
Lo stampaggio di semiespansi strutturali attraverso la schiumatura fisica dei polimeri nello stampo – meglio conosciuto come MuCell – non è certamente una novità. Eppure, nonostante siano trascorsi quasi dieci anni dalle prime applicazioni industriali, la tecnica sembra aver trovato una nuova vitalità, che privilegia i comparti dell’automotive, dei componenti tecnici e dell’imballaggio, ai quali promette leggerezza senza pregiudicare la stabilità del manufatto.
A guidare la tendenza contribuisce indubbiamente il nuovo approccio strategico di Trexel (start-up del Massachussets Institute of Technology avviato nel 1995 per diffondere la tecnologia, NdR), che negli ultimi anni ha stretto accordi di collaborazione con i leader nella costruzione di presse a iniezione e messo in atto iniziative fortemente orientate alla promozione tecnica del sistema. Ma l’aspetto forse più interessante, dal momento che ogni tecnologia avanzata finisce inevitabilmente per scontrarsi con i risvolti economici, è che l’azienda statunitense ha deciso di abolire le royalty sulla produzione – poco gradite dai potenziali utilizzatori – e di mantenere una “one time fee” inclusa nel prezzo di fornitura dell’equipaggiamento.
La politica commerciale più dinamica non è però il solo driver. MuCell si è evoluto: oggi, l’integrazione del dosaggio del gas allo stato di fluido supercritico (SCF) nel controllo delle macchine a iniezione, i polimeri con formulazione specifica e gli stampi progettati appositamente permettono di raggiungere risultati migliori, più riproducibili. Insomma, più adeguati a garantire un processo industriale utilizzabile per le produzioni di grande serie.
I principi della tecnologia MuCell
Rispetto allo stampaggio a iniezione tradizionale, MuCell prevede l’iniezione di un gas (azoto o anidride carbonica) in condizioni supercritiche nel polimero all’interno del cilindro di plastificazione. La vite, grazie a una particolare configurazione del profilo, disperde finemente e in modo omogeneo il SCF nella massa fusa. La viscosità della soluzione così ottenuta è inferiore a quella del semplice polimero fuso, e quindi scorre più facilmente nello stampo.
Quando la soluzione gas-polimero arriva allo stampo, dove la pressione è minore rispetto al cilindro di plastificazione, il gas comincia a separarsi e ad espandersi, iniziano così a formarsi micro bolle. La velocità di espansione dipende dall’entità della caduta di pressione: tanto è elevata, quanto più sarà repentina. L’espansione del gas favorisce un più rapido riempimento della cavità dello stampo, perché, rispetto allo stampaggio tradizionale, qui il gas sostituisce il volume di materiale continuamente iniettato in fase di compattazione per compensare le contrazioni volumetriche del polimero in fase di raffreddamento. In pratica, non è necessaria la fase di post pressione, che viene sostituita dalla pressione interna del gas nel pezzo, che spinge il polimero contro le pareti dello stampo riempiendo l’impronta in modo uniforme, compresi gli angoli e i sottosquadri. Questo elimina le forti differenze di pressione e di temperatura tra il punto di iniezione e la fine del flusso, generando una struttura microcellulare omogenea nel manufatto, con stress e tensionamenti minori, ritiro uniforme in ogni punto della superficie e quindi un maggiore rispetto delle tolleranze.
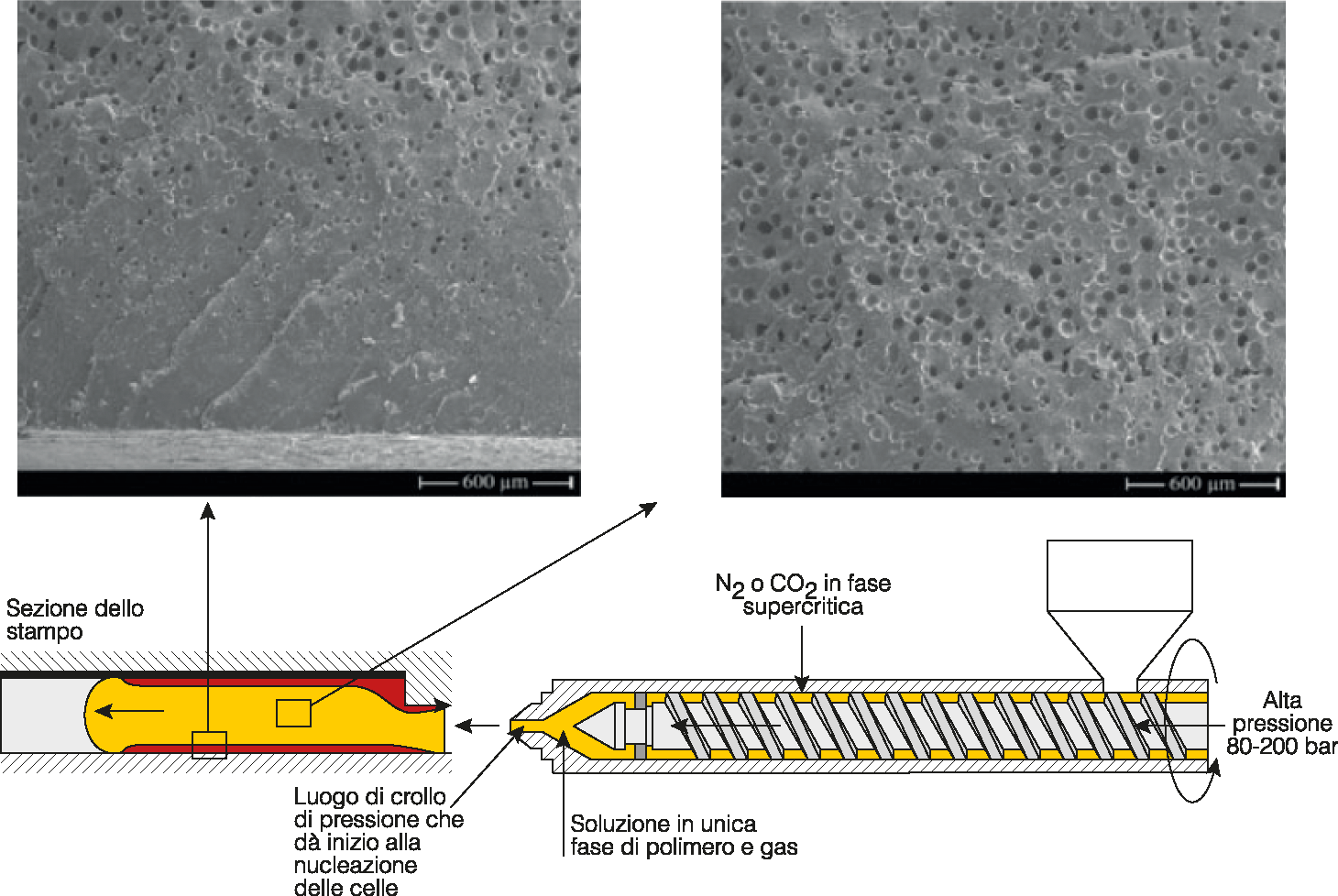
A destra, immagine dell’espansione al centro del corpo dello stampo
A sinistra, immagine dell’espansione vicino alla parete dello stampo
I vantaggi dell’espansione fisica
Il primo vantaggio di MuCell è facilitare le operazioni di stampaggio a iniezione rispetto al processo tradizionale, dove la difficoltà è far fluire il polimero, senza che si raffreddi, dal punto di iniezione fino al termine del riempimento della cavità dello stampo, e di compattarlo nel modo più uniforme possibile per ottenere un ritiro del pezzo uniforme (accrescendone così la stabilità dimensionale) e per evitare problemi di risucchio e le deformazioni. La riduzione della viscosità, che può arrivare anche al 30% (al 10-15% nei caricati con fibre di vetro), garantisce infatti una migliore fluidità del materiale, che scorre più velocemente riducendo il tempo di iniezione. Questo, unito al fatto che lo stampo può essere tenuto a una temperatura inferiore e che non c’è la fase di post pressione, contribuisce in modo significativo anche alla diminuzione del tempo ciclo, che può arrivare fino al 50%.

Inoltre, la maggior fluidità del fuso permette di operare a pressione minore, e quindi con forza di chiusura sensibilmente inferiore (fino al 50% in meno). Macchine più piccole risultano economicamente più accessibili, occupano meno spazio e consumano meno energia, tre fattori determinanti ai fini dell’efficienza del processo produttivo.
Anche l’espansione del gas nello stampo comporta parecchi vantaggi. Diminuiscono il peso del pezzo e la quantità di polimero necessario, dal momento che viene sostituito da micro-celle di gas che formano una struttura espansa e resistente, molto simile a quella delle ossa umane. Secondo sperimentazioni condotte da Trexel, le prestazioni migliori si ottengono con una riduzione del peso del 10%. Altra peculiarità, è possibile ottenere pezzi con pareti estremamente sottili (anche fino a 1 mm) e questo significa che, prevedendo già in fase di progettazione di realizzare un pezzo con MuCell, si riesce ad arrivare a una riduzione del peso di circa il 20%, alla quale va sommato il 10% che si ottiene per effetto dell’espansione.
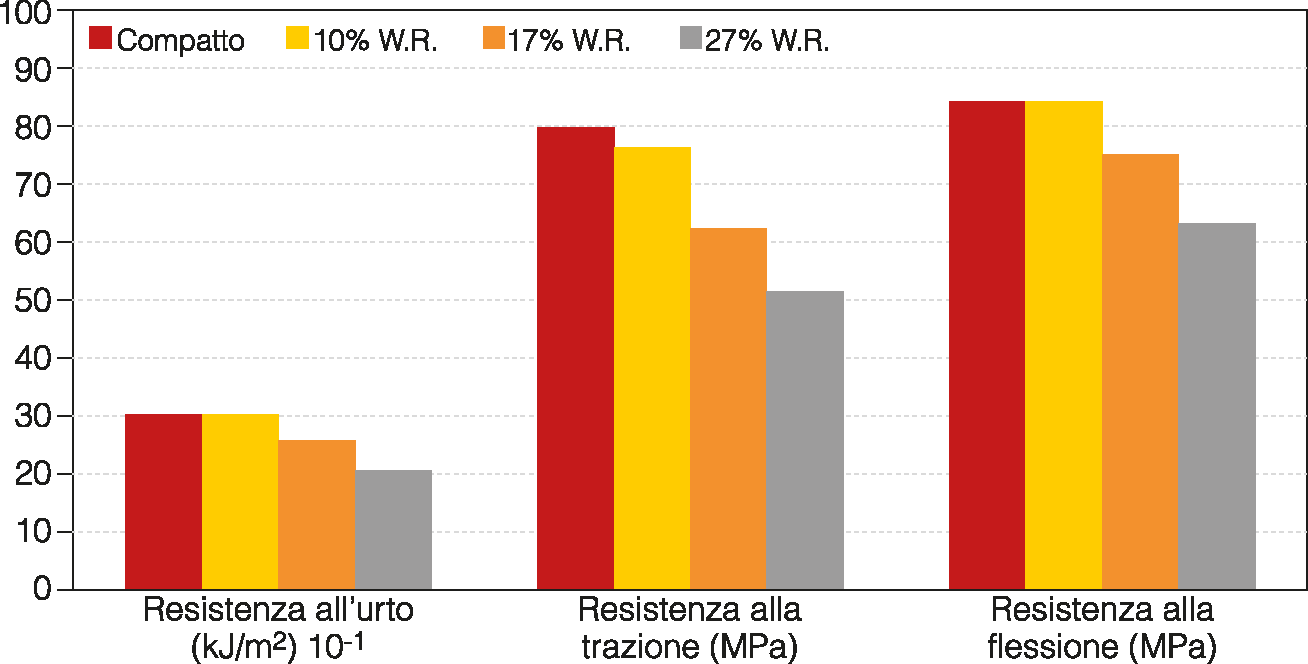
Un vantaggio per l’automotive
Leggerezza, riduzione dei consumi di materiale e di energia. Una combinazione decisamente interessante soprattutto per il settore automotive, dove la leggerezza è diventata il driver strategico. Obiettivo dei costruttori di veicoli è infatti una riduzione del peso delle vetture, variabile secondo le diverse case da 150 a 300 chilogrammi. Un traguardo che permetterebbe di compensare l’inserimento dei pesanti dispositivi di sicurezza del passeggero, ma anche delle batterie e del motore elettrico nelle versioni ibride.
Italia in recupero
In tutto il mondo, sono migliaia le applicazioni di MuCell in produzione nel settore auto, del packaging, e nello stampaggio di parti tecniche, macchine per ufficio e di componenti elettrici ed elettronici. In Italia ancora nessuna. È questa la ragione che ha spinto Trexel, in collaborazione con Engel Italia, a supportare l’installazione di un’isola dimostrativa del sistema MuCell al Consorzio Proplast di Rivalta Scrivia (Alessandria).
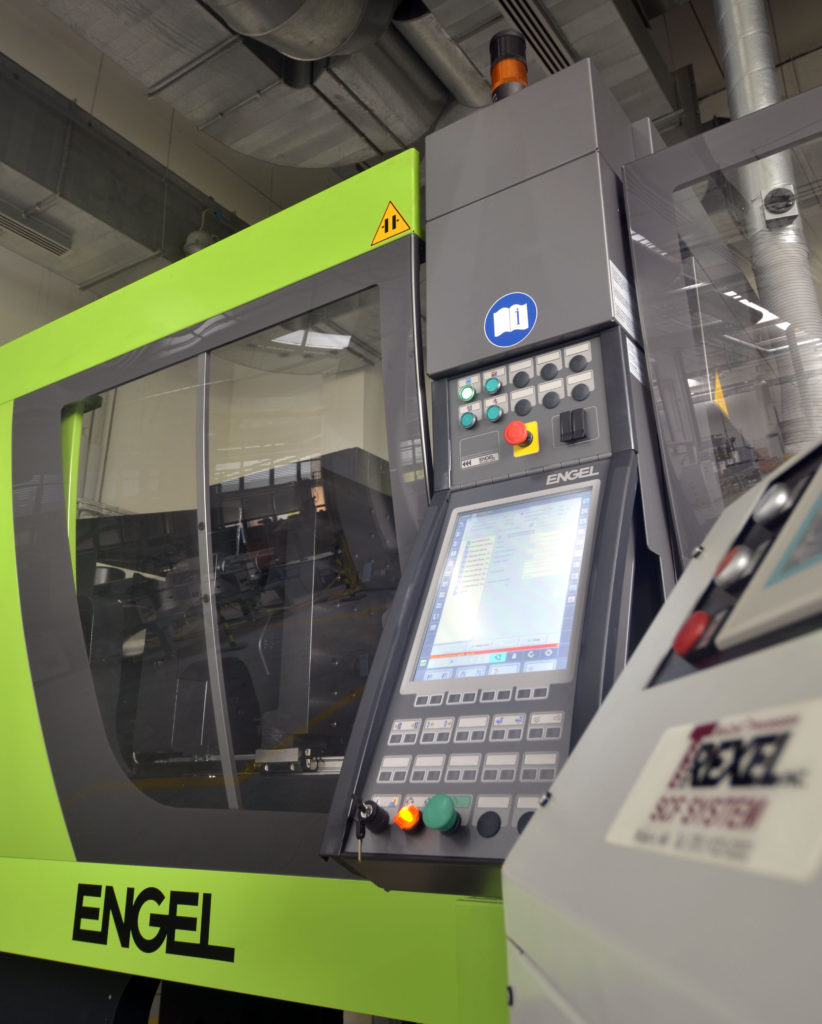
Qui gli stampatori italiani possono valutare le potenzialità applicative dello stampaggio a espansione, usufruire di un supporto – a livello consulenziale – alla simulazione di processo e strutturale FEM sul componente espanso, ma anche del trasferimento tecnologico. L’implementazione della tecnologia in azienda potrà quindi essere effettuata in tutta tranquillità, solo dopo averne verificato il funzionamento. Inoltre, grazie a un accordo recentemente siglato con RocTool, nei reparti del centro di ricerca alessandrino è installato un sistema heat&cool a induzione magnetica. Tra le ipotesi di ricerca c’è quella di abbinare l’induzione magnetica e MuCell; lo scopo è di ottenere pezzi più leggeri, stabili dimensionalmente e con aspetto superficiale ineccepibile, in altre parole i componenti in plastica ideali.