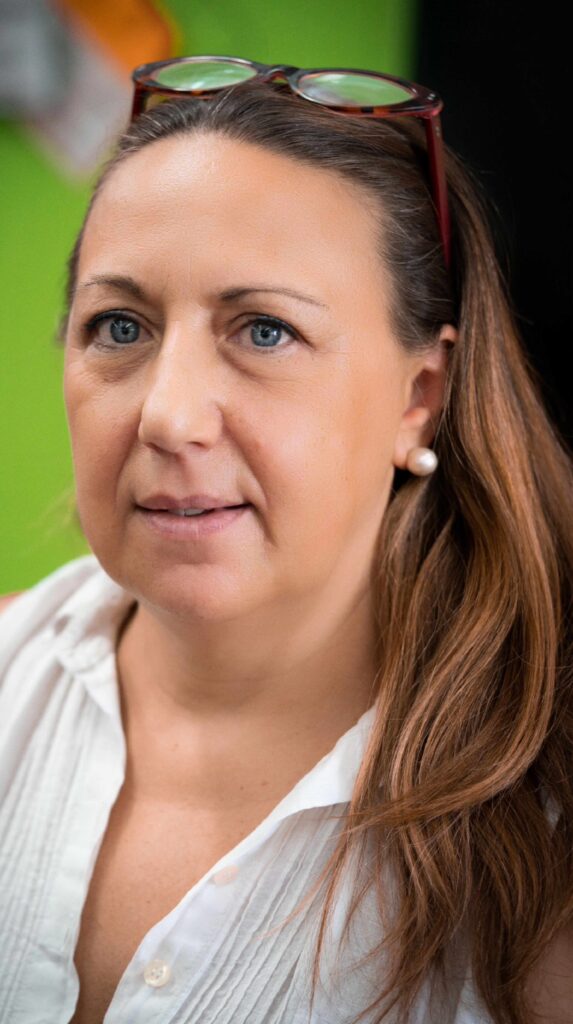
CB Costruzioni Brescianini è nata nel 1986 dall’intuizione di Davide Brescianini, l’attuale amministratore delegato, che apre la sua attività – letteralmente – nel cortile di casa, specializzandosi in servizi di cablaggio, prevalentemente per il settore automotive. Una veloce crescita porta al trasferimento in una nuova e più ampia sede a Pogliano Milanese (Milano), dove dal 1994 vengono approntate officina e reparto di stampaggio a iniezione. Brescianini, infatti, aveva iniziato a progettare e realizzare particolari plastici legati al mondo del cablaggio, prima migliorandoli seguendo la sua esperienza di utilizzatore e successivamente, in una logica di economia di scala, passando a produrli e commercializzarli. Una svolta per l’azienda che oggi può vantare una solida reputazione, collaborazioni con importanti brand internazionali e oltre dieci brevetti di sistemi di fissaggio, componenti elettrici e fascette riutilizzabili. Ma il reale cambio di passo arriva con una strip in plastica colorata che scrive nuove regole nel cablaggio delle vetture riducendo errori, danni ai cavi e consumo di materie prime. Ne parliamo con Clelia Petri, responsabile controllo e gestione dell’azienda che l’ha brevettata.
Come è nata l’idea di realizzare fascette riutilizzabili in plastica?
La nostra azienda è partner di un’importante casa automobilistica, una collaborazione storica, avviata negli anni Ottanta per lo sviluppo di cablaggi. È dal contatto diretto con chi fisicamente si occupava della produzione in catena di montaggio che Davide Brescianini ha ricavato gli spunti più interessanti per ideare e poi proporre le nostre fascette riutilizzabili, che si può dire siano nate direttamente dall’ascolto delle esigenze degli utilizzatori. Persone come i capo reparto che spesso non vengono coinvolti nei processi decisionali, ma che meglio di altri hanno un impatto diretto con le problematiche che sorgono in fase di lavorazione. La nostra prima fascetta è nata proprio da questi confronti diretti e, indubbiamente, ha contribuito a determinare il nostro successo.
Da quale esigenza siete partiti?
Quando abbiamo iniziato a produrre fascette riutilizzabili, nel 2004, ai principali brand dell’auto venivano forniti cablaggi fissati con nastri adesivi in carta per mantenerli in ordine durante il trasporto. Una situazione non certo ideale, che creava qualche difficoltà nelle operazioni in catena di montaggio e non di rado danneggiamenti alle parti elettriche legati alla rimozione dei fissaggi. La nostra prima fascetta venne percepita dal mercato come un prodotto fortemente innovativo, perché introduceva un concetto fino ad allora inedito per questa tipologia di prodotto: il riutilizzo. Prodotta in tre lunghezze, assicurava notevole capacità di tenuta anche in caso di grandi carichi e, al momento di posizionare il cablaggio, con una rapida operazione poteva essere sganciata facilmente. In più, abbiamo introdotto il concetto del colore, che di fatto ha generato uno standard nel settore. Oggi i cablatori identificano tutti i rami di destra con il verde, quelli di sinistra con il giallo, le mezzerie o i punti di snodo con il rosso. In tal modo le operazioni di posizionamento dei cavi sono più rapide e intuitive: il tempo di stesura del cablaggio di un’auto è infatti sceso da 5 a 1,5 minuti. Di fatto, una “semplice” fascetta colorata ha permesso una vera ridefinizione nelle linee di assemblaggio delle auto.
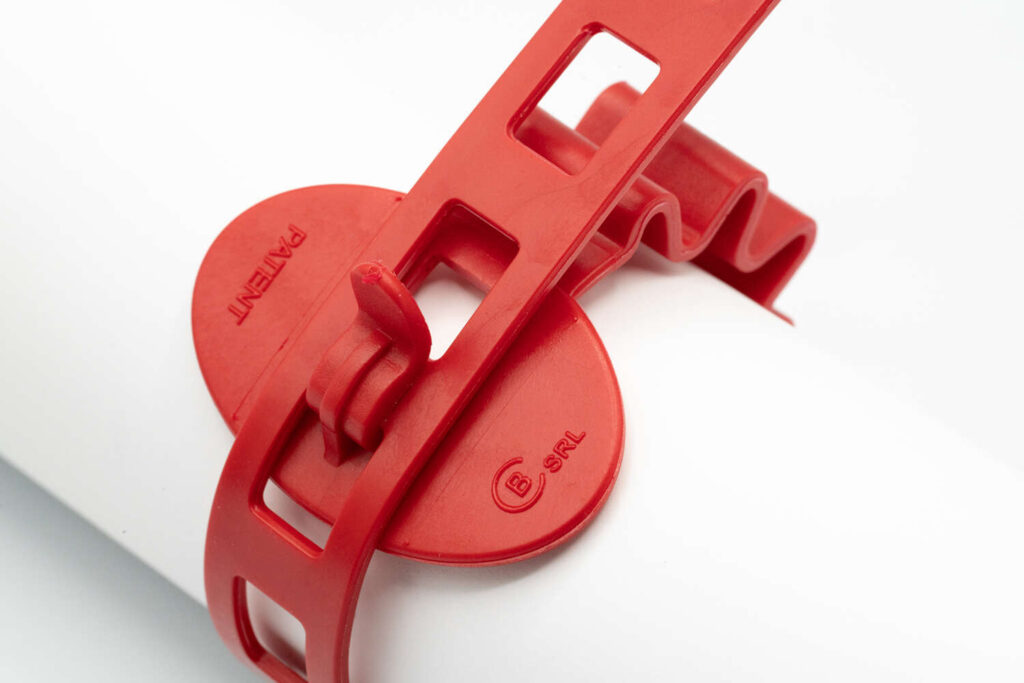
Il mercato vi ha premiati da subito?
Come spesso accade alle novità, partono in sordina, perché non basta sostituire un componente se non viene cambiata anche la mentalità, ma i vantaggi sono stati recepiti. Dopo la crisi del 2009, il mondo automotive è ripartito con grande slancio e questo per noi ha comportato un vero e proprio boom in termini di volumi. Pur producendo quella che di fatto è una commodity, abbiamo deciso di investire significativamente nei processi di fabbrica. Ci siamo quindi dotati di un moderno software di rilevamento delle non conformità, che si avvale della presenza di telecamere a bordo macchina e permette di evidenziare anche minime imperfezioni sull’ultimo punto di riempimento, che potrebbero causare difettosità all’anello della fascetta e conseguentemente inconvenienti nell’operazione di sganciamento. Al momento dell’apertura dello stampo, la telecamera effettua una lettura a pixel molto ingranditi su tutti i punti critici, scartando l’intera stampata in caso di anomalie, per garantire la massima qualità e fornire piene garanzie ai nostri clienti.
In fase di produzione adottate altri accorgimenti particolari?
Soprattutto per la fascetta più lunga, stampiamo con una centralina di sequenziamento della Yudo, riuscendo così a contenere il tempo ciclo e a migliorare la qualità. Stiamo sfruttando al massimo le potenzialità dei nostri stampi multimpronta su presse a iniezione Engel victory che, grazie all’assenza delle colonne, ci permettono di sfruttare l’intera area del piano portastampi. È quindi possibile utilizzare una macchina di tonnellaggio inferiore, ottenendo grandi vantaggi in termini di riduzione dei consumi energetici e dello spazio necessario nello stabilimento.
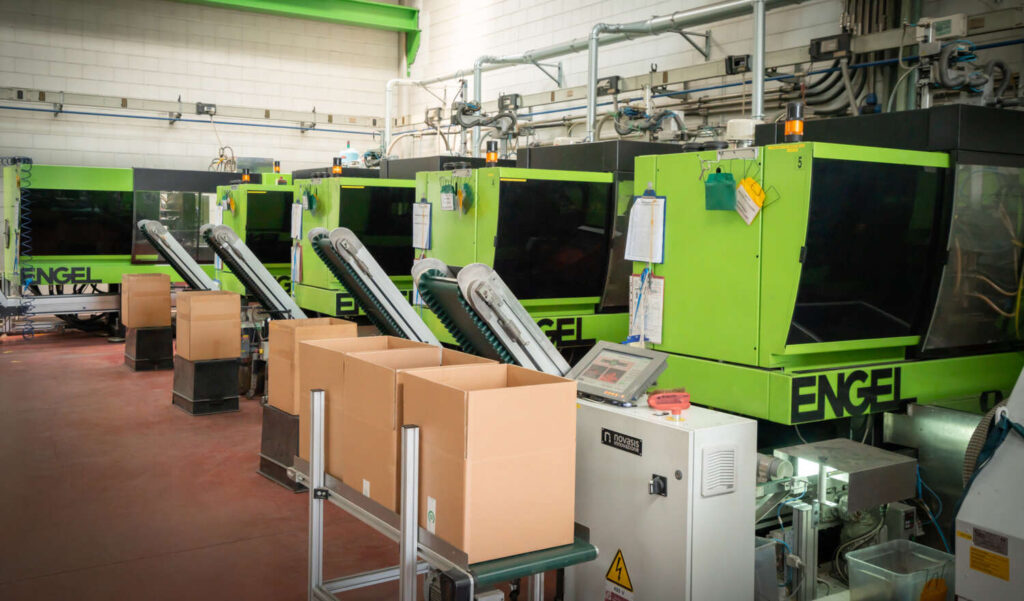

Le vostre fascette, nel tempo, hanno subito delle evoluzioni migliorative?
Con il forte rallentamento del settore auto, già evidente prima della pandemia, i grandi player hanno iniziato ad adottare politiche sempre più rigide in tema di contenimento dei costi. Consapevoli che le stesse avrebbero potuto mettere in discussione anche le forniture della nostra fascetta, abbiamo iniziato a lavorare a nuove soluzioni migliorative. Così, nel 2019 è nata BET, progettata e pronta per essere prodotta nel corso di soli tre mesi. È una nuova fascetta riutilizzabile brevettata, molto resistente e versatile, che si mostra come la perfetta risposta per ogni tipologia di impiego. Basta non porre limiti alla fantasia.
Quali sono le peculiarità di BET?
Vanta caratteristiche simili alla precedente fascetta ma ne migliora le prestazioni sotto molti aspetti, a partire dal peso, che è circa la metà. È prodotta in tre differenti misure e tre colori, e in fase progettuale è stato rivisto il funzionamento del meccanismo di aggancio, che rende ancora più agevole l’utilizzo e l’apertura e sicura la tenuta. Ha un’adattabilità millimetrica e può essere utilizzata per stringere oggetti di dimensioni molto ridotte o, se giuntata ad altre fascette BET, utilizzata per prese su volumi più ingombranti.
Siamo convinti che tutte queste caratteristiche, unite al concetto del recupero e riutilizzo, possano portarci a proporla anche a nuovi settori: nata per rispondere a esigenze dell’automotive, a nostro avviso ha potenzialità molto più ampie.
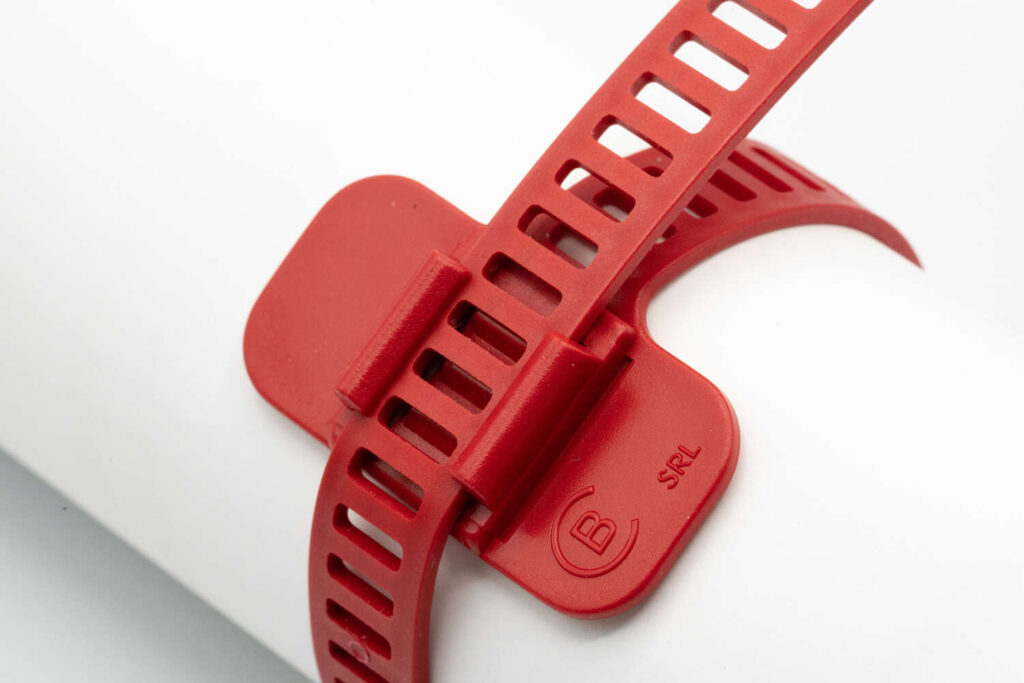
A quali settori applicativi state pensando?
La fascetta monouso ha ovviamente un senso in contesti nei quali deve garantire una perfetta tenuta nel tempo, ma il suo potenziale diminuisce negli impieghi temporanei perché, visto il costo ridotto, una volta utilizzata viene buttata, spesso anche nei rifiuti indifferenziati. Pensiamo ad esempio agli elettricisti che, dopo aver fissato provvisoriamente i cavi, le devono eliminare tagliandole con le forbici: una perdita di tempo e di materiale plastico. BET, invece, viene agganciata, sganciata e recuperata. Un altro settore che a mio giudizio potrebbe essere potenzialmente molto interessato è quello della viticoltura, dove BET può essere impiegata per operazioni di legatura vantando morbidezza ed elasticità. Anche le diverse colorazioni rappresentano un valore aggiunto: si può introdurre un metodo industriale nelle operazioni in vigna o, più semplicemente, differenziare le piante per segnalare particolari lavori da effettuare.
Stesso discorso per il florovivaismo e l’orticoltura, ma anche in numerosi altri campi in ambito hobbistico.
Questi prodotti possono essere realizzati anche con biopolimeri compostabili e plastiche rigenerate?
Abbiamo pensato alle bioplastiche per le applicazioni in agricoltura, ma al momento non abbiamo ancora trovato un prodotto che ci possa garantire le medesime prestazioni di flessibilità e tenuta. In merito all’utilizzo della plastica riciclata, riteniamo che sia un’opzione perseguibile ma con alcune difficoltà legate agli alti costi e alla scarsa disponibilità di polimero da post consumo o post industriale. Stiamo comunque valutandone l’utilizzo soprattutto per la fascetta BET e per i mercati nei quali questa scelta può essere vista come un valore aggiunto.
BET, la vostra principale novità, ha dovuto subito fare i conti con la crisi dovuta alla pandemia…
Quando, a partire da settembre dell’anno scorso, arrivavano i primi segnali di ripresa, i mercati sono decollati con una tale schizofrenia da costringerci ad accantonare ogni considerazione relativa a scelte strategiche e di visione per seguire i clienti con una flessibilità quasi ossessiva. Non solo l’economia si rimetteva in moto, ma cambiavano profondamente certe dinamiche, con molte aziende che hanno ripensato le strategie di reshoring. Ci siamo subito resi conto che stavamo raggiungendo i nostri limiti di capacità produttiva proprio quando tutti i segnali erano di un ulteriore aumento della domanda. Prendere tempo o peggio rifiutare richieste avrebbe potuto rivelarsi controproducente e per questo abbiamo colto l’occasione per rilevare due capannoni adiacenti la nostra sede, che ci consentiranno di raddoppiare la superficie produttiva ma soprattutto di riorganizzare il layout di fabbrica, dedicando una delle nuove aree allo stoccaggio delle materie prime e dei prodotti finiti. Liberiamo spazio per ospitare potenzialmente quattro nuove presse a iniezione. La prima è arrivata da pochi mesi e ci sta già consentendo di aumentare la nostra capacità produttiva.
Come siete organizzati attualmente?
L’organico conta dieci addetti altamente specializzati. Questo per una scelta precisa, frutto di un percorso che abbiamo intrapreso nel 2009, coinciso con il mio arrivo in azienda. L’obiettivo era costruire un’organizzazione con carattere industriale più marcato, finalizzata a ottimizzare i flussi di lavoro ma anche a valorizzare al meglio ogni figura presente. Il tutto, partendo da un’analisi di processo che mettesse il controllo dei dati al centro delle nostre strategie per migliorare le performance. Una scelta netta e di fatto obbligata, lavorando per settori nei quali è sempre più difficile agire sull’elemento prezzo, sia dei nostri prodotti sia in fase di trattativa d’acquisto delle materie prime.
Abbiamo quindi puntato a eliminare i processi inutili, introducendo un alto livello di automazione che ci ha permesso di standardizzare produzione e qualità, ma anche di attribuire un ruolo preciso alle risorse umane in base all’attitudine e al know-how, puntando su specializzazione e responsabilizzazione. Abbiamo poi progressivamente abbandonato i lavori diretti di cablaggio.
Un cambiamento radicale, quindi…
Di fatto, si sono modificati gli equilibri: mentre anni fa l’azienda era più concentrata su attività manuali oggi abbiamo potenziato la produzione, l’officina e il servizio, anche perché nel frattempo i nostri mercati esteri sono saliti dal 10 all’80% del nostro business.
L’automazione ha letteralmente salvato l’azienda. Se non avessimo effettuato questa scelta a monte, quando nel 2016 i mercati ci hanno chiesto di triplicare i volumi produttivi, non avremmo potuto far fronte a un simile cambio di passo. Ma eravamo pronti, anche grazie alle proiezioni che avevamo accuratamente effettuato negli anni precedenti, proprio per prepararci a un sensibile aumento delle richieste e per capire se tutti gli investimenti sarebbero stati ripagati. È stata la decisione giusta: la razionalizzazione dell’azienda ci ha permesso di risparmiare e generare nuovi investimenti per oltre due milioni di euro.
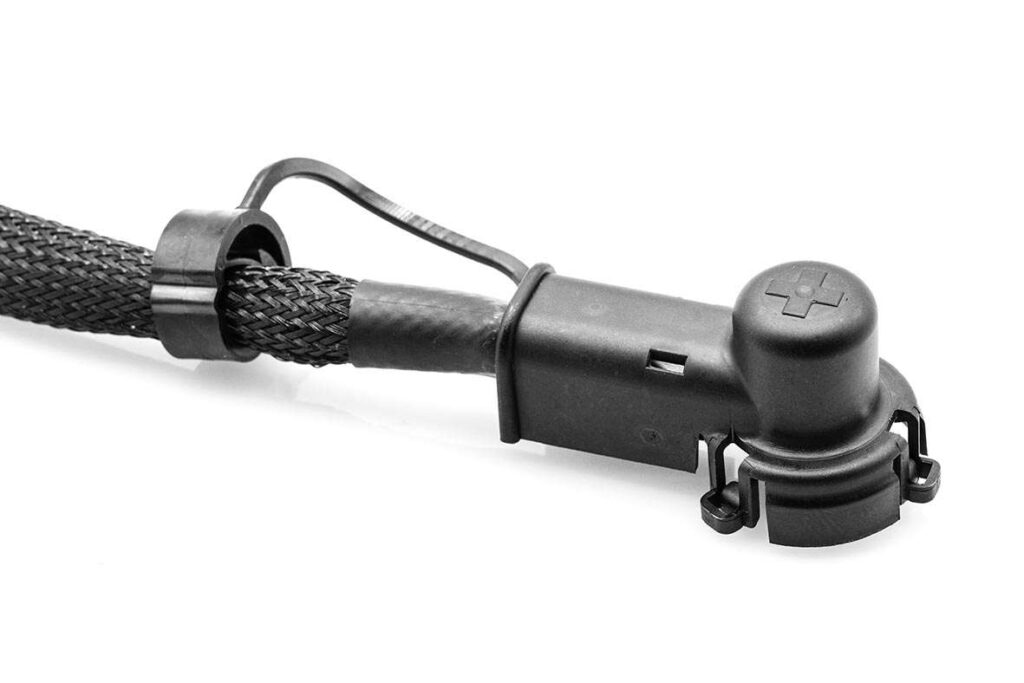
Da cosa deriva la scelta di abbandonare il cablaggio?
Si tratta di un lavoro complesso, che richiede molte operazioni manuali e conseguentemente alti costi di manodopera, oltre a un magazzino con un numero elevato di parti da gestire. Avremmo potuto ridurre i costi scegliendo di delocalizzare ma abbiamo preferito cercare, credo con un’etica che ci è stata riconosciuta, di accompagnare i clienti in una transizione che li mettesse in contatto con altre aziende, abbandonando progressivamente le grandi forniture e mantenendo solo, in un’ottica di ricerca e sviluppo, diverse preserie.
Quali altre scelte migliorative avete effettuato?
Il potenziamento dell’officina è funzionale al lavoro di stampaggio: ci permette di essere sempre più performanti grazie alla manutenzione interna degli stampi, ma anche di migliorare il servizio al cliente. Oggi siamo in grado di seguire lo sviluppo di un prodotto dalla progettazione alla costruzione dello stampo, alla prototipazione fino allo stampaggio. Una scelta che riteniamo indovinata. Nel tempo, infatti, sono aumentate le collaborazioni virtuose proprio con aziende per le quali produciamo conto terzi, che scelgono di rivolgersi a noi fin dalla progettazione dello stampo, in un percorso che ci permette di condividere idee e criticità da risolvere in tutte le fasi che portano alla realizzazione del manufatto finito, compresa l’analisi del suo impatto ambientale.
Quali sono i prossimi passi?
Credo che i tempi siano maturi per comunicare non solo un prodotto, ma il valore dell’azienda che lo realizza. Questo significa lavorare a un miglioramento del marketing e della comunicazione, presentandoci a mercati consolidati ma anche esplorandone altri, nuovi, a cui potremmo essere utili. Già a partire da quello che conosciamo meglio, il settore automobilistico, rivolgendoci non solo ai grandi player ma anche al mondo dei concessionari e delle officine, così al comparto degli elettrodomestici, che ha svariati altri campi di applicazione dei nostri prodotti. Ma, soprattutto nei confronti di chi ancora non ci conosce, dobbiamo essere in grado di presentare un marchio, una storia e un saper far vedere ciò che siamo in grado di realizzare. Pensiamo di essere bravi a farlo, dovremo esserlo altrettanto a dirlo.