Fallire più velocemente per arrivare prima al successo. Questa è la chiave di lettura per comprendere il ruolo cruciale giocato dalle tecnologie Stratasys nello sviluppo delle vetture da corsa McLaren, come si può dedurre da questo articolo del direttore tecnico della rivista Plastix, Giovanni Lucchetta, pubblicato sul numero di giugno 2024
Nel mondo attuale, caratterizzato dalla rapida evoluzione e ferocemente competitivo, i team ad alte prestazioni fungono da esempio per tutte le organizzazioni che perseguono un vantaggio competitivo significativo e una crescita esponenziale. Uno dei migliori esempi di team ad alte prestazioni è il gruppo McLaren, che abbiamo avuto il piacere di conoscere attraverso una visita organizzata da Stratasys presso il quartier generale di Woking, nel Regno Unito.
Il pilota neozelandese Bruce McLaren fu il fondatore del celebre team di Formula 1 McLaren, vincendo la sua prima gara nel 1959 all’età di 22 anni e stabilendo il record come il più giovane a riuscirci, un primato che mantenne per i successivi 44 anni. Nonostante la sua prematura scomparsa a 32 anni, Bruce lasciò un gruppo di persone che proseguì il suo lavoro nell’innovazione e nel motorsport, facendo di McLaren una delle più titolate scuderie della storia del campionato di Formula 1, con 12 titoli e 8 titoli costruttori. Le sue origini autodidatte e la sua mente orientata alle novità hanno ispirato gli attuali membri del team McLaren a cercare soluzioni innovative in Formula 1, uno sport noto per le sue regole estremamente rigide, come ad esempio il telaio monoscocca in composito rinforzato con fibre di carbonio, il brake steer e il geniale sistema aerodinamico noto come F-duct.
Il ruolo chiave dell’AM nello sviluppo delle monoposto di Formula 1
“Fail faster, succeed sooner”, con questo motto (che potremmo tradurre con “fallisci più velocemente per arrivare prima al successo”) la scuderia McLaren riassume efficacemente l’essenza della cultura del suo team. Una monoposto McLaren a fine stagione non è la stessa vettura presentata a inizio campionato (figura 1). In appena nove mesi gli ingegneri riescono ad apportare modifiche migliorative sull’80% della vettura. La maggior parte di queste modifiche riguarda l’aerodinamica e viene studiata utilizzando software di calcolo fluidodinamico estremamente potenti.
I software di fluidodinamica computazionale (CFD) permettono al team di simulare e analizzare i flussi d’aria attorno alle macchine in vari scenari virtuali. Tuttavia, nonostante l’avanzamento delle tecnologie CFD, i prototipi fisici testati in galleria del vento rimangono essenziali per diversi motivi:
1) Le simulazioni CFD possono fornire stime accurate, ma i risultati devono essere validati con dati reali per garantire la loro affidabilità. Testare un modello fisico in una galleria del vento permette di confrontare i dati simulati con quelli effettivi, rilevando discrepanze e ottimizzando i modelli di simulazione.
2) Le simulazioni CFD presuppongono spesso condizioni ideali e possono non tener conto completamente delle complessità legate ai materiali reali o alle tecniche di costruzione. I prototipi fisici aiutano a comprendere come i materiali reagiscono alle forze aerodinamiche e a identificare eventuali problemi strutturali o di fabbricazione.
3) Anche con i computer più potenti, le simulazioni CFD possono essere limitate dalla risoluzione dei modelli, o dalla capacità di simulare fenomeni fisici complessi come turbolenze estreme o interazioni dinamiche precise tra diverse parti della vettura.
4) Se si dispone di una tecnologia di additive manufacturing veloce e accurata, i test in galleria del vento permettono agli ingegneri di fare modifiche più rapidamente e vedere immediatamente gli effetti sul comportamento aerodinamico della vettura.
La partnership tra McLaren e Stratasys rappresenta quindi un tassello fondamentale nella realizzazione di prototipi per la galleria del vento e componenti per le vetture di Formula 1.
McLaren e Stratasys: insieme per vincere in Formula 1
Leader nell’ambito della stampa 3D, Stratasys collabora strettamente con McLaren per fornire soluzioni di produzione additiva che accelerano il processo di test e sviluppo.
Piers Thynne, Chief Operating Officer di McLaren Racing, sottolinea l’importanza di questa tecnologia nel motorsport: “L’additive manufacturing è parte vitale della Formula 1. Disponiamo di molteplici stampanti 3D che utilizzano vari aspetti della tecnologia. È fantastico avere Stratasys come partner in questo campo; circa l’80% dei pezzi prodotti per additive manufacturing è destinata alla nostra galleria del vento e circa il 20% alla vettura”. Questa collaborazione permette a McLaren di sperimentare rapidamente nuove soluzioni aerodinamiche, riducendo i tempi di sviluppo e migliorando la competitività delle loro monoposto in uno sport dove ogni millisecondo conta.
McLaren utilizza in maniera intensiva 21 stampanti 3D di Stratasys, tra cui modelli avanzati come l’FDM F900, il Fortus 450mc (figura 2), la Polyjet J750 e le stampanti stereolitografiche NEO 450 e NEO 800 (figura 3). Queste stampanti variano per volume di lavoro, consentendo la produzione di componenti di piccole dimensioni fino a elementi grandi come un intero spoiler.
Utilizzando le stampanti stereolitografiche NEO e la resina Somos® PerFORM Reflect, il team è in grado di produrre fino a 9000 parti all’anno per lo sviluppo delle superfici aerodinamiche anteriori e posteriori, oltre a parti del corpo laterale della vettura (figura 4).
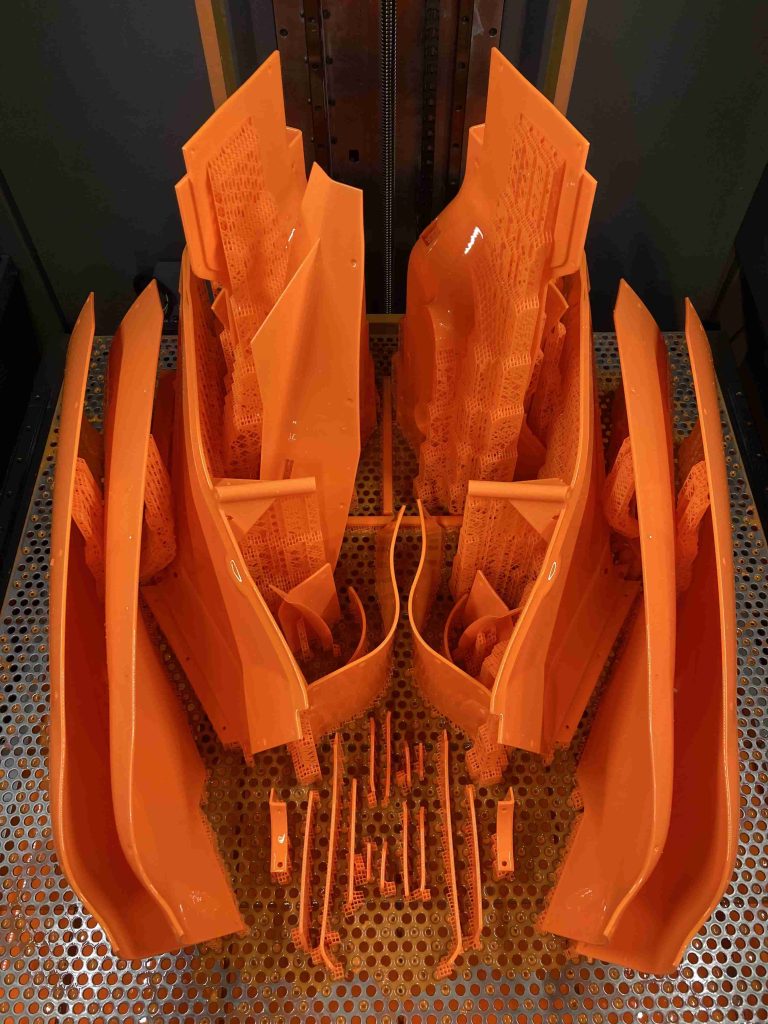
La resina PerFORM Reflect, sviluppata specificamente per i modelli da galleria del vento, crea componenti robusti e rigidi che, abbinati all’elevata finitura superficiale ottenuta con le stampanti NEO, riducono i tempi di post processing di oltre il 30%. Queste parti, combinate con un supporto in alluminio lavorato, formano il modello in scala pronto per la galleria del vento.
I test in galleria del vento vedono regolarmente molteplici iterazioni del design degli alettoni anteriori e posteriori, delle pance laterali e dell’intera parte superiore del corpo dell’auto.
Grazie alla velocità di stampa e all’elevata finitura superficiale, che consente di ridurre drasticamente i tempi del ciclo di finitura, l’efficienza del processo di sviluppo aerodinamico è migliorata significativamente, consentendo al team di rispondere velocemente alle esigenze dinamiche delle gare, adattando e perfezionando le componenti dell’auto in base alle prestazioni e ai feedback raccolti direttamente dalle sessioni di prova. Questo approccio incrementale alla progettazione e al miglioramento continuo conferisce a McLaren un vantaggio significativo sulle sue rivali in Formula 1, dove l’innovazione e la velocità d’esecuzione sono decisive. Per McLaren, la velocità, la precisione e l’affidabilità dei sistemi Stratasys sono quindi cruciali.
Dalla prototipazione alla produzione
Pioniere della stampa 3D polimerica da oltre 35 anni, Stratasys è stato testimone di una crescita notevole e di avanzamenti tecnologici significativi fin dalla sua fondazione. Con oltre 14000 stampanti 3D installate globalmente e partnership con giganti dell’industria quali Boeing e Tesla, la società si è consolidata come leader nella manifattura additiva.
Yann Rageul, vicepresidente Commercial Enablement della Business Unit Industrial di Stratasys, ha delineato il percorso di evoluzione dell’azienda: “Quando sono stato assunto, circa dieci anni fa, eravamo principalmente concentrati sulla prototipazione, ma la tecnologia si è evoluta enormemente da allora. Ora, ci siamo spostati verso la realizzazione di attrezzature e dispositivi di montaggio, e abbiamo iniziato a sostituire processi tradizionali come lo stampaggio a iniezione e la lavorazione CNC nella produzione industriale”.
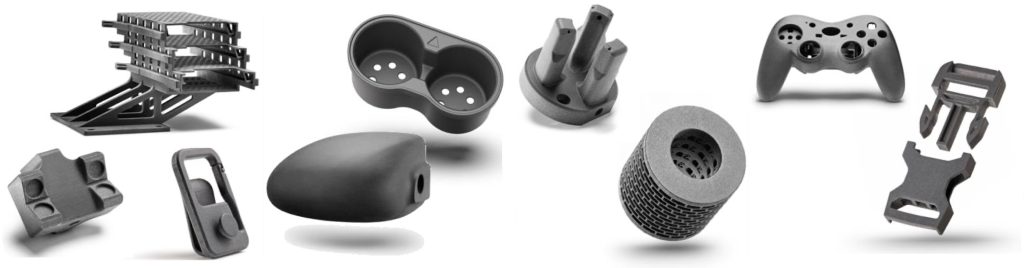
In diversi settori, le aziende più innovative stanno iniziando a utilizzare la stampa 3D per produrre parti utilizzabili direttamente nei prodotti finiti (figura 5): dagli elementi di collegamento, come cerniere, clip e sistemi di aggancio, a elementi di finitura per il settore automobilistico, fino a custodie elettroniche, coperture, staffe e condotti per i macchinari industriali.
Nonostante questo, le parti realizzate con manifattura additiva rappresentano solo lo 0,1% del totale della produzione manifatturiera, ancora largamente dominata da tecnologie tradizionali. Questi processi sono spesso molto rigidi e richiedono un elevato investimento in capitale, indipendentemente dal volume e dalla diversificazione dei prodotti, e sono soggetti a incertezze della filiera di approvvigionamento. Inoltre, sono scarsamente digitalizzati, pongono dei vincoli significativi al design dei componenti e non consentono una personalizzazione su larga scala.
Per sbloccare nuove applicazioni manifatturiere, Stratasys ha migliorato ogni fase del flusso di lavoro che caratterizza la produzione additiva (figura 6). “Si tratta di semplificare il flusso di lavoro per il cliente e di ridurre la manodopera necessaria per la produzione”, ha dichiarato Rageul:
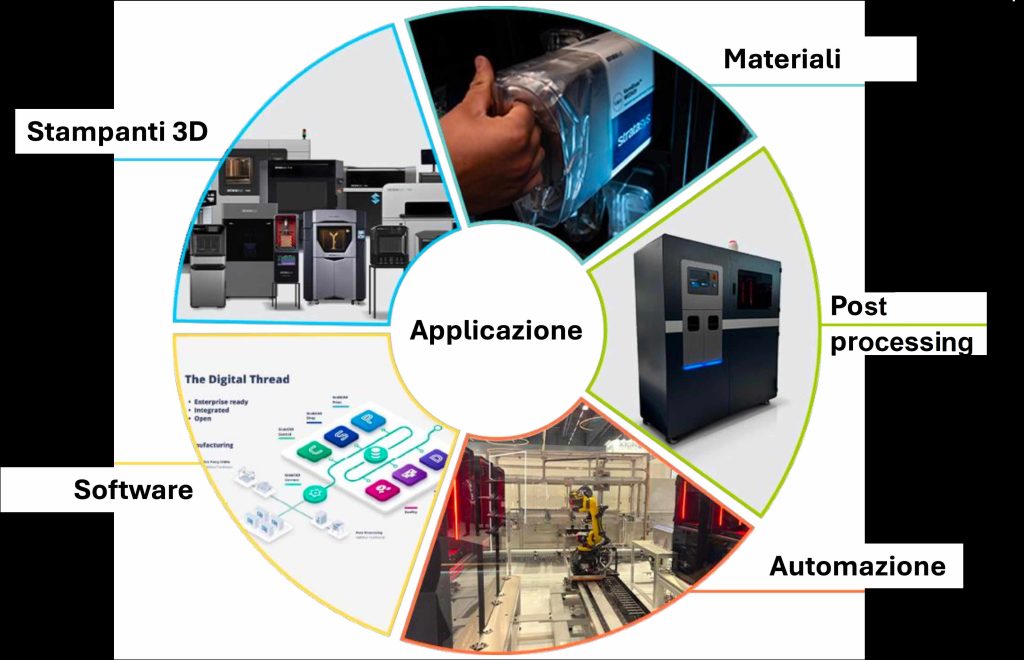
- L’azienda possiede il più vasto portafoglio di hardware innovativo, includendo tecnologie come PolyJet, SLA, FDM, P3 e SAF, che coprono l’intera catena del valore dalla prototipazione rapida alla produzione seriale di parti finali.
- L’ecosistema di materiali di Stratasys offre un’ampia gamma di opzioni e accesso alle impostazioni delle stampanti per l’ottimizzazione delle parti, con oltre 100 materiali validati sviluppati internamente o con leader di materiali terzi, che rispondono a una vasta gamma di applicazioni e caratteristiche funzionali e di prestazione.
- Inoltre, il software GrabCAD di Stratasys rappresenta una delle piattaforme di stampa 3D più avanzate e grandi del settore, integrata pienamente con le industrie manifatturiere.
- Per il post processing, Stratasys propone diverse soluzioni per effettuare le operazioni di pulizia, lucidatura, colorazione e trattamento termico delle parti stampate, riducendo il lavoro manuale nelle fasi chiave, come la rimozione delle parti finite dalla macchina.
- L’automazione programmabile di Stratasys dimostra come la tecnologia possa essere “scalata” a soluzioni di livello fabbrica, abilitando una produzione continua e ottimizzata.
Questi avanzamenti posizionano Stratasys all’avanguardia nella trasformazione della produzione additiva da un’opzione per prototipi a una soluzione pienamente produttiva.
L’ampia offerta di Stratasys porta velocità, agilità e valore in ogni fase del ciclo di vita dello sviluppo del prodotto: 1) nella prototipazione rapida, per un realismo funzionale e di design, 2) nella realizzazione di attrezzature e dispositivi di fissaggio per montaggi, controlli e mani di presa, nonché 3) nella realizzazione di preserie e nella produzione di basso volume.
Fadi Abro, direttore globale della divisione Transportation di Stratasys, evidenzia come le aziende partner utilizzino le tecnologie di stampa 3D soprattutto nello sviluppo di prodotto. “Quando aziende come McLaren concepiscono un’innovazione, spesso non possono seguire le vie tradizionali di produzione”, spiega Abro. “La nostra tecnologia può aiutare con la prototipazione quando hanno bisogno, ad esempio, di cinque versioni diverse di uno spoiler. Possono poi utilizzare questi prototipi in gallerie del vento, che imitano l’ambiente di corsa, per capire come si comporteranno aerodinamicamente”.
Il supporto alla produzione rappresenta il passo successivo. Nel caso di McLaren, ciò significa che i sistemi Stratasys vengono utilizzati per realizzare attrezzature per l’assemblaggio dei veicoli stradali, o la creazione di modelli per parti. “Tutto ciò che supporta la produzione, ma non è un prototipo o una parte finale, rientra in questa categoria. Ciò include supporti per l’assemblaggio e dispositivi per il controllo dimensionale, soluzioni che aiutano a far uscire più auto dalla fabbrica”, afferma Abro. Per McLaren, questo si traduce nella produzione di componenti su misura per i suoi veicoli stradali.
La collaborazione tra Stratasys e i suoi partner si estende anche alle parti d’uso finale. Il 20% della capacità di produzione additiva di McLaren è utilizzata per realizzare parti per l’auto, come ad esempio alcuni componenti del volante (figura 7). McLaren è il partner ideale perché produce parti in basso volume, ma ad alto valore. Questo approccio sfrutta pienamente le potenzialità della manifattura additiva, offrendo soluzioni personalizzate che rispondono perfettamente alle esigenze specifiche di prestazioni e design.
Il futuro sarà caratterizzato da sistemi più rapidi e maggiormente sostenibili
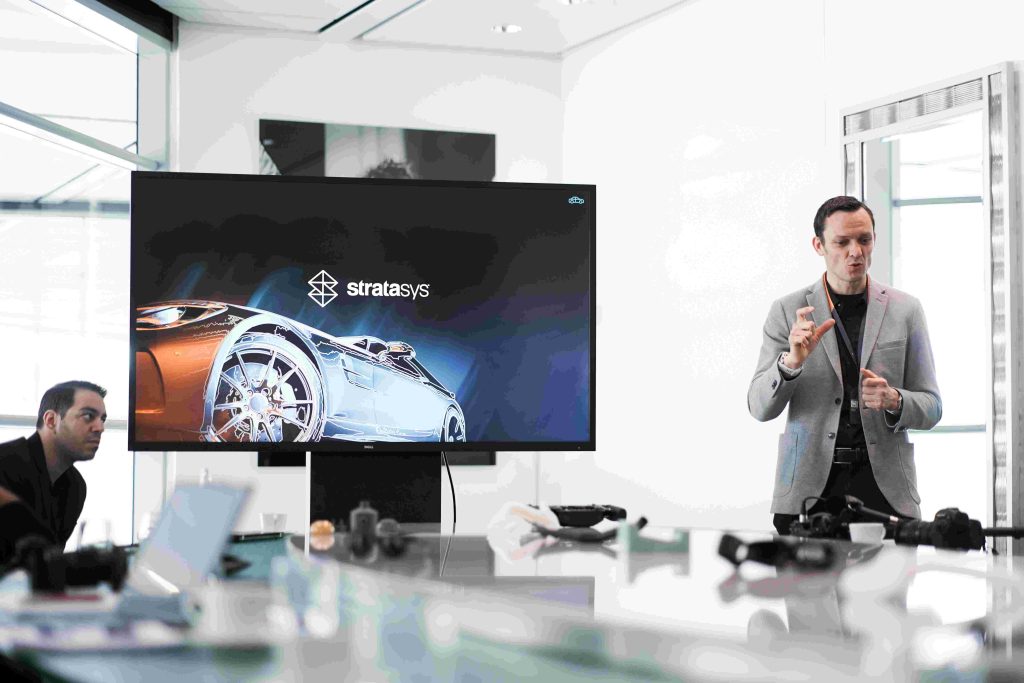
L’industria automobilistica sta manifestando un forte interesse verso la riduzione degli sprechi, ponendo sempre maggiore attenzione all’utilizzo di materiali riciclati, soprattutto nel campo della prototipazione. Questa tendenza riflette un’ampia consapevolezza delle implicazioni ambientali associate alla produzione tradizionale e un crescente impegno verso pratiche più sostenibili.
In risposta a queste esigenze, Stratasys ha introdotto soluzioni innovative che abbracciano la sostenibilità senza compromettere le performance. “Con il nuovo software OpenAM di Stratasys, utilizzabile sulle nostre stampanti industriali 3D F900 e Fortus 450mc, è possibile realizzare parti stampate in 3D a partire da plastica riciclata”, ha dichiarato Yann Rageul. “I clienti possono modificare parametri come la temperatura dell’estrusore o la portata, migliorando notevolmente la qualità dei componenti. Stratasys è orgogliosa di offrire soluzioni open source per stampare i materiali, lanciando nuove applicazioni per i clienti e lavorando verso un’economia circolare”.
Fadi Abro, da parte sua, sottolinea un cambio di focus strategico per il futuro: “Se in passato Stratasys si è concentrata particolarmente sullo sviluppo dei materiali, il prossimo obiettivo principale sarà massimizzare la produttività per competere con lo stampaggio a iniezione. I motori lineari saranno utilizzati per aumentare la velocità delle stampanti”.
Questo approccio non risponde solo alla crescente domanda di processi produttivi ecologici, ma spinge anche l’industria verso soluzioni più efficienti e veloci, mirando a rivoluzionare il tradizionale equilibrio tra velocità, qualità e sostenibilità. L’impegno di Stratasys verso l’innovazione continua e l’adozione di tecnologie avanzate segna un passo significativo verso un futuro in cui la produzione additiva potrà sostituire con successo tecnologie più tradizionali, contribuendo significativamente alla creazione di un ambiente industriale più versatile e sostenibile.
Giovanni Lucchetta, Università di Padova