Nella giornata di giovedì 30 novembre, presso il consorzio Proplast di Alessandria, si è tenuto il seminario tecnico: “Tecnologie non convenzionali – Stampaggio di compositi termoplastici fibrorinforzati e di espansi con struttura microcellulare”. L’evento, organizzato dal consorzio in collaborazione con partner tecnologici qualificati come Altair, Centro Ricerche Fiat, DMagis ed Engel, ha rappresentato un’ottima occasione per approfondire le proprie conoscenze in merito alle recenti soluzioni sviluppate per realizzare componenti fibrorinforzati a matrice termoplastica (tecnologia Engel organomelt) ed espansi microcellulari mediante la tecnologia Engel foammelt basata sul processo MuCell di Trexel.
Come dichiarato dal direttore di Proplast, Giuseppe Augugliaro: “L’affluenza è stata così elevata da dover chiudere le iscrizioni con largo anticipo, a causa del raggiungimento della massima capienza della sala conferenze di Proplast, pari a circa 80 persone”. La redazione di Plastix era presente e l’articolo che segue intende riassumere, seppur in estrema sintesi, i concetti esposti durante le singole presentazioni e nel corso dell’esperienza tecnico-pratica di fine mattinata. Ma andiamo con ordine…
Dopo i saluti di rito da parte del direttore di Proplast, il seminario è iniziato con l’interessante presentazione di Vito Guido Lambertini, Materials technical expertise & Innovation manager, presso il Centro Ricerche Fiat (CRF) del gruppo Stellantis.
Verso i futuri veicoli Carbon Net Zero
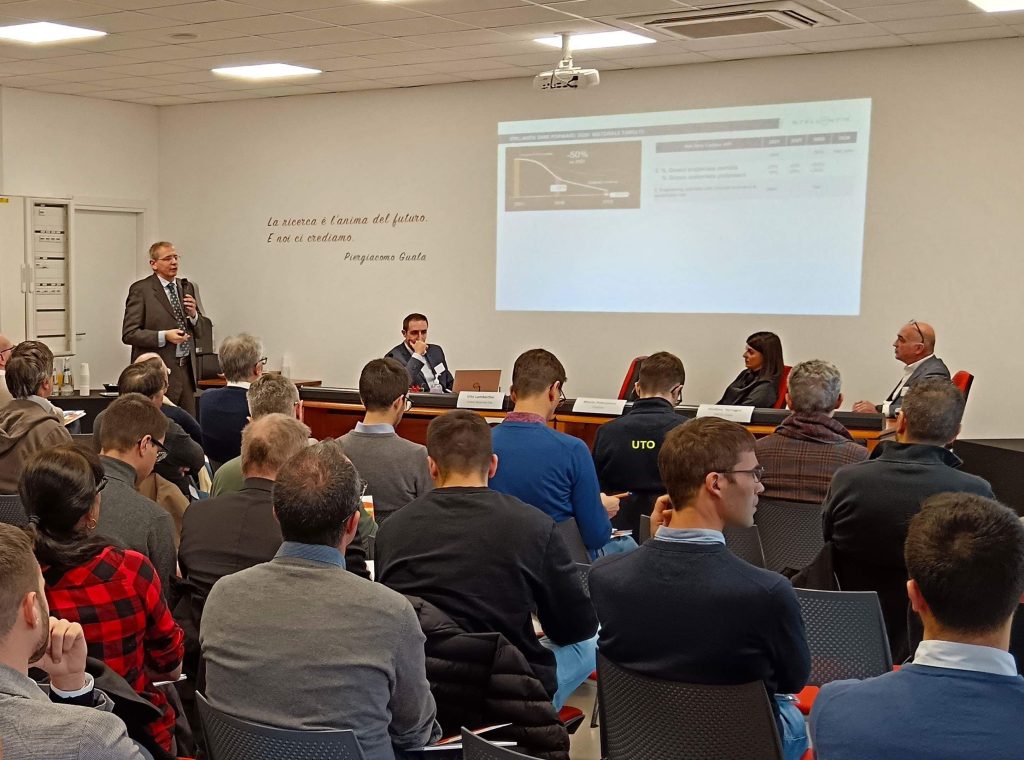
Con il titolo “Gli obiettivi di sostenibilità per i materiali utilizzati da Stellantis, verso i futuri veicoli Carbon Net Zero”, la relazione di Lambertini si è inizialmente concentrata sulle motivazioni che hanno portato Stellantis a introdurre determinati “materiali green” ed ecologici nei propri veicoli. Tra tali motivazioni, vi è, in primo luogo, la sua strategia per la mitigazione del cambiamento climatico. In questo ambito, l’azienda si è posta l’obiettivo di ridurre la propria impronta di carbonio del 50% entro il 2030 (rispetto al 2021). Sono quindi in corso diverse attivitàdi CRF/Stellantis nell’ambito di progetti di collaborazione volti a raggiungere tale obiettivo di sostenibilità.
Scendendo più nel concreto, Vito Guido Lambertini ha voluto quindi illustrare alla platea cinque tra i più interessanti progetti di collaborazione in corso:
– PP e ABS riciclati post triturazione. Selezione, recupero e riciclo ad alto valore aggiunto di materiali termoplastici secondari di alta qualità provenienti dal flusso di rifiuti degli ELV (End-of-Life Vehicles: veicoli a fine vita).
– Rinforzi riciclati: fibre di carbonio (CF) e fibre di vetro (GF). Il progetto europeo EoLO-HUBs sta sviluppando soluzioni innovative per riciclare materiali ad alto valore provenienti dal recupero delle pale eoliche.
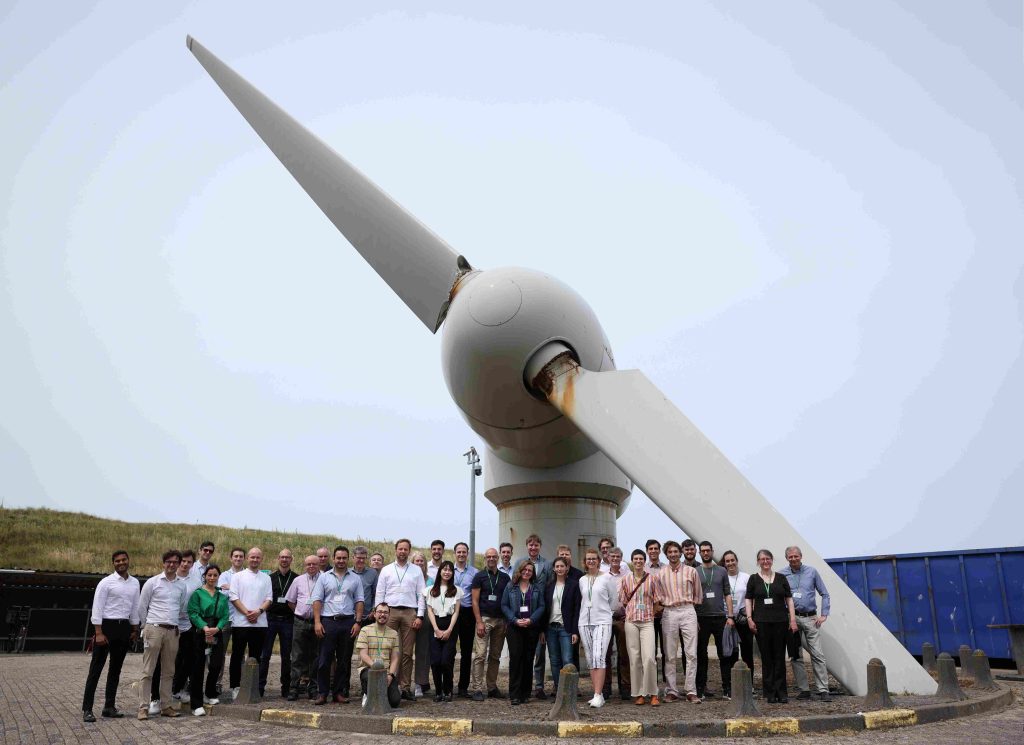
– Compositi bio-based e riciclati. Finanziato dall’UE, il progetto r-LightBioCom punta all’ottenimento di nuove materie prime a base biologica e sostenibili in grado di “abilitare” catene del valore circolari di biocompositi leggeri e ad alte prestazioni.
– Polimeri bio-based. Il progetto Life Viable mira a migliorare la sostenibilità e l’impatto ambientale della produzione di resine epossidiche riducendo dal 20 al 50% il contenuto di bisfenolo A (BPA) nella loro formulazione. Questo, grazie all’utilizzo di componenti competitivi provenienti dai processi di valorizzazione delle biomasse a base di lignina e capaci di sostituire gradualmente il BPA.
– Materiali green per l’industria tessile. Il progetto my.fi, finanziato dall’UE, si è posto l’obiettivo di “reinventare l’industria tessile”, rendendola smart, circolare e competitiva grazie alle “micofibre”; il micelio può infatti essere trasformato in cluster di microfibre per produrre materiali avanzati, ottimi anche per gli interni auto.
“L’evoluzione delle automobili necessita quindi di materiali ecosostenibili (più leggeri, più performanti ed ecologici) con prestazioni adeguate al settore automobilistico”, si è avviato a concludere Vito Guido Lambertini. “Diversi prodotti green sono già sul mercato o stanno per esservi immessi, ma sono necessari ancora step di ottimizzazione/miglioramento per una loro completa introduzione nel settore automobilistico, dal punto di vista sia tecnico che della filiera di fornitura. Come si è visto, il CRF è coinvolto in diversi progetti di ricerca volti a ottenere polimeri sostenibili, che però presentino: prestazioni costanti (cioè una fonte stabile), una rete di raccolta efficiente per il loro riciclo, processi di trasformazione affidabili, nuovi standard specifici per tali materiali e una nuova progettazione di prodotto, per sfruttare al meglio le loro proprietà. Un approccio collaborativo è fondamentale per sfruttare appieno il potenziale di questi nuovi materiali polimerici”.
Simulazioni strutturali di laminati compositi a matrice termoplastica
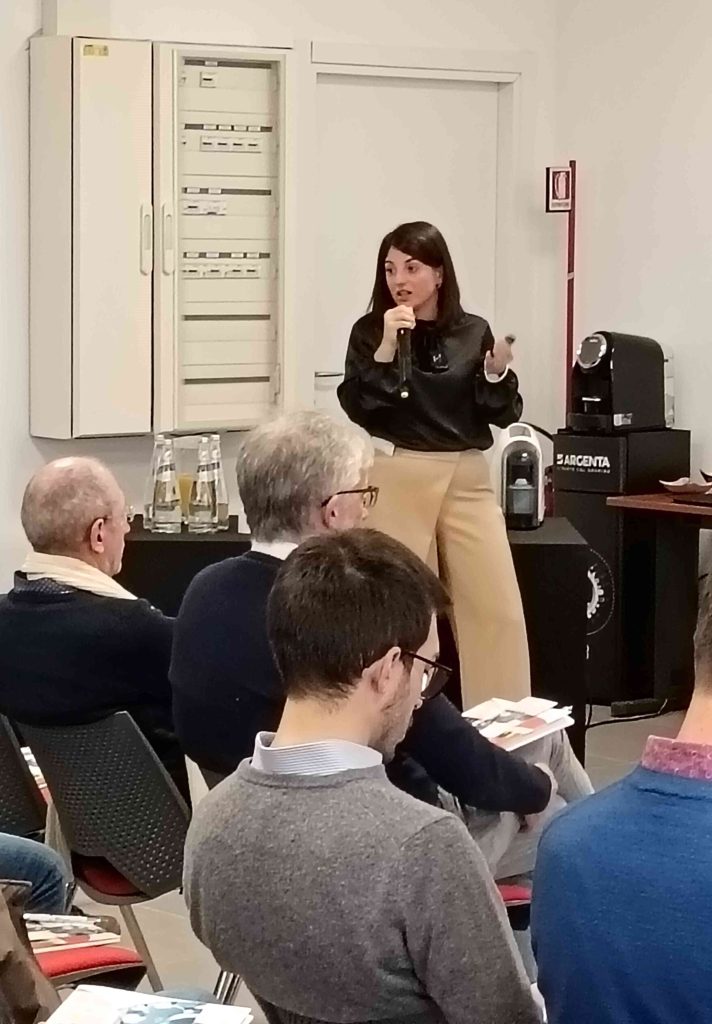
L’intervento successivo di Marta Palenzona, progettista componenti plastici e analista FEM presso Proplast, ha discusso delle “Simulazioni strutturali di materiali complessi”, focalizzandosi proprio sui laminati compositi a matrice termoplastica, od organosheet, citati da Terragni.
“I laminati compositi a matrice termoplastica sono materiali tecnologicamente avanzati”, ha spiegato Marta Palenzona, “tanto da essere ritenuti validi sostituti dei metalli in un’ottica di alleggerimento dei componenti. Sono altresì caratterizzati da una forte dipendenza delle proprietà meccaniche dalla direzione di sollecitazione; in altre parole, sono materiali fortemente anisotropi. Questa peculiarità complica l’utilizzo delle organosheet: di fatto, la complessità strutturale del materiale è strettamente correlata alla complessità nel descriverlo e nel prevederne il comportamento in fase d’esercizio. Pertanto, nell’ottica di una progettazione ottimizzata, risulta fondamentale disporre di strumenti che permettano lo studio preliminare della risposta meccanica dei manufatti realizzati in materiali complessi”.
“Negli ultimi anni, grazie anche ad alcuni progetti di ricerca, Proplast ha sperimentato le potenzialità e l’affidabilità del software di simulazione strutturale Altair Hyperworks, solutore Radioss”, è scesa più in dettaglio Palenzona. “Quest’ultimo si è dimostrato un indispensabile alleato nel design di manufatti in materiali complessi. Inoltre, è stato possibile definire e consolidare la procedura alla base della descrizione del materiale: cominciando con lo studio del singolo elemento, per una prima stima dei parametri di elasticità e plasticità, si sono poi replicate fedelmente le prove di caratterizzazione di trazione, taglio, compressione e flessione, per validare i parametri inseriti e definire quelli di danneggiamento, avendo cura di dettagliare meticolosamente sia il laminato (compresa la “stacking sequence”) sia il sistema dinamometrico, fino alla simulazione della prova di flessione a tre punti di un manufatto reale. La bontà della “card material” così compilata è stata determinata tramite il confronto tra i risultati derivanti dai test reali e quelli virtuali”.
Componenti leggeri in un unico step produttivo
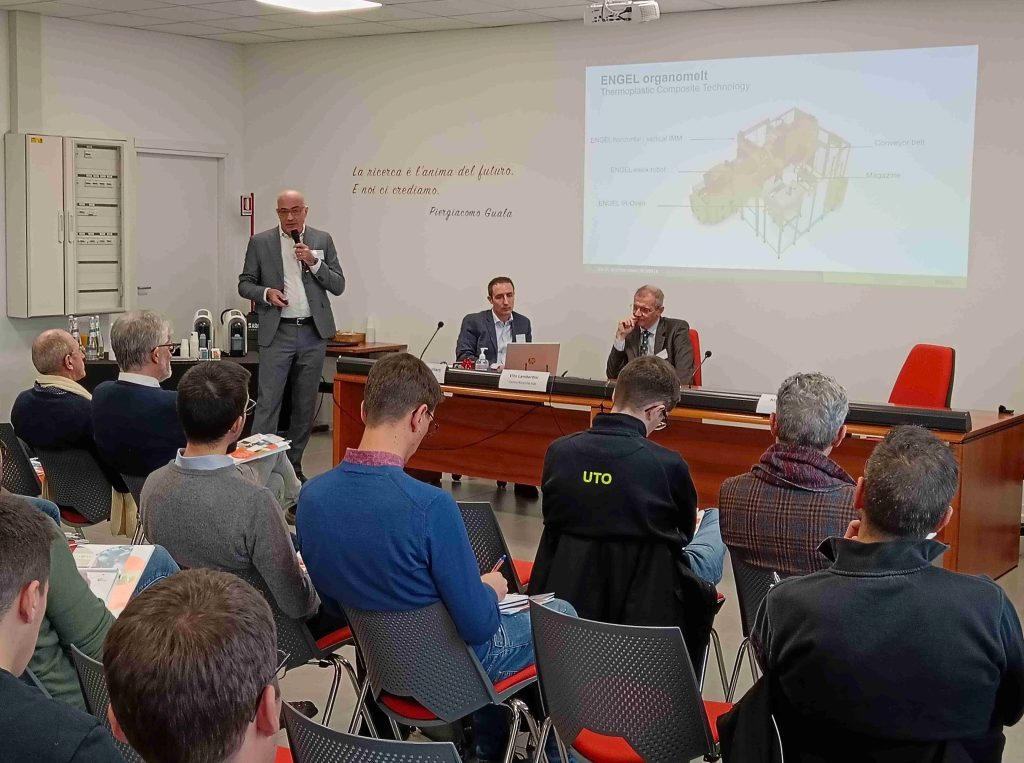
La parola è quindi passata all’amministratore delegato di Engel Italia, Matteo Terragni, con la propria relazione dal titolo: “Tecnologia organomelt per applicazioni strutturali in compositi termoplastici”.
La crescente importanza acquisita dai materiali termoplastici nella produzione di strutture leggere ha spinto Engel a effettuare negli ultimi anni sostanziosi investimenti in tecnologie e sistemi per la lavorazione dei compositi termoplastici. “Siamo tra le prime aziende al mondo in grado di offrire un processo completamente integrato, che inizia in una cella di posa degli UD tape (nastri in fibra di carbonio unidirezionale) e finisce con un componente leggero in termoplastico, sovrastampato e perfettamente consolidato”, ha esordito Terragni.
La cella adibita alla posa degli UD tape si basa sul principio “pick and place”: i nastri possono essere depositati e saldati insieme in loco a intervalli di 3-4 secondi. Dal momento che la qualità dello strato di UD tape dipende dalla precisione con cui vengono posizionati i singoli nastri, Engel ha equipaggiato la cella con un sistema di misurazione dotato di videocamera ad alta risoluzione. A valle si trova un’unità di consolidamento, che provvede a fissare lo strato di UD tape durante il ciclo di stampaggio a iniezione.
Il cuore del processo integrato è rappresentato dall’isola di lavoro Engel organomelt. Qui, i preimpregnati in composito termoplastico fibrorinforzato, quali per esempio i nastri UD e le foglie organiche (organosheet), vengono sovrastampati e funzionalizzati. Parti funzionali come le nervature di rinforzo o gli elementi d’assemblaggio possono essere sovrastampati immediatamente dopo la termoformatura, utilizzando una resina termoplastica del medesimo tipo della matrice. Ciò rende possibile un processo produttivo altamente integrato e completamente automatizzato che, al contempo, agevola il riciclo dei pezzi al termine della loro vita utile.
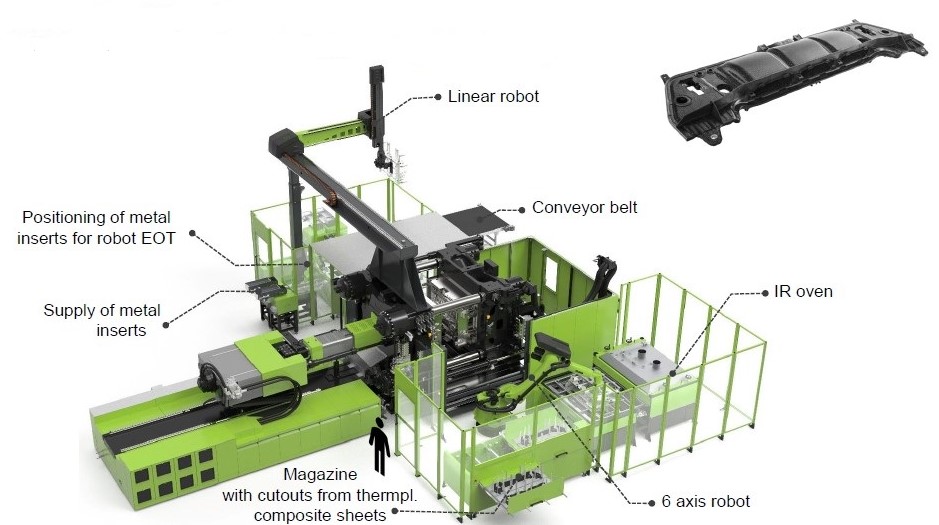
La tecnologia organomelt è stata sfruttata, per esempio, nella fabbricazione dei moduli porta della società tedesca Brose, che, rispetto ai tradizionali sistemi in acciaio, pesano circa il 40% in meno (-5 kg), pur mantenendo le medesime prestazioni di sicurezza in caso d’impatto. Inoltre, Brose è riuscita ad abbattere lo spessore delle pareti ad appena 0,6 mm.
“Alla fiera K 2019 avevamo mostrato proprio quest’applicazione in collaborazione con Brose”, ha raccontato Terragni. “In quel caso, l’isola di stampaggio era caratterizzata da due forni a infrarossi e da tre robot antropomorfi, che provvedevano a caricare le tre diverse organosheet all’interno dello stampo, sovrastampandole successivamente per ottenere il pannello porta. L’anno successivo Engel ha poi vinto lo JEC Innovation Award grazie a un sistema in grado di disporre le singole organosheet una sopra all’altra, con orientamenti diversi, e di consolidarle, creando una struttura davvero resistente”.
“L’evento Lightweight Future Day 2021 di Engel ha poi rappresentato l’occasione giusta per presentare una più recente linea completamente automatizzata per la produzione di organosheet in un singolo passaggio. L’isola di lavoro, completa e funzionante, prevede in pratica una prima fase di posizionamento degli UD tape”, ha spiegato più in dettaglio l’AD di Engel Italia. “Una volta che il singolo UD tape è stato posizionato, viene saldato a ultrasuoni con quello precedente a cui è stato sovrapposto, in modo da tenerli insieme e poterli movimentare, a quel punto già sotto forma di “foglia organica”. In seguito, prima di riscaldarle nel forno a infrarossi, occorre consolidare le organosheet, altrimenti tendono ad aprirsi. Per questo Engel e la società costruttrice Fill hanno sviluppato congiuntamente un particolare sistema per il consolidamento, che avviene totalmente in automatico. In estrema sintesi, tale dispositivo si basa su una serie di pressori: il primo riscalda e consolida, il secondo raffredda, mentre dal terzo esce l’organosheet finita. A quel punto un robot la preleva e la carica nel forno a infrarossi per la polimerizzazione (curing). Infine, l’organosheet viene sovrastampata grazie a una pressa a iniezione Engel dedicata”.
Matteo Terragni ha concluso il suo intervento in Proplast citando anche altre applicazioni della tecnologia Engel organomelt, come lo stampaggio di un pedale per il freno con un risparmio del 50% in peso e la produzione di una struttura in PP fibrorinforzato, a doppia conchiglia, realizzata da Valeo per il “frontend” di alcune vetture di Mercedes-Benz Group.
Pezzi stampati a iniezione con struttura in espanso microcellulare
Alle 11 circa, subito dopo il coffee break, è stata la volta della seconda presentazione di Matteo Terragni: “Tecnologia foammelt per applicazioni leggere: produzione di pezzi stampati a iniezione con struttura in espanso MuCell”. La tecnologia foammelt è stata messa a punto da Engel per gestire lo stampaggio a iniezione di espansi microcellularimediante la tecnica Mucell, sviluppata dalla società statunitense Trexel, per consentire d’ottenere manufatti espansi con un intrinseco alleggerimento in peso. A tale riguardo, oltre ai successivi paragrafi riguardanti gli altri interventi su questo tema, rimandiamo al seguente articolo d’approfondimento pubblicato su Plastix qualche anno fa, ma ancora attuale: https://www.plastix.it/cresce-lefficienza-con-il-gas-espandente/
Percorso guidato per ottenere il massimo dalla tecnologia Mucell
L’intervento successivo, “Stampaggio microcellulare MuCell: un percorso guidato per ottenere il massimo dalla tecnologia”, di Andrea Romeo, responsabile del laboratorio Advanced Design di Proplast, ha illustrato il percorso in tre step messo a punto da Proplast per offrire il massimo supporto alle aziende che intendano approcciare la tecnologia Mucell, grazie all’esperienza maturata negli anni e alle strumentazioni software e hardware di cui si è dotata.
“In particolare”, ha spiegato Romeo, “il primo step di sviluppo consiste in un prestudio volutamente snello e agile, chiamato “MuCell Lean Preview and ROI Estimation”, che consente di ottenere indicazioni chiave sull’applicabilità della tecnologia e sui potenziali attesi in termini di riduzione del peso dell’articolo stampato, forza di chiusura e riduzione del tempo di ciclo.
Il secondo approccio, più approfondito e maggiormente customizzabile sulle esigenze del committente, prevede lo sviluppo di un design di componente mirato per MuCell con l’utilizzo di strumenti di analisi virtuale, tra cui simulazioni FEM con i software Altair Hyperworks per guidare la fase di sviluppo prodotto, e software di simulazione di flusso per validare il processo MuCell, fornendo indicazioni numeriche precise sui risultati attesi. Come terza modalità d’approccio alla tecnologia, è possibile eseguire prove di stampaggio presso le strutture di Proplast, dove è presente una pressa Engel Victory da 120 tonnellate, equipaggiata con cilindro e vite MuCell e interfacciata a un’unità di Trexel per il controllo e il dosaggio del gas nel materiale fuso”.
“Con questo approccio multistep”, ha chiosato Andrea Romeo, “Proplast è in grado di seguire il cliente in tutte le fasi del progetto MuCell, dall’analisi teorica alla valutazione del risultato sul pezzo reale”.
L’IA nei contesti industriali
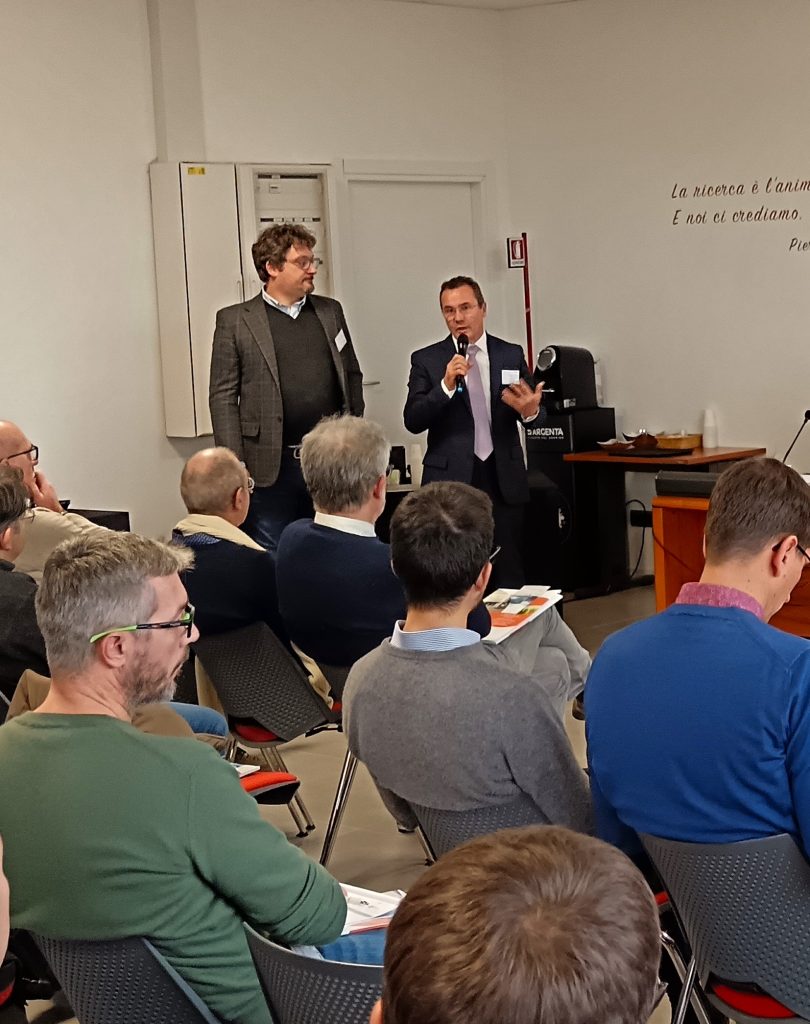
L’ultimo intervento in aula, dal titolo: “Applicazioni di Intelligenza Artificiale (IA) nei contesti industriali: dallo sviluppo del prodotto alla produzione”, è stato quello di Federico Urban, cofondatore della società Plus, introdotto da Mosè Necchio, responsabile marketing di Dmagis, tra gli sponsor/organizzatori dell’evento.
La PMI Plus si propone di realizzare strumenti basati sulle più evolute tecniche di machine learning affinché le aziende riescano a “mettere a terra” il completo potenziale derivante dall’applicazione degli algoritmi d’intelligenza artificiale.
“Oggigiorno viviamo nell’era della complessità”, ha esordito Urban. “In ogni fase del ciclo di ricerca, sviluppo e produzione dei prodotti si devono affrontare sfide tecnologiche sempre più severe. L’accorciamento del tempo di progettazione e la necessità di adeguare la produzione ai sempre più stringenti vincoli d’impatto ambientale pongono il tecnico in una situazione per la quale è indispensabile essere supportati da assistenti virtuali”.
“Questi assistenti, siano essi ChatBot più o meno evoluti oppure piattaforme digitali che automatizzano sofisticati flussi progettuali, sono di primaria importanza nel momento in cui l’ingegnere viene chiamato a prendere la migliore decisione basata sui dati disponibili”, ha proseguito Urban. “Si pensi, per esempio, alla necessità di configurare al meglio lo stampaggio a iniezione laddove, oltre all’individuazione del punto d’iniezione, venga anche richiesto di definire le condizione operative più adatte all’ottenimento di componenti d’alta qualità, cercando al contempo il migliore setup per ridurre pure i costi d’esercizio. Per questo, Plus si propone di sviluppare applicativi ad hoc che rispondano a tali richieste facendo largo uso di metodi numerici e informatici. Per fornire la migliore soluzione possibile, l’interlocuzione con i clienti avviene con un team di ingegneri industriali che traducono le richieste in un piano d’implementazione mediando con le altre professionalità dell’azienda, come il team di data scientist e gli IT specialist. In questo modo Plus è in grado di fornire soluzioni legate ai vari domini dell’IA nella forma di strumenti impiegabili nei processi e non solo di semplici report tecnici poco azionabili”.
Gli applicativi forniti ad aziende quali Stellantis, Electrolux, gruppo VW, rappresentano esempi di soluzioni software sviluppate da Plus per facilitare gli operatori concependo un esperienza d’uso che possa abbattere gli ostacoli che si frappongono tra l’utilizzatore e la macchina. Si tratta, per esempio, di chatbot che sono in grado di rispondere a richieste a cui, causa la “segregazione” dei dati aziendali, è difficile dare una pronta e oggettiva risposta. Questo è possibile attraverso lo sviluppo dell’integrazione dei silos informativi, impiegando tecnologie informatiche allo stato dell’arte. Un altro esempio riguarda l’impiego di reti neurali profonde per conoscere il consumo di un veicolo, senza doverlo misurare in galleria del vento. Oppure, ancora: concepire algoritmi che riescano ad automatizzare stazioni di progettazione di componenti meccanici complessi.
“L’obiettivo della società Plus”, ha concluso Federico Urban, “è quindi quello di risolvere i problemi di oggi accompagnando le aziende verso l’adozione di tecnologie che saranno quotidiane nel prossimo futuro, sempre più pervaso dall’intelligenza artificiale”.
Prove stampo con tecnologia Mucell
Dalle 12.00 alle 13.00 circa, in concomitanza con i tour guidati all’interno dei laboratori e degli uffici di Proplast, si è infine svolta una sessione tecnico-pratica con la tecnologia MuCell, grazie ad Andrea Onnis, responsabile del laboratorio Stampaggio a iniezione di Proplast.
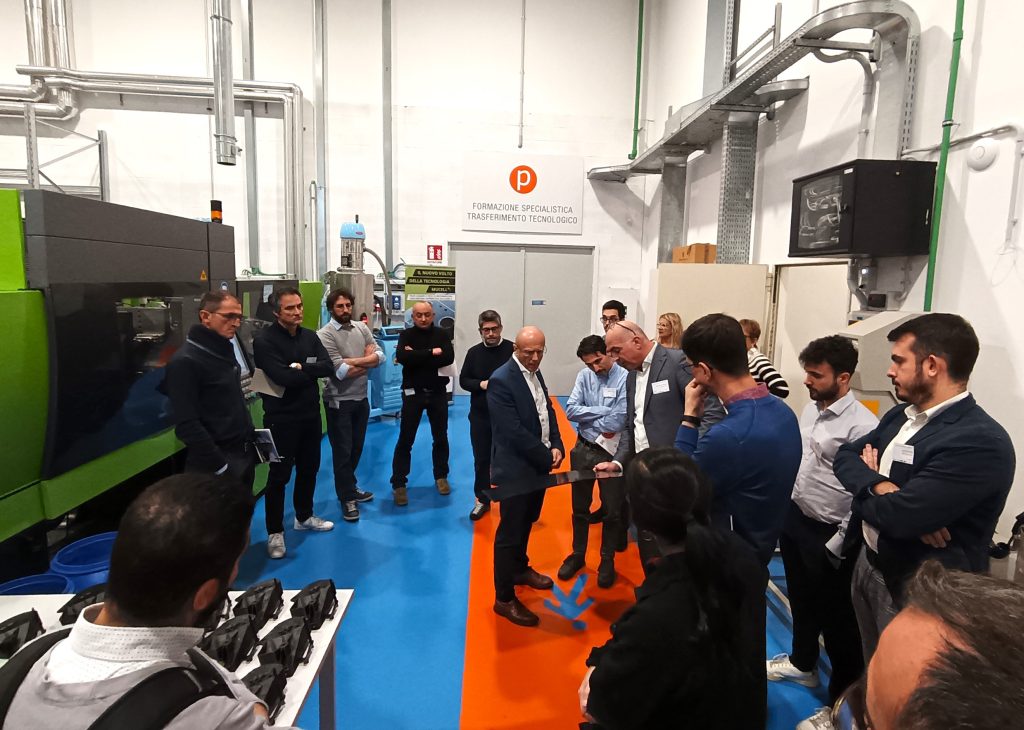
“Lo stampaggio con tecnologia MuCell offre vantaggi che partono da un diverso approccio rispetto allo stampaggio tradizionale”, ha spiegato Onnis. “Questa filosofia si traduce anche in un ciclo di stampaggio diverso e in alcuni criteri che risulta necessario osservare e seguire. Le velocità d’iniezione molto più elevate, ma con pressioni d’iniezione più basse, e l’assenza della fase attiva di mantenimento effettuata dalla macchina sono alcuni dei piccoli cambiamenti necessari per portare a termine questo stampaggio con tecnologia non convenzionale”.
“L’immissione di un gas, come l’azoto, comandata dall’operatore offre un margine di manovra per l’espansione fisica che è diverso e più ampio rispetto all’espansione chimica”, ha aggiunto Onnis. “Questo margine è un vantaggio per l’ottenimento del risparmio desiderato. Risparmio che, essendo dettato da diversi criteri, può avere differenti valori percentuali a seconda della base polimerica usata, del componente da stampare, degli spessori e della qualità meccanica, ma con il grande vantaggio di essere raggiunto sempre mediante lo stesso mezzo: l’azoto.
Tutto ciò rende possibile soprattutto l’alleggerimento del componente e un minore tempo di ciclo. Inoltre, grazie alla caduta della viscosità del polimero con l’azoto all’interno, si arriva anche a una riduzione della forza di chiusura, che può tranquillamente superare il 50%. Il tutto a vantaggio di un minor consumo energetico della macchina a iniezione e di una minor usura del gruppo di chiusura”.
“L’aspetto estetico dei componenti ottenuti con Mucell prevede solo un cambiamento a livello superficiale, chiamato effetto “silver streaks” (striature argentate)”, ha poi precisato Onnis. “Quest’ultimo, però, può essere eliminato con particolari tecnologie e/o lavorazioni, oppure semplicemente trascurato, per esempio nel caso di alcuni componenti sotto cofano, dove spesso è richiesta una qualità che l’utente finale non potrebbe osservare”.
“In Proplast, la competenza con MuCell dal lato del processo è decennale, annoverando esperienze con grandi aziende a livello nazionale e internazionale, su molteplici tipologie di componenti e materiali polimerici”, si è avviato a concludere Andrea Onnis. “Un’esperienza che, nel corso della giornata dimostrativa, ha portato a mettere in evidenza, per esempio, un risparmio del 16% in termini di peso del manufatto, ottenuto con il 23% di tempo in meno e risparmiando il 58% sulla forza di chiusura”.
Riccardo Ampollini