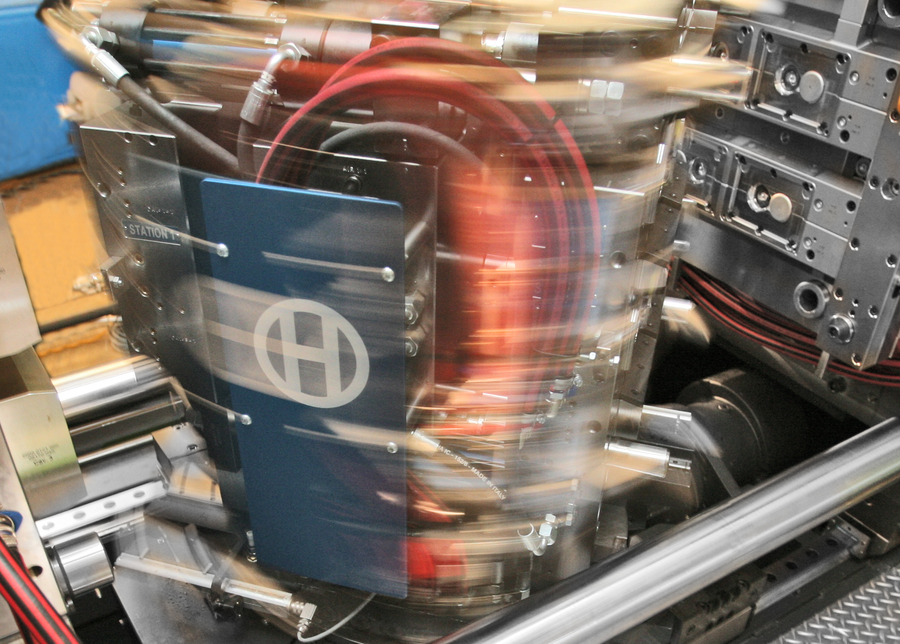
Oltre ad assicurare una sensibilità più elevata ai sistemi meccanici, i servomotori elettrici permettono di operare con una precisione maggiore e migliori possibilità di controllo, potenzialità che spesso aprono la strada a nuove funzioni. Quando si parla degli azionamenti elettrici delle macchine a iniezione, generalmente si fa riferimento ai tre movimenti principali – chiusura dello stampo, plastificazione e iniezione –, trascurando il contributo alla produttività che potrebbe derivare dall’adozione di azionamenti elettrici anche per i movimenti secondari, come quelli di tavola rotativa, estrattori e nuclei di trazione a comando elettrico. Mentre alcuni fornitori tecnologici hanno già implementato sistemi elettrici per i movimenti di potenza, o almeno li forniscono come optional, per i movimenti secondari la strada sembra ancora lunga.
È appunto questo l’aspetto che verrà trattato nel seguito.
Le potenzialità delle tavole rotative elettriche
Le tavole rotative servo-elettriche offrono grandi potenzialità di miglioramento, soprattutto per il fatto che eliminano i fermi meccanici, riducendo quindi i tempi di rotazione generalmente legati al diametro della tavola e al peso dello stampo. Se l’unità di controllo della pressa rileva automaticamente il peso e l’eventuale errore di posizione dello stampo dopo ciascun cambio stampo, è anche in grado di regolare in maniera accurata il movimento della tavola rotativa sulla base delle condizioni operative esistenti (sistema brevettato in Austria). Nella maggior parte dei casi, questa regolazione riduce ulteriormente il tempo di rotazione (figura 1).
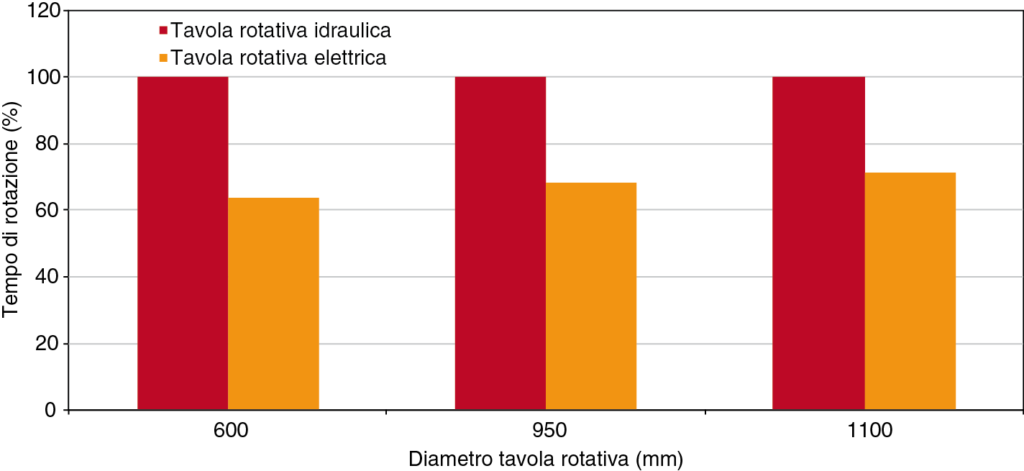
Maggiori velocità di rotazione e tempi di ciclo più brevi richiedono anche una più elevata precisione di posizionamento. Tuttavia, a meno che non vengano impiegate tecniche di posizionamento intelligenti, le compensazioni vengono effettuate in tempi troppo lunghi anche a causa degli attriti, facendo perdere, di conseguenza, il controllo della dinamica della rotazione. Una soluzione a questo problema consiste nel ricorso a un ciclo di apprendimento seguito da un movimento estremamente veloce per fissare l’esatto valore di impostazione. Ciò consente di compensare il gioco meccanico oltre che le deviazioni dai valori di temperatura all’interno dello stampo e l’usura dei perni di guida (figura 2). Dopo la regolazione, la deviazione massima si attesta a circa 0,1 millimetri sulla circonferenza della tavola rotativa.
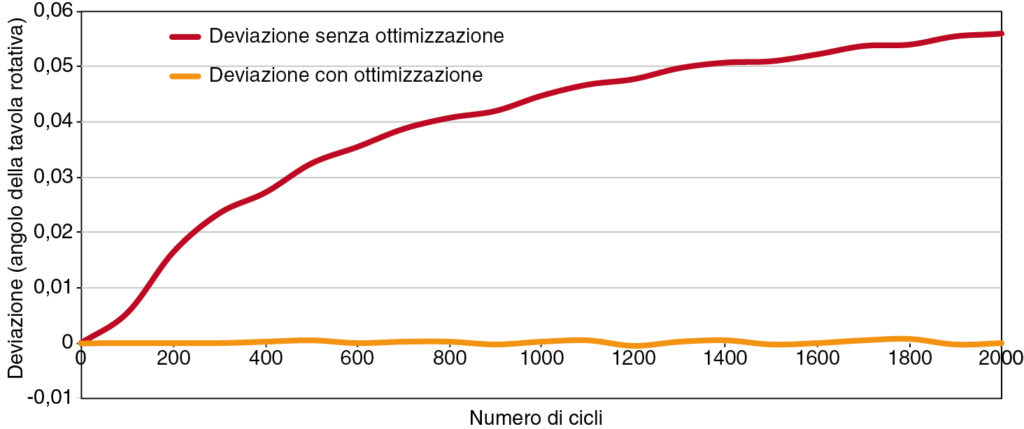
In sintesi, l’utilizzo di tavole rotative a servomotore elettrico assicura quattro vantaggi principali rispetto ai sistemi idraulici:
• tempi di ciclo più brevi;
• maggiore precisione di posizionamento;
• minore usura;
• controllo più flessibile del processo.
Dal momento che i dispositivi di ottimizzazione sono incorporati nel sistema di controllo della macchina, l’operatore non deve effettuare ulteriori interventi di regolazione. Al contrario, dopo il cambio stampo il sistema di controllo utilizza i valori di velocità, accelerazione e coppia motore per calcolare automaticamente le rampe di accelerazione e decelerazione ideali, necessarie per controllare il movimento della tavola rotativa. Questi strumenti di ottimizzazione, che equipaggiano di serie tutte le presse elettriche, sono disponibili per tavole rotative sia orizzontali che verticali dei tipi finora montati soprattutto sulle presse di tonnellaggio elevato.
Estrattori elettrici ad alta sensibilità
A causa dell’elevata precisione dei movimenti e del controllo accurato della corsa, gli estrattori ad azionamento elettrico offrono grandi spazi di ottimizzazione del processo, spazi ancora oggi parzialmente inesplorati dal punto di vista operativo.
In presenza di estrattori idraulici, gli operatori spesso aggiungono deliberatamente alcuni decimi di millimetro al punto di arresto impostato al fine di assicurare l’effettivo raggiungimento della posizione di fine corsa meccanica. Questa procedura va evitata in caso di estrattori elettrici, in quanto eventuali movimenti meccanici non previsti potrebbero causare l’usura prematura delle viti a ricircolazione di sfere. Di conseguenza, proprio come succede con i veicoli dotati di sensori di parcheggio, quando si utilizzano gli estrattori elettrici, il sistema di controllo determina l’esatta corsa dell’estrattore mediante contatti mirati tra i componenti meccanici per scongiurare la possibilità di movimenti indesiderati. Il fine è essenzialmente quello di estrarre completamente i pezzi dallo stampo in un solo colpo.
Nonostante l’utilizzo dei servomotori elettrici, alcuni movimenti di estrazione necessitano di un arresto meccanico, e quindi viene offerta l’opzione di disabilitare l’impostazione automatica della posizione di fine corsa. In ogni caso, la forza di arresto viene ancora monitorata in continuo, in modo tale da evitare carichi eccessivi sul sistema anche durante l’espulsione. Questa eventualità viene comunque impedita dall’elevata precisione del movimento e dal sistema di controllo intelligente.
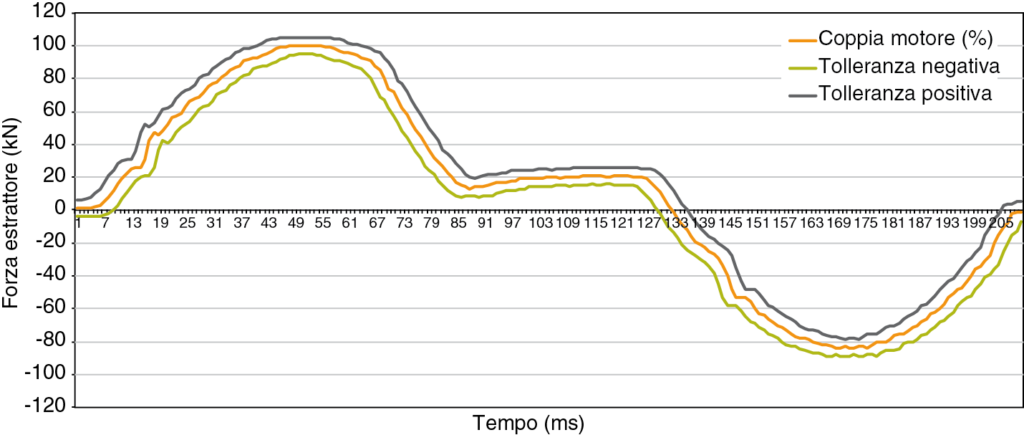
Il pacchetto software salvastampo AutoProtect (figura 3) sviluppato e brevettato da Engel garantisce un’ulteriore margine di affidabilità. Il sistema confronta i parametri di processo preimpostati (curve di valori impostati) da stampata a stampata, e monitora il processo entro limiti di tolleranza predefiniti. In caso di deviazione, la macchina si ferma e viene emesso un segnale d’allarme. Questa soluzione permette di proteggere in maniera affidabile anche gli stampi più delicati. Inoltre, consente all’operatore di rilevare tempestivamente l’usura dello stampo ed eventuali danni alla catena cinematica della macchina. Un aspetto particolarmente importante per l’operatore è dato dal fatto che il sistema funziona in auto apprendimento. Rispetto a un’impostazione convenzionale, il limite per l’arresto di emergenza impostato da un programmatore esperto è più elevato di quello impostato dal sistema salva stampo. AutoProtect quindi è più sensibile rispetto all’operatore umano.
Una tipica applicazione in cui la forza dell’estrattore di solito non è sufficiente a rimuovere i pezzi raffreddati dallo stampo è rappresentata dalla produzione di capsule per le bottiglie di bevande. Proprio per questo segmento, Engel offre una funzione boost per gli estrattori elettrici di una certa dimensione, originariamente sviluppata per gli estrattori a comando idraulico. La funzione boost consente al motore di superare temporaneamente il suo limite operativo massimo. Dopo avere attivato manualmente la funzione, il motore gira alla coppia massima per un periodo di tempo definito con precisione. Al fine di proteggere tutti i componenti meccanici ed elettrici, la funzione boost può essere avviata solamente se la temperatura del motore è inferiore a un certo limite e se sono stati osservati i tempi di fermo che dipendono dalla temperatura. Il sistema provvede a monitorare automaticamente anche queste condizioni.
Una delle altre funzioni intelligenti consentite dagli estrattori elettrici è il movimento di contrasto controllato. Di conseguenza, quando si usa una piastra index, è possibile servirsi del movimento dello stampo al posto della ritrazione attiva dell’estrattore. Questa soluzione impedisce che i pezzi vengano sfilati dall’estrattore durante la corsa di ritrazione.
In alcuni casi, l’estrattore può anche fungere da punzone di coniatura. Dal momento che la forza dell’estrattore è minore rispetto alla forza di chiusura della pressa, solo una parte della superficie del pezzo viene effettivamente coniata. Gli estrattori ad azionamento elettrico hanno il vantaggio di offrire le funzionalità di un punzone di coniatura convenzionale senza bisogno di installare componenti aggiuntivi. Per esempio, la coniatura può iniziare in parallelo con l’iniezione, e i profili di velocità o forza possono essere gestiti in circuito aperto o chiuso.
È possibile chiarire meglio le potenzialità del sistema attraverso un caso reale. In una particolare applicazione era essenziale che il pezzo avesse una superficie piana: mentre lo stampaggio a iniezione convenzionale dava un errore di planarità di circa 320 micron, la coniatura con l’estrattore ha ridotto l’errore a meno di 15 micron.
Radiali elettrici: spesso ancora una sfida
Per accrescere la precisione di posizionamento dei radiali, e soprattutto per assicurare un controllo in circuito aperto o chiuso in relazione alle necessità, sono disponibili varie tipologie di martinetti radiali ad azionamento elettrico. I diversi modelli si differenziano essenzialmente per l’interfaccia tra lo stampo e la macchina a iniezione, oltre che per la modalità di comando:
• il martinetto radiale elettrico è collegato mediante un’interfaccia Euromap 74. In questo caso, dalla macchina vengono trasmessi solamente i segnali di controllo (movimento, avvio, arresto) quindi lo stampista è responsabile della programmazione del sistema di controllo;
• il sistema di controllo viene programmato e regolato dal costruttore della pressa. A questo riguardo, il sistema di controllo viene fornito incorporato nell’unità in modo tale da risparmiare spazio e costi, oppure si installa un sistema di controllo indipendente che può essere utilizzato in maniera flessibile anche per altri stampi. Attualmente si privilegia la soluzione integrata, di conseguenza i costruttori delle presse tendono a diventare fornitori di sistemi.
A prescindere dal modello, Engel offre tutti i martinetti radiali anche in versione a comando elettrico. La registrazione dell’encoder tra il motore e il sistema di controllo a circuito chiuso è particolarmente importante in questo contesto.
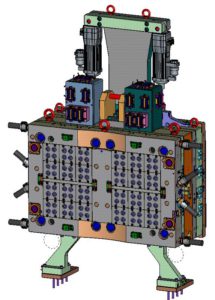
Fra tutti i movimenti secondari, i martinetti radiali elettrici oggi rappresentano la sfida più ardua per la conversione dalla tecnologia idraulica (figura 4). La definizione dell’applicazione con lo stampista è resa difficile dalla grande varietà dei modelli sul mercato e dal fatto che spesso il carico totale non è noto. Ma il passaggio alla tecnologia elettrica è solo questione di tempo. La superiore precisione e flessibilità dei martinetti elettrici assicurerà senz’altro il loro successo a lungo termine.
Movimenti sincronizzati per processi altamente integrati
I servomotori elettrici offrono un grande potenziale anche nel campo del sincronismo dei movimenti, come per esempio nel caso degli stampi a cubo rotativi in cui la tavola rotativa e il piano di chiusura si muovono in maniera indipendente l’uno dall’altro. I servomotori consentono di sincronizzare in tempo reale i vari movimenti, incrementando da un lato le prestazioni dinamiche e garantendo, dall’altro, la precisione e la riproducibilità necessarie per le applicazioni specifiche.
La produzione di tubetti in plastica per cosmetica e alimenti su di una pressa a iniezione Engel e-motion illustra chiaramente questo potenziale (figura in apertura). I tubi pronti per l’uso già muniti di etichetta (metodo IML) e completi tappo flip-top in bicomponente vengono prodotti in un unico ciclo con uno stampo a cubo rotativo. In questa applicazione, la tavola rotativa e il piano di chiusura dello stampo si muovono in maniera indipendente l’uno dall’altro. La tecnologia dei servomotori elettrici consente il controllo sincronizzato dei movimenti e offre la precisione necessaria per assicurare la qualità del prodotto e alte prestazioni dinamiche.
I comparti più attivi
A prescindere dalla tecnologia, sia essa idraulica, elettrica o ibrida, la scelta della pressa a iniezione presume un’analisi approfondita dei requisiti dell’applicazione e delle condizioni operative, oltre che un attento studio delle prestazioni offerte dai vari tipi di azionamento.
In futuro i movimenti secondari servocomandati diventeranno sempre più importanti man mano che i trasformatori si accorgeranno dei vantaggi che sono in grado di assicurare. Ciò nonostante, sarà necessario ancora del tempo prima che le varie difficoltà di ordine pratico vengano superate e che le soluzioni elettriche per i movimenti secondari si consolidino definitivamente sul mercato. Quando ciò accadrà, saranno i costruttori di stampi a dover affrontare la sfida più ardua, perché, in generale, dovranno attrezzarsi in modo specifico per soddisfare i nuovi requisiti imposti dai servomotori elettrici. Nel frattempo, per i costruttori di macchine a iniezione diventerà sempre più urgente rispondere alla crescente richiesta di soluzioni integrate da parte dei clienti.
Il ritmo al quale avverrà il passaggio alla tecnologia elettrica per i vari movimenti secondari delle presse a iniezione è diverso da settore a settore. In questa direzione, i comparti medicale e del packaging si sono dimostrati i più attivi.