La domanda di siringhe usa-e-getta, che in tempi “normali” conta miliardi di unità, ha raggiunto valori ancora più importanti dall’inizio delle campagne vaccinali anti Covid, rendendo indispensabile un aumento della capacità produttiva in tutto il mondo. La situazione, ovviamente, ha trainato la richiesta di stampi a iniezione – da consegnare in tempi record – in grado di produrre in maniera rapida ed efficiente dispositivi più leggeri. Tra le soluzioni proposte per l’applicazione, quella del costruttore di stampi tedesco Werkzeugbau Ruhla (Seebach) si delinea come una delle più interessanti. Si tratta di due stampi a 64 cavità, a canale caldo integrale, destinate una alla produzione del corpo e l’altra allo stantuffo di una siringa in polipropilene da 0,5 millilitri costituita da tre componenti.
Uno stampo modulare e standardizzato
La specializzazione negli stampi ad altra precisione per componenti medicali ha portato Ruhla ad affidarsi costantemente a un concetto modulare dello stampo, con elevata standardizzazione nella costruzione, sviluppata e perfezionata anche grazie alla lunga collaborazione con il produttore di canali caldi Ewikon. Una delle priorità dell’azienda è costruire attrezzature compatte e dal peso ottimizzato, con raffreddamento efficace e manutenzione semplificata, in modo da poterli installare su presse a iniezione con forza di chiusura ridotta. Obiettivo perseguito anche nello stampo in questione.
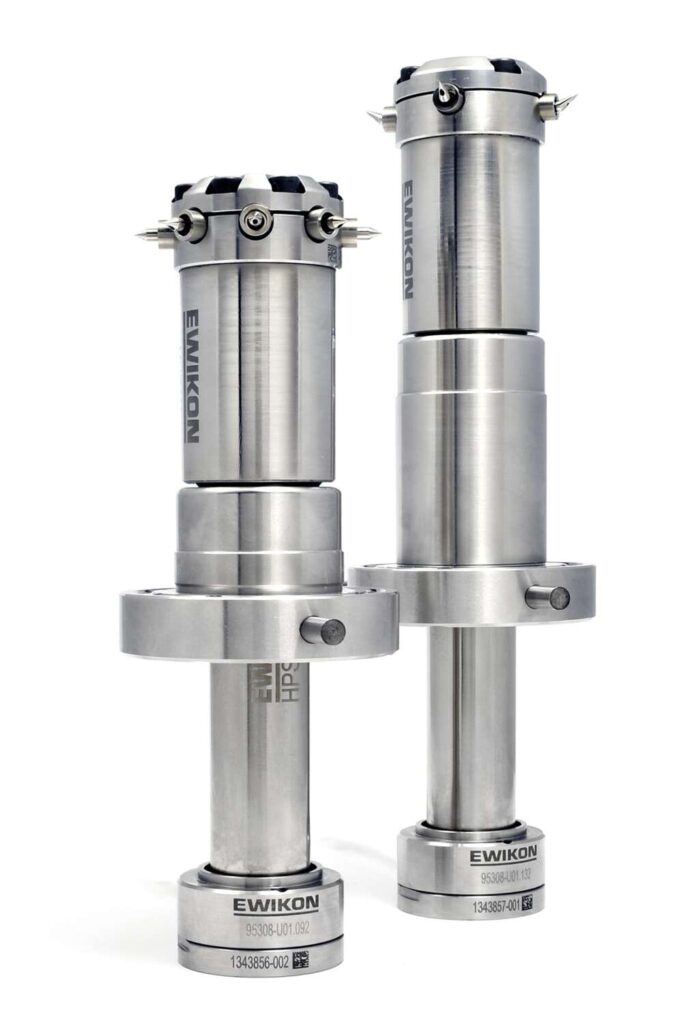
Dal punto di vista del canale caldo, l’aspetto primario è l’iniezione laterale diretta, realizzata con due versioni degli ugelli ad alte prestazioni HPS III-MH di Ewikon pensati per garantire gli elevati standard di qualità del punto di iniezione richiesti nel settore medicale. Per la produzione del corpo della siringa è stato scelto l’ugello in versione radiale. Appositamente sviluppato per l’applicazione, monta inserti punta estesi ed è caratterizzato da un corpo di ingombro particolarmente ridotto e lunghezza facilmente adattabile a componenti stampati di diversa lunghezza. «Utilizzando la versione radiale, la distanza tra il corpo dell’ugello e le parti stampate è sufficiente per permettere l’installazione degli inserti con un raffreddamento circolare intorno alla cavità» spiega Udo Koellner, direttore generale di Ruhla. «Questa soluzione viene applicata su tutti i nostri stampi per siringhe, in combinazione con maschi interni anch’essi raffreddati, in modo da garantire tempi ciclo molto ridotti. Inoltre, il particolare design degli inserti ne assicura una rapida sostituzione».
Per la produzione degli stantuffi della siringa, disposti in linea nello stampo, è stata invece preferita la versione lineare dell’ugello, dalla sezione rettangolare.
Manutenzione più semplice
Ruhla progetta gli stampi ponendo grande attenzione alla manutenzione, che deve essere la più semplice possibile per snellire le operazioni di routine anche in paesi lontani. Un contributo particolarmente significativo a questo approccio è legato all’adozione delle punte dei sistemi Ewikon, che possono essere facilmente sostituite direttamente in macchina, senza la necessità di smontare lo stampo. «Un altro aspetto importante è la progettazione modulare dello stampo, che integra gli ugelli e il loro cablaggio in una piastra separata, che può essere smontata semplicemente in caso di sostituzione di uno degli ugelli. Questa soluzione rende l’ugello facilmente accessibile e rimpiazzabile in modo rapido» puntualizza Udo Koellner. «Ewikon ci supporta anche nello studio delle scatole di connessione con speciali connettori».
Obiettivo alleggerimento
I componenti della siringa sono stati progettati in stretta collaborazione tra Ruhla e il cliente finale, puntando al massimo contenimento di consumo di materia prima. In particolare, il corpo è stato ottimizzato riducendo lo spessore della parete e la lunghezza, mentre lo stantuffo è stato concepito con un design a tre costole. Il concetto della siringa in tre pezzi, infine, ha permesso di evitare stampi a carrelli, semplificando ulteriormente lo stampo. «Portando il peso del corpo a soli 1,1 grammi e dello stantuffo a 0,35 grammi siamo riusciti a risparmiare il 25% di polipropilene rispetto alle siringhe per vaccinazione della stessa capacità» dichiara soddisfatta Lena Lueneburger, amministratore delegato di Ruhla. «E questo la colloca tra le più leggere oggi disponibili sul mercato». Ewikon, invece, ha contribuito al progetto supportando la fase dedicata all’analisi di riempimento e con approfonditi calcoli di caduta di pressione e sforzo di taglio nel sistema, così da garantire la produzione di massa in tempi ciclo ridotti al minimo.
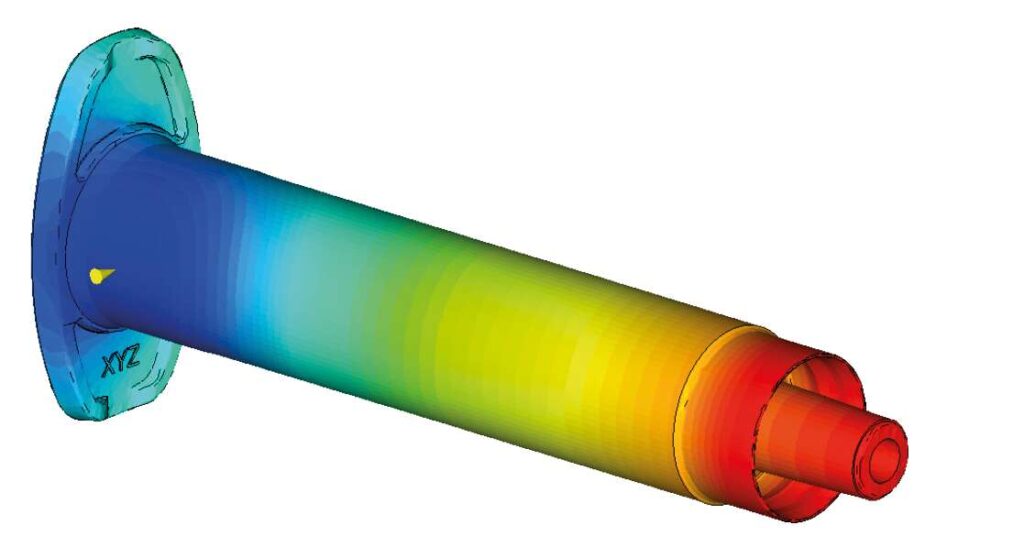
Il rigido protocollo previsto dall’Organizzazione Mondiale della Sanità (WHO) per la somministrazione del vaccino contro il virus Sars-Cov-2 prevede l’impossibilità di riutilizzo delle siringhe. La soluzione sviluppata dal costruttore di stampi tedesco per soddisfare questo requisito prevede l’integrazione di due sottosquadri circolari nella parete del corpo della siringa per formare due posizioni di blocco definite per lo stantuffo. Arretrando, lo stantuffo si arresta una volta raggiunto il volume di 0,5 millilitri, mentre dopo aver somministrato la dose di vaccino raggiunge la posizione frontale di blocco. Terminata l’iniezione, nel caso si tentasse di riempire nuovamente la siringa, lo stantuffo si separerebbe in due punti predefiniti rendendo la siringa inutilizzabile.
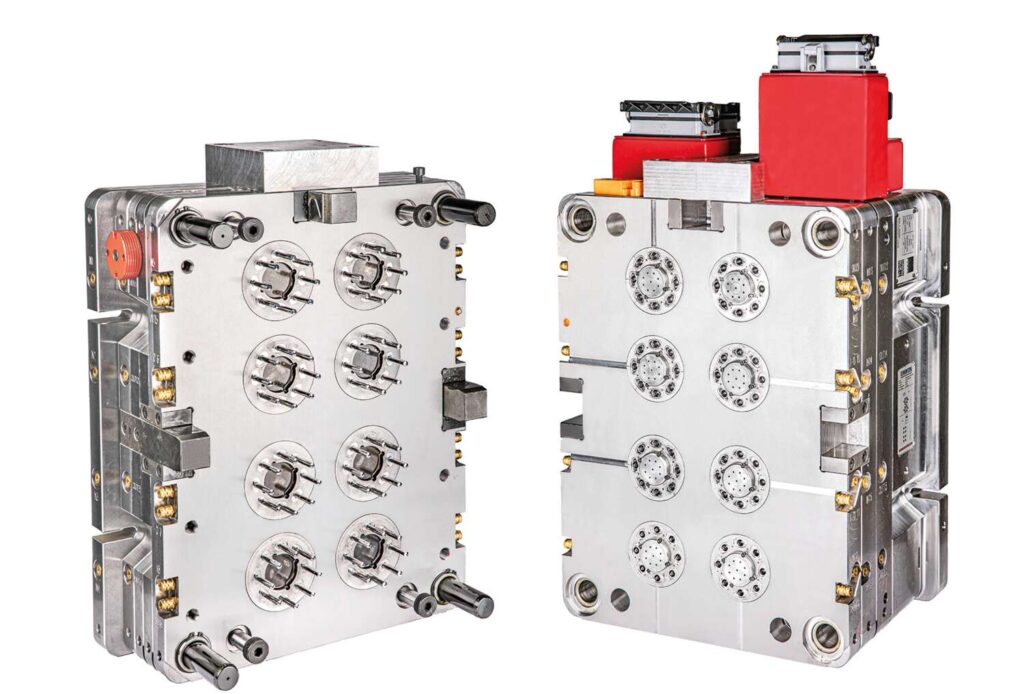
Elevato numero di impronte e dimensioni contenute
Nonostante l’elevato numero di impronte, utilizzando solo otto ugelli è stato possibile realizzare un’attrezzatura molto compatta. Lo stampo per il corpo della siringa (base 446×596 millimetri) monta gli ugelli in due colonne, da quattro ugelli ciascuna, con le impronte disposte circolarmente attorno a essi. L’iniezione è realizzata con puntali termoconduttivi angolati a 60 gradi, disposti sulla parete del cilindro, vicino alla base del maschio, in modo da minimizzare il suo spostamento e le conseguenti anomalie di stampaggio. Lo stampo per il pistone (base 546×596 millimetri) utilizza invece ugelli lineari, con quattro cavità disposte su ogni lato del corpo rettangolare, con iniezione sul pulsante. I sistemi a canale caldo per entrambi gli stampi sono stati forniti da Ewikon come parte calda completa di cablaggio e connessioni, e integrati da Ruhla con la piastra matrice e lato estrazione stampo. Grazie all’elevato livello di standardizzazione e alle moderne tecnologie di produzione (inclusa una cella integrata per gli elettrodi), il costruttore di stampi tedesco ha completato l’intero progetto – dalla ricezione dell’ordine al progetto, ai test di pre-produzione nel centro tecnico interno fino alla consegna – in sole 16 settimane. Obiettivo che – insieme a un tempo ciclo di 10 secondi per il corpo siringa – è riuscito a soddisfare le aspettative del committente. Alla consegna dello stampo, è stato fornito un pacchetto di assistenza che non include esclusivamente i ricambi più comuni e un dettagliato manuale per l’operatore, ma anche filmati esplicativi sulle più importanti operazioni di manutenzione.
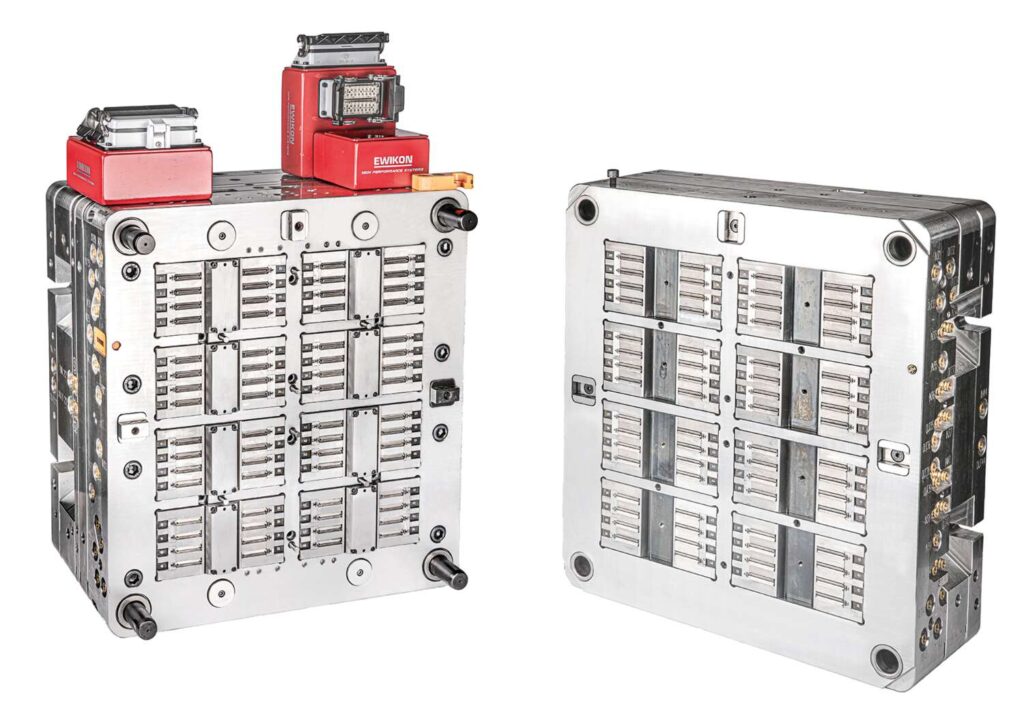
I vantaggi della modularità
Il concetto alla base del progetto, secondo Ruhla, si è dimostrato davvero convincente, tanto che un’azienda asiatica ha commissionato un set di stampi analogo per siringhe della stessa taglia e un altro per dispositivi da 0,3 millilitri (la capacità più comune nelle dosi di vaccino anti Covid). «Passare facilmente da una versione all’altra è uno dei vantaggi più evidenti legati alla modularità della nostra soluzione, perché anche la versione più piccola può essere realizzata semplicemente muovendo uno dei sottosquadri nel corpo della siringa» conclude Lena Lueneburger.