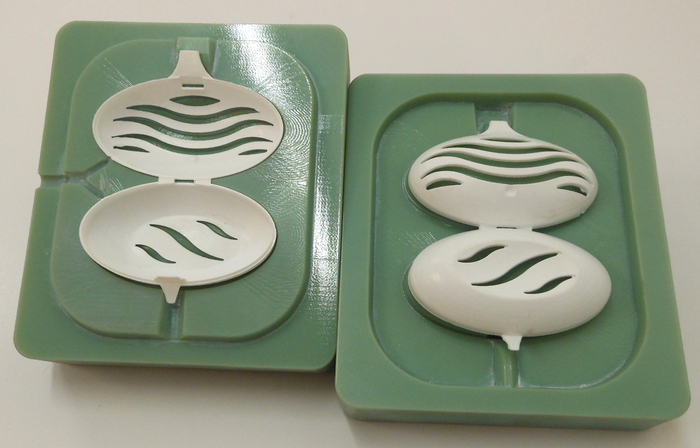
La divisione italiana del gigante internazionale dei beni di consumo Unilever ha ridotto del 40% i lead time per i prototipi da quando ha introdotto le tecnologie 3D printing nel proprio processo di produzione. Tecnologie con le quali oggi realizza stampi a iniezione per le proprie divisioni di prodotti per la casa e la biancheria, con cicli di stampa di circa 50 unità per un’ampia gamma di parti per prototipi, quali tappi e chiusure per flaconi…
«La tecnologia di stampa 3D Stratasys permette di progettare e stampare nell’arco di una sola giornata una varietà di attrezzature per lo stampaggio a iniezione di diverse parti da sottoporre a test funzionali e sui consumatori», spiega Stefano Cademartiri, R&D, specialista di CAD e prototipazione presso Unilever. «In passato, con il processo tradizionale di produzione degli stampi, occorrevano diverse settimane per avere i prototipi e questo non solo allungava i lead time, ma aumentava anche i costi nel caso fossero richieste delle iterazioni. Con la stampa 3D siamo oggi in grado di applicare le iterazioni di progettazione allo stampo in poche ore e di produrre prototipi nei materiali finali come il polipropilene in tempi inferiori del 40% rispetto a prima».
Attraverso un sistema 3D multimateriale Stratasys Objet500 Connex (acquistato presso il rivenditore italiano Overmach) vengono realizzati stampi in ABS digitale, un materiale apprezzato per la sua resistenza alle alte temperature e la sua robustezza, caratteristiche che lo rendono ideale per applicazioni di stampaggio a iniezione. «Costruendo in 3D gli stampi a iniezione in ABS digitale possiamo mantenere l’alto livello di qualità caratteristico dei precedenti prototipi realizzati nel modo convenzionale, riuscendo al contempo a resistere alle alte temperature e pressioni dello stampaggio a iniezione, con costi e tempi significativamente ridotti», aggiunge Cademartiri.
Unilever produce anche prototipi di stampi per termoformatura sul proprio sistema di produzione 3D basato sulla tecnologia FDM Fortus 360mc, utilizzando il materiale platico di produzione ABS-M30. L’azienda è così in grado di produrre stampi realistici con un’alta rigidità alla flessione e in grado di resistere a test funzionali, cruciali per lo sviluppo dello stampo di termoformatura finale. «In passato ricorrevamo a fornitori esterni per i nostri requisiti di termoformatura, ma accumulavamo costi di manodopera particolarmente elevati e dovevamo combattere con lead time piuttosto lunghi», continua Cademartiri. «Da quando produciamo noi stessi queste parti con la stampa 3D abbiamo accorciato i tempi della fase di sviluppo concettuale di circa il 35%. Questa tecnologia ha migliorato il nostro processo di produzione, permettendoci di valutare rapidamente i nostri progetti ed eliminare quelli non idonei, prima di compiere un investimento significativo per la produzione di massa».