La società austriaca Engel è stata una delle prime del settore materie plastiche a scegliere la Cina come sede produttiva e commerciale ed è stata la prima azienda costruttrice europea di presse a iniezione ad aprire uno stabilimento a Shanghai, quasi vent’anni fa. Dopo il lancio del marchio Wintec, adattato alle esigenze del mercato asiatico, nel 2014 l’azienda ha aperto un secondo stabilimento a Changzhou. Da allora, con il marchio Wintec, sono state vendute più di mille macchine a due piani della serie t-win.
In occasione della fiera Chinaplas (Shanghai, 23-26 aprile 2024) Engel ha deciso di ampliare ulteriormente il portafoglio Wintec, aggiungendo la nuova serie t-win SE di modelli a due piani. Inoltre, il lancio della serie e-win vede l’ingresso sul mercato della prima gamma di modelli Wintec completamente elettrici.
Questo è un esempio di come il duplice orientamento dell’azienda, collaudato da anni, stia dando i suoi frutti. Da un lato, infatti, c’è lo sguardo rivolto ai mercati locali: la produzione avviene all’interno della medesima regione asiatica e con la competenza locale nello sviluppo e nella produzione; dall’altro lato Engel offre standard di qualità uniformi, servendo il mondo intero, indipendentemente da dove il cliente acquista la macchina.
“Stiamo portando avanti la nostra filosofia di fornire soluzioni sia locali che globali e attualmente stiamo creando la struttura per un hub globale”, afferma Stefan Engleder, CEO del Gruppo Engel. Ciò significa che ciascuna delle tre regioni coperte dal gruppo – Americhe, Europa e Asia – è composta da unità largamente indipendenti, ciascuna delle quali si occupa di vendite, elaborazione degli ordini, produzione e assistenza post vendita. Ognuno di questi tre hub è in stretto contatto con la sede centrale al fine di stabilire e implementare standard globali, ove richiesto e opportuno. Ciò crea le condizioni ideali per servire il mercato asiatico anche in futuro.
Una nuova macchina a due piani per il mercato asiatico
Con più di 1000 unità vendute, t-win SE è l’ultimo modello aggiunto alla serie di presse a due piani ed è stato creato appositamente per soddisfare le esigenze dei mercati asiatici. “Con la t-win SE come nuova macchina base e la serie Engel duo per le applicazioni più impegnative, ora possiamo coprire tutti i livelli di complessità applicativa nella regione asiatica con le nostre presse a iniezione a due piani”, prosegue Engleder. Lo sviluppo e la produzione della t-win SE hanno luogo a Changzhou. Inizialmente, per i clienti asiatici saranno disponibili i modelli da 6500, 10500 e 18000 kN.
Presso lo stand C42, nel padiglione 5.1 di Chinaplas, una nuova Wintec t-win SE 6500-2310 mostra un’efficiente soluzione di sistema per la produzione di cornici per fari fendinebbia in polipropilene. I materiali vengono iniettati in uno stampo a due cavità realizzato da uno stampista locale e prelevati da un robot cartesiano Wintec α-win.
Oltre alla t-win SE, anche la serie e-win completamente elettrica festeggia la sua prima apparizione a Chinaplas.
Parti ottiche di precisione
Tre ulteriori sistemi in mostra vedono l’azienda affrontare il settore in forte espansione della mobilità cinese. In linea con il passaggio in atto dai motori a combustione interna alle trasmissioni elettriche, la classica griglia del radiatore è diventata obsoleta come principale elemento di definizione dell’identità per i marchi automobilistici. Infatti, questo ruolo è ora svolto sempre di più dai “fari firmati”. Le guide luminose necessarie a questo scopo devono essere prodotte con grande cura e precisione per evitare irregolarità o impurità nella massa fusa, che possono compromettere la qualità ottica richiesta.
La pressa Engel Victory 120 senza colonne, in combinazione con il processo optimelt, sfrutta appieno i suoi punti di forza in questa applicazione: i componenti per la plastificazione del PMMA, sviluppati e prodotti internamente, consentono una lavorazione delicata della massa fusa, prevenendo eventuali ingiallimenti o bruciature.
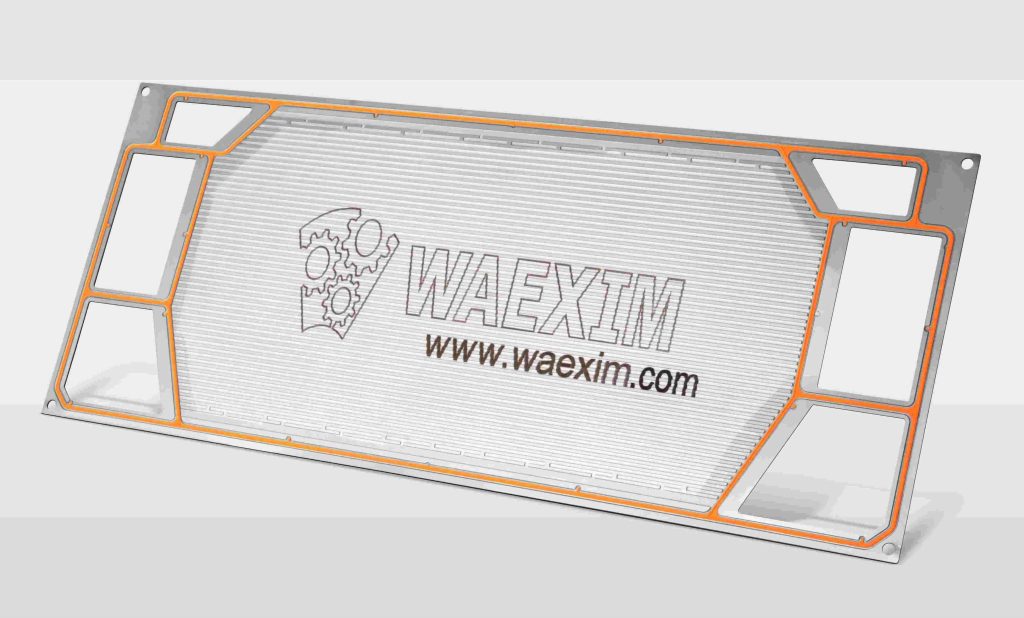
L’unità di chiusura senza colonne supporta lo stampaggio preciso di pezzi lunghi e sottili, grazie alla distribuzione particolarmente omogenea della forza di chiusura. Tutto ciò rende questa macchina ideale per la produzione di guide luminose particolarmente lunghe e con qualità ottica elevata. Ulteriori vantaggi: la struttura senza colonne consente di utilizzare anche stampi molto grandi su presse a iniezione relativamente piccole. Infatti, la victory esposta ha una forza di chiusura di soli 1200 kN, mentre una macchina con colonne necessiterebbe di una forza di chiusura notevolmente maggiore, a causa dello spazio richiesto per lo stampo.
Pezzi in composito per la mobilità del futuro
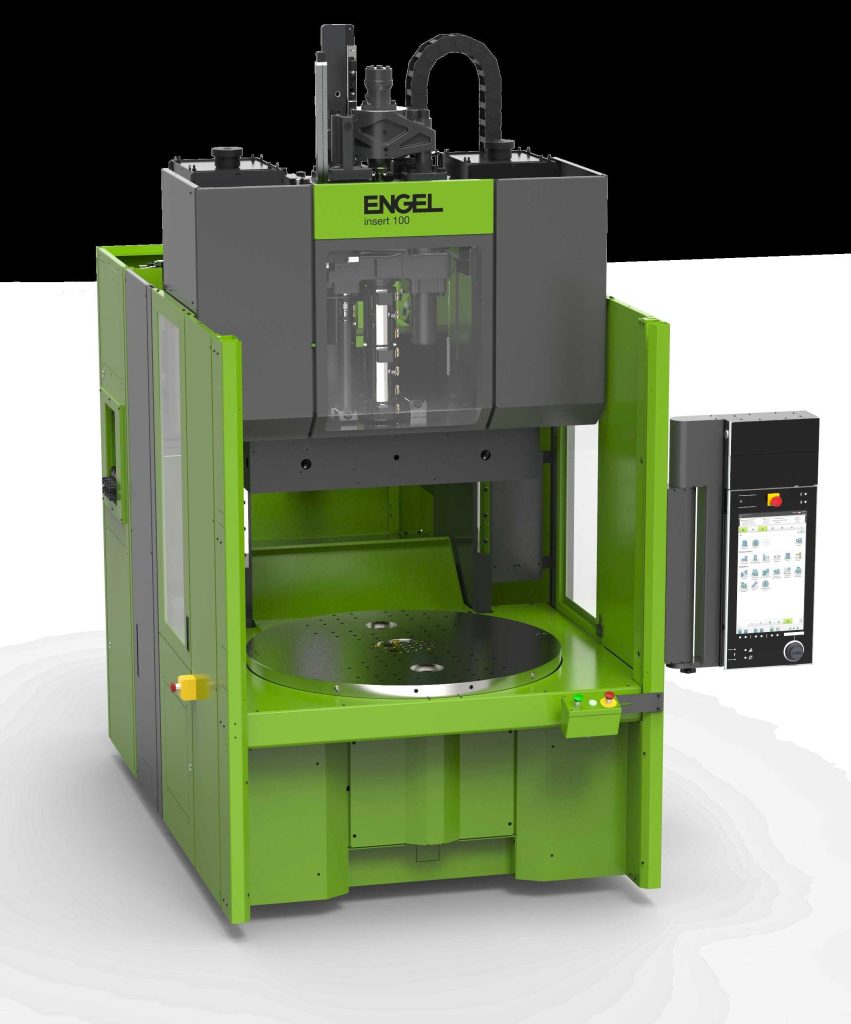
La terza applicazione in mostra, per il settore automobilistico, si basa su una pressa a iniezione verticale della serie Insert. La insert 100 è infatti utilizzata per produrre, in una sola fase di lavoro, piastre bipolari per celle a combustibile con guarnizione in silicone.
L’ingombro particolarmente ridotto della pressa verticale e la sua area di lavoro ergonomica garantiscono una produzione efficiente di parti complesse in materiali compositi.
I precisi azionamenti servoidraulici della serie insert semplificano il sovrastampaggio con geometrie complesse e la funzionalizzazione delle parti, anche con materiali difficili da processare.
L’area dello stampo, facilmente accessibile, consente inoltre una semplice integrazione dell’automazione a monte e a valle. Per la movimentazione dei pezzi viene utilizzato un robot Engel easix a 6 assi.
Tecnologie green per la logistica
Engel porta avanti costantemente gli sviluppi per un’economia circolare e il processo skinmelt rappresenta un ottimo esempio di questa attività. Consente infatti l’uso di materiale riciclato in un’ampia gamma di prodotti in plastica, senza dover scendere a compromessi per ciò che concerne la qualità ottica o meccanica dei pezzi.
Alla fiera Chinaplas, il costruttore austriaco dimostra come il processo skinmelt renda possibile produrre contenitori da trasporto con un’elevata percentuale di riciclato post consumo (PCR). Il materiale riciclato è nascosto nello strato interno (core) di questo box per la logistica, completamente incapsulato da materiale vergine. Dall’esterno i clienti finali non riusciranno a distinguere le differenza tra questo e un contenitore realizzato interamente con materiale vergine.
Il contenuto di materiale riciclato può superare il 50% del totale. L’intero processo può essere controllato facilmente dall’unità di controllo CC300. Quest’applicazione si basa sulla macchina duo 700 a due piani, attrezzata con un robot cartesiano viper 40 che si occupa della movimentazione dei pezzi. La funzione iQ weight control garantisce una plastificazione e un’iniezione sicure del materiale riciclato, monitorando il peso della stampata in tempo reale e compensando le fluttuazioni nelle proprietà del materiale in modo completamente automatizzato. Ciò garantisce un riempimento affidabile e costante della cavità.
Efficienza, precisione e ingombro ridotto per le camere bianche
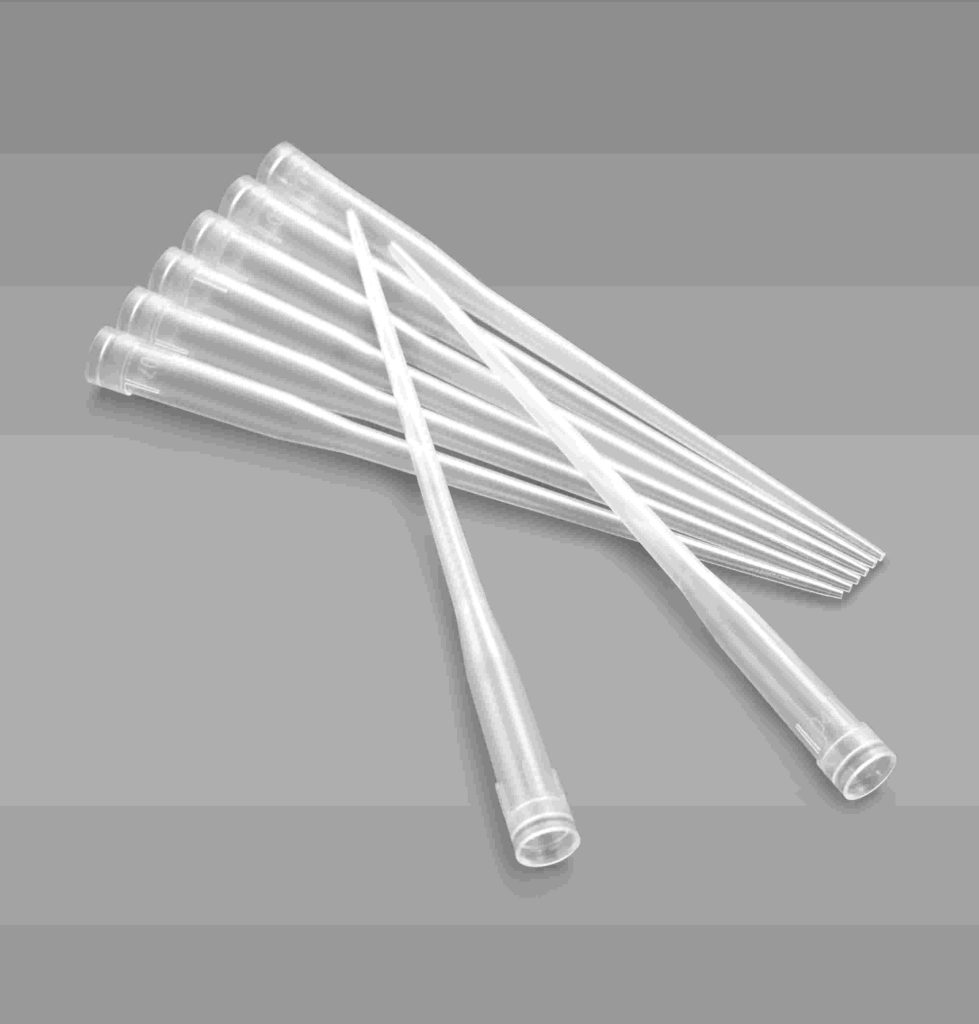
La serie completamente elettrica e-mac di Engel si caratterizza in particolare per il suo ingombro ridotto.
Grazie al nuovo pacchetto per camere bianche disponibile opzionalmente per le e-mac, anche i produttori del settore medicale possono ora beneficiare di una maggiore produttività per unità di superficie.
Presso lo stand in fiera, i puntali per pipette in PP vengono prodotti su un Engel e-mac 100, utilizzando uno stampo a otto cavità dello stampista cinese Cartisan.
La precisione degli azionamenti servoelettrici rappresenta un altro vantaggio, oltre alle dimensioni compatte.
Consentono la produzione di “sfidanti” componenti filigranati, come questi puntali per pipette, con un consumo minimo di energia.