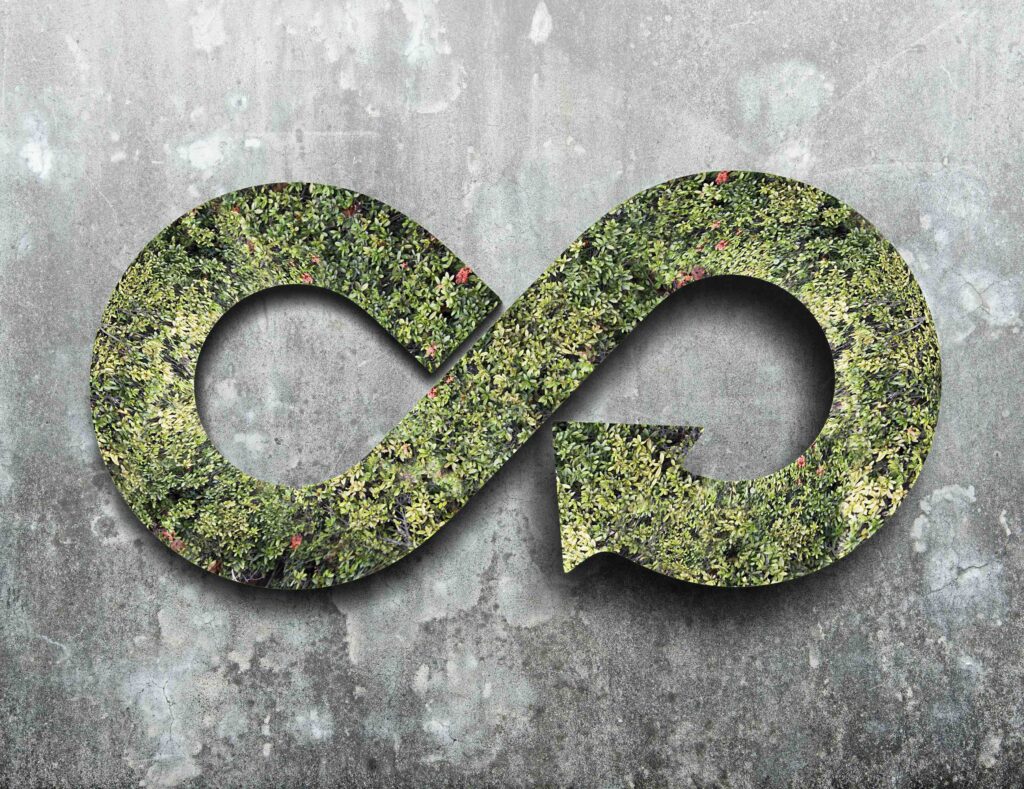
Sensibilità ambientale e crescente domanda di materiali più sostenibili, certamente, ma anche il timore di dover fare i conti in un futuro non troppo lontano con restrizioni e gabelle a carico di articoli in plastica monouso o materiali non riciclabili. Sono queste le motivazioni che stanno spingendo i grandi produttori di polimeri a impegnarsi direttamente in attività di riciclo, attraverso acquisizioni o, più frequentemente, alleanze strategiche, soprattutto laddove sia possibile sfruttare il valore aggiunto di avere in casa impianti di cracking, ovvero il riciclo chimico di rifiuti plastici misti.
C’è riciclo e riciclo
Attraverso trattamenti termici o termo-catalitici si possono ottenere dalle frazioni di plastiche miste, difficilmente riciclabili per via meccanica, oli o gas sintetici destinati a sostituire materie prime di origine fossile nei processi di produzione delle materie plastiche, ad esempio nel cracking al posto della nafta, senza passare per la depolimerizzazione, da cui si ottiene invece direttamente il monomero. Quindi, grazie al bilancio di massa certificato da terza parte – il più gettonato è ISCC Plus –, si possono allocare queste materie prime seconde nei prodotti finiti, anche dove la presenza di materiale riciclato non sarebbe possibile, come nelle resine trasparenti o in quelle ad alte prestazioni destinate alla produzione di articoli a contatto con alimenti. Materiale riciclato “attribuito”, quindi, e non necessariamente presente nel polimero venduto come “circolare”. Resta da capire come questo approccio potrà essere accolto dalle autorità a livello nazionale (dove la quota riciclata dei MACSI non sarà soggetta alla plastic tax italiana) o europeo, dove la tassa sulla plastica colpirà gli imballaggi non avviati a riciclo. Un’altra strada è la depolimerizzazione, fattibile tecnicamente e – probabilmente – anche economicamente qualora si parta da rifiuti omogenei per famiglia polimerica, soprattutto se facili da trattare, come il polistirene o il PET. Dal monomero si può tornare al polimero che possiede caratteristiche pari al vergine, senza necessità di un’attribuzione di terze parti.
Primi impianti in Francia
Dopo una prima e lunga fase di studi e ricerche, e una seconda volta a creare alleanze strategiche con l’obiettivo di costituire consorzi e filiere, incominciano a delinearsi i primi progetti concreti di riciclo chimico in Europa, che potrebbero trasformarsi in impianti nell’arco dei prossimi anni. Se la pirolisi è apprezzata soprattutto in Nord Europa, la Francia si candida a diventare l’hub europeo nella depolimerizzazione di rifiuti plastici e anche in Italia non mancano sviluppi interessanti. Due importanti produttori di resine stireniche, Trinseo e Ineos Styrolution, stanno collaborando da tempo, insieme ad alcuni partner tecnologici, alla depolimerizzazione di rifiuti di polistirene compatto ed espanso, materiale difficile da selezionare e recuperare per via meccanica. I due partner hanno anche scelto il sito dove costruire il primo impianto: Wingles, nel Nord della Francia, dove è presente un polo chimico di Ineos Styrolution. Il piano prevede di avviare l’unità nel 2023 con una capacità di trattamento pari a 50 tonnellate al giorno, ottenendo stirene monomero che verrà impiegato dai due produttori in modo indipendente per sintetizzare nuove resine stireniche, come parte dell’impegno preso di introdurre, in media, il 30% di riciclato nei materiali destinati al mercato europeo dell’imballaggio. Non è stata ancora scelta la tecnologia di processo tra quelle proposte da Agilyx e Recycling Technologies: la decisione sarà presa nei prossimi mesi in base a criteri come la qualità del monomero, la resa e la versatilità nel trattare diversi flussi di rifiuti in ingresso. Nei prossimi tre anni dovrebbe sorgere nel vecchio continente anche un impianto per la depolimerizzazione di PET, frutto di una joint-venture tra la statunitense Loop Industries e la francese Suez. Il progetto prevede la messa in marcia, nel 2023, di un impianto con tecnologia Infinite Loop capace di produrre oltre 80.000 tonnellate annue di PET rigenerato, con proprietà pari al vergine, partendo da feedstock ottenuti dal riciclo chimico di rifiuti di poliestere.
Sfrutterà invece un processo di riciclo enzimatico l’impianto – per ora dimostrativo – che la francese Carbios ha annunciato di voler costruire presso il sito Michelin a Clermont Ferrant, dove verranno trasferite anche le attività di ricerca e sviluppo. L’unità, non ancora su scala commerciale ma più di un “pilota”, sarà costruita da TechnipFMC ed entrerà in funzione a settembre 2021; l’obiettivo è di licenziare il primo impianto commerciale nel 2023. Rispetto al riciclo chimico – afferma Carbios – quello enzimatico utilizza meno calore, non avviene in pressione e può fare a meno di solventi, impattando così in maniera minore sull’ambiente.
Dai rifiuti olio per il cracking
Il riciclo chimico è anche nei progetti del gruppo francese Total, come parte della riconversione della raffineria di Grandpuits, nell’Ile-de-France, in una bioraffineria “zero-crude” con un investimento stimato in circa 500 milioni di euro nei prossimi quattro anni. Oltre al primo impianto europeo per acido polilattico (PLA), il nuovo polo green di Total ospiterà anche un impianto per il riciclo chimico di plastiche non altrimenti recuperabili, frutto di una joint-venture con Plastic Energy (che deterrà una quota del 40%): dai rifiuti si otterrà un olio di pirolisi (Tacoil), riutilizzabile come feedsotck per produrre nuove plastiche con caratteristiche pari al vergine, adatte quindi anche per produrre materiali a contatto con alimenti. L’impianto consentirà al gruppo francese di raggiungere l’obiettivo fissato al 2030 di produrre almeno il 30% dei suoi polimeri con materiali rigenerati.
La via italiana del riciclo chimico
Anche il nostro paese è in corsa per sfruttare il riciclo chimico di rifiuti plastici, seppur non vi siano per ora all’orizzonte unità su scala commerciale. Il primo progetto ha sede a Ferrara, dove al termine della pausa estiva LyondellBasell ha messo in funzione, presso il Centro Ricerche Giulio Natta, l’impianto pilota MoReTec per il riciclo di molecolare, mediante pirolisi catalitica, di rifiuti plastici post-consumo. Il processo è stato messo a punto insieme all’Istituto di tecnologia di Karlsruhe (KIT), partendo da catalizzatori proprietari sviluppati nel Centro Tecnologico di Houston (HTC). L’impianto, per ora su scala pilota, può trattare tra 5 e 10 chilogrammi l’ora di rifiuti plastici provenienti dalla raccolta differenziata urbana. Nei prossimi quattro anni verrà utilizzato per valutare l’interazione tra i vari tipi di rifiuti nel processo di riciclo chimico, testare e ottimizzare i sistemi di catalisi, verificare temperature di processo e tempi necessari per decomporre la plastica nelle molecole di partenza. Passi necessari per pianificare un impianto su scala industriale. Nel frattempo, presso i laboratori texani del gruppo si affinano i catalizzatori, si eseguono test sui prodotti di pirolisi e si valutano processi di post-trattamento volti a migliorarne la qualità, oltre a elaborare nuove tecniche analitiche per la caratterizzazione dei rifiuti plastici e dell’olio in uscita dall’impianto.
MoReTec è parte dell’impegno di LyondellBasell per la sostenibilità, con l’obiettivo di produrre 2 milioni di tonnellate annue di polimeri da riciclo o da rinnovabili entro il 2030, investendo nel recupero di plastiche e nella gestione dei rifiuti post-consumo. Rientrano nel piano anche l’ampliamento dell’offerta di materiali contenenti plastica riciclata, attraverso la joint-venture olandese Quality Circular Polymers, e la produzione di poliolefine contenenti materie prime rinnovabili; inoltre, LyondellBasell sta collaborando con trasformatori e utenti finali per migliorare la riciclabilità dei manufatti in materiale plastico.
Eni scende in campo con tre progetti
Al riciclo della frazione mista dei rifiuti, o plasmix, è interessato anche il gruppo italiano Eni, che sta lavorando su più fronti. Insieme a Corepla e Versalis (braccio chimico del gruppo) valuta il riciclo chimico, mediante gassificazione e pirolisi, di rifiuti da imballaggio in plastica difficili da separare e riciclare, come i film multistrato, oggi destinati in gran parte ai cementifici o al recupero energetico. Corepla fornirà il materiale da riciclare mentre Versalis metterà disposizione, una volta pronto, l’impianto per il riciclo chimico che sorgerà a Mantova, oggi in fase di progettazione, frutto di un accordo con la società italiana di ingegneria Servizi di Ricerche e Sviluppo.
Un secondo accordo, sottoscritto da Eni e Corepla, vuole verificare la fattibilità di produrre idrogeno e metanolo mediante gassificazione di plasmix a Porto Marghera e Livorno; progetto che coinvolge anche Maire Tecnimont, attraverso la consociata NextChem. L’intesa prevede inoltre l’estensione del programma RiVending per il riciclo delle palette e dei bicchierini da caffè in polistirene dei distributori automatici, che coinvolgerà uffici e siti industriali di Eni e Versalis.
Il gruppo energetico milanese è anche partner di NextChem per un terzo impianto, da realizzare all’interno della raffineria Eni di Taranto, destinato alla conversione in syngas di scarti plastici misti e combustibile solido secondario (CSS). Nell’agone è pronta a scendere anche un’azienda lombarda, Tregenplast, già attiva nella selezione e riciclo di rifiuti plastici, che ha ottenuto di recente l’autorizzazione a costruire e mettere in marcia un impianto di pirolisi da rifiuto, sperimentale ma di taglia industriale. Una volta avviato, tratterà rifiuti di matrice poliolefinica trasformandoli in un olio che, dopo un processo di distillazione, potrà essere convertito in carburanti o intermedi chimici.
Anche da pneumatici e materassi
Il riciclo chimico può risolvere anche i problemi di rigenerazione di materiali poco o per nulla recuperabili, oppure con un valore a fine vita scarso, da cui si può ottenere un feedstock dall’anima circolare.
BASF, ad esempio, sta avviando progetti per il recupero di pneumatici fuori uso e di imbottiti, al fine di sostenere il suo programma di riciclo chimico ChemCycling. Il gruppo chimico tedesco ha deciso di investire 16 milioni di euro nella connazionale Pyrum, titolare di un processo per la pirolisi di pneumatici fuori uso (PFU), già implementato in un impianto pilota a Dillingen (Germania) con capacità di 10.000 tonnellate annue, equivalenti a 2.500-3.000 pneumatici al giorno; unità che verrà ampliata con l’aggiunta di due nuove linee entro il 2022. Mediante la costruzione di nuovi siti con eventuali partner, Pyrum punta ad arrivare a produrre 100.000 tonnellate annue di olio di pirolisi, destinato a diversi impieghi finali. BASF aveva già siglato in precedenza un accordo di fornitura di olio di pirolisi da PFU con la società ungherese New Energy, destinato a divenire feedstock nella produzione di polimeri immessi sul mercato con il suffisso Ccycled, con approccio “mass balance” certificato.
Oltre ai PFU, l’interesse di BASF è rivolto ai poliuretani utilizzati nei materassi e imbottiture varie, oggi destinati a finire in discarica o nell’inceneritore. A Schwarzheide, in Germania, sono in corso prove su un impianto pilota alimentato con poliuretani flessibili, da cui si ottengono polioli idonei per un riutilizzo nella sintesi di nuovi poliuretani, quindi con approccio closed-loop. L’obiettivo dei test è ottenere materie prime con una qualità comparabile a quella dei polioli vergini. I primi lotti di rigenerato saranno consegnati ai partner del progetto entro la fine dell’anno per gli sviluppi applicativi, anche se ancora a un livello sperimentale.
Su questo fronte sta lavorando anche Dow Polyurethanes, che ha annunciato il passaggio alla fase industriale del programma Renuva per il recupero in closed-loop di materassi e imbottiti a fine vita. Un primo impianto sarà avviato l’anno prossimo in Francia presso la società Orrion Chemicals Orgaform.