Durante i mesi del lockdown, il settore del riciclo di materie plastiche è stato messo sotto pressione: la raccolta di rifiuti da imballaggio è aumentata di quasi il 10%, le esportazioni di rifiuti riciclabili sono crollate (tra marzo e aprile il calo è stato pari a oltre 16.000 tonnellate di rifiuti urbani) e la tradizionale alternativa al riciclo meccanico – la valorizzazione energetica – si è trovata in forti difficoltà per la chiusura dei cementifici, che rappresentano il canale di smaltimento del 75% degli imballaggi non riciclabili meccanicamente, il cosiddetto plasmix.
Per fortuna il sistema ha retto, anche perché il lockdown è durato solo sette settimane e termovalorizzatori e discariche nel nostro paese non mancano (una parte dei rifiuti è stata però avviata a impianti esteri). È emersa tuttavia la carenza strutturale di impianti per il riciclo dei rifiuti urbani e, in particolare, degli imballaggi in plastica.
Obiettivo “discarica zero”
Per i rifiuti difficili o impossibili da recuperare per via meccanica, come i film multistrato o gli imballaggi multimateriale, una valida alternativa può essere il riciclo chimico, sia mediante depolimerizzazione quando la frazione è sufficientemente omogenea e il polimero si presta a questo scopo – polistirene e PET sono buoni esempi –, sia attraverso processi di pirolisi, dai quali si ottengono materie prime per il cracking o carburanti. Con una dotazione impiantistica opportuna, con tecnologie già oggi disponibili, si potrebbe raggiungere l’obiettivo della “discarica zero” e sgravare il recupero energetico dalle fluttuazioni dei volumi conferiti.
A questo scopo, poco prima della pausa estiva, ENI ha siglato alcuni accordi con NextChem e con Corepla, coinvolgendo in questo caso anche Versalis, per avviare impianti di recupero di plasmix all’interno dei poli petrolchimici italiani, parte del più ampio piano di decarbonizzazione varato dal gruppo energetico milanese all’inizio dell’anno, che si propone di abbattere l’80% delle emissioni entro il 2050.
A Taranto syngas da plasmix
A fine giugno, ENI ha firmato con NextChem – la società del Gruppo Maire Tecnimont attiva nella chimica verde e transizione energetica – un accordo che amplia quello siglato l’anno scorso per la realizzazione di impianti destinati al trattamento di rifiuti plastici difficili da riciclare per via meccanica. Ai progetti già avviati dai due partner – uno per la sintesi di idrogeno da rifiuti plastici a Porto Marghera, l’altro per la produzione di metanolo a Livorno – si è aggiunto anche quello per la conversione in “gas circolare” (syngas) di scarti plastici misti (plasmix) e combustibile solido secondario (CSS) all’interno della raffineria ENI di Taranto. Si parte con uno studio di fattibilità per poi eventualmente realizzare un’unità per la produzione di gas di sintesi mediante gassificazione ad alta temperatura di plasmix e CSS. Questo processo si basa su una reazione termica, in ambiente chiuso con presenza di ossigeno, quindi senza emissioni dirette in camino; le temperature sono tali da “vetrificare” gli inquinanti, rendendoli così inerti e stabili.
Il progetto NextChem
Secondo il progetto di massima concordato dai due partner, utilizzando le tecnologie presenti nel portafoglio NextChem, il syngas sarà in seguito raffinato in due flussi indipendenti: idrogeno, destinato a un utilizzo in loco (all’interno della raffineria ENI per alimentare i processi di idrodesolforazione dei carburanti), e un gas ricco di ossido di carbonio destinato all’impiego nelle acciaierie, per i processi in altoforno e nelle nuove tecnologie DRI (Direct Reduced Iron), fornendo così un contributo alla decarbonizzazione dell’industria siderurgica.
La soluzione proposta da NextChem porterebbe, secondo un’analisi del ciclo di vita del materiale (LCA), a una sostanziale riduzione delle emissioni di CO2 rispetto al trattamento di CSS e plasmix mediante termovalorizzazione, oggi l’alternativa più sfruttata. Il progetto rientra in un approccio che l’azienda ha battezzato “distretto circolare”, volto a recuperare, combinando diverse tecnologie – dall’upcicycling al riciclo chimico fino alla chimica verde – le diverse frazioni dei rifiuti, con l’obiettivo di ridurre fino a eliminare il conferimento in discarica, sfruttando quanto più possibile il carbonio e l’idrogeno presente nella plastica indifferenziata.
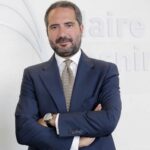
In tre per riciclare plasmix
All’inizio di luglio, un secondo accordo sullo stesso binario è stato siglato da ENI, dalla controllata Versalis e da Corepla. Anche in questo caso l’obiettivo è trovare una soluzione di riciclo chimico alle eccedenze di plasmix proveniente dalla raccolta differenziata di imballaggi in plastica, mettendo a fattore comune competenze, conoscenze e dotazioni infrastrutturali. Se l’alleanza con NextChem è prevalentemente tecnologica, quella con Corepla attiene all’approvvigionamento dei rifiuti plastici da trattare.
Un primo protocollo è stato sottoscritto da Corepla e Versalis con l’obiettivo di analizzare, a fini di recupero, le diverse frazioni di plasmix disponibili nel circuito del Consorzio. La società chimica del gruppo ENI metterà disposizione, una volta realizzato e avviato, il primo impianto di riciclo chimico in progetto a Mantova: il progetto Hoop, frutto di un accordo raggiunto a febbraio con la società italiana di ingegneria Servizi di Ricerche e Sviluppo con l’obiettivo di attivare nel polo lombardo capacità di trattamento pari a 6.000 tonnellate annue, ottenendo materie prime per la produzione di nuove plastiche.
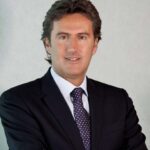
Il secondo accordo, stretto da Corepla con ENI, estende l’alleanza che coinvolge NextChem. L’obiettivo, infatti, è verificare la possibilità di valorizzare le plastiche a fine vita nella bioraffineria di Porto Marghera e presso la raffineria di Livorno per la produzione, rispettivamente, di idrogeno e metanolo ottenuti da gassificazione.
ENI procede verso la decarbonizzazione
In questo ambito, Corepla fornirà un contributo essenziale nel definire disponibilità e composizione del plasmix gestito attraverso il suo circuito a livello nazionale, in collaborazione con le imprese specializzate nel settore del recupero, al fine di renderlo idoneo rispetto alle diverse esigenze delle varie tecnologie.
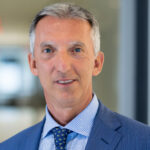
L’intesa con il Consorzio per il recupero degli imballaggi in plastica vede anche l’estensione del progetto RiVending, avviato nelle sedi ENI a San Donato Milanese per il riciclo delle palette e dei bicchierini da caffè in polistirene dei distributori automatici, con un allargamento della raccolta anche ad altre sedi e in tutti i siti industriali del gruppo.
«Vogliamo essere protagonisti e propulsori di una vera economia circolare basata su progetti concreti e innovativi, rafforzando al contempo la leadership italiana di una chimica sempre più sostenibile» nota al momento della firma Antonello Ciotti, il presidente di Corepla. «Obiettivo che è reso possibile dall’avanzamento tecnologico e dal costante lavoro di innovazione e ricerca messo in campo da ENI con il piano di riconversione dei suoi impianti, sapendo guardare a un futuro green con lungimiranza ed efficienza».