Oltre 500 visitatori hanno affollato il Design Center di Linz e lo stabilimento di Engel a St. Valentin, in Austria, per gli Engel Mobility Days 2023, nei giorni 14 e 15 giugno. La redazione di Plastix era presente alla conferenza stampa condotta dal CEO Stefan Engleder sulle novità tecnologiche di Engel per il settore della mobilità, che non riguardavano solo l’automotive, ma anche la micromobilità urbana (con moto, e-scooter e bici elettriche) e addirittura l’aeronauticae i cosiddetti “air cab” (aerotaxi).La due giorni di Engel, supportata da KTM Technologies, con relatori d’alto livello e l’esposizione di macchine orientate al futuro, ha unito e ampliato le precedenti conferenze Engel trend.scaut e Lightweight Future Day per creare un nuovo evento di networking.
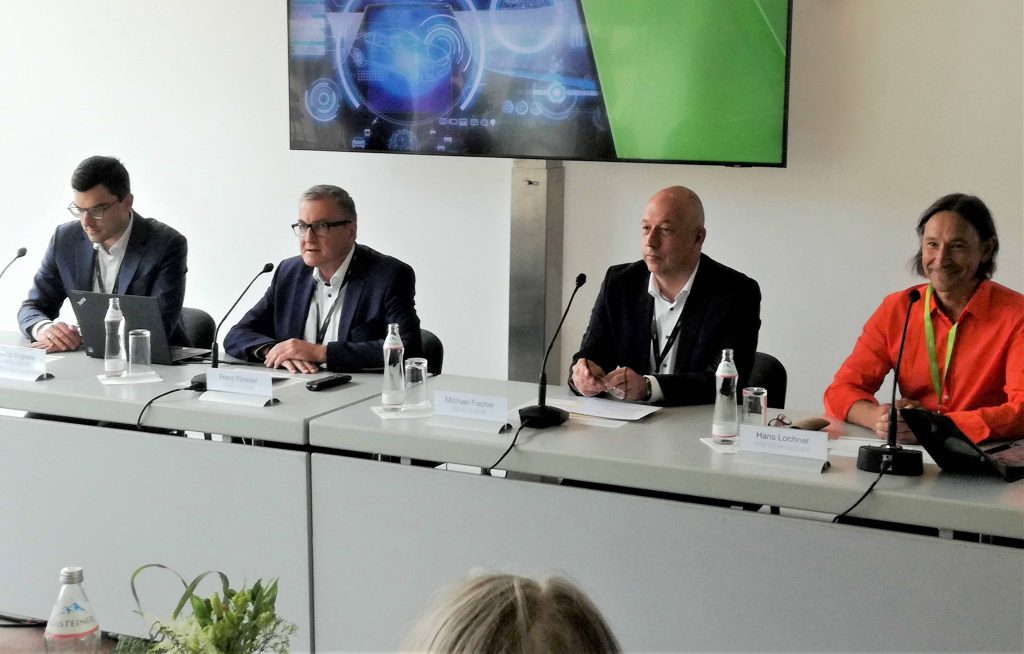
“Ma c’è un trend che accomuna tutti i settori della mobilità… ed è quello volto a rendere i mezzi di trasporto più sostenibili”, ha dichiarato Stefan Engleder. Infatti, sia che si tratti di nuove soluzioni di trasmissione o di guida autonoma, queste tendenze stanno cambiando radicalmente le esigenze di mobilità, richiedendo in alcuni casi soluzioni produttive e materiali completamente nuovi. Ciò crea enormi opportunità per l’industria dello stampaggio a iniezione.
“Le materie plastiche svolgeranno un ruolo ancora più significativo nella mobilità del futuro di quanto non svolgano oggi”, ha sottolineato Franz Füreder, vicepresidente della business unit Automotive & Mobility di Engel. “I materiali polimerici sono di per sé leggeri e consentono un uso conservativo di energia e materie prime. Possono essere processati in modo molto efficiente tramite lo stampaggio a iniezione, e questo rende le tecnologie innovative accessibili anche al mercato del largo consumo”. Gli Engel Mobility Days 2023 hanno mostrato numerosi esempi d’applicazione in questo ambito.
La guida autonoma promuove l’uso della plastica
Michael Fischer, direttore della divisione Development Technology di Engel, ha messo in evidenza un ulteriore vantaggio: “Le materie plastiche sono permeabili alle onde sonore e alle radiazioni elettromagnetiche e questo le rende indispensabili per la guida autonoma. Per questo hanno già sostituito alluminio e acciaio nella parte anteriore e posteriore delle automobili”. I sensori di distanza, per esempio, funzionano con gli ultrasuoni, mentre il cruise control adattivo si basa su radar e i sistemi d’assistenza per la visione notturna utilizzano gli infrarossi.
“Più efficiente di qualsiasi altro metodo di lavorazione della plastica, lo stampaggio a iniezione aiuta a combinare sistemi di sensori e caratteristiche elettroniche con un design visivamente accattivante”, ha aggiunto Fischer. In particolare, Engel ha sviluppato la sua tecnologia clearmelt per questo scopo: un processo bicomponente che combina la decorazione in stampo (IMD) con il rivestimento in poliuretano (o “flood-coating”), che consente di ottenere una superficie liscia perfettamente ripetibile e uno spessore parete uniforme, ideali per l’integrazione dei sensori ottici.
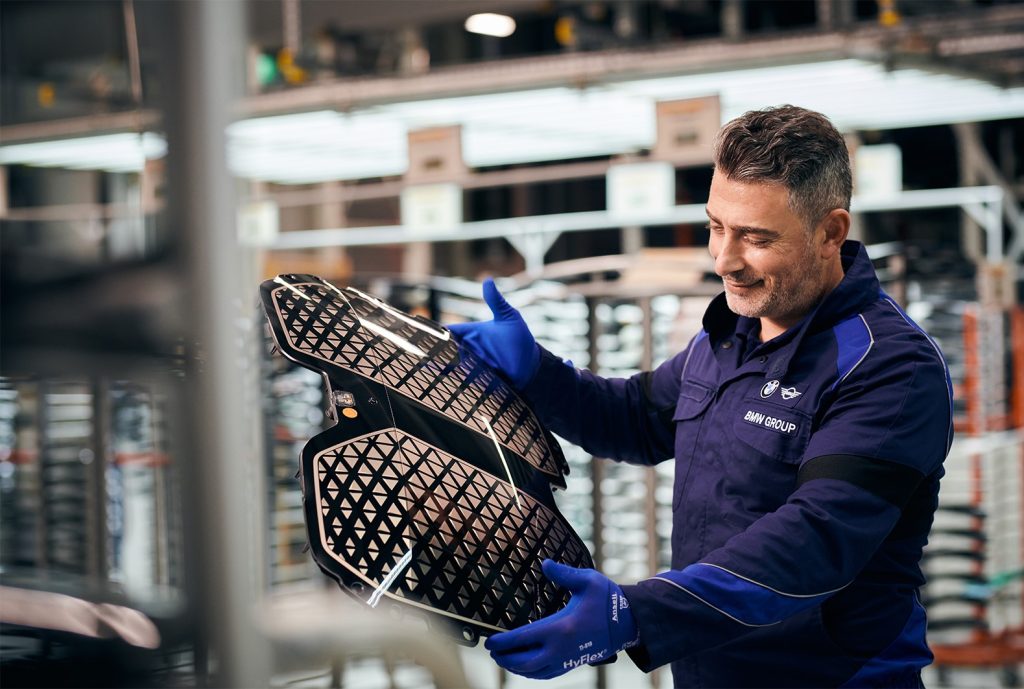
La casa automobilistica BMW utilizza questa base tecnologica per produrre in camera bianca i suoi tipici pannelli “a forma di rene” per il veicolo elettrico iX. Questo design che una volta caratterizzava la griglia del radiatore di tutti i modelli BMW, ha assunto un nuovo ruolo dopo l’elettrificazione delle trasmissioni. Oggi i pannelli “a forma di rene” proteggono infatti una serie di sensori per la guida assistita e, in futuro, autonoma. Per garantire che i sensori funzionino in modo affidabile anche in inverno, BMW retroinietta con policarbonatouna pellicola funzionale riscaldabile, che viene poi rivestita con poliuretano.
Dopo diverse applicazioni per l’interno del veicolo, questa è la prima volta che BMW utilizza una combinazione di retroiniezione di film e rivestimento in stampo con PU per la produzione in serie di parti funzionali per esterni auto, esposte a sollecitazioni particolarmente elevate. L’elettronica “touch” è ben protetta sotto la superficie in poliuretano antigraffio. L’alto livello di brillantezza e l’effetto di profondità (che può raggiungere anche un sottile strato di poliuretano) trasmettono una sensazione d’eleganza. L’isola di produzione utilizzata integra una pressa a iniezione Engel duo combi M con tavola rotante orizzontale, due grandi robot antropomorfi per la manipolazione dei film e dei pezzi stampati, un sistema di pulizia del film, una stazione di controllo qualità in linea e diverse unità periferiche, compreso il sistema d’alimentazione del poliuretano.
Nell’ambito di un progetto pilota, le aziende partner (tra cui Leonhard Kurz Stiftung, Schöfer e Votteler Lackfabrik) sono state in grado di dimostrare che il rivestimento in stampo con PU, che equivale alla verniciatura in stampo (in-mould painting) in termini di processo, rappresenta solo il 20% dell’energia totale consumata per produrre un articolo. Ciò significa che il processo integrato offre un’efficienza energetica notevolmente migliore rispetto alla verniciatura delle parti fuori linea.
Compositi leggeri ed efficienti realizzati con i termoplastici
La leggerezza gioca un ruolo centrale nel raggiungimento degli obiettivi di protezione del clima. Nel proprio centro tecnologico interdisciplinare per i compositi leggeri, presso lo stabilimento di produzione di St. Valentin, Engel sta sviluppando da oltre dieci anni soluzioni composite innovative in collaborazione con diversi partner. Il suo obiettivo principale è quello di mettere a punto processi integrati e automatizzati per una produzione su larga scala economicamente vantaggiosa con l’uso di materiali termoplastici. “Il motivo è duplice: da un lato i processi di lavorazione dei termoplastici sono altamente efficienti e, dall’altro, tali materiali sono pure più sostenibili, poiché facilmente riciclabili”, ha affermato Füreder.
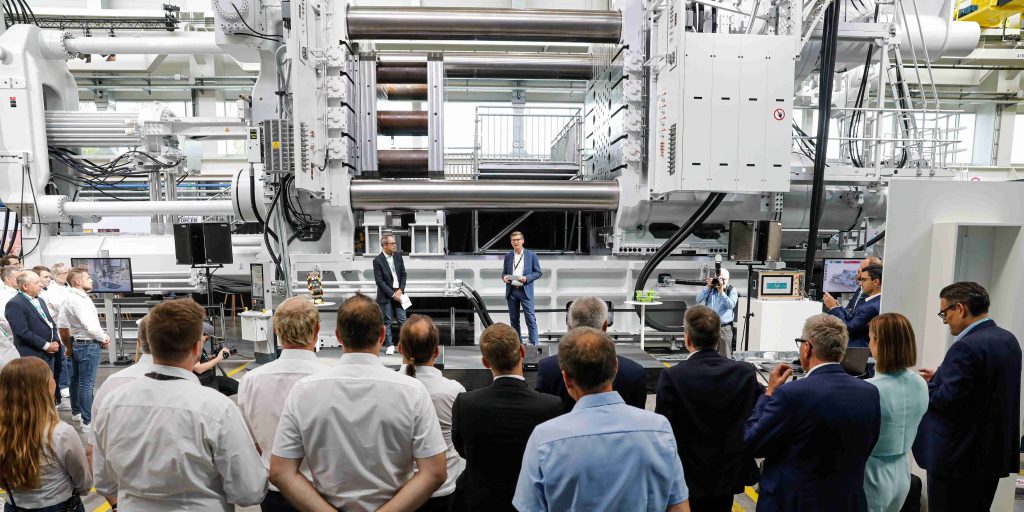
Nel processo organomelt di Engel, le foglie preimpregnate (prepreg) a base di compositi termoplastici fibrorinforzati – come per esempio foglie in termoplastico o nastri unidirezionali (UD-tape) – vengono modellate e funzionalizzate in un unico passaggio. Per ottenere tale funzionalizzazione, le nervature di rinforzo o gli elementi d’assemblaggio vengono stampati nello stesso stampo immediatamente dopo la termoformatura, usando un termoplastico appartenente allo stesso gruppo di materiali della matrice della foglia utilizzata.
La prima applicazione su larga scala di questa tecnologia è datata 2018 ed è stata realizzata presso la società Valeo Front End Modules di Smyrna, in Tennessee (USA). Partendo da foglie in termoplastico, Valeo produce per un OEM tedesco supporti per pannelli frontali con condotte dell’aria integrate. La soluzione fornita da Engel per la produzione automatizzata in grandi volumi prevede una pressa a iniezione duo 1700, tre robot articolati Engel easix per la preparazione di grandi quantità d’inserti metallici e per la movimentazione della foglia termoplastica, un robot lineare Engel viper 90 e un forno IR sempre a marchio Engel.
La struttura a doppio guscio ha permesso d’integrare le condotte dell’aria direttamente nella struttura portante. I due semigusci sono prodotti in un unico processo “one-shot”. Per ottenere tutto questo, le due lastre termoplastiche vengono riscaldate contemporaneamente nel forno IR e quindi inserite nello stampo, dove vengono formate e funzionalizzate.
Riciclo innovativo di pezzi in composito fibrorinforzato
Il riciclo dei componenti in composito rinforzato con fibre è un altro obiettivo di sviluppo presso l’Engel Technology Center for Lightweight Composites. “Prevediamo che in futuro il riciclo nel settore automobilistico giocherà un ruolo importante nel restituire molte parti in poliammide e polipropilene fibrorinforzate al ciclo produttivo monomateriale. Tuttavia, le fibre di vetro si accorciano quando i pezzi vengono triturati. Per produrre nuovamente parti composite d’alta qualità partendo dai materiali recuperati, le nuove fibre devono essere miscelate durante la lavorazione dei materiali riciclati”, ha spiegato Fischer. “Stiamo quindi lavorando a una soluzione che consenta di modulare le proprietà del materiale in modo più efficiente”.
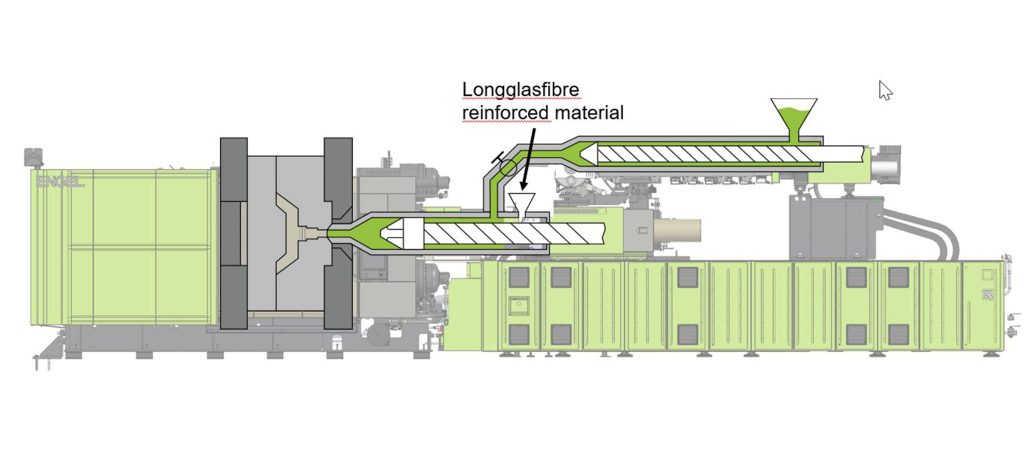
La base è il nuovo processo a due stadi (estrusore per compounding + unità d’iniezione) che Engel ha presentato alla fiera K 2022. Per poter integrare un filtro per il fuso e un’unità di degassaggio, le fasi di plastificazione e di iniezione sono state rese indipendenti, ma sincronizzate. Grazie a questa strategia, i rifiuti in plastica possono essere stampati sotto forma di scaglie direttamente dopo la granulazione, ottenendo comunque una qualità eccellente.
Poiché si tratta di una lavorazione completa, la fase di compounding viene eliminata e il processo a due stadi consente di risparmiare un’enorme quantità d’energia e lavoro rispetto al riciclo tradizionale. Per poter riprocessare le parti triturate in composito fibrorinforzato per creare parti di veicoli in grado di sopportare carichi meccanici elevati, Engel sta ora integrando un sistema per l’alimentazione delle fibre di vetro in aggiunta al filtro per il fuso. Le fibre di vetro lunghe vengono mescolate prima dell’iniezione del fuso. “In questo caso, siamo nella fase di prove iniziali, che però paiono molto promettenti”, ha aggiunto Fischer.
Tecnologia “tape sandwich” in anteprima mondiale
Sostenuti da KTM Technologies, gli Engel Mobility Days 2023 hanno visto un’anteprima mondiale: una base per sella di motocicletta prodotta utilizzando il nuovo processo “tape sandwich”.
“Stiamo installando un numero crescente di componenti elettronici sui nostri veicoli e abbiamo quindi bisogno di spazio per farlo”, ha affermato in conferenza stampa Hans Lochner, responsabile Material and Applications presso la società KTM Technologies di Anif, Salisburgo. A causa dell’elettrificazione della trasmissione, questo trend non sta avendo un impatto importante solo sui produttori di moto e biciclette, ma sull’intero settore della mobilità.
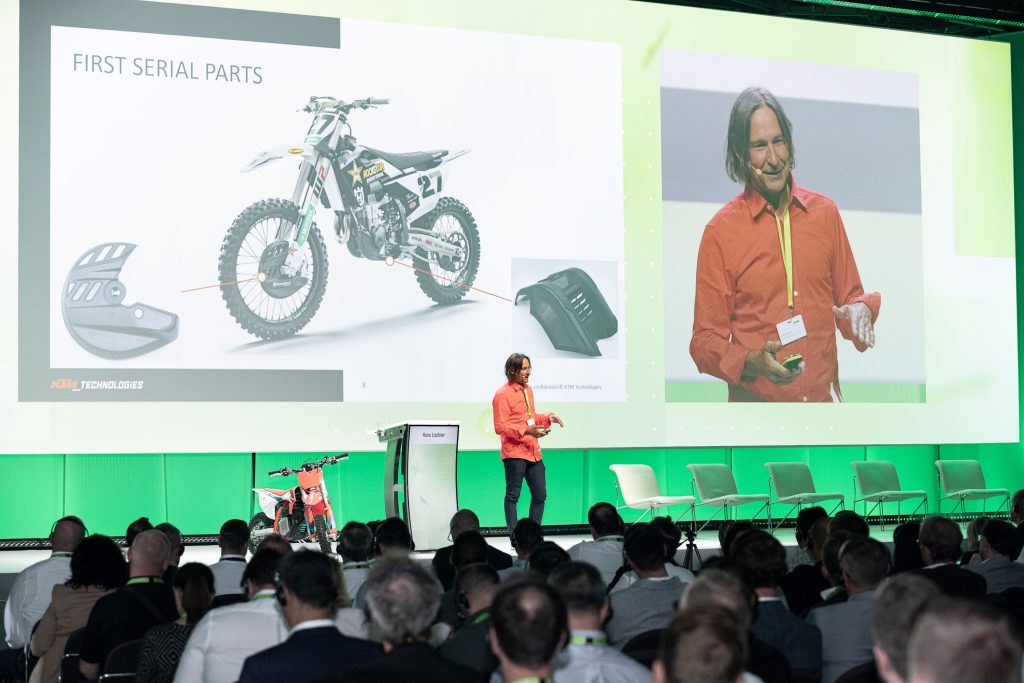
Per offrire valore aggiunto ai mercati di largo consumo, oltre ai vantaggi tecnici, è necessario un processo di produzione efficiente in termini economici. Engel e KTM Technologies hanno così deciso di unire le loro competenze per un lavoro di sviluppo congiunto. Engel sta contribuendo con la sua esperienza nelle tecnologie per la produzione di componenti leggeri e nell’industrializzazione, mentre KTM è responsabile dell’ideazione e dello sviluppo tecnologico su misura per il prodotto finale. A loro si è aggiunto, come terzo partner di sviluppo, il produttore di stampi Feronyl, con sede in Belgio.
Finora, le basi dei sedili per moto KTM erano realizzate completamente in resine termoplastiche stampate a iniezione. La rigidità richiesta veniva ottenuta mediante “irrigidimento geometrico” (ad esempio tramite nervature), che porta però a uno spessore del pezzo relativamente elevato, fino a 9 mm. Per ridurre lo spazio necessario per l’installazione e liberarne altro per la parte elettronica, KTM ha esaminato da vicino i materiali compositi e i relativi processi di produzione e, in collaborazione con Engel, ha messo a punto un processo produttivo caratterizzato da un livello d’efficienza particolarmente elevato e denominato “tape sandwich” (che può essere tradotto come sandwich di nastri o, più genericamente, come sistema multistrato).
Due terzi in più di spazio per l’installazione, ma rigidità identica e riduzione del GWP
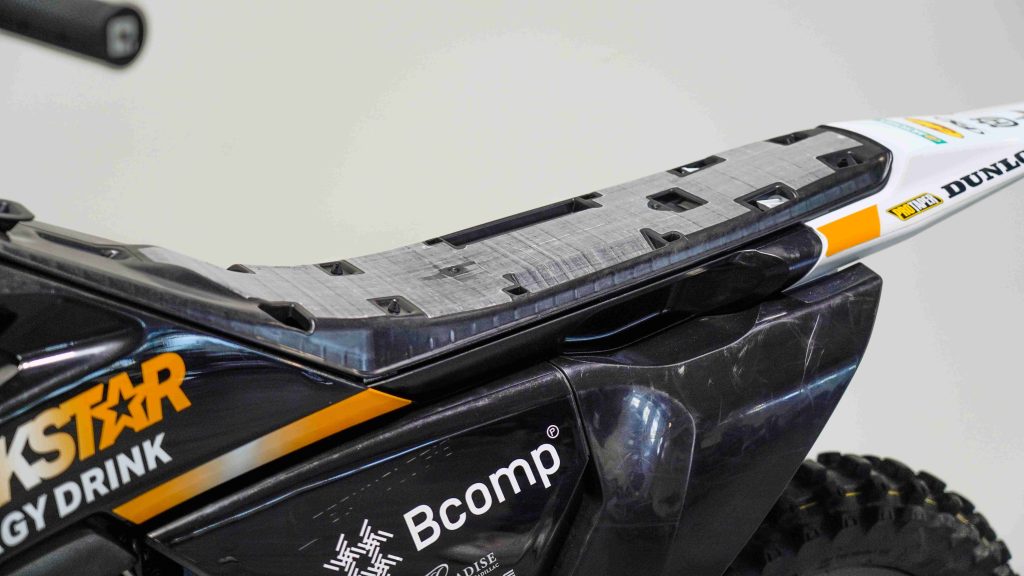
“Nel processo tape sandwich, lavoriamo con materiali di rinforzo monostrato molto sottili, come nastri e tessuti con matrice in polipropilene, che vengono inseriti in entrambe le semicavità dello stampo senza preriscaldamento, prima del riempimento con polipropilene”, ha spiegato Franz Füreder. “Grazie alle specifiche proprietà meccaniche della struttura a sandwich, possiamo già soddisfare la rigidità richiesta per le basi dei sedili con un nastro UD monostrato. Ciò significa che questo processo richiede molta meno energia e isole produttive tecnologicamente più semplici rispetto ai tradizionali metodi di lavorazione dei compositi fibrorinforzati. Nello stesso tempo, i costi di produzione diminuiscono”.
Nel caso del “dimostratore tecnologico” esposto agli Engel Mobility Days, per il fondo del sedile con rigidità identica a quello tradizionale, lo spazio necessario per l’installazione può essere ridotto del 66% e il peso di circa il 26%. “La nuova struttura a sandwich offre la massima rigidità riducendo al minimo il numero delle fibre richieste”, ha affermato Lochner. Un altro vantaggio della struttura a sandwich è che i materiali termoplastici standard possono essere utilizzati in componenti esposti a sollecitazioni meccaniche elevate, poiché le prestazioni del pezzo sono definite esclusivamente dalla struttura a nastri. E questo aumenta anche l’economicità del processo.
I partner di sviluppo hanno testato un’ampia varietà di materiali per lo stampaggio a iniezione, compresi gradi di PP a base biologica e riciclati, oltre al PP convenzionale da fonti fossili. È stato quindi misurato il potenziale di riscaldamento globale (GWP) per le varie combinazioni di materiali e, rispetto alla versione di serie (un sedile realizzato interamente in PP “fossile”), la tecnologia “tape sandwich” riduce il GWP del 27% quando si utilizza anche PP fossile: questo valore si ottiene esclusivamente riducendo il materiale. Con il polipropilene da fonti rinnovabili, invece, il valore di GWP si riduce addirittura dell’85%. In ogni caso, il peso dei componenti è stato ridotto del 26%, grazie al fatto che anche i componenti molto sottili raggiungono un’elevata rigidità.
Nella visione generale, l’approccio monomateriale contribuisce anche alla riduzione dei gas serra. In combinazione con i nastri a matrice polipropilenica, è possibile creare pezzi che possono essere riciclati al termine della loro vita in esercizio. “Questo nuovo sviluppo ci vede aprire una soluzione economica e sostenibile per la mobilità del futuro”, ha concluso Füreder.