Per decenni Lati ha prodotto e lavorato le materie termoplastiche ad alte prestazioni con macchine di sviluppo e produzione proprie. Successivamente si è affidata sempre di più all’esperienza dei fornitori di impianti specializzati nel settore dei tecnopolimeri. Nel 2021 l’azienda italiana, di grande tradizione, ha preso una strada diversa relativamente ai sistemi di taglio: da allora i termoplastici tecnici e i polimeri ad alte prestazioni sono prodotti nella sede produttiva di Gornate Olona, in Lombardia, con i sistemi di granulazione di Maag
Tradizione, esperienza e coraggio per l’innovazione: sono queste le attitudini alla base del successo dell’azienda italiana Lati Industria Termoplastici. Fondata nel 1945 come produttore di compound di acetato di cellulosa, in breve tempo Lati ha conquistato nuovi mercati. Con la specializzazione in materiali ad alte prestazioni è cresciuta la sede lombarda di Vedano Olona ed è cresciuto il numero delle sedi all’estero. Oggi Lati ha all’attivo più di 2000 formulazioni di compound termoplastico, tra cui spiccano poliammidi rinforzate, autoestinguenti, termicamente ed elettricamente conduttive, autolubrificanti e, appunto, polimeri ad alte prestazioni. I clienti industriali provengono dal settore elettrico ed elettronico, elettrodomestico, automobilistico, nonché alimentare e altro ancora.
In quanto fornitore di soluzioni speciali, un pilastro della filosofia di Lati prevede la produzione propria di tutti i compound, ma non solo. Anche gli impianti dell’ampio parco macchine sono tradizionalmente sviluppi propri: ad esempio granulatori, linee di estrusione compound, impianti di miscelazione e impianti generali di servizio. Chi ha idee precise sulle caratteristiche dei suoi prodotti dovrebbe anche occuparsi personalmente dei mezzi di produzione: questo è stato per decenni un principio indiscusso per Lati.
Tuttavia, all’inizio del nuovo millennio ci si mise alla ricerca di nuove vie per migliorare ulteriormente la produzione di Lati. All’epoca Diego Imbrighi, a cui fu affidata la responsabilità di questo compito complesso, si fece carico di integrare nella produzione un granulatore fornito dal mercato che però, nonostante gli opportuni aggiustamenti, non riuscì a soddisfare pienamente le aspettative della produzione.
Imbrighi ebbe l’opportunità di fare altrove nuove esperienze: nei 20 anni che seguirono lavorò per diversi produttori europei di materie plastiche, principalmente in Italia e in Germania, per poi tornare nel 2021 in Lati come direttore Technology & Innovation. Nelle sue diverse esperienze professionali tornava sempre una costante: nelle sedi produttive dei produttori di compound di materie plastiche venivano impiegate molto spesso le macchine di Maag. I sistemi di granulazione, gli essiccatori, i polverizzatori, le pompe e i filtri del fornitore di lunga data di sistemi per la lavorazione dei polimeri fornivano risultati convincenti a tutti i produttori. “Le macchine, anche se diversissime per grandezza e portata, garantivano sempre altissima qualità”, si ricorda Imbrighi.
Lati segue nuove vie con il supporto di Maag
Quando Imbrighi, nel 2021, cominciò il secondo capitolo della sua carriera in Lati, i produttori di compound dell’intero settore stavano affrontando diversi problemi su più fronti: l’aumento dei costi per l’energia, la mancanza di manodopera specializzata e l’incalzare della concorrenza resero necessari l’aumento della produttività e la riduzione dei costi. Imbrighi vide quindi una nuova opportunità nella società Maag, per portare in Lati un valido know-how esterno.
Decise di contattare Jürgen Skanda, sales manager Pelletizing di Maag e suo amico da molto tempo. “Ovviamente conoscevo Lati come produttore italiano leader di compound tecnici di alta qualità e, già da alcuni anni, ero in contatto con il suo team”, Skanda ricorda così il primo approccio. Dopo tutto, già in passato era stato realizzato con successo un progetto nell’ambito della granulazione sott’acqua (taglio sommerso, ndr). “Inoltre, nel corso degli anni Jürgen Skanda e io avevamo avuto spesso contatti, praticamente in tutte le aziende in cui ho lavorato”, aggiunge Imbrighi. “Ciononostante, all’inizio non è stato facile inserire un nuovo fornitore di sistemi di taglio a secco, vista la non soddisfacente esperienza fatta in passato”.
Maag accettò un accordo individuale: Lati avrebbe avuto il tempo necessario per testare il nuovo granulatore continuo Primo Plus sotto ogni punto di vista. “Se la nostra macchina non fosse stata in grado di soddisfare i requisiti molto specifici dell’azienda, Lati avrebbe potuto restituirla”, così Skanda descrive l’offerta di Maag.
Granulazione continua con taglio a secco
L’esperto di polimeri, tuttavia, era certo che ciò non sarebbe successo. Maag ha una vasta esperienza nel settore della granulazione (o “pellettizzazione”, ndr): solo nell’ambito della granulazione continua con taglio a secco, il produttore ha introdotto sul mercato più di 10 mila macchine, perfezionandone la tecnologia nel corso dei decenni.
Il granulatore continuo con taglio a secco Primo Plus di Maag aveva convinto Imbrighi già durante il periodo in cui lavorava presso altri produttori europei di materie plastiche; infatti il sistema era sviluppato in modo specifico per la granulazione di resine termoplastiche tecniche rinforzate di alta qualità.
Test approfonditi con diversi compound
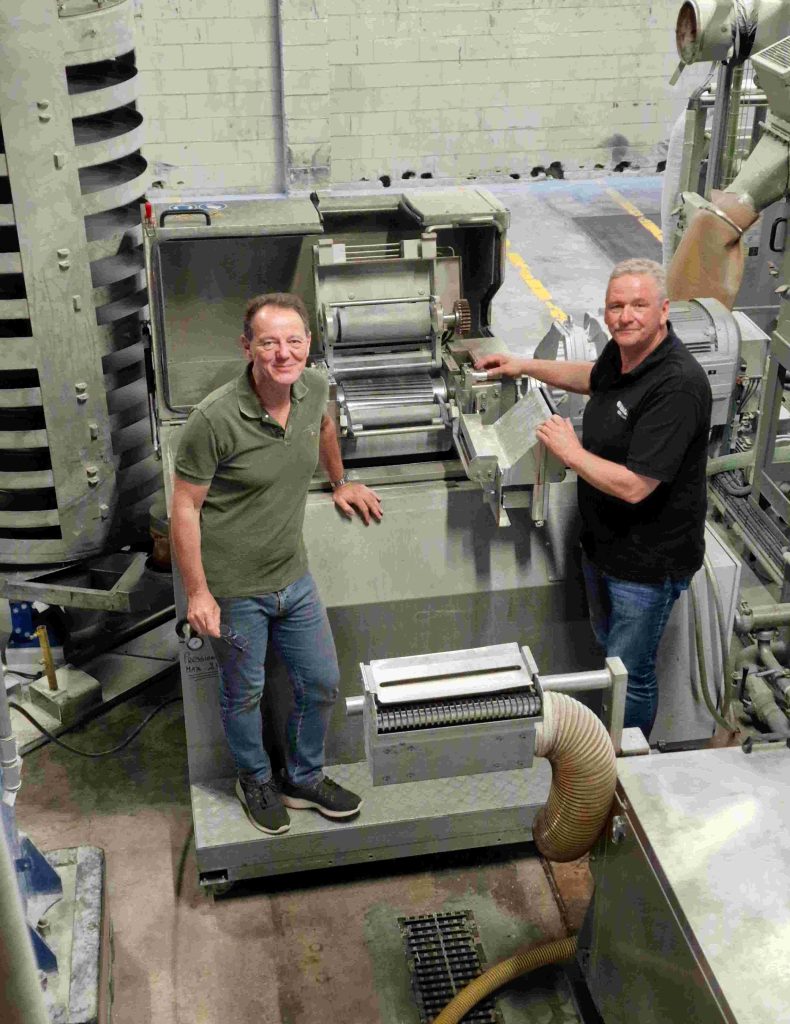
Pochi mesi dopo l’accordo personalizzato tra Lati e Maag, il sistema di granulazione fu fornito dalla Bassa Franconia in Lombardia. Primo Plus doveva dare prova di sé in una linea di produzione completamente riallestita. I prodotti da lavorare includevano:
- PA66 con una percentuale di fibre di vetro dal 25 al 50% e diversi additivi (ad es. ritardanti di fiamma alogenati e non alogenati);
- PA6 con diverse percentuali di fibre di vetro, anche in questo caso con additivi ritardanti di fiamma;
- PPS con una percentuale di fibre di vetro dal 60 al 65 percento e riempitivi minerali.
“Insieme al team tecnico di processo, abbiamo avviato un’ampia serie di test accurati e raccolto dati affidabili che dovevano poter essere comparati con quelli delle macchine sviluppate e realizzate internamente e competere con dati oggettivi”, così descrive Imbrighi il processo.
“Il principale limite riscontrato sui sistemi di taglio sviluppati internamente era la durata del rotore di taglio in relazione alle portate e alle quantità prodotte”, afferma Imbrighi. Questo fu il primo problema risolto da Primo Plus: “In pochi mesi fu evidente che il nuovo granulatore continuo era in grado di lavorare con estrema affidabilità gli elevati volumi necessari, con un’eccellente qualità del taglio”. Contemporaneamente migliorò anche il comfort nella produzione, infatti il sistema di Maag offre il vantaggio di livelli di rumorosità decisamente inferiori rispetto alla macchina precedentemente impiegata da Lati.
Maggiore durata e geometria ottimizzata
Tuttavia, anche un altro fattore importante era cambiato. La durata del rotore di taglio aumentò notevolmente passando da pochi giorni a diversi mesi. Questa lunga durata suscitò grande entusiasmo in Lati, specialmente nelle “operation”, che videro aumentare il tempo d’attività (“uptime”) della linea d’estrusione su cui era installata la nuova taglierina.
Il primo cambio rotore venne fatto alla presenza di Jürgen Skanda, che dimostrò la sua grande esperienza e simpatia coinvolgendo tutto il gruppo operation di Lati durante il suo ripristino. Fu un’occasione per trasferire alla manutenzione interna dell’azienda la metodologia di set-up e spiegare tutte le potenzialità della nuova taglierina.
“Poiché da allora la manutenzione del rotore è affidata a Maag, ora risparmiamo ulteriori costi e i colleghi della manutenzione hanno più tempo da dedicare ad altre attività richieste dalle operation”, riferisce Imbrighi.
Per garantire che Lati possa trarre vantaggio anche in futuro dal know-how di processo degli ingegneri di Maag, i collaboratori addetti alla manutenzione e al funzionamento partecipano periodicamente a corsi di formazione tecnica. “Con questi workshop vogliamo supportare i nostri clienti offrendo loro informazioni esaurienti sulle possibilità e sulle innovazioni dei nostri impianti”, spiega Jürgen Skanda.
Prospettive per progetti successivi futuri
La convinzione e l’impegno personale di Diego Imbrighi hanno dato i loro frutti: grazie alla durata decisamente maggiore del rotore di taglio, alla riduzione del lavoro di manutenzione e alla geometria ottimizzata dei pellet, Lati ha potuto migliorare la qualità e rendere i suoi processi produttivi più efficienti. Dal progetto traiamo gli insegnamenti seguenti: “Con ogni probabilità in futuro sostituiremo tutti i granulatori attualmente installati sulle linee ad alta efficienza e, come primo passo, abbiamo deciso di acquistare altri sistemi di granulazione dello stesso modello da Maag, di cui uno è già stato fornito nell’ottobre del 2023”, afferma Imbrighi
Oltre all’acquisto dei citati sistemi di granulazione in bagno d’acqua (WSG), o a taglio sommerso, Lati fa già il passo successivo. Con il sistema EBG semiautomatico di Maag, sviluppato appositamente per il compounding di prodotti sensibili all’acqua, ad alta carica e fragili, il produttore italiano leader di compound speciali reagisce ai maggiori requisiti richiesti dai suoi clienti.
La particolarità del sistema EBG è che i trefoli (“spaghetti”) di polimero sono estrusi direttamente su un nastro trasportatore, o su uno scivolo ad acqua, e l’intero trasporto degli spaghetti di polimero avviene attivamente dalla testa d’estrusione al granulatore. Il vantaggio è che, se durante il funzionamento gli spaghetti si rompono, normalmente il prodotto viene ricondotto automaticamente al granulatore. Di conseguenza, questo sistema convince rispetto alla granulazione in bagno d’acqua convenzionale, soprattutto per masterbatch e compound molto fragili o ad alta carica. Inoltre, sul sistema EBG di Maag è possibile raffreddare compound sensibili all’acqua e ad alta carica senza contatto diretto con l’acqua: una prerogativa in parte imprescindibile che, in fin dei conti, garantisce eccellenti valori di umidità residua nel granulato.
“A volte si deve accettare che un costruttore di macchine proponga soluzioni diverse rispetto a un utilizzatore (in alcuni casi perfino migliori), proprio perché ha un maggiore grado di specializzazione”, spiega il direttore Technology & Innovation. Il progetto ha confermato che fornitori come Maag possono supportare a lungo termine aziende per la lavorazione della plastica come Lati e aiutarle a riconoscere nuove opportunità di sviluppo… non solo nel settore dei sistemi di granulazione.
“Gli ottimi risultati ottenuti con l’inserimento del nuovo granulatore hanno portato Lati a selezionare Maag come partner per gli importanti investimenti in corso, finalizzati all’aumento della capacità produttiva del sito di Torba (Gornate Olona, Varese). Da qui la decisione di dotarsi di ulteriori cinque nuove macchine che saranno consegnate nel corso del 2024, fondamentali per completare il fine linea di due nuovi estrusori ad alta capacità”, conclude Diego Imbrighi.
Alexander Helm, product manager Dry Cut, e Jürgen Skanda, sales manager Pelletizing di Maag Group