Novamont ha fatto del processo reindustrializzazione il suo modello di crescita. Bio. Un esempio è lo stabilimento Mater-Biotech, il primo sito industriale al mondo per la produzione di biobutandiolo, intermediario chimico, prodotto direttamente da zuccheri tramite l’utilizzo di batteri anziché fonti fossili, usato per realizzare sacchetti bio e teli per l’agricoltura. Interamente riciclabili e compostabili. Nel pieno rispetto dell’economia circolare.
«I campioni non si fanno nelle palestre. I campioni si fanno con qualcosa che hanno nel loro profondo: un desiderio, un sogno, una visione» diceva un grande fuoriclasse come Muhammad Alì. Ed è proprio la capacità di visione quella che contraddistingue da sempre il gruppo Novamont, protagonista a livello internazionale nel settore delle bioplastiche e dei “biochemicals”.
La società, infatti, ha creato negli anni a un modello di bioeconomia fondato sulla rigenerazione di siti deindustrializzati o in grave crisi, dando così nuova vita al territorio circostante.
Al momento sono 6 i siti che il gruppo ha rivitalizzato e 5 le tecnologie prime al mondo realizzate e moltiplicabili secondo il modello di bioraffineria integrata nel territorio, dove vengono messi a punto tecnologie e prodotti capaci di dare risposte concrete a problemi come quello della valorizzazione del rifiuto organico.
L’esempio di Mater-Biotech
Tra i siti a cui il gruppo Novamont ha dato nuova vita c’è quello di Bottrighe, frazione del comune di Adria, in provincia di Rovigo, dove negli anni ’70 veniva prodotto glutammato per l’industria alimentare.
Attività proseguita fino a metà degli anni ’90, quando venne ceduta a una multinazionale giapponese che utilizzò l’impianto per la produzione di aminoacidi destinati a mangimi per animali fino al 2006, anno in cui decise di chiudere l’attività.
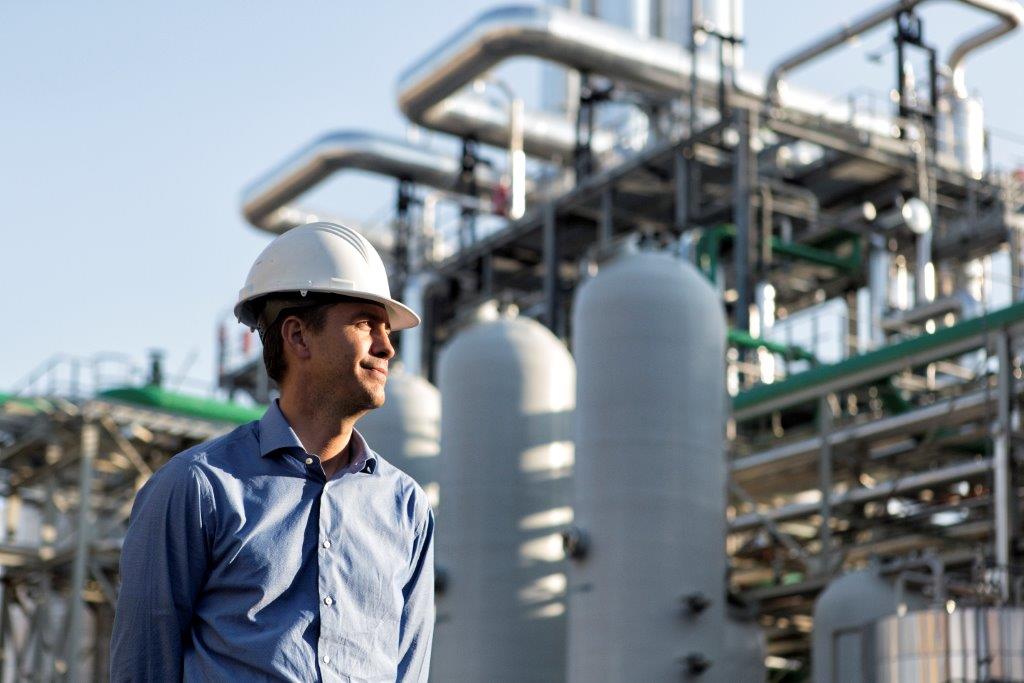
Per i seguenti dieci anni il sito produttivo venne abbandonato fino all’acquisizione, nel 2016, da parte del Gruppo Novamont, che dopo una profonda riconversione industriale, costata oltre 100 milioni di euro, inaugurò il primo sito industriale al mondo per la produzione di biobutandiolo (BDO), un intermediario chimico prodotto direttamente da zuccheri attraverso l’utilizzo di batteri anziché fonti fossili.
Nello specifico si tratta di un materiale destinato alla produzione della quarta generazione delle bioplastiche Mater-Bi, il biopolimero di Novamont, e si contraddistingue per il suo contenuto elevato di materie prime rinnovabili.
E’ stato calcolato che la sostituzione di 1,4 BDO da fonte fossile con il biobutandiolo BDO per la produzione di Mater-Bi, porta a un aumento del contenuto rinnovabile dal 36 al 61% con una riduzione del 10-15% dell’impronta di carbonio.
«Quella che produciamo è una materia prima liquida che viene usata nel processo di polimerizzazione destinato alla produzione del Mater Bi, prodotto che viene poi usato per fare sacchetti bio o teli per l’agricoltura. Prodotti biodegradabili che se trattati in impianti di compostaggio possono essere poi riutilizzati come compost» spiega Stefano Dessì, direttore dello stabilimento Mater-Biotech di Novamont.
Punto di partenza la fermentazione
A sviluppare il microorganismo per la produzione della molecola di 1.4 butandiolo biotecnologico è stata Genomatica, società californiana leader nel settore della bioingegneria, che poi ha dato a Novamont la licenza per produrla.
Da qui la realizzazione di una piattaforma biotecnologica che, partendo da zuccheri, attraverso l’azione di batteri di tipo Escherichia coli (E. Coli) opportunamente ingegnerizzati, li trasforma in biobutandiolo.
«La produzione avviene tramite un processo di fermentazione assimilabile a quello di un grosso birrificio» precisa Dessì.
«All’interno di grandi serbatoi il microrganismo dell’E. Coli riconverte le soluzioni di glucosio degli zuccheri in 1.4 butandiolo, generando anche della biomassa. La fase successiva del processo, invece, è quella di purificazione dell’1.4 butandiolo, ovvero della sua separazione dalla biomassa. Quest’ultima, dopo essere stata inattivata dall’Escherichia coli viene valorizzata in un impianto di biodigestione generando biogas. Il butandiolo, invece, prosegue il suo processo di purificazione attraversando una serie di fasi che prevedono scambi ionici, evaporazioni per recupero dell’acqua fino a una distillazione che porta poi al prodotto finito.»
A sei anni dall’inaugurazione l’impianto veneto oggi è in grado di produrre 30 mila tonnellate l’anno di BDO a basso impatto con un risparmio di oltre il 50% di emissioni di CO2.
«La maggior parte della materia prima che esce dallo stabilimento è destinata a Novamont» prosegue Dessì.
«Ma negli ultimi anni anche altri operatori del mercato si sono dimostrati interessati alla nostra produzione, tanto che ora ci stiamo aprendo a forniture terze. Inoltre, abbiamo anche iniziato a produrre 1.3 butilenglicole, altra molecola nata nei laboratori di Genomatica, simile all’1.4 butandiolo, ma con applicazioni diverse: viene, infatti, utilizzata come materia prima nella cosmetica. Questo ci consentirà di ampliare sempre di più il nostro parterre di clientela.»
Efficienza energetica in primo piano
Certo un impianto di produzione energivoro nel suo complesso, per questo dalla sua nascita, è stata data grande attenzione al tema dell’efficienza energetica. L’azienda, infatti, è stata concepita per poter riutilizzare i sottoprodotti della lavorazione per il suo fabbisogno energetico, ottimizzando così il ciclo di vita dell’intero processo.
«Consapevoli del fatto che mediamente i costi dell’energia impattano per il 30% sul prezzo del prodotto finale, fin dall’inizio abbiamo attivato una serie di procedure per mitigare i consumi» dice Dessì.
«Per esempio, abbiamo investito molto in motori ad alto rendimento ed efficienza, abbiamo cercato di riutilizzare, dove possibile, i cascami termici all’interno dello stabilimento e utilizziamo la riconversione meccanica del vapore per poterlo riutilizzare nell’impianto. Ma abbiamo anche implementato l’impianto di cogenerazione per generare l’elettricità di cui la produzione necessita. Infine, dai nostri scarti (biomassa) generiamo biogas e, grazie a un upgrading attuato nel 2018 siamo in grado di riconvertirlo in biometano che viene poi messo in rete. A oggi il 10% del metano che utilizziamo è costituito dal biometano di nostra produzione. Tutto questo ci ha permesso di rendere molto efficiente l’impianto energetico e, quindi, di contenere i costi.»
Il futuro
Nel momento in cui scriviamo (NdR luglio) il gruppo Novamont guarda al futuro, che è legato a doppio filo alla proposta di acquisizione fatta da Versalis, azienda chimica italiana della galassia Eni, che già possiede il 36% delle quote di Novamont.
Una mossa che rientra nella strategia di forte specializzazione del portafoglio che Versalis sta perseguendo da anni e che ora guarda con interesse alla chimica da fonti rinnovabili, in linea con il percorso di transizione energetica che sta portando avanti la multinazionale del cane a sei zampe.
L’operazione di acquisizione, che dovrebbe essere conclusa entro la fine di settembre 2023, permetterà di rafforzare la piattaforma Novamont, accelerando la crescita di filiere multi prodotto ad alto valore aggiunto e i progetti di territorio per disaccoppiare l’utilizzo delle risorse naturali dalla crescita economica nella logica di fare di più con meno.
Senza contare il fatto che, unendo le loro competenze tecniche e di mercato le due società potranno accelerare lo sviluppo di tecnologie e filiere, avendo così la possibilità di giocare un ruolo chiave nel campo della chimica da fonti rinnovabili e della bioeconomia circolare a livello nazionale e internazionale.
«Un passo strategico importante che consentirà a Novamont di raggiungere una posizione di leadership nella chimica da fonti rinnovabili, grazie allo sviluppo continuo delle nostre tecnologie e ad acquisizioni selezionate, offrendo al mercato un’ampia gamma di prodotti specializzati di origine bio» afferma Dessì.
L’obiettivo di Novamont è, infatti, quello di continuare a crescere anche nei polimeri, in particolare aumentando la quota di prodotti specializzati dall’attuale 20% del fatturato totale dell’azienda ad almeno il 35%, pari a circa la metà del portafoglio polimeri totale, entro il 2026.
Per questo l’operazione di acquisizione viene vista come una grande opportunità di accelerazione della strategia attraverso l’integrazione di una piattaforma tecnologica unica e complementare, in grado di fornire un contributo determinante alla decarbonizzazione del portafoglio prodotti.
Costituito nel 2018 dai sei produttori e trasformatori di bioplastiche (Ceplast, Ecozema, Ibi Plast, Industria Plastica Toscana, Novamont e Polycart), il Consorzio conta oggi oltre 200 aziende consorziate e ha l’obiettivo di gestire la fine vita degli imballaggi in plastica biodegradabile e compostabile attraverso il loro riciclo organico insieme alla frazione umida dei rifiuti urbani per trasformarli in compost.
Il processo seguito è quello della decomposizione biologica della sostanza organica che avviene in condizioni controllate.
«Siamo un Consorzio di diritto privato, senza fini di lucro. Il nostro statuto è stato approvato con un decreto del Ministero della Transizione Ecologica e del Ministero dello Sviluppo Economico» spiega Carmine Pagnozzi, Direttore generale del Consorzio.
«Ci occupiamo di favorire lo sviluppo della raccolta differenziata dell’organico, garantendo fondi ai Comuni convenzionati con noi per coprire i costi da loro sostenuti per raccogliere, trasportare e trattare gli imballaggi compostabili insieme ai rifiuti umidi, così da non far gravare il servizio sull’utente finale.»
Ma il Consorzio si occupa anche di sviluppare campagne di comunicazione per facilitare, stimolare e incentivare la raccolta differenziata tra i cittadini e presidia eventuali fenomeni di contraffazione.
«Molti sono infatti i casi di uso e commercializzazione di sacchetti illegali, spesso provenienti da filiere estere non controllate. Parlo di sacchetti per l’asporto di merci e quelli forniti come imballaggio primario di alimenti sfusi, che contengono poliolefine (PO), come il polietilene (PE), in percentuali variabili» precisa Pagnozzi.
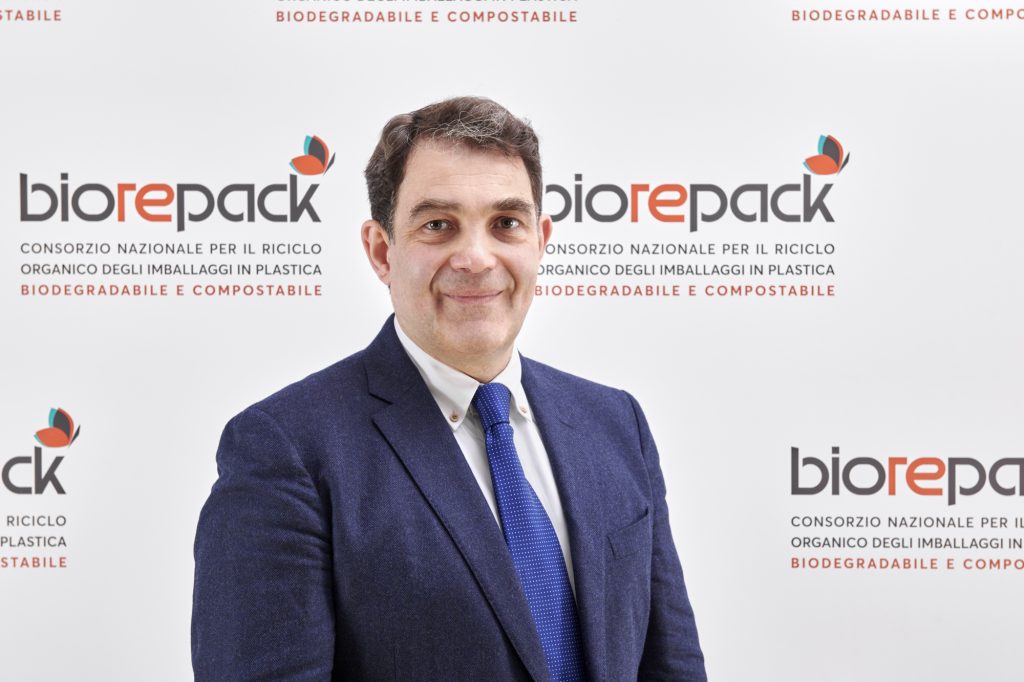
Nel 2022 sono state riciclate 46.600 tonnellate di imballaggi in bioplastica compostabile insieme all’umido e sono state quindi trasformate in compost.
Il tasso di riciclo ha quindi raggiunto il 60,7% dell’immesso al consumo, superando con otto anni di anticipo l’obiettivo del 55% fissato per il 2030.
«Ma il nostro obiettivo è continuare a far crescere qualità e quantità della raccolta, aumentando il numero di convenzioni con gli enti locali e i gestori dei rifiuti in tutta Italia» chiosa Pagnozzi.
di Nadia Anzani