Le ultime acquisizioni nel comparto della componentistica auto rivelano un comparto sempre più concentrato e competitivo. Grandi gruppi si dividono il mercato, producendo pezzi e assemblati per le principali case automobilistiche, investendo decine di milioni di euro nella ricerca e delocalizzando gli impianti produttivi in un’ottica globale. Nonostante ciò, in Europa – e soprattutto in Italia – esiste una fiorente industria dei componenti in plastica che, pur mantenendo dimensioni contenute nell’ambito di una media industria nazionale, riesce a restare competitiva. E lo fa puntando su flessibilità , creatività e capacità di innovare i processi, migliorandoli in modo incrementale. Un esempio è la campana SAPA, fondata e ancora oggi guidata dalla famiglia Affinita, che attraverso una crescita strategica per acquisizioni si è trasformata da terzista a Tier One di case automobilistiche di primo piano come, FCA, Volkswagen, CNH, Porsche e Ferrari.
Da subfornitori a Tier One
«Il punto di svolta è stato l’acquisizione di Lucchesi, perché ci ha permesso di stingere con il cliente finale un rapporto più organico» spiega Giovanni Affinita, Sales Strategist e membro del consiglio d’amministrazione di SAPA. «Come corollario, abbiamo dovuto sviluppare internamente attività di ricerca e sviluppo, che prima non eravamo tenuti a fornire. Non potendo competere con i grandi gruppi nella ricerca di base, ci siamo concentrati sull’innovazione di processo verticale, ottimizzando i prodotti e i processi di produzione con l’obiettivo di ridurre i tempi, i costi e migliorare al contempo la qualità , focalizzandoci nelle aree dove possediamo le migliori competenze». Un approccio che possiamo sintetizzare in una frase: individuare margini di miglioramento nei processi di produzione esistenti e attuarli con investimenti sostenibili, anche per una media impresa industriale come la nostra.
Una ricetta semplice, almeno in apparenza… Può fornirci qualche esempio di questo approccio alla ricerca e sviluppo?
Nel nostro reparto di ricerca – che non a caso abbiamo battezzato “Ingegneria dell’innovazione” – puntiamo a migliorare le tecnologie esistenti nel campo dello stampaggio a iniezione. Un esempio concreto è la tecnologia One-shot, inizialmente messa a punto per lo stampaggio di cover motore, frutto di un ripensamento complessivo dell’intera fase di produzione, con l’obiettivo di semplificarla e abbreviarla.
Una cover è costituita da tre elementi principali: un guscio in materiale termoplastico, un elemento decorativo superiore e un isolamento termoacustico in schiuma poliuretanica o melamminica rivolto verso la testata del motore. Nei processi tradizionali, i tre pezzi vengono prodotti separatamente, in altrettante isole, e quindi assemblati. Con l’approccio One-shot siamo riusciti a stampare il componente completo in un’unica fase, combinando nella stessa isola lo stampaggio a iniezione e la schiumatura poliuretanica. Ciò ha consentito di ridurre del 30 per cento i tempi complessivi di produzione, portandoli a 50-75 secondi in funzione della dimensione e complessità del pezzo.
Avete coinvolto dei partner nel processo di ricerca e sviluppo?
L’idea è nostra, come il brevetto, ma abbiamo trovato dei partner competenti nel gruppo chimico BASF, per lo sviluppo e la fornitura delle materie prime poliuretaniche, e nel costruttore italiano Cannon, per quanto concerne le tecnologie di schiumatura. Grazie a questa partnership a tre siamo riusciti a estrarre più valore dagli impianti di stampaggio, aumentando la produttività e riducendo i costi tra il 10 e il 20 per cento rispetto al processo convenzionale. Non meno importante, abbiamo ottenuto una cover di qualità più elevata, poiché abbiamo eliminato dal processo una serie di operazioni manuali – soggette a errori – sostituendole con un processo automatizzato e altamente ripetibile.
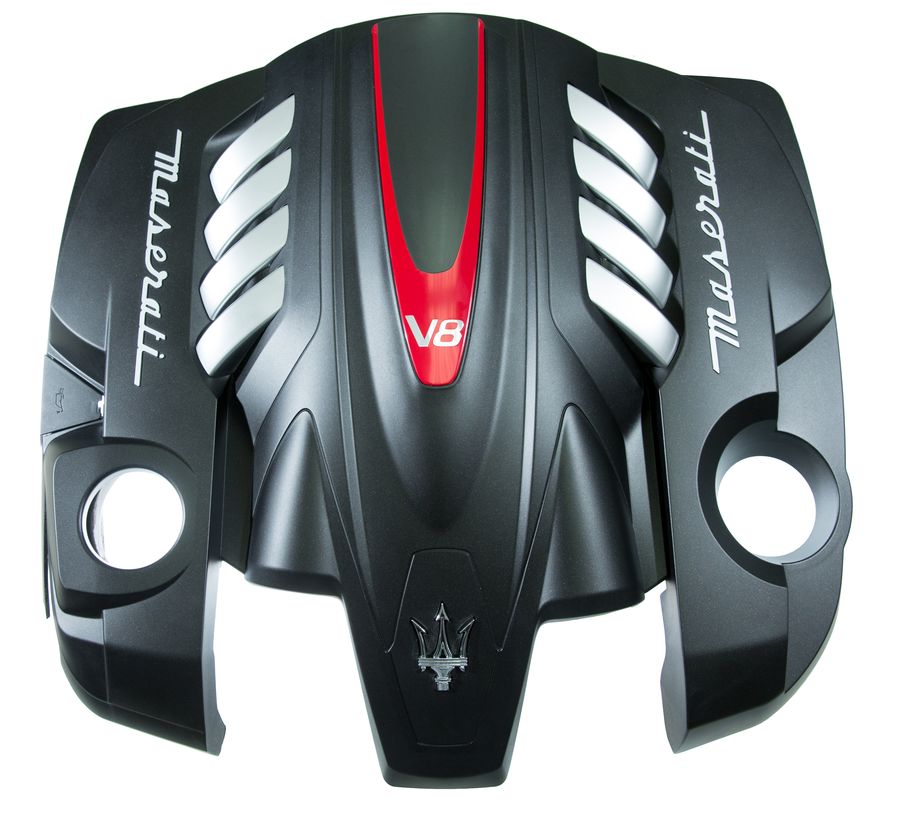
Avete individuato ulteriori sviluppi di questo processo?
Stiamo cercando di integrare nel pezzo anche altri componenti, come i gommini. Ma stiamo testando la tecnica One-shot anche nella produzione di interni auto, soprattutto in vista del futuro sviluppo dei veicoli elettrici, dove il tema della coibentazione è molto sentito, poiché per riscaldare l’abitacolo si utilizza l’energia elettrica delle batterie e ciò riduce l’autonomia. La tecnica di sovrastampaggo e schiumatura può essere utilizzata, ad esempio, per stampare pannelli in resina termoplastica retroschiumata, al contempo isolanti e leggeri, due elementi critici per il successo della mobilità elettrica.
Siete entrati nella rosa dei finalisti del premio sull’innovazione assegnato da SPE in occasione dell’Automotive TPO Conference. Con quale processo eravate in concorso?
Si tratta di un’altra innovazione di tipo incrementale, Injection Gas Venting, che non rivoluziona il processo di stampaggio, ma apporta benefici in termini di riduzione del numero di elementi, quindi operazioni, impegno di macchine e tempi di ciclo. In sostanza è un processo di stampaggio assistito da gas e aria compressa, che consente di produrre pezzi più leggeri e resistenti, anche di forma complessa, integrando diverse funzioni. Lo abbiamo sperimentato con successo per realizzare la cornice del lunotto posteriore di un modello Volkswagen, prodotta in TPO rinforzato talco, passando da tre elementi a un unico pezzo. La cornice ora è più leggera (pesa l’8 per cento in meno di quella tradizionale) e al tempo stesso più rigida, evitando così i rischi di deformazione. Un altro importante traguardo è un risparmio nei costi di produzione intorno al 10 per cento. Per ottenere questo risultato, insieme alla resina, viene iniettato prima azoto e quindi aria compressa che agevola il riempimento delle cavità dello stampo.
Digitalizzazione dei processi di stampaggio, un altro tema di attualitĂ . A che punto siete?
Stiamo procedendo verso Industria 4.0 con il progetto Wiki, avviato alla fine dell’anno scorso. L’obiettivo è introdurre l’intelligenza artificiale nei reparti di stampaggio mettendo in connessione tutte le macchine – presse e attrezzature ausiliarie – e immagazzinando i dati a livello centrale. Il passo seguente sarà utilizzare tutte queste informazioni per programmare la produzione, sfruttando in modo più efficiente le macchine, ridurre gli scarti e prevenire i fermi macchina attraverso la manutenzione programmata e quella predittiva. A questo fine stiamo sviluppando un software ad hoc.
I vostri stabilimenti sono pronti per Industria 4.0?
Abbiamo un parco macchine relativamente giovane – l’eta media è intorno ai dodici anni – che in gran parte può essere interconnesso. Disponiamo di un centinaio di presse Negri Bossi ed Engel con forza di chiusura da 90 a 2.000 tonnellate, ma sono in programma nuovi investimenti nelle macchine elettriche di ultima generazione.
Crediamo anche nella collaborazione con atenei, centri di ricerca e nella formazione interna: in Italia abbiamo instaurato negli anni partnership con l’Università di Napoli Federico II e con l’Università di Salerno, mentre all’estero stiamo avviando un progetto di ricerca con l’ateneo di Cracovia, in Polonia. Al nostro interno, invece, abbiamo attivato un programma di formazione continua, SAPA Academy, rivolto ai nostri addetti, dai capi turno fino ai direttori di stabilimento.