Prosegue il nostro viaggio nel vasto e variegato mondo dei polimeri che ci porterà alla scoperta delle proprietà uniche di ogni materiale, delle sue applicazioni specifiche, delle tecniche di lavorazione delle possibilità di riciclo. Nella prima puntata, pubblicata sulla rivista Plastix di marzo, abbiamo parlato del polietilene, nella seconda del polipropilene e questa è la volta del polistirene: dalle auto alle tavole da surf, questo materiale e i suoi derivati si contraddistinguono per l’elevata versatilità nelle applicazioni
Nel vasto universo dei materiali polimerici, il polistirene (PS) si distingue come uno dei polimeri più versatili e ampiamente utilizzati. Questa plastica unica, che può essere prodotta anche in forma espansa, è diventata un elemento fondamentale nella produzione di una miriade di prodotti, dai contenitori per alimenti agli imballaggi, dimostrando la sua indispensabilità nella vita quotidiana. Il polistirene solido si fa apprezzare per la sua rigidità e la trasparenza simile al vetro, mentre il polistirene espanso è utilizzato per la sua leggerezza e capacità isolante. La popolarità del polistirene è attribuibile al suo basso costo (assieme a PE, PP e PVC, è una delle quattro plastiche considerate “commodity”), alla sua eccellente lavorabilità e a proprietà distintive quali l’elevata rigidità, che lo rendono adatto a un’ampia gamma di applicazioni.
Al di là del polistirene tradizionale, l’innovazione nel campo dei polimeri ha portato allo sviluppo di numerosi copolimeri del polistirene, che estendono ulteriormente le applicazioni e le funzionalità di questo materiale. I copolimeri, creati dalla polimerizzazione dello stirene con altri monomeri, offrono nuove proprietà e caratteristiche. Tra questi, il polistirene ad alta resistenza all’impatto (HIPS) e l’acrilonitrile-butadiene-stirene (ABS) si distinguono per la loro maggiore resistenza agli urti. Questi materiali innovativi non solo ampliano le possibilità d’utilizzo del polistirene, ma aprono anche nuove frontiere nel design dei prodotti, dalla elettronica all’edilizia, evidenziando la continua evoluzione e l’adattabilità del polistirene alle esigenze moderne.
Struttura e proprietà
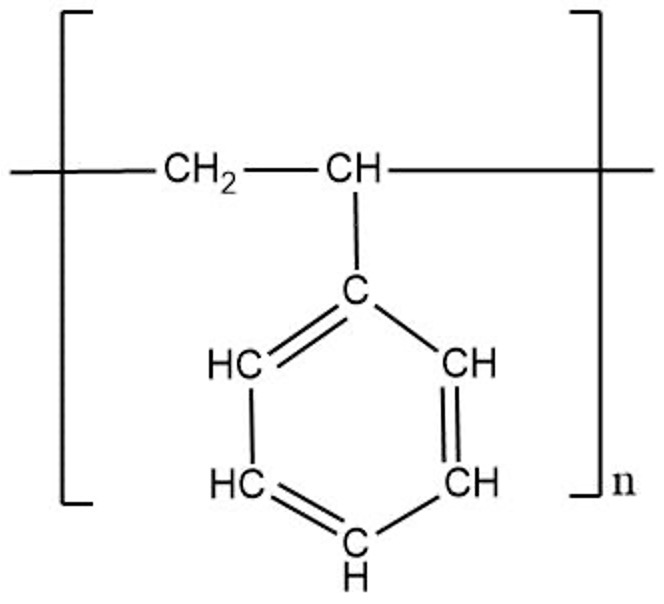
Dal punto di vista chimico, il polistirene può essere descritto come un “polivinilbenzene”: un idrocarburo a catena lunga in cui gli atomi di carbonio sono legati a gruppi fenilici (un derivato del benzene) in modo alternato, come illustrato in figura 1. Il polistirene commercialmente più significativo è quello atattico, con gruppi fenilici disposti in modo casuale su entrambi i lati della catena polimerica (vedi figura 2). Questa disposizione aleatoria impedisce la formazione di domini cristallini, rendendo il polistirene standard (atattico) un materiale termoplastico amorfo e trasparente. Il posizionamento casuale dell’ingombrante gruppo fenilico impedisce alle catene di allinearsi con la regolarità necessaria per ottenere una struttura cristallina, conferendo al materiale una temperatura di transizione vetrosa (Tg) di circa 100°C.
L’uso di catalizzatori stereospecifici, sviluppati da Giulio Natta, porta alla formazione di polimeri isotattici nei quali tutti i gruppi fenilici si trovano nella stessa disposizione spaziale. Questi polimeri possono raggiungere fino al 50% di cristallinità e diventano opachi quando raffreddati lentamente dallo stato fuso, o dopo esposizione a temperature di 150°C.
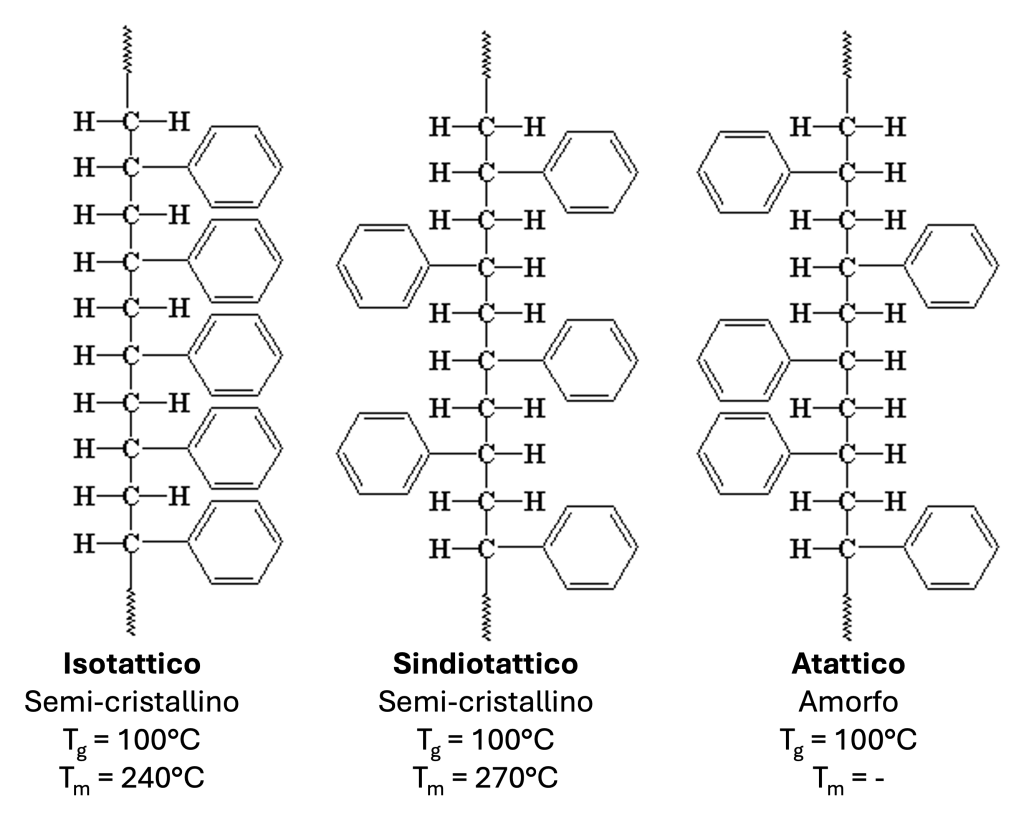
Il polistirene polimerizzato con catalizzatori metallocenici è conosciuto come sindiotattico. È cristallino e possiede una temperatura di fusione di 270°C; per questa ragione, è considerato una plastica resistente alle alte temperature, seppur poco utilizzata.
Il PS omopolimero si distingue per la sua trasparenza cristallina e lucentezza. Ha un modulo elastico molto elevato, ma è fragile e quindi meno adatto a carichi dinamici. La resistenza all’usura, all’abrasione e all’assorbimento d’acqua sono minimi, mentre la stabilità dimensionale è elevata. Il PS mostra eccellenti proprietà elettriche e dielettriche; è resistente all’umidità e a soluzioni saline, alcali e acidi non ossidanti. Tuttavia, esteri, chetoni, idrocarburi aromatici e clorurati agiscono come solventi.
Effetto della temperatura sulla rigidità
La figura 3 mostra la dipendenza del modulo elastico dalla temperatura per due polimeri commodity che sono spesso considerati in alternativa l’uno all’altro: il polipropilene e il polistirene. Entrambi i materiali testati non sono rinforzati. Il PP è un polimero semicristallino, mentre il PS è amorfo, e i risultati mostrati rappresentano il comportamento tipico di queste due classi di materiali. A temperatura ambiente, il modulo elastico di entrambi i materiali concorda con il modulo di trazione riportato sulla scheda tecnica.
Il PS amorfo presenta una sola temperatura di transizione a circa 100°C, nota come temperatura di transizione vetrosa (Tg). Questa rappresenta la temperatura alla quale le singole catene polimeriche diventano sufficientemente mobili a livello molecolare da potersi muovere indipendentemente, nonostante rimangano aggrovigliate. Strutturalmente, questo evento può essere paragonato a una temperatura di rammollimento e, a fini ingegneristici, il materiale perde tutte le proprietà strutturali quando attraversa questa fase di transizione.
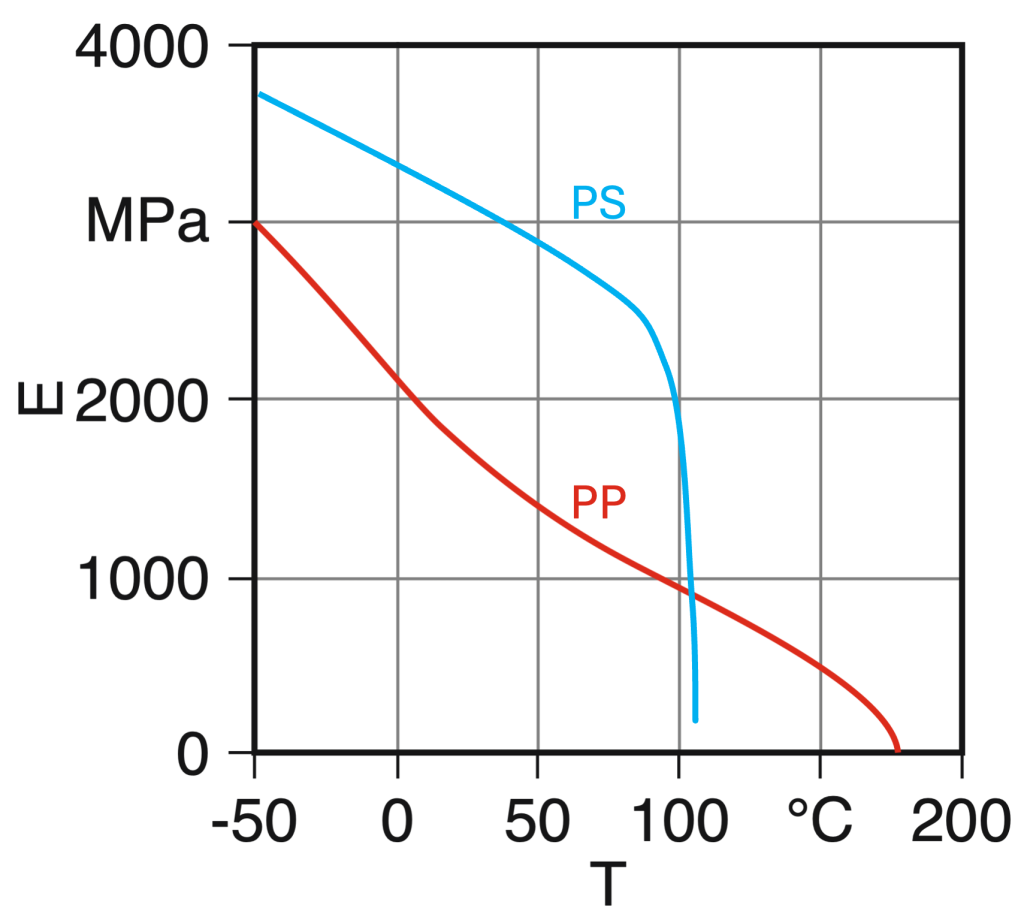
Tra la temperatura ambiente e l’inizio della transizione vetrosa, il modulo del PS si mantiene relativamente elevato, diminuendo di circa il 25% tra la temperatura ambiente e 90°C. Un valore che si accorda bene con la temperatura di deflessione sotto carico (HDT) indicata nella maggior parte delle schede tecniche. Tuttavia, tra la temperatura ambiente e la HDT, la maggior parte delle schede tecniche fornisce poche indicazioni sugli effetti della temperatura sulle capacità di carico.
Il comportamento del PP semicristallino è leggermente diverso da quello del PS amorfo. Il PP è definito semicristallino perché, come tutti i polimeri di questa classe, è costituito da una miscela strutturale di regioni cristalline e amorfe. Con l’aumento della temperatura, le regioni amorfe diventano mobili e questa mobilità è nuovamente segnalata dalla transizione vetrosa. Questa si verifica intorno ai -20°C e, di conseguenza, a temperatura ambiente il modulo è già molto diminuito e continua a calare, ma non crolla a zero come nel caso del PS, grazie alla presenza della struttura cristallina. Questa struttura organizzata conserva un livello ridotto di prestazioni che è mantenuto fino a quando la temperatura non sale al punto di fusione dei cristalli, ossia circa 170°C.
Tutti i polimeri amorfi seguono una risposta alla temperatura simile a quella del PS. L’unica differenza tra i vari polimeri amorfi, come PVC, PC e polisulfone, è la temperatura di transizione vetrosa. Il PP funge da modello per il comportamento in funzione della temperatura di tutti i polimeri semicristallini. Le caratteristiche che distinguono i polimeri semicristallini sono la temperatura di transizione vetrosa, la temperatura di fusione (Tm) e il grado di diminuzione del modulo associato alla transizione vetrosa. Per la maggior parte dei polimeri semicristallini non caricati, questo declino sarà pari al 60-90% del modulo pre-Tg. È importante sottolineare che la Tg e la Tm sono proprietà fondamentali per ogni polimero.
È possibile ridurre l’effetto della temperatura sul modulo elastico di un polimero semicristallino aggiungendo cariche e rinforzi. Si possono ottenere benefici simili nei polimeri amorfi a temperature inferiori alla Tg. Tuttavia, le temperature di transizione non cambiano. La Tg (per i polimeri amorfi) e la Tm (per i polimeri semicristallini) rappresentano il limite superiore a cui il polimero può operare in un ambiente applicativo, anche in un arco di tempo molto breve (qualche minuto).
Infine, in applicazioni dove è richiesta la rigidità strutturale a temperature che possono avvicinarsi a 100°C, il PS è preferibile al PP, il cui modulo elastico si riduce già significativamente a temperatura ambiente, poiché ha superato la sua Tg attorno ai -20°C. Per esempio, prodotti che devono mantenere la forma in condizioni d’esercizio con temperature abbastanza elevate, come componenti per apparecchiature elettroniche che possono generare calore durante il funzionamento, o imballaggi per oggetti che devono sopportare alte temperature durante il trasporto o lo stoccaggio, beneficiano delle proprietà del PS. Questa capacità di sostenere carichi a temperature più elevate fa del PS un materiale ideale per un’ampia gamma di applicazioni che richiedono rigidità e stabilità dimensionale.
Copolimeri e blend stirenici
Considerando la limitazione principale del polistirene (PS) omopolimero, ossia la sua fragilità che ne restringe l’uso in molte applicazioni pratiche, è fondamentale esplorare come le modifiche molecolari possano ampliare il suo ambito d’utilizzo. I copolimeri e i blend stirenici rappresentano un’evoluzione cruciale nel mondo dei polimeri, offrendo una modifica mirata delle proprietà del polistirene per soddisfare esigenze specifiche in diversi settori applicativi. Tra questi, il SAN (stirene-acrilonitrile) è particolarmente rilevante perché serve come base per la produzione di ABS (acrilonitrile-butadiene-stirene) e ASA (acrilonitrile-stirene-acrilato), con l’aggiunta di elastomeri. Questi materiali sono poi miscelati in blend come ABS + PC (policarbonato) e ABS + PA (poliammide), risultando in una modifica delle caratteristiche come la rigidità e la resistenza al calore, agli urti, alle sostanze chimiche e alla fatica.
La maggior parte dei polimeri stirenici è lavorata mediante stampaggio a iniezione, con temperature del fuso che variano da 180 a 280°C e temperature degli stampi da 5 a 80°C. Temperature degli stampi molto basse e velocità d’iniezione elevate (impostate per minimizzare il tempo di ciclo) possono però causare tensioni residue elevate e forte orientamento delle catene polimeriche, riducendo così la qualità a lungo termine dei pezzi prodotti.
Il PS ad alta resistenza agli urti (HIPS) è ottenuto mediante copolimerizzazione a innesto con elastomeri come la gomma stirene-butadiene (SBR). I blend di polimeri e i copolimeri di polistirene, inclusi quelli che contengono gomma EPDM (etilene-propilene-diene monomero), o elastomeri termoplastici come il poliuretano (PUR), offrono un equilibrio ottimale di proprietà termiche, meccaniche e di tenacità. Pur riducendo rigidità e resistenza, migliorano notevolmente la resistenza a fatica, anche a basse temperature. Sono disponibili in varianti opache e persino trasparenti.
L’ASA si distingue per la sua resistenza alle intemperie e al calore, grazie al contenuto di gomma acrilestere, rendendolo adatto per applicazioni all’aperto senza la necessità di rivestimenti o vernici aggiuntive. I blend ASA + PC offrono una resistenza al calore superiore rispetto all’ABS.
Per quanto riguarda l’ABS, la varietà nelle proprietà si ottiene attraverso la polimerizzazione a innesto di stirene e acrilonitrile su una catena di butadiene, o la produzione separata di questi componenti, che sono poi miscelati e granulati. Variando il componente in gomma e sostituendo lo stirene con α-metil stirene, è possibile controllare specificatamente la temperatura di transizione vetrosa e, di conseguenza, il punto di distorsione termica e la resistenza agli urti. Infine, l’ABS, noto per la sua elevata resistenza agli urti, diventa ancora più versatile quando combinato con il PC, migliorando ulteriormente la resistenza termica e le proprietà meccaniche.
I blend ABS + PC mostrano una maggiore resistenza al calore rispetto all’ABS puro. D’altra parte, i blend ABS + PA mitigano alcune proprietà meno favorevoli della PA, come la contrazione e la scarsa resistenza agli urti a basse temperature, risultando in materiali con ottima tenacità, lavorabilità, resistenza chimica e densità inferiore rispetto al blend ABS + PC. Inoltre, l’ABS e i relativi blend vengono spesso scelti perché permettono di realizzare plastiche cromate con finalità estetiche. Questa capacità rende l’ABS particolarmente apprezzato nell’industria automobilistica e in quelle applicazioni dove è richiesto un aspetto metallizzato duraturo (figura 4).
Il polistirene espanso
Il polistirene espanso (EPS) è un materiale che, per le sue caratteristiche uniche, trova un’ampia applicazione soprattutto in edilizia, come materiale isolante. Questo espanso è costituito da una struttura cellulare chiusa e rigida, con una densità che, in genere, varia da 11 a 32 kg/m3. Di solito è di colore bianco ed è prodotto da perle di polistirene pre-espanso.
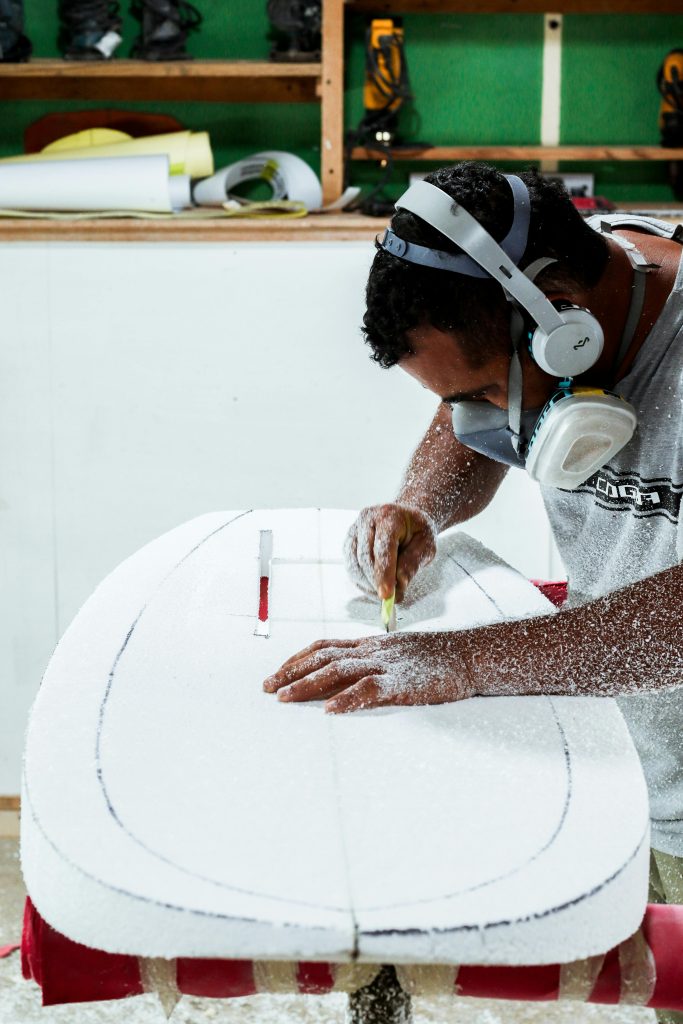
Il processo di produzione dell’EPS inizia con la creazione di piccole perle di polistirene. I monomeri di stirene, a cui possono essere aggiunti altri additivi, sono sospesi in acqua e lì subiscono una polimerizzazione per aggiunta radicalica libera. Queste perle di polistirene possono avere un diametro medio di circa 200 µm e vengono poi impregnate con un agente schiumogeno, come il pentano, che permette l’espansione delle perle. L’espansione avviene attraverso l’uso del vapore.
L’EPS non è solo impiegato per contenitori alimentari e pannelli per l’isolamento edilizio, ma è anche utilizzato come materiale da imballaggio, sia come blocchi solidi formati per adattarsi all’oggetto da proteggere sia come riempimento sciolto. Nelle applicazioni automobilistiche e per la sicurezza stradale, l’EPS è utilizzato per caschi da moto e barriere antiurto.
L’EPS viene scelto non solo per le sue proprietà isolanti ma anche per la sua leggerezza, essendo composto da aria per il 95-98%. Questa caratteristica lo rende ideale per applicazioni che richiedono materiali leggeri ma robusti (figura 5). In edilizia, l’EPS è comunemente prodotto sotto forma di pannelli rigidi, la cui densità varia in base all’applicazione desiderata, e può essere personalizzato con additivi o strati esterni sottili su uno o entrambi i lati, per migliorare varie proprietà. Un esempio è la laminazione con lastre di cemento per formare pannelli isolanti strutturati.
Il polistirene espanso estruso (XPS), invece, si compone di celle chiuse e offre una superficie più ruvida, una maggiore rigidità e una ridotta conducibilità termica rispetto all’EPS. Utilizzato anche nell’hobbistica e nella realizzazione di modelli architettonici, l’XPS è un materiale molto apprezzato per la sua omogeneità, che lo rende un ottimo sostituto del cartone ondulato. Sia l’EPS che l’XPS trovano quindi un ruolo significativo nella costruzione moderna e nell’industria del packaging, grazie alle loro proprietà isolanti, alla leggerezza e alla versatilità d’applicazione.
Giovanni Lucchetta, Università di Padova