La produzione di pezzi stampati in modo riproducibile e con una qualità elevata pone stringenti requisiti alla tecnologia di controllo, soprattutto durante il processo d’iniezione nello stampo. Per questo, Arburg ha sviluppato strategie di controllo collegate tra loro e le ha combinate in tre funzioni d’assistenza presenti nel sistema di controllo Gestica delle sue presse Allrounder. Il costruttore ne parlerà in modo approfondito durante il prossimo Congresso delle materie plastiche di TMP, che si terrà l’8 novembre presso il Quark Hotel di Milano.
L’aXw Control ScrewPilot è il prerequisito per movimenti precisi della vite e del processo di riempimento, mentre l’aXw Control PressurePilot assicura una transizione intelligente dalla pressione d’iniezione a quella di mantenimento. L’aXw Control ReferencePilot regola a sua volta la pressione di mantenimento nello stampo in modo riproducibile e in tempo reale, sulla base di una curva di riferimento. Per ogni ciclo, i rapporti di pressione interni allo stampo corrispondono a quelli di riferimento, in modo da garantire pesi stampata costanti e un’elevata qualità dei pezzi.
Il sensore e il software registrano la curva di pressione in tempo reale
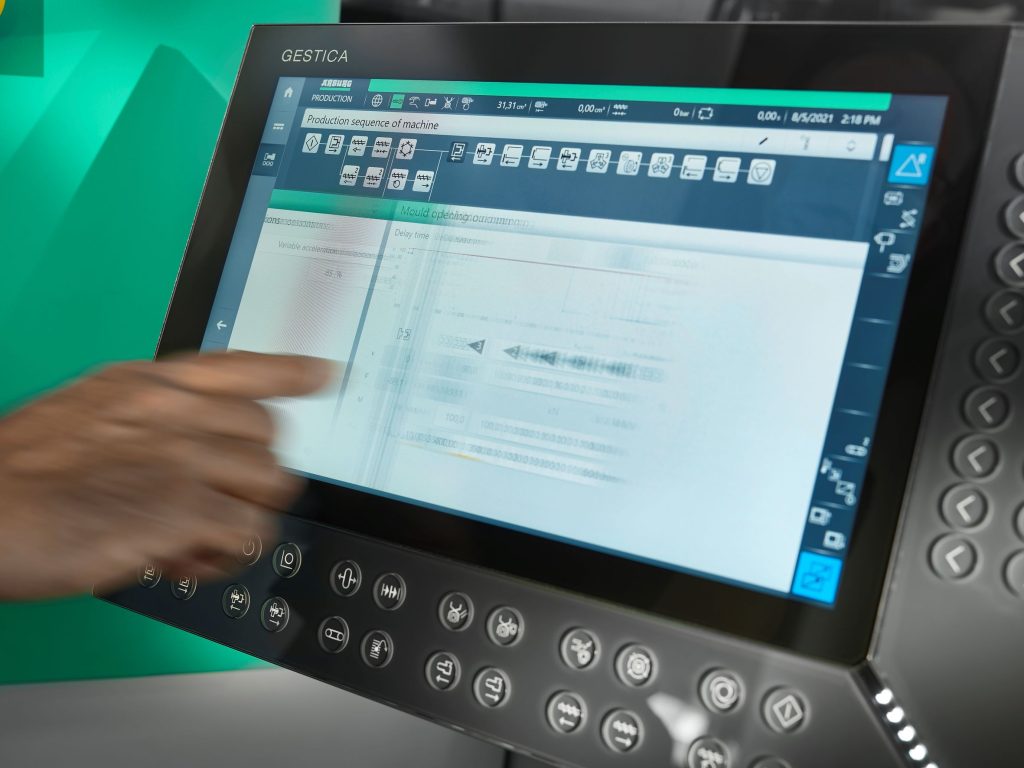
Normalmente, una curva di pressione di mantenimento viene programmata e seguita in modo costante. Tuttavia, non è possibile tenere conto delle variabili di disturbo, come le fluttuazioni di viscosità del materiale fuso o l’usura della vite, che inevitabilmente portano a fluttuazioni di pressione nello stampo e, quindi, a una qualità irregolare dei pezzi.
Per questo motivo, già nel 1988 Arburg aveva sviluppato un “controllo integrato del processo di iniezione” che regolava la curva della pressione di mantenimento in tempo reale, attraverso un sensore di pressione nello stampo. Questa funzione software è stata continuamente sviluppata fino a diventare l’attuale “ReferencePilot”, integrato nel sistema di controllo Gestica.
L’hardware associato richiede un sensore di pressione posizionato il più vicino possibile alla materozza nello stampo. La modalità di funzionamento è paragonabile a quella della guida autonoma: oltre al GPS, per muoversi in sicurezza nel traffico stradale sono necessari anche sensori attivi, ad esempio per rilevare cantieri, dossi o utenti della strada.
Con “ReferencePilot”, il segnale di pressione della cavità viene utilizzato in tempo reale per regolare la pressione di mantenimento in caso di variazioni dell’ambiente, in modo che la pressa a iniezione possa reagire di conseguenza durante il ciclo d’iniezione.
“ReferencePilot” riduce i cicli di avviamento e i costi unitari
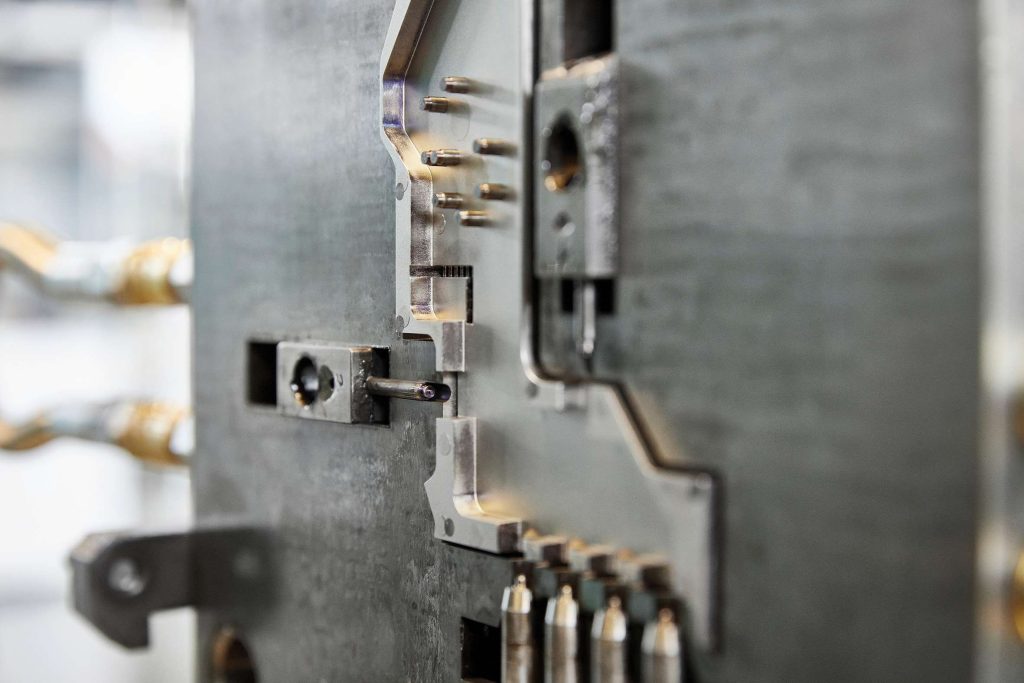
Affinché la macchina “comprenda” quali pressioni sono ottimali nella cavità, viene prima prodotto un pezzo come base per il controllo, viene registrata la sua curva di pressione della cavità e, da quest’ultima, viene creata una curva di riferimento. Nella successiva produzione in serie, l’interazione tra software e hardware regolerà così in modo affidabile la curva di pressione nello stampo.
La curva di misurazione viene eseguita per ogni ciclo a partire dai dati registrati direttamente nello stampo. Ciò significa che la macchina sa sempre esattamente quali pressioni prevalgono nella cavità dello stampo e può regolarsi di conseguenza.
Il controllo della curva di riferimento con “ReferencePilot” assicura condizioni di pressione costanti nella cavità da un’iniezione all’altra, anche, per esempio, in presenza di piccole fluttuazioni di temperatura dello stampo, le quali vengono compensate attivamente
I calcoli dei costi unitari hanno dimostrato che, a seconda dell’applicazione, la produzione può essere fino al 30% più economica. Il necessario investimento aggiuntivo per i sensori si può quindi ammortizzare rapidamente.
Risultati
Con l’aiuto di “ReferencePilot”, il processo di stampaggio a iniezione può essere stabilizzato in modo rapido e conveniente in base a una specifica qualità dei pezzi e il numero di cicli d’avviamento può essere notevolmente ridotto. Inoltre, sono necessari meno processi di controllo a valle e si producono meno scarti. Le fluttuazioni delle condizioni ambientali o della viscosità della massa fusa, per esempio, possono essere compensate in modo affidabile. Ciò è particolarmente importante nel caso di differenze di lotto dovute a cambiamenti di materiale, o alla lavorazione di materiali riciclati.