di Roberto Carminati
Con la sua ventinovesima edizione, il Congresso Annuale dell’Associazione dei Tecnici delle Materie Plastiche (TMP), organizzato il 21 novembre in collaborazione con la rivista Plastix, è riapprodato alla storica sede dell’NH Congress Center di Milanofiori (Assago, Milano) in una fase di indubbia difficoltà per l’industria.
Con oltre 500 iscritti, in mattinata il Congresso ha cercato di fare luce su alcuni comparti strategici per l’industria della plastica, automotive ed elettrodomestico, alle prese con una crisi strutturale dettata anche dall’emergenza ambientale, per dare poi voce e visibilità agli studenti premiati per le loro ricerche.
Nella seconda parte della giornata le aziende sponsor hanno invece illustrano le soluzioni studiate per fronteggiare questo complesso periodo e rispondere alle richieste sempre più pressanti dei clienti in tema di sostenibilità. L’innovazione declinata nei tre pilastri dell’industria della plastica, tecnologie, materiali e processi, è stata la vera protagonista degli interventi tecnici del pomeriggio.
Abbiamo così assistito alla descrizione di processi realmente sostenibili, alla presentazione di materiali rispettosi dell’ambiente e di tecnologie green.
Sui prossimi numeri della rivista Plastix e sui nostri canali social troverete tutti gli approfondimenti. Ma torniamo ai dati della mattina…
Dati e mercati: un quadro nebuloso
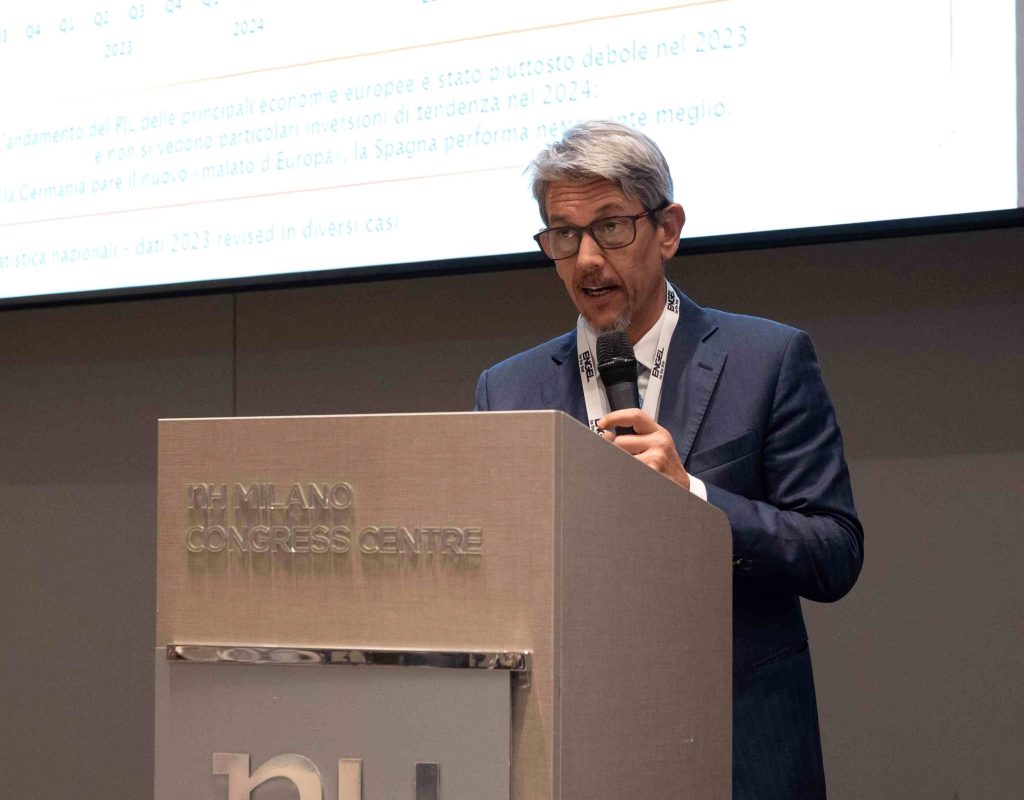
La congiuntura, si sa, è quel che è: la bilancia commerciale delle materie plastiche toccava quota 4,7 miliardi di euro nel 2012 e nel 2023 non è andata oltre i 4,3; la domanda di manufatti potrebbe registrare un calo dell’1,25% a fine anno, dopo una flessione pari al 2,3% circa nel quarto trimestre.
Se a questo si sommano le difficoltà di un tradizionale Paese di sbocco quale la Germania – dove la produzione industriale segnava un -7,4% lo scorso maggio – e quelle dell’auto (dal 2019 l’Europa ha contato tre milioni di unità vendute in meno) si ottiene dell’economia del 2024 un quadro fosco. L’ombra della crisi si estende ben al di là della lavorazione dei polimeri e la riflessione sulle criticità da affrontare e risolvere quanto prima ha caratterizzato una buona parte delle relazioni mattutine in agenda al ventinovesimo Congresso TMP.
Col verde, non si passa
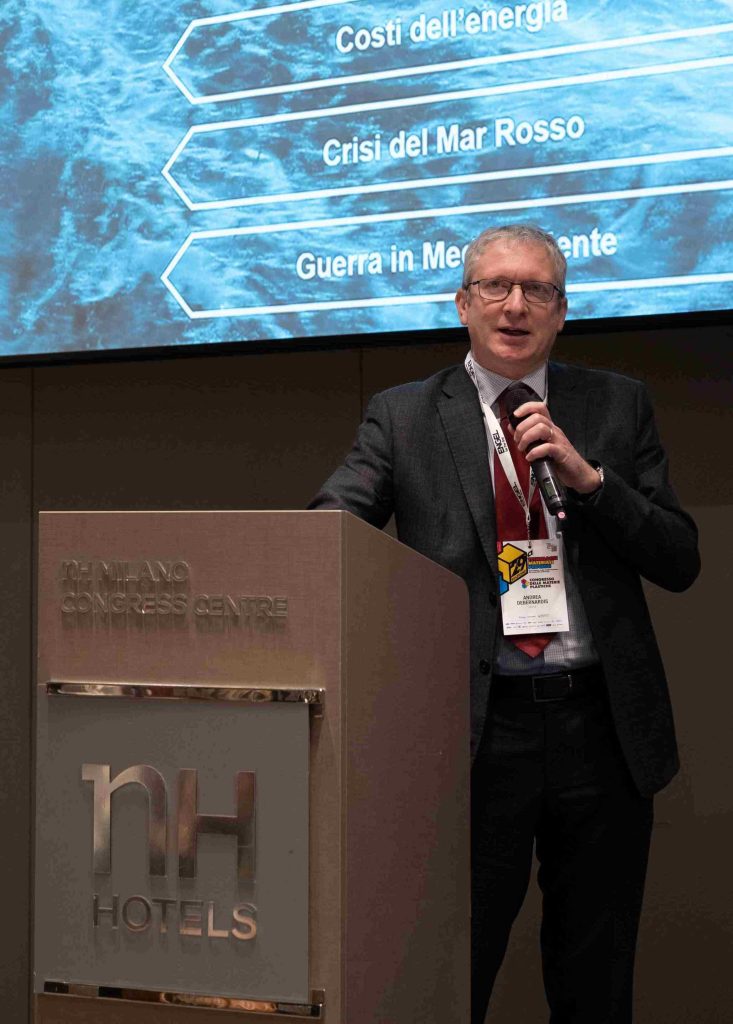
Alle cifre illustrate rispettivamente dal direttore di Plastic Consult, Paolo Arcelli, e dal responsabile per la componentistica auto di Anfia (sigla di rappresentanza della filiera automotive), Andrea Debernardis, si sono aggiunte quelle di Paolo Falcioni, direttore generale di Applia. Quest’ultima dà voce ai produttori di apparecchi domestici e professionali nel nostro Paese e si trova alle prese con le numerose quanto complicate sfide della transizione green.
Prendendo a esempio il settore del bianco, Falcioni ha notato come gli elettrodomestici siano realizzati per il 23% in plastica, ma solo l’1% di tale contenuto provenga da materiali riciclati. Perché l’idea di circolarità possa acquisire reale valore e significanza è necessario lavorare – pure di concerto con realtà internazionali quali Circular Plastics Alliance – su tre concetti chiave: quantità, qualità e costo dei processi e dei prodotti. I margini di miglioramento sono senza dubbio ampi: basti pensare che nel post consumo è solo poco più di un terzo dei rifiuti elettronici e casalinghi a essere avviato al riciclo. Tornando poi brevemente alla mobilità privata, tematica trattata dal senior economist di Allianz Trade, Luca Moneta, l’impressione è che lo scarso appeal delle vetture elettriche sia dovuto a fattori molteplici.
L’ecodesign ci salverà
Fra questi c’è anche la debolezza della rete delle infrastrutture: se in Italia gli ICE (Internal Combustion Engine) godono tuttora delle quote di mercato più rilevanti e i modelli elettrici arrancano è anche perché le colonnine di ricarica disponibili ogni cento chilometri sono un decimo rispetto a quelle della minuscola Olanda.
Materie plastiche e relativo recupero o riuso e sostenibilità possono però viaggiare a braccetto se sostenute da una ricerca innovativa. È questa la strada intrapresa da Gewiss e spiegata al pubblico di TMP dal sourcing raw materials and metal manager della divisione acquisti e servizi generali, Luca Sorrentino. Per raccogliere la sfida del rispetto per l’ambiente l’azienda ha dato vita a una business unit dedicata alla mobilità e ha puntato sull’ecodesign, facendo tesoro, da un lato, dell’uso di materiali da riciclo e, dall’altro, garantendo un completo recupero dei suoi articoli giunti a fine vita.
L’adozione di scelte progettuali precise – un facile disassemblaggio delle parti in plastica e di quelle metalliche è decisivo – è fonte per Gewiss di vantaggi economici; non soltanto di ecocompatibilità. L’esempio è dato dai cavi universali di ricarica per veicoli elettrici della serie I-Cord, creati facendo ampio ricorso ai tecnopolimeri speciali da recupero della gamma Renycle®. Si può sempre fare di più e Gewiss non si tira indietro. Sono composte per poco meno del 70% (il 68% per la precisione) anche alcune sue famiglie di borse porta cavi, che spiccano per il 100% di riciclabilità.
Un podio in verde
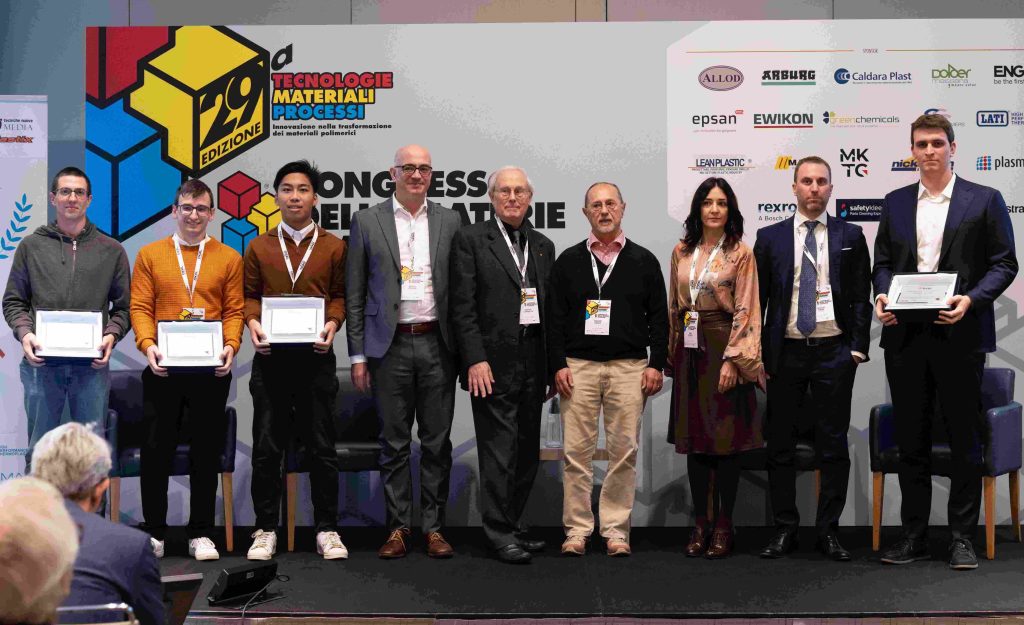
È necessariamente verde – ma nella circostanza il rispetto per l’ambiente c’entra sino a un certo punto: il colore è quello della giovane età – il parterre dei vincitori del Premio di Laurea TMP, al quale, per il secondo anno consecutivo, si è accompagnato il riconoscimento a due talenti usciti dagli ITS. Partendo da qui, un’ideale medaglia è stata assegnata a Christian Sacchetti della Fondazione Jobs Academy di San Paolo d’Argon, in provincia di Bergamo. La motivazione è data dal valore delle attività di sperimentazione, progettazione, stampaggio, termoformatura e verifica di manufatti plastici, condotte in occasione degli stage annuali compiuti presso aziende del settore.
Insieme a lui è salito sul podio per la Fondazione ITS “Nuove tecnologie della vita” di Lainate (Milano) June Junior Buera. Ha lavorato sul finishing di polimeri fluorurati che trovano applicazione nell’ambito della produzione di energia elettrica a emissioni zero, tramite celle a combustibile con membrane a scambio protonico.
Provenienti dagli atenei di più regioni del Nord Italia, anche i laureati hanno affrontato e studiato argomenti di stretta attualità: materiali che si autoriparano, riciclo chimico e biopolimeri. Il primo classificato, Mirko Coser, ha studiato al dipartimento di Industrial Engineering dell’Università di Trento ed è autore della tesi dal titolo: “Development of thermoplastic carbon fiber reinforced composites with self-healing capability”. Per questo ha sviluppato una PA6 rinforzata con fibre di carbonio con proprietà autoriparanti, grazie all’uso di copolimeri olefinici ciclici che permettono il recupero parziale delle proprietà del materiale vergine.
Alle sue spalle, sempre da un dipartimento di Ingegneria Industriale ma dell’Università di Padova, si è piazzato Niccolò Cenzato col lavoro “Valorization of biopolymers waste through chemical recycling”. Al centro, il riciclo chimico del PBAT tramite glicolisi, al fine di ottenere precursori in forma liquida per la produzione di schiume poliuretaniche dalle caratteristiche molto simili a quelle dei benchmark utilizzati.
Infine, Alejandro Lopez Olmedo ha utilizzato polimeri vitrimerici per la produzione di laminati. Ha così dimostrato il loro potenziale come materiali di riparazione dei danni da delaminazione, fornendo una possibile soluzione per ridurre lo scarto dei componenti in materiali compositi. Il titolo della tesi, portata a termine presso la Scuola di Ingegneria industriale e dell’informazione del Politecnico di Milano, è: “Repairing of Woven Glass Fibre and Vitrimer Matrix Composites Fractured in Mode I and II”.