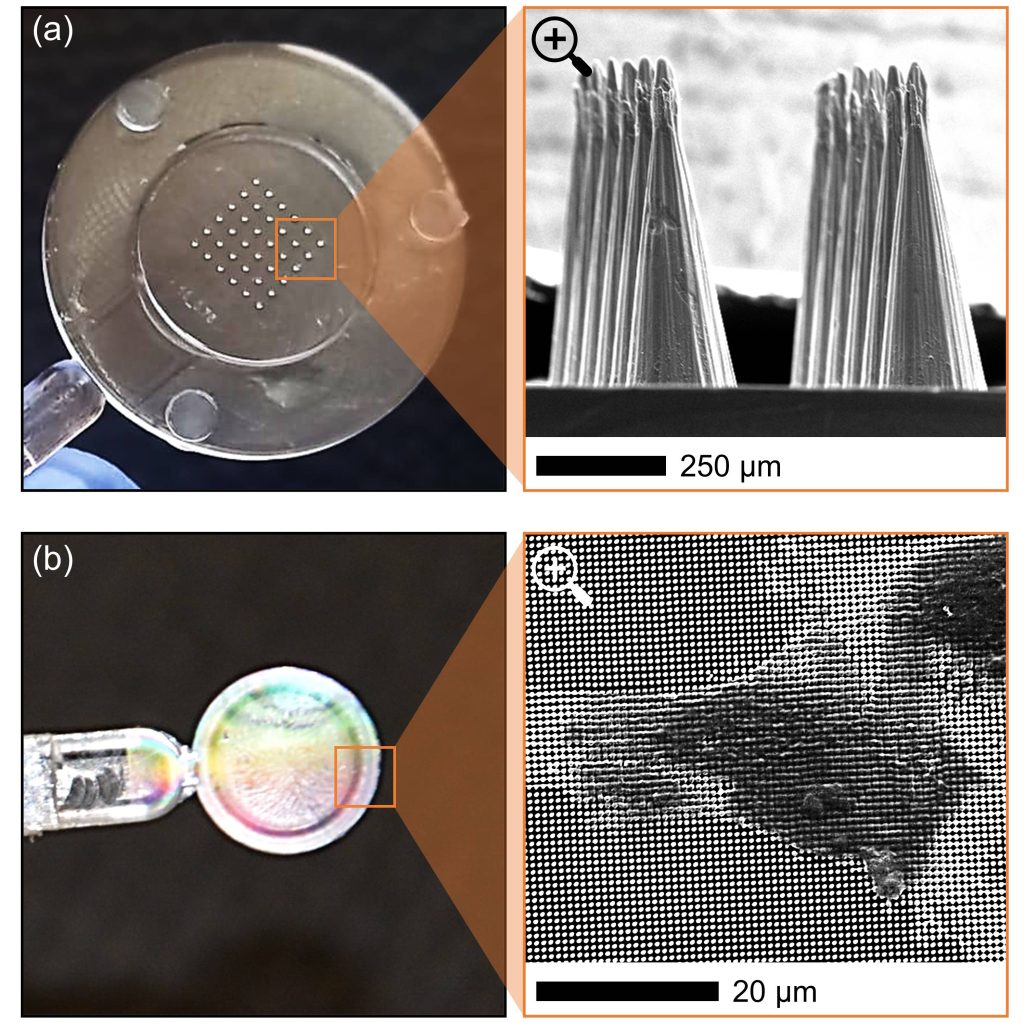
Nel caso di componenti macro con superfici microstrutturate, come per esempio la matrice di microaghi di figura 3a e la superficie a nanopilastri di figura 3b, particolare attenzione deve essere posta anche al posizionamento del punto d’iniezione per evitare il fenomeno dell’esitazione: il fuso polimerico tende a riempire prima la parete principale e solo successivamente le feature secondarie. Questo ritardo (esitazione) causa il raffreddamento del fuso all’imbocco delle microfeature superficiali e una conseguente parziale replicazione.
La scelta del polimero è guidata anche dalla necessità di garantire la replicazione sfruttando bassi valori di viscosità e un marcato comportamento pseudoplastico (la viscosità si riduce significativamente con il gradiente di velocità). Il passaggio attraverso punti d’iniezione con diametro di 0,1-0,3 mm comporta una deformazione a taglio molto elevata che, se da un lato è benefica perché riduce la viscosità, dall’altro tende a modificare le proprietà meccaniche del polimero e l’anisotropia di ritiro. Per questo motivo, alcuni specialisti del microstampaggio testano preventivamente i materiali stampando microprovini per prove a trazione, con cui valutano le proprietà meccaniche e i coefficienti di ritiro specifici per questa scala e diversi da quelli riportati sulle schede tecniche dei materiali.
Microstrutture con elevato rapporto d’aspetto (cioè con altezza superiore al diametro di base) possono essere realizzate, ma particolare cura dev’essere posta nel garantire la loro integrità durante l’estrazione. L’angolo di sformo e la finitura superficiale sono i fattori critici su cui lavorare per evitare che una completa replicazione delle microstrutture si traduca in un’elevata adesione alle pareti della cavità. A complicare questo compito contribuisce la difficoltà di posizionamento dei microestrattori.
Sistemi dedicati per il microstampaggio a iniezione
La scelta di un sistema dedicato è essenziale per la riuscita di un progetto di microstampaggio. La soluzione tecnologica adottata dalla maggior parte dei costruttori di presse consiste nel disaccoppiare le fasi di plastificazione e dosaggio da quella d’iniezione. Una vite di plastificazione in grado di essere alimentata con granuli standard e plastificare efficacemente può essere ridotta fino a un diametro di 14 mm. Se venisse impiegata anche per iniettare il polimero in cavità ad alta velocità, un errore di posizione, un ritardo nella chiusura della valvola di non ritorno o l’inerzia stessa della vite (che ne pregiudica la performance in accelerazione e frenata) si tradurrebbe in una variazione del volume iniettato fuori tolleranza. In altre parole, comporterebbe formazione di bava, o incompleta replicazione della cavità. Il disaccoppiamento implementato nei sistemi di microstampaggio dedicati (figura 4) permette di plastificare efficacemente utilizzando una vite adeguata e d’iniettare a elevate velocità sfruttando la bassa inerzia e l’elevata precisione posizionale di un sistema a pistone.
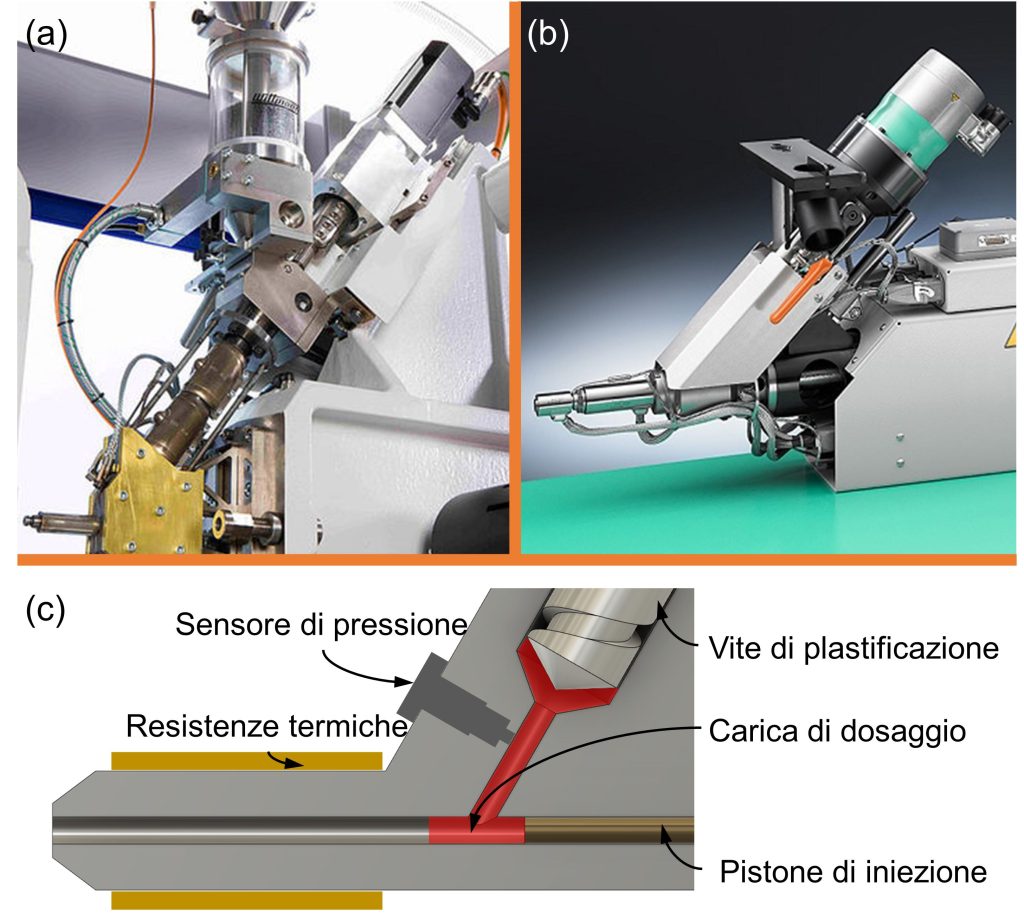
Alcuni stampatori hanno cercato di risolvere questo problema aumentando il numero di cavità e allargando il diametro dei canali d’alimentazione, in modo da poter utilizzare una pressa convenzionale ed essere comunque in grado di controllare il volume d’iniezione. Questa soluzione è tutt’altro che ideale ed estremamente costosa, perché non solo si spreca più materiale (ad ogni stampata il volume della materozza può essere 100 volte più grande di quello delle parti stampate), ma si allungano anche i tempi di ciclo. Inoltre, non risolve il problema della degradazione del polimero dovuto a elevati tempi di residenza nel cilindro.
Nuovi sviluppi
La stampa 3D è sempre più utilizzata per supportare lo sviluppo di dispositivi medici miniaturizzati. I più avanzati sistemi di fotopolimerizzazione sono in grado di garantire tolleranze di 1 micrometro e finiture superficiali inferiori, con Sa<1 μm. La fotolitografia laser a due fotoni può scendere di un altro ordine di grandezza e prototipare microcomponenti come le matrici di microaghi mostrate in figura 5.
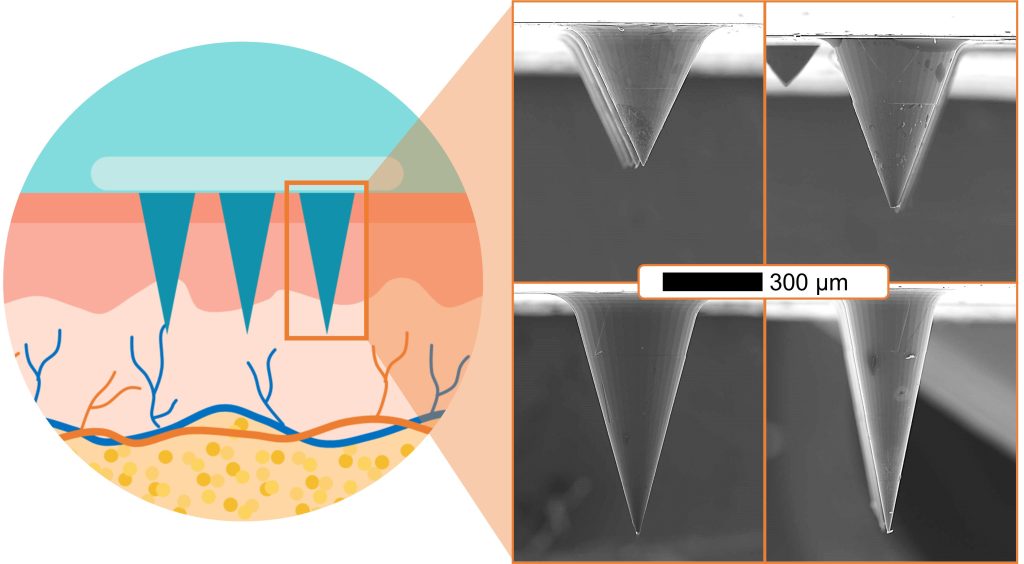
Anche se lo stampaggio a iniezione e la stampa 3D vengono talvolta presentati come tecnologie rivali, è evidente che in realtà sono complementari: il microstampaggio è una soluzione molto scalabile per i dispositivi prodotti in grandi volumi, ma se è necessario disporre di parti in tempi rapidi, o se il cliente richiede più iterazioni di progettazione (ad esempio, i microaghi con diversa angolazione mostrati in figura 5), la microstampa 3D può essere vantaggiosa. Il recente sviluppo di fotopolimeri avanzati, che mantengono un’elevata resistenza anche ad alte temperature, consente di stampare direttamente inserti per microstampi per prototipare i microcomponenti con il polimero termoplastico definitivo (ad es., polimeri bioriassorbibili per impianti). Modificare la geometria dei pezzi, o mettere a punto un progetto ed essere in grado di iterarlo dopo appena un giorno è un enorme vantaggio per la tempistica degli studi clinici. Questi prototipi di parti e inserti stampo apriranno la strada a tempi più rapidi per le sperimentazioni cliniche, mediche e farmaceutiche.
Infine, un’altra tecnologia che si sta rivelando di grande utilità nello sviluppo di microcomponenti stampati a iniezione è la microtomografia computerizzata di assorbimento dei raggi X (X-ray microCT). Si tratta di una tecnica di imaging tridimensionale che consente d’indagare la geometria esterna e interna di un componente in maniera non distruttiva e con risoluzione submicrometrica. In pochi minuti di scansione è possibile rilevare tutte le variazioni negli attributi cruciali per la qualità in funzione dei parametri di processo utilizzati e definire così la finestra ottimale di stampaggio.
Giovanni Lucchetta e Marco Sorgato (Università degli Studi di Padova)