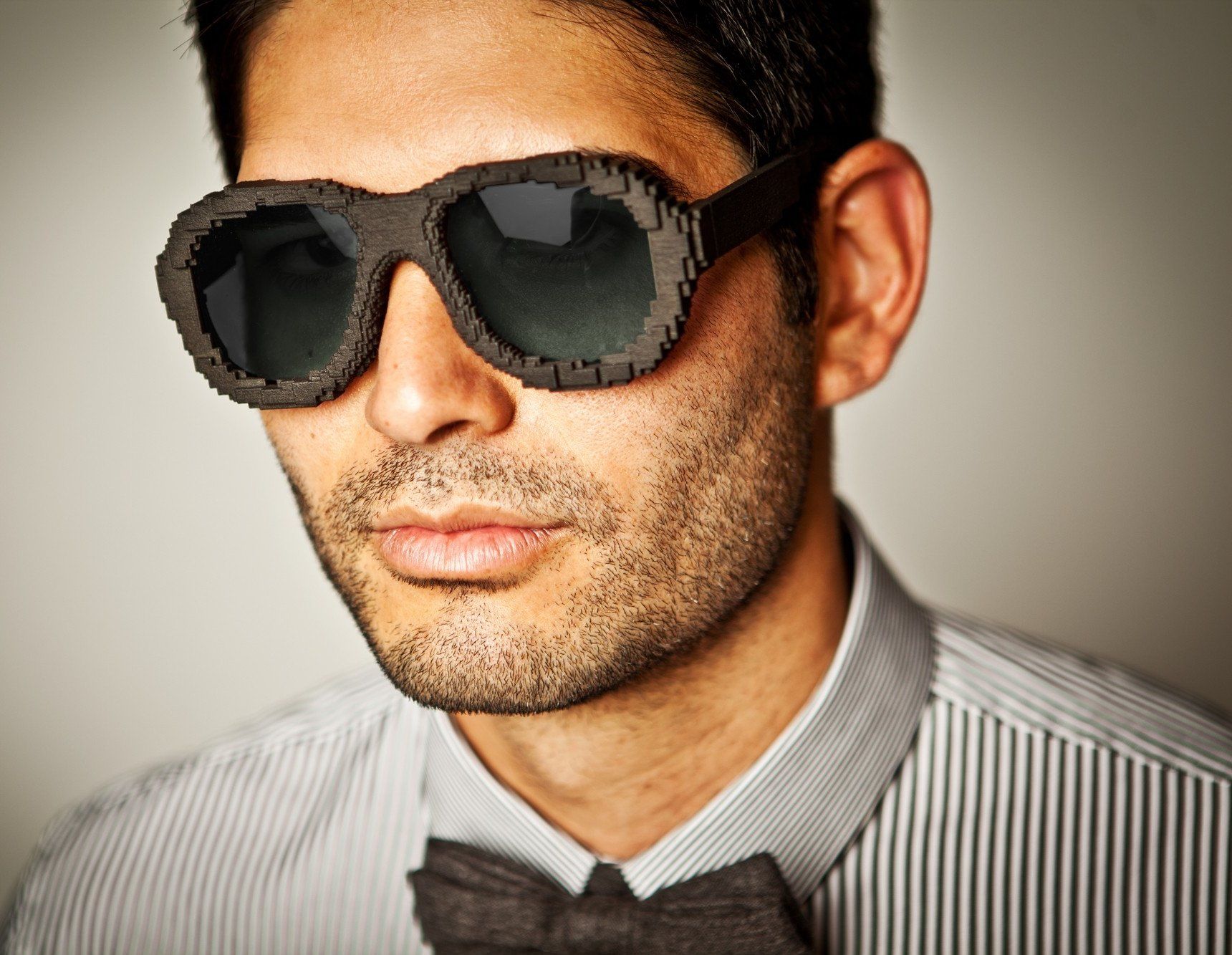
L’occhialeria è un candidato ideale per valorizzare le caratteristiche peculiari dell’additive manufacturing, perché la tecnologia riesce a conciliare sapientemente l’esigenza di personalizzazione dettata dalla necessità sia di realizzare articoli perfettamente calzabili con il massimo comfort, sia di assecondare il gusto individuale dell’utilizzatore. Interfacciandosi con strumenti che rilevano le proporzioni e le morfologie del volto di ciascun individuo, la stampa 3D customizza i singoli modelli impiegando il materiale solo dove serve, realizzando così strutture leggere, elastiche e robuste, che riducono al minimo il peso e l’ingombro della montatura.
Montature su misura
Fornitori di servizi di stampa 3D come il portale sculpteo.com e importanti produttori di tecnologie come Materialise hanno sostenuto lo sviluppo delle realtà manifatturiere più interessanti. Una delle pioniere è la danese Monoqool, che declina il gusto minimale e razionalista tipico del design scandinavo in modelli leggerissimi ed essenziali: le montature della collezione Slider pesano solo quattro grammi. Le estremità dei frontali, in gergo musetti, che si prolungano a includere le cerniere per l’aggancio alle aste, sono modellate a incastro: la complessità di forme e la precisione nel dettaglio, peculiari della tecnologia SLS (Selective Laser Sintering), permettono di eliminare le viti dalle cerniere in un design brevettato. Anche il fondatore di October71, Christophe Mouty, sottolinea la leggerezza dei modelli del proprio brand, con un peso ridotto del 30% rispetto alle versioni standard in acetato di cellulosa o nylon stampato a iniezione, e spessori sottili. Coloratissimi e Pop, gli occhiali da sole sono promossi con il plus di un prodotto Made in France (sono realizzati da Sculpteo).
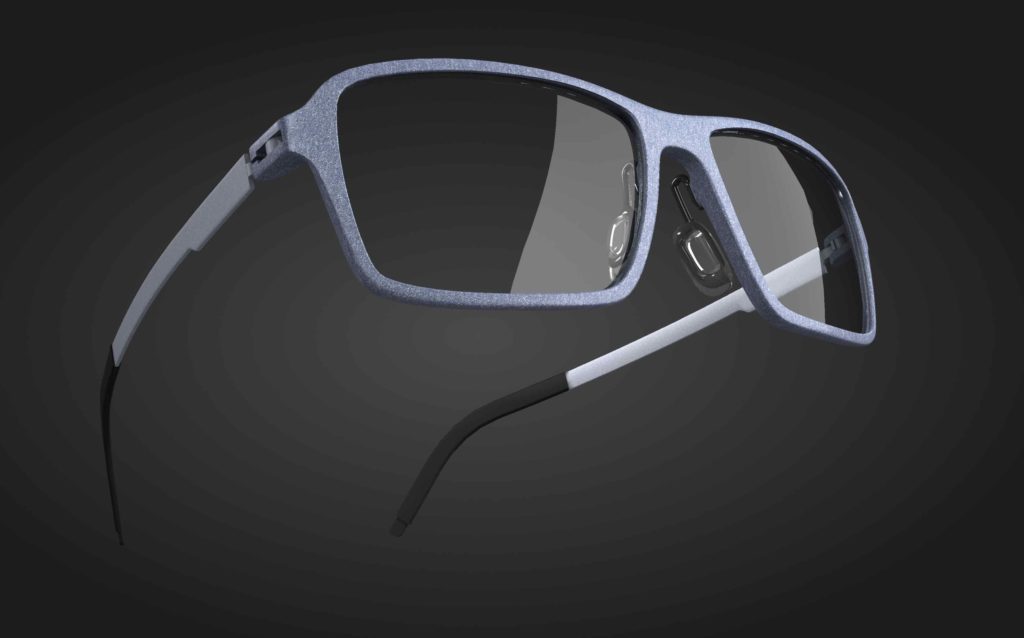
La californiana Protos Eyewear, invece, ha sviluppato un software capace di ricavare da una coppia di foto fronte-profilo del cliente le misure personalizzate per montatura e lenti, suggerendo anche il modello che meglio si armonizza al viso. Le lenti sono in policarbonato con rivestimenti antigraffio, antiriflesso e con protezione UV 400 (lo standard di sicurezza per la schermatura del sole), mentre le montature sono stampate in 3D con bioplastiche ipoallergeniche brevettate, caratterizzate da un’elevata elasticità e resistenza.
Visioni di design
KiteONE è la collezione di occhiali modulari che il designer Benjamin Hubert dello studio Layer firma per il marchio britannico Kite. Commercializzato dalla scorsa primavera e presentato durante il festival londinese designjunction 2018, il cuore di questo progetto è un device portatile per scannerizzare la testa e il viso dell’utilizzatore registrandone le proporzioni esatte, cioè la distanza tra le pupille, l’ampiezza del capo e del naso, e la posizione delle orecchie. Il volto è poi visualizzato su un’app dedicata, abbigliato con gli occhiali prescelti adeguatamente dimensionati modulando la montatura e le aste. L’utente può ulteriormente personalizzare gli occhiali modellando la curvatura delle lenti per armonizzarle alla forma del proprio viso e aggiungendo un messaggio sulle aste.
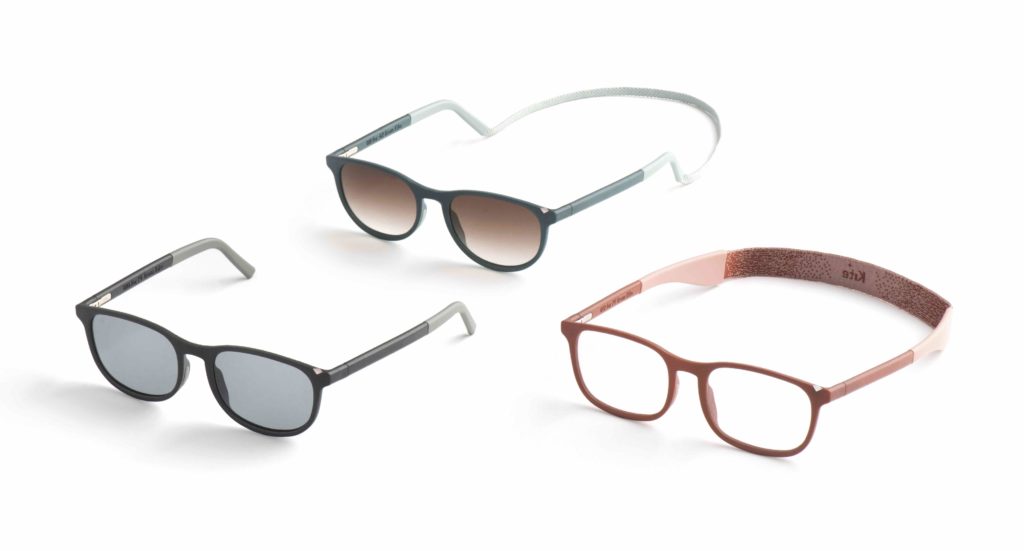
Il file definitivo è inviato al fornitore più vicino per la stampa, la finitura e la colorazione, condotte a termine nell’arco di tre settimane. La montatura, disegnata con linee elegantemente minimali, è realizzata con tecnologia additiva in nylon in tre colori moda, mentre i naselli sono prodotti in gomma siliconica traspirante che riduce al minimo il punto di contatto con il naso per evitare il disagio del surriscaldamento e del sudore in quel punto. Le estremità delle aste degli occhiali sono proposte, oltre che nel tipo Classic in cui il pezzo è interamente stampato in 3D, nelle versioni Tip, con particolari stampati a iniezione per un’aderenza al viso ottimale e corredati da una corda per portarli al collo o da una fascetta elastica per indossarli durante le attività sportive.
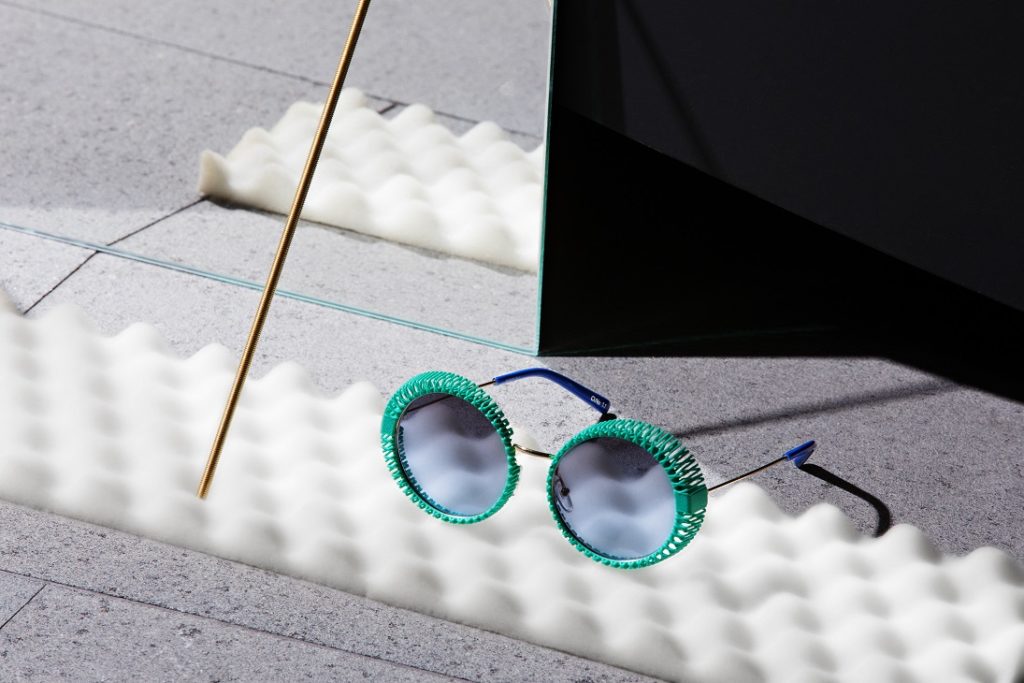
Eclettico Made in Italy
L’italiana Safilo ha collaborato con Materialise per una delle sue collezioni più eclettiche, Oxydo SS 2017. «Ci siamo concentrati nell’affinare la capacità propria del 3D printing di produrre motivi ornamentali estremamente precisi e con dettaglio fine, mantenendo al contempo una silhouette molto minimale. Ci interessava investigare su quale aspetto avrà la decorazione nella prossima generazione» osserva l’artista newyorkese Francis Bitonti, autore di alcuni modelli. Texture e grafismi futuribili sono realizzati con tecnologia SLS presso il centro di produzione additiva certificata di Materialise usando poliammide 12. Con il trattamento post-processing Luxura ai prodotti stampati sono conferite resistenza agli UV e alle macchie, prestazioni anallergiche e traspirabilità, oltre a una vasta gamma di cromie accattivanti.
Benjamin Hubert ha progettato per Kite uno scanner portatile per rilevare la morfologia del viso nel punto vendita e un’app che per mostrare come calzerà di modello di occhiali scelto
Lenti finite e prototipi super realistici
Con le tecnologie additive è possibile stampare anche le lenti. Il nome di riferimento in proposito è Luxecel, che utilizza il sistema VisionEngine con tecnologia Material Jetting e resina a base acrilica VisionClear. In questo processo si depositano gocce di materiale che polimerizzano per effetto di sorgenti di luce UV. Le teste di stampa si muovono avanti e indietro lungo l’intera superficie di lavoro e non punto per punto come, ad esempio, nel metodo FDM (Fused Deposition Modelling), perciò la costruzione è particolarmente rapida e precisa. La tecnologia permette anche di stampare insieme resine con diversa rigidità, cromia o densità. Le stampanti VisionEngine sono in grado di produrre fino a quattro lenti l’ora e non richiedono post-lavorazioni di lucidatura: le loro prestazioni ottiche possono essere ottimizzate con rivestimenti antiriflesso, anti UV o antigraffio. Luxecel supporta questa produzione dedicata anche con il software VisionMaster, che progetta lenti personalizzate, asferiche – più sottili dello standard ma con lo stesso indice di rifrazione –, lenti ad alta diottria o con cilindri alti. La tecnologia Material Jetting è impiegata anche dai sistemi PolyJet di Stratasys, come la macchina J750, che al settore dell’occhialeria è proposta con un materiale dedicato, VeroFlex, per realizzare con uno stesso materiale prototipi definitivi che imitano fedelmente l’aspetto di montature a più colori e delle loro lenti.