Piccoli lotti, un’ampia gamma di materiali e colori differenti, oltre a frequenti cambi stampo, ostacolano l’obiettivo di ottenere bassi costi unitari. Secondo Paolo Chiarabaglio, CEO di Zeca, si tratta di problemi riconducibili a un “mercato inefficiente”. La sua azienda ha accettato quindi la sfida di rafforzare la propria competitività grazie alla produzione interna e soprattutto all’utilizzo di soluzioni complete di stampaggio da un unico fornitore: Wittmann
Sembrano “fatte con lo stampino”. Questo è ciò che viene in mente osservando le otto presse a iniezione Wittmann, di diverse tipologie ma ben allineate tra loro, installate nello stabilimento produttivo di Zeca, a solo mezz’ora d’auto da Torino. Tutte le macchine sono sistematicamente equipaggiate con attrezzature ausiliarie e robot, anch’essi prodotti da Wittmann, e, dopo l’ultima pressa, è presente una grande unità centrale per l’essiccazione e il trasporto dei granuli plastici.
Uno sguardo al monitor centrale del reparto rivela che anche la digitalizzazione è parte integrante della “scena”. Le isole di stampaggio sono tutte collegate in rete tramite connessioni Wittmann 4.0 e integrate in Temi+: il sistema MES sviluppato dall’italiana Wittmann Digital per il Gruppo Wittmann. “I nostri clienti rimangono colpiti quando vengono a visitare il nostro stabilimento produttivo”, afferma con orgoglio Paolo Chiarabaglio, il quale, insieme al fratello Marco, gestisce quest’azienda quasi centenaria, giunta ormai alla sua quarta generazione di proprietari. “Presentiamo ai nostri clienti uno stabilimento pulito e moderno, dove tutto si adatta perfettamente ai colori scelti per i reparti. Sono sicuro che le persone lavorino con maggiore motivazione in un ambiente così bello”.
I colori Zeca, giallo, grigio e nero, sono quelli dominanti anche nei pezzi stampati a iniezione che scorrono sui nastri trasportatori. L’azienda è specializzata in attrezzature per le officine dei professionisti, ma pure per i laboratori del “fai da te”, nonché in stazioni di ricarica per i veicoli elettrici. I sistemi avvolgicavo e avvolgitubo sono tra i suoi articoli più noti. In Italia, il marchio Zeca si è affermato ormai da tempo come sinonimo dell’intero gruppo di prodotti. “Ogni volta che le persone hanno bisogno di un avvolgitore, entrano in un negozio e chiedono uno Zeca”, racconta Chiarabaglio.
Qualità e costi completamente sotto controllo
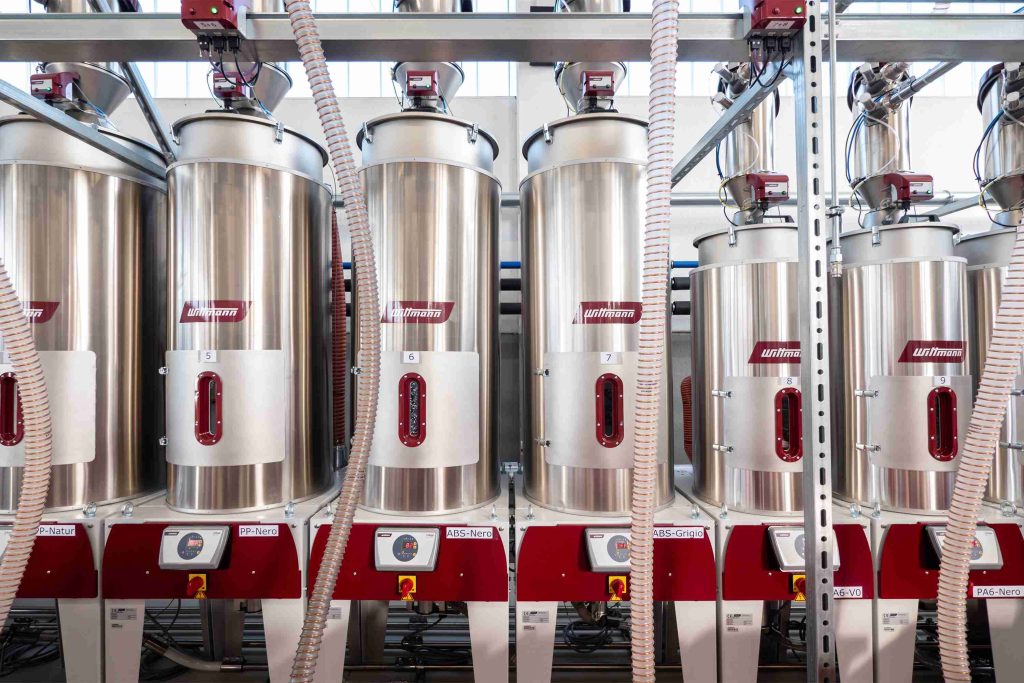
Per molto tempo i pezzi stampati a iniezione sono stati acquistati da fornitori esterni. Poi, nel 2022, i dirigenti hanno deciso di avviare una propria produzione tramite stampaggio a iniezione. Tuttavia, non hanno costruito su un proverbiale “terreno incolto”. Al contrario, Zeca ha acquisito un edificio industriale già esistente e per il layout del nuovo reparto di stampaggio ha cercato di sfruttare tutte le possibili potenzialità in termini di efficientamento.
Purtroppo, però, la concorrenza è agguerrita. “In Asia si realizzano prodotti simili a metà prezzo, ma anche con standard qualitativi inferiori”, spiega Paolo Chiarabaglio, il quale sottolinea pure che: “La buona reputazione di Zeca si basa sull’ottima qualità dei nostri prodotti. Ma dobbiamo comunque produrli a prezzi competitivi”.
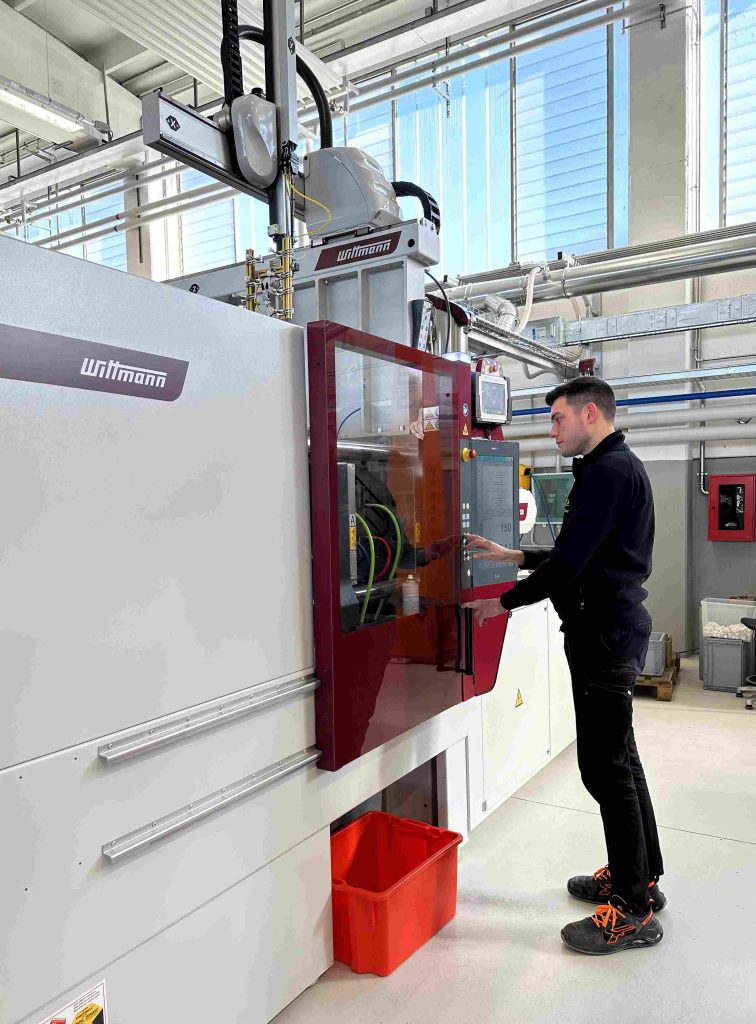
Avere il pieno controllo sui costi e sulla qualità è stata la ragione principale per cui la direzione ha deciso di avviare una propria produzione. “In passato, abbiamo dovuto scartare molti dei pezzi forniti a causa di problemi di qualità”, riferisce Chiarabaglio. “A volte sono stati utilizzati materiali diversi da quelli da noi indicati e il calcolo dei prezzi non è stato del tutto trasparente”.
Grazie a un proprio reparto di produzione, Zeca è anche più flessibile, soprattutto in considerazione dell’enorme varietà di colori possibili. Infatti, mentre i prodotti dell’azienda richiedono solo i tre colori già citati, l’attività conto terzi prevede molti altri colori e la lavorazione di diverse tipologie di materiali. Ciò comporta lotti di piccole dimensioni e, quindi, costi unitari spesso elevati. Di conseguenza, Zeca ordinava generalmente lotti più grandi da tenere a magazzino come scorta, il che implicava però costi di stoccaggio aggiuntivi a carico dell’azienda. Secondo Paolo Chiarabaglio, tali problemi sono riconducibili a un “mercato inefficiente”.
C’è stato poi un altro motivo, molto personale, che ha portato alla decisione di dedicarsi a una propria produzione. “Quando ero bambino, mio padre mi portava spesso con sé quando faceva visita ai propri clienti”, racconta Chiarabaglio. “Presentando la nostra azienda, diceva sempre che noi assembliamo prodotti e questo, in realtà, mi irritava un po’: dopotutto, si trattava dei nostri prodotti e dei nostri progetti. Di conseguenza, volevo poter dire che siamo noi i creatori effettivi di questi prodotti”.
Tutto da un’unica fonte per ridurre le spese
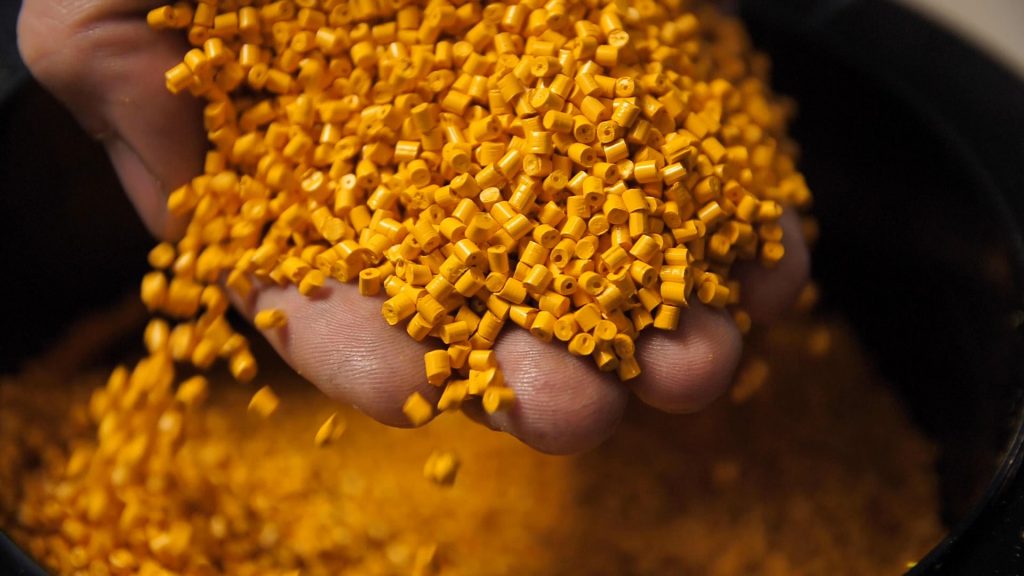
Accanto a una delle nuove isole di stampaggio Wittmann incontriamo Giacomo Meaglia. È a capo della nuova Divisione Plastica e rappresenta un vero “colpo di fortuna” per Zeca, come conferma anche Paolo Chiarabaglio: “Con Giacomo abbiamo acquisito per la nostra azienda un ampio bagaglio di conoscenze e competenze nello stampaggio a iniezione”. Il giovane ingegnere di processo e tecnologo delle materie plastiche si è formato presso l’azienda di stampaggio di suo padre. Fin dall’inizio ha imparato a pensare non solo in termini di parametri tecnici, ma anche di cifre chiave dell’amministrazione aziendale. È quindi predestinato a guidare lo sviluppo del nuovo stabilimento produttivo di Zeca in una posizione di responsabilità.
Con l’aiuto degli esperti Wittmann ha progettato il layout del nuovo reparto di stampaggio e ha stilato procedure di lavoro efficienti. “Il supporto più efficace che potevamo dare a Zeca era quello di fornire isole di produzione “chiavi in mano” da un’unica fonte”, sottolinea Gianmarco Braga, amministratore delegato di Wittmann Battenfeld Italia. “Il coordinamento tra diversi fornitori richiede molto tempo. Ai nostri clienti viene risparmiata tale spesa”.
Tempi di attrezzaggio ridotti del 40%
La chiave per ottenere costi unitari competitivi è un’elevata efficienza dei processi produttivi. In questo caso, le fasi di setup/attrezzaggio presentano un potenziale d’efficientamento particolarmente elevato presso Zeca, per via dei piccoli lotti. Per consentire un cambio stampo estremamente rapido, tutte le presse sono dotate di piani magnetici. A tale scopo, Wittmann ha dotato le macchine delle interfacce necessarie.
“Con i piani magnetici abbiamo ridotto i tempi di attrezzaggio fino al 40%”, riferisce Andrea Landriscina, COO di Zeca. Grazie alla scheda digitale relativa ai parametri stampo, le presse riconoscono gli stampi già al loro secondo utilizzo e impostano automaticamente i parametri di processo ottimali. Questa esecuzione “plug & produce” non consente solo di risparmiare molto tempo, ma incrementa anche l’affidabilità del processo.
Viene così eliminato il rischio di errori, che invece non può mai essere escluso con le impostazioni manuali. Poiché tutti i componenti delle celle di produzione sono completamente integrati, grazie alla connessione Wittmann 4.0, anche gli ausiliari e i manipolatori possono essere controllati molto facilmente tramite il pannello di controllo della macchina.
Secondo Landriscina, un ulteriore contributo all’ottimizzazione dei tempi di attrezzaggio è dato dal MES Temi+, poiché consente una migliore pianificazione dei cambi stampo. “Il caso peggiore potrebbe essere quello di dover effettuare quattro cambi stampo in contemporanea, su quattro presse diverse. Utilizzando Temi+ possiamo evitare tale problema controllando a video, con un unico colpo d’occhio, l’utilizzo delle singole macchine. In questo modo è possibile ottimizzare i tempi di produzione delle nostre isole di stampaggio”.
Consumo energetico ridotto al minimo
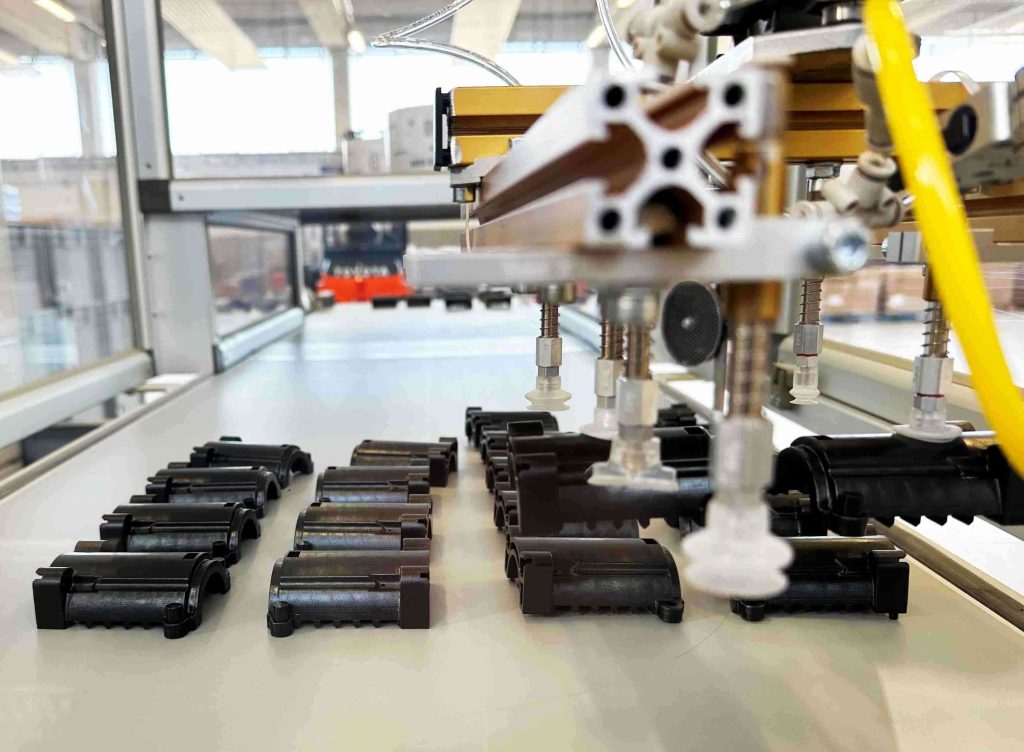
Un fattore decisivo per la scelta degli otto diversi modelli di presse a iniezione riguardava la possibilità d’installare un’ampia gamma di stampi. Sui modelli scelti, con forze di chiusura da 60 a 700 tonnellate, è infatti possibile allestire in modo efficiente stampi sia piccoli che grandi. Anche le tipologie d’azionamento selezionate consentono di coprire una vasta gamma di requisiti differenti. Le macchine scelte sono state quindi quattro SmartPower e due MacroPower, tutte con azionamenti servoidraulici, oltre a due EcoPower completamente elettriche.
Grazie alla tecnologia d’azionamento “all-electric”, Zeca intende infatti guardare al futuro, per esempio espandendo ulteriormente l’attività di produzione conto terzi. “Con l’attuale gamma di macchinari siamo ora molto flessibili e in grado di accettare ordini provenienti da molti campi d’applicazione diversi”, afferma Landriscina.
In termini di consumo energetico, le presse servoidrauliche Wittmann si stanno già dimostrando estremamente parsimoniose. “Ho sempre pensato che la lavorazione delle materie plastiche fosse un processo altamente energivoro”, racconta Giacomo Meaglia. “Sono invece rimasto stupito nel constatare quanta poca energia consumano le nuove macchine Wittmann”.
Prodotti durevoli e per la massima sostenibilità
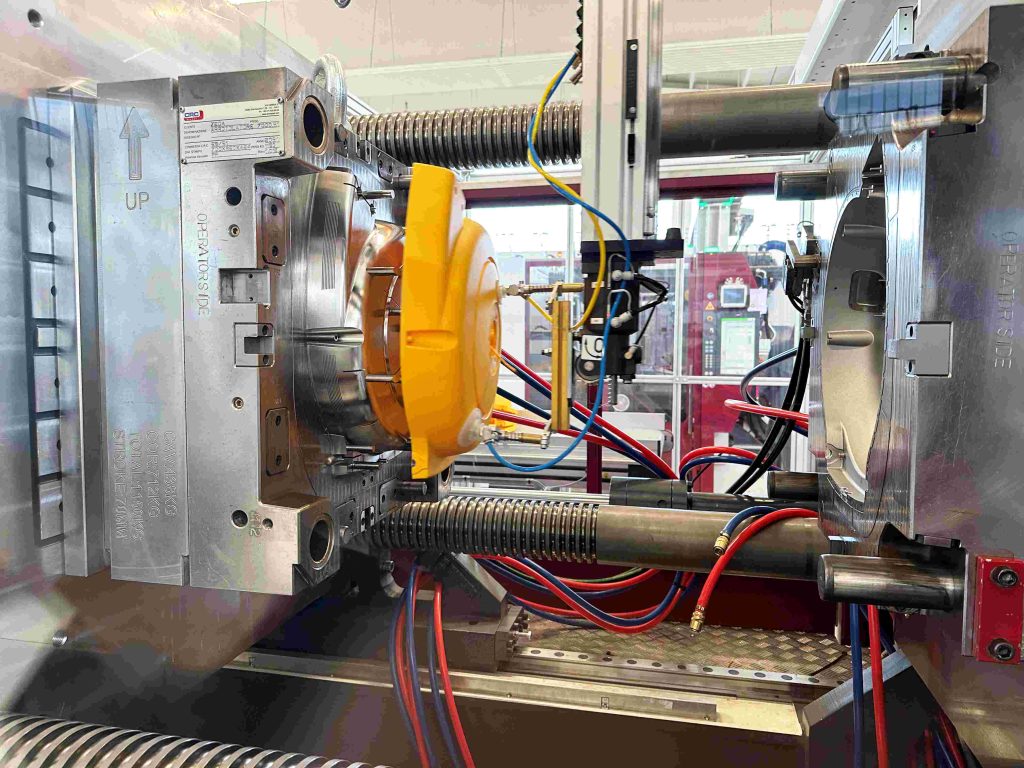
Il polipropilene fa la parte del leone tra i polimeri lavorati in Zeca. Segue il PETG, seppur in quantità minori, che offre un’elevata trasparenza ma è anche più impegnativo da processare, a causa della sua bassa viscosità e sensibilità al taglio. Tuttavia, i cambi stampo non richiedono la sostituzione simultanea delle unità di plastificazione.
“Con le viti standard delle presse Wittmann, otteniamo un fuso assolutamente omogeneo praticamente con tutti i polimeri da stampare. Una perfetta uniformità del colore è per noi fondamentale”, afferma Landriscina. Per l’alimentazione dei masterbatch vengono invece utilizzati i dosatori gravimetrici Gravimax di Wittmann. Sempre più spesso è poi necessario miscelare anche percentuali predefinite di materiali riciclati. A volte le materozze vengono macinate direttamente a bordo macchina e immediatamente riutilizzate.
In Zeca la sostenibilità assume però svariate forme. “Innanzitutto i nostri prodotti sono riparabili”, enfatizza Paolo Chiarabaglio, descrivendo un’inversione di tendenza purtroppo non ancora presente ovunque. “Per noi, questo è un punto molto importante”, afferma il CEO. “Dopotutto, stiamo realizzando prodotti in plastica, che molte persone ritengono non sostenibili. Abbiamo quindi deciso di dimostrare il contrario, per esempio aumentando la durata in servizio dei nostri articoli. Inoltre, i proprietari delle officine possono restituire i prodotti Zeca danneggiati al nostro stabilimento per la riparazione, oppure ordinare i pezzi di ricambio necessari per ripararli essi stessi”. “Anche questo è possibile solo con uno stabilimento produttivo di nostra proprietà”, spiega Chiarabaglio. “Qui abbiamo accesso in qualsiasi momento a tutti gli stampi e possiamo quindi produrre i pezzi di ricambio richiesti anche per i modelli più vecchi, pure con un breve preavviso”.
Una maggiore creatività nello sviluppo dei prodotti
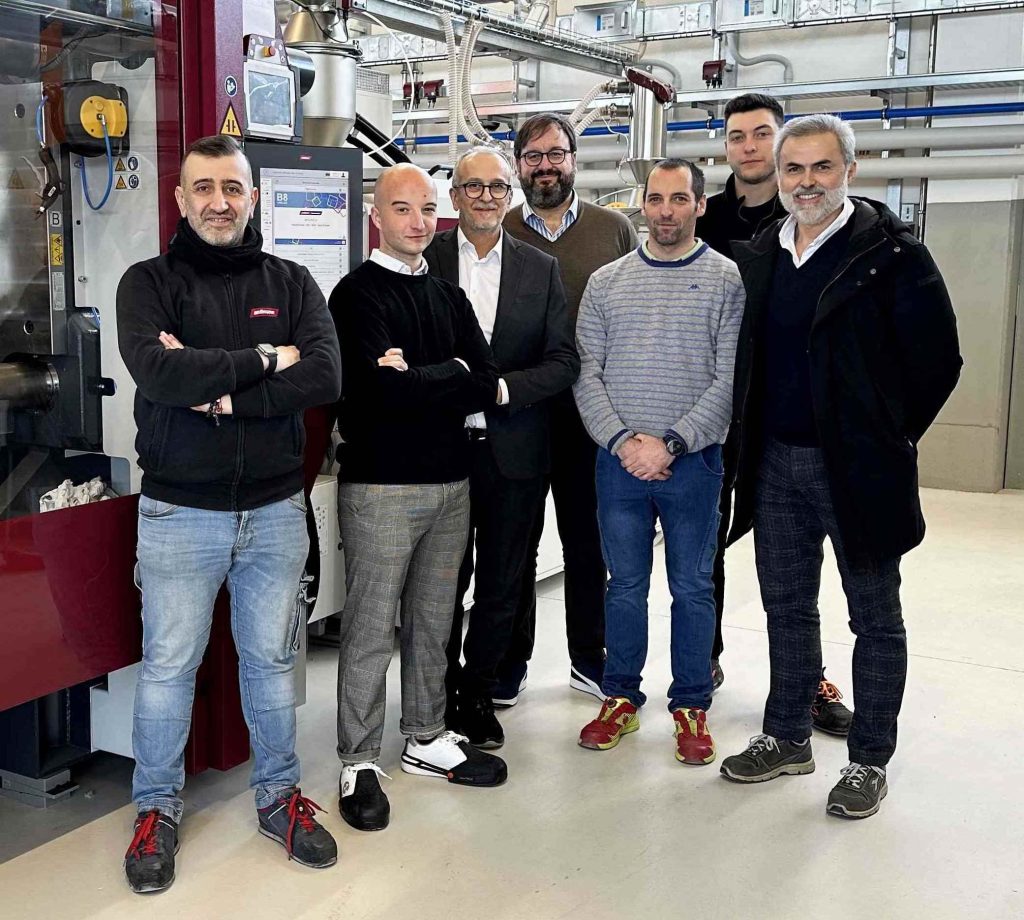
Poter contare su propri macchinari stimola la creatività e anche lo sviluppo di prodotto ne trae vantaggio. Prendiamo, ad esempio, l’etichettatura in stampo (IML, In-Mould-Labelling). “Prima non ci avevamo mai pensato, semplicemente perché non era redditizio per i piccoli lotti forniti dai terzisti”, spiega Chiarabaglio. “Invece ora, per i sistemi avvolgicavo e avvolgitubo, stiamo pensando di applicare i nostri loghi sul corpo dell’avvolgitore tramite IML, anziché incollare le etichette sui coperchi dopo il loro stampaggio. Questo ci renderà ancora più efficienti, facendoci risparmiare un’intera fase di lavoro”.
Quando Paolo Chiarabaglio fa oggi visita ai propri clienti, può così parlare con orgoglio del proprio stabilimento produttivo e “mettere sul tavolo” tutti i vantaggi offerti da Zeca durante le trattative riguardanti i nuovi progetti. Il suo reparto di stampaggio a iniezione ha aumentato la flessibilità dell’azienda, migliorato l’affidabilità degli standard qualitativi e, di conseguenza, la competitività. “Abbiamo ormai raggiunto il livello d’efficienza necessario per servire anche i nostri mercati inefficienti”, conclude Chiarabaglio.
Riccardo Ampollini (rivista Plastix n. 5, giugno 2024)