La fusione dei granuli è un processo imprescindibile nella trasformazione delle materie plastiche in manufatto, tuttavia, durante il loro riscaldamento possono liberarsi componenti volatili o sottoprodotti di decomposizione potenzialmente tossici per gli addetti alla produzione. L’identificazione di tali sostanze è piuttosto complessa, perché, nonostante siano disponibili diversi studi sulla caratterizzazione delle specie chimiche prodotte in fase di riscaldamento delle materie plastiche, la grande quantità di polimeri e compound disponibili sul mercato impedisce lo sviluppo di un database adeguato, almeno per uno screening preliminare del livello di rischio per gli operatori. L’analisi delle informazioni disponibili, infatti, ha evidenziato una grande dispersione dei dati, giustificata, oltre che dall’ampiezza dell’offerta, anche dalla diversità degli impianti e delle condizioni di trasformazione, delle attrezzature di laboratorio utilizzate per l’analisi delle emissioni e degli impianti di aerazione utilizzati nell’ambiente di lavoro oggetto degli studi.
Questo significa che non è possibile identificare a priori i potenziali composti tossici nelle emissioni generate durante la lavorazione dei polimeri, che in senso più generale significa che non è possibile trarre conclusioni generalizzate per lo screening delle situazioni più pericolose. Per quantificare il livello di rischio è quindi necessario effettuare un’analisi ambientale che comprenda la ricerca di tutti gli inquinanti. Tale procedura, sebbene di indubbia validità ed efficacia, si scontra con problemi di risorse umane ed economiche – si tenga infatti presente che le aziende di trasformazione sono spesso PMI – e con il fatto che può essere effettuata solo dopo l’avvio della produzione, quindi quando gli operatori sono già stati esposti alle sostanze tossiche.
Sulla base di queste premesse, un gruppo di ricercatori del Dipartimento di Chimica, Materiali e Ingegneria Chimica del Politecnico di Milano, guidati da Giuseppe Nano e Renato Rota, ha sviluppato una procedura di screening [1] semplice ed economica, che rileva, non solo il tipo ma anche la quantità delle sostanze immesse nell’ambiente in condizioni di processo simili a quelle reali. La validità della procedura è stata quindi verificata in due aziende attive nella produzione di cavi e tubi in PVC.
La procedura di screening
Il metodo di screening sviluppato dai ricercatori del Politecnico di Milano si basa sulla tecnologia EGA (Evolved Gas Analysis), che consiste nell’accoppiare un’analisi TGA (Thermo Gravimetric Analysis), in cui una piccolissima quantità del campione viene riscaldato in modo controllato misurandone la perdita di peso (un fattore associato allo sviluppo di sostanze volatili), a una strumentazione analitica (spettrofotometro infrarosso a trasformata di Fourier o gascromatografo con spettrometro di massa) adeguata a misurare la concentrazione delle specie gassose rilasciate durante il riscaldamento.
La tecnica si avvale di un’apparecchiatura da laboratorio (figura 1) in grado di controllare in maniera precisa sia la temperatura cui vengono sottoposti i provini, sia il campionamento degli inquinanti, che vengono trasportati da un gas ai punti di prelievo del sistema sperimentale. Nel caso in esame, sono stati utilizzati granuli in PVC, mentre nei due punti di campionamento è stato inserito, nell’uno un separatore a carboni attivi per la raccolta di VOC e nell’altro un separatore per le aldeidi.
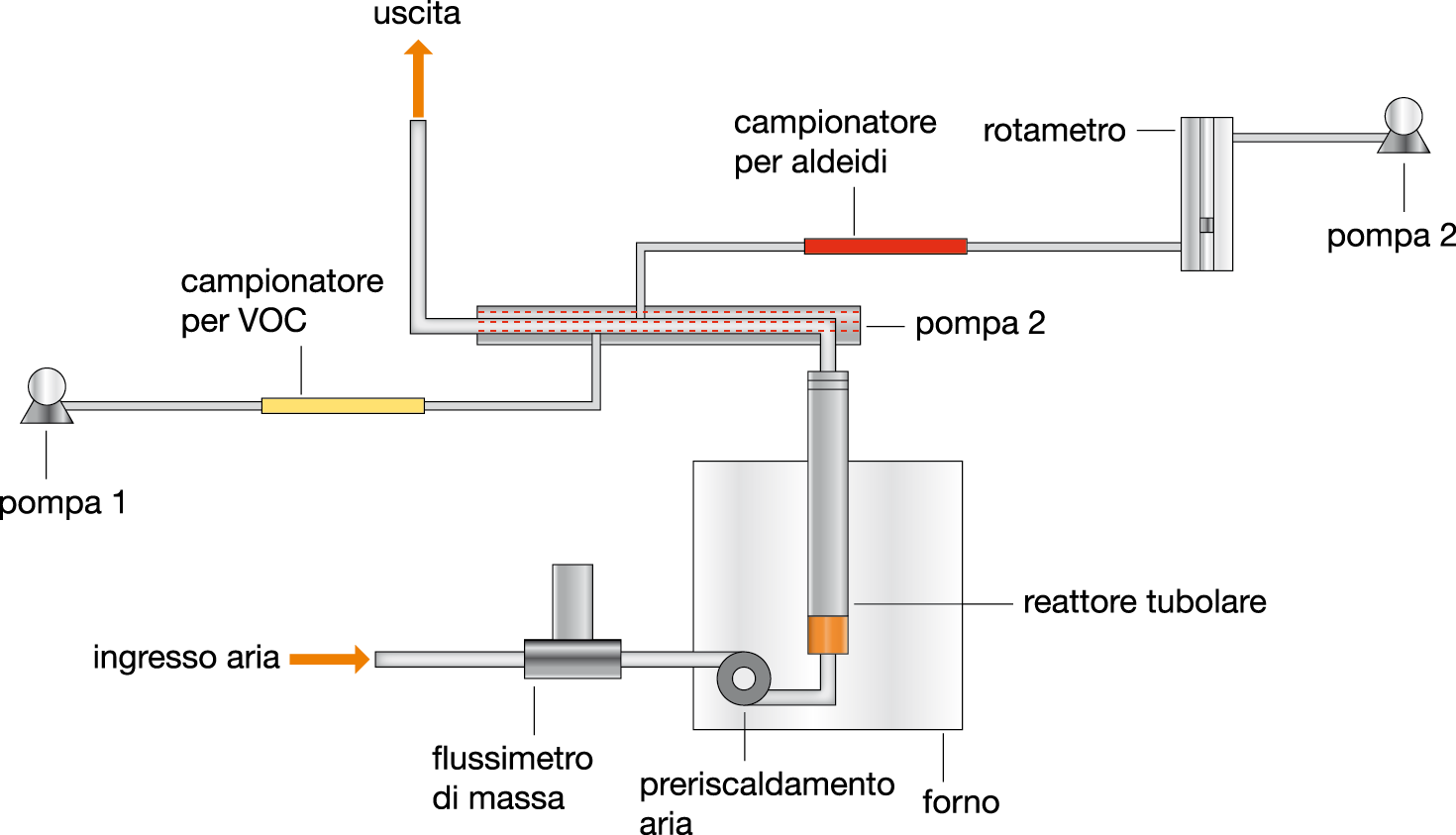
La procedura del test è molto semplice. Dopo aver portato il reattore alla temperatura desiderata, viene introdotto all’interno di esso il campione di plastica e i punti di campionamento vengono rapidamente collegati all’uscita del reattore. La durata della prova viene protratta fino a permettere il completo campionamento sulle cartucce di tutti gli inquinanti (per esempio 30 minuti). Le cartucce vengono quindi rimosse e analizzate, e i risultati ottenuti espressi in termini di fattore di emissione delle specie “i” come EFi (ovvero la quantità in microgrammi di un inquinante “i” emesso in un minuto da un grammo di plastica).
L’analisi dei dati
I risultati del test possono essere valutati sia qualitativamente sia quantitativamente. Dal punto di vista qualitativo, i dati rivelano gli inquinanti immessi nell’ambiente di lavoro, permettendo così di effettuare facilmente lo screening del processo in funzione dei sottoprodotti pericolosi previsti. Dal punto di vista quantitativo, invece, i fattori di emissione rivelano quali inquinanti vengono immessi in maggiore quantità nell’ambiente di lavoro (cioè, quelli con EFi più elevato) e permettono di stimare, anche se in modo approssimato, il rapporto tra le concentrazioni (C) di due diversi inquinanti sotto forma di rapporto fra i relativi fattori di emissione:
eq. 1) Ci/Cj = EFi/EFj
Ciò significa che, una volta che la concentrazione di una specie chiave viene misurata nell’ambiente di lavoro, possono essere dedotti i valori – almeno come ordine di grandezza – delle concentrazioni di altre specie chimiche, dal valore rilevato per la specie chiave e dal rapporto tra i fattori di emissione, applicando l’equazione (1).
La specie chiave può essere definita attraverso un indicatore chiave di prestazione (KPI o Key Performance Indicator) adeguato per il processo in esame: per esempio, il valore di KPI può essere ragionevolmente calcolato come rapporto tra il fattore di emissione e un valore soglia detto TLV:
eq. 2) KPIk = EFk/TLVk
Di conseguenza, la specie chiave può essere definita come quella con il KPI più elevato. I risultati ottenuti dallo screening possono essere interpretati in termini sia assoluti sia relativi. Nel primo caso, i risultati si interpretano come discusso in precedenza, nel secondo i valori vengono confrontati con quelli ottenuti dall’analisi di un altro processo o materiale già utilizzato nello stesso settore industriale (ovvero, con le medesime apparecchiature e dispositivi di ventilazione), il cui rischio per gli operatori si è dimostrato trascurabile. Se i fattori di emissione determinati in laboratorio sono più elevati rispetto a quelli relativi a un processo o materiale già testato si può prevedere un aumento del rischio per l’operatore (si noti che mediante l’equazione 1 è possibile dedurre almeno l’ordine di grandezza di questo aumento del rischio). Ciò permette di effettuare facilmente lo screening dei cambi di processo o di materiale per i quali si prevede un aumento del rischio per l’operatore.
La procedura sviluppata dai ricercatori del Politecnico può essere utilizzata non solo per la valutazione del rischio per il personale nella routine quotidiana, ma anche del rischio legato ad alcune situazioni indesiderate, come il riscaldamento eccessivo della plastica a causa di un’eventuale perdita di controllo del dispositivo di riscaldamento. In questo caso, la procedura può essere facilmente ripetuta impostando la temperatura del reattore sul valore accidentale stimato.
I casi di studio
La validità della procedura è stata verificata attraverso lo studio di due casi reali, che hanno preso in esame l’estrusione di cavi e di tubi corrugati condotti da due diverse aziende.
Il primo (nel seguito definito azienda 1) si riferisce al rivestimento di cavi elettrici mediante estrusione con PVC additivato con ritardanti alla fiamma. Il processo prevede l’impiego di un estrusore monovite, equipaggiato con una cappa di aspirazione posizionata vicino alla testa di estrusione sempre attiva, a eccezione delle fasi di allineamento della vite e di cambio materiale. Durante queste operazioni manuali, la cappa aspirante viene spostata di circa 30 centimetri dalla testa di estrusione. La temperatura di esercizio è di 150-170 °C.
Il secondo processo (nel seguito definito azienda 2) si riferisce alla produzione di tubi corrugati in PVC caricato con calcio e zinco. Anche in questo caso, viene utilizzato un estrusore monovite raffreddato ad acqua; la temperatura di esercizio è di 180-200 °C. L’impianto è provvisto di una cappa di aspirazione posizionata vicino alla testa di estrusione, mantenuta sempre attiva, tranne nelle fasi di allineamento della vite e del cambio materiale. Durante le operazioni manuali, la cappa aspirante viene spostata di circa 30 centimetri dalla testa di estrusione.
Una procedura semplice ed efficace
I due diversi gradi di PVC utilizzati dalle due aziende sono stati testati in laboratorio attraverso la procedura di screening precedentemente illustrata. Gli esperimenti sono stati effettuati a 165 °C, valore che corrisponde approssimativamente alla temperatura media dei due processi di estrusione considerati. Per ciascun materiale sono stati misurati i fattori di emissione di alcuni inquinanti. Negli impianti di lavorazione, sono state misurate le concentrazioni in aria di diverse sostanze inquinanti utilizzando i metodi standard EN (per esempio EN 689:1995, EN 1232:1997, EN 482:2006). I risultati delle diverse serie di prove sono rappresentati nelle figure 2 e 3. I valori sono stati normalizzati rispetto alla misura più elevata per ciascun grado di PVC.
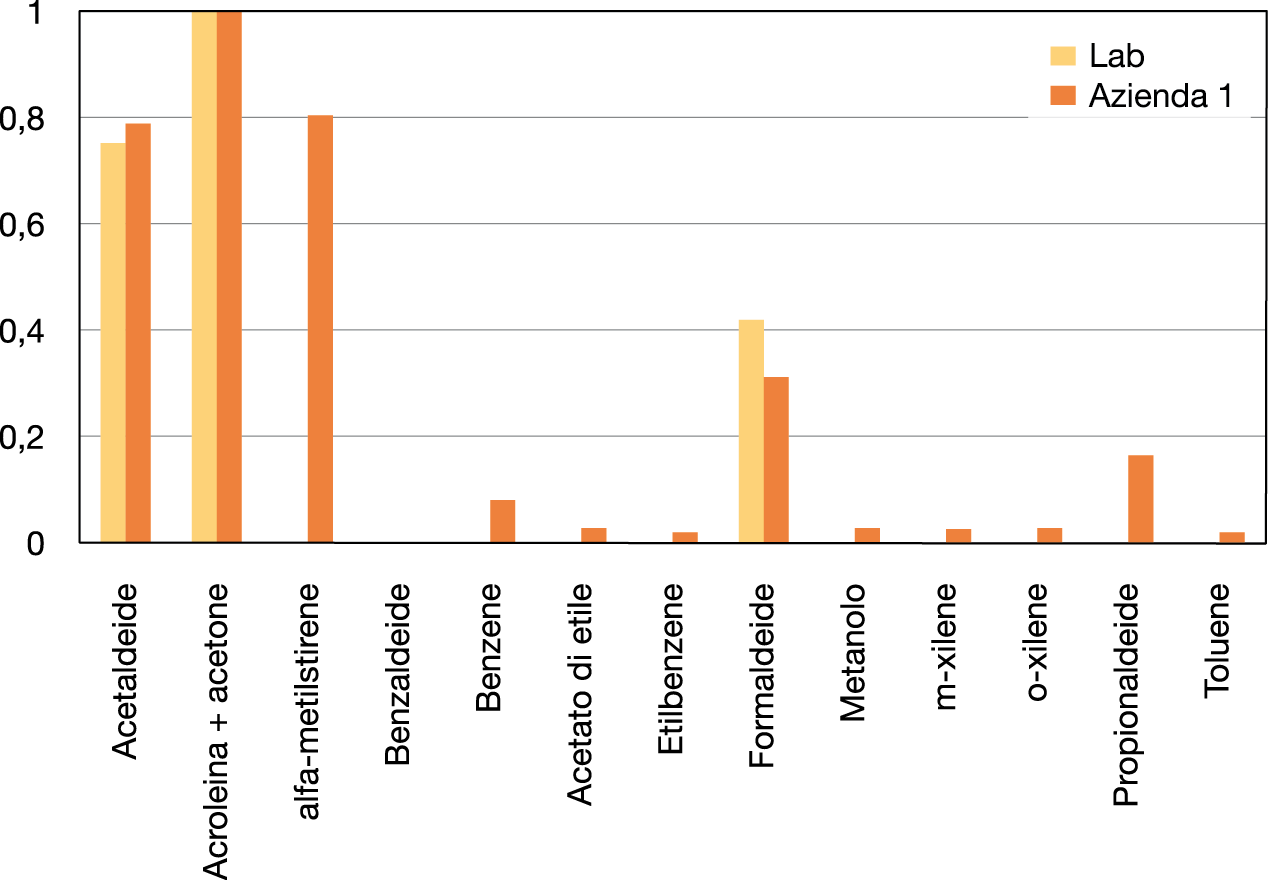
Il fattore di emissione totale dei VOC riferito al PVC dell’azienda 1 è circa quattro volte più elevato rispetto quello dell’azienda 2. Ciò dimostra, come evidenziato anche dalle figure 2 e 3, che il polimero può generare emissioni di inquinanti tossici molto diverse in funzione del contenuto di additivi. Tali risultati coincidono con quanto emerso nell’analisi della letteratura e conferma inoltre che non è possibile definire fattori di emissione validi in termini generali, mentre sono invece necessarie misure mirate al processo e al materiale specifico.
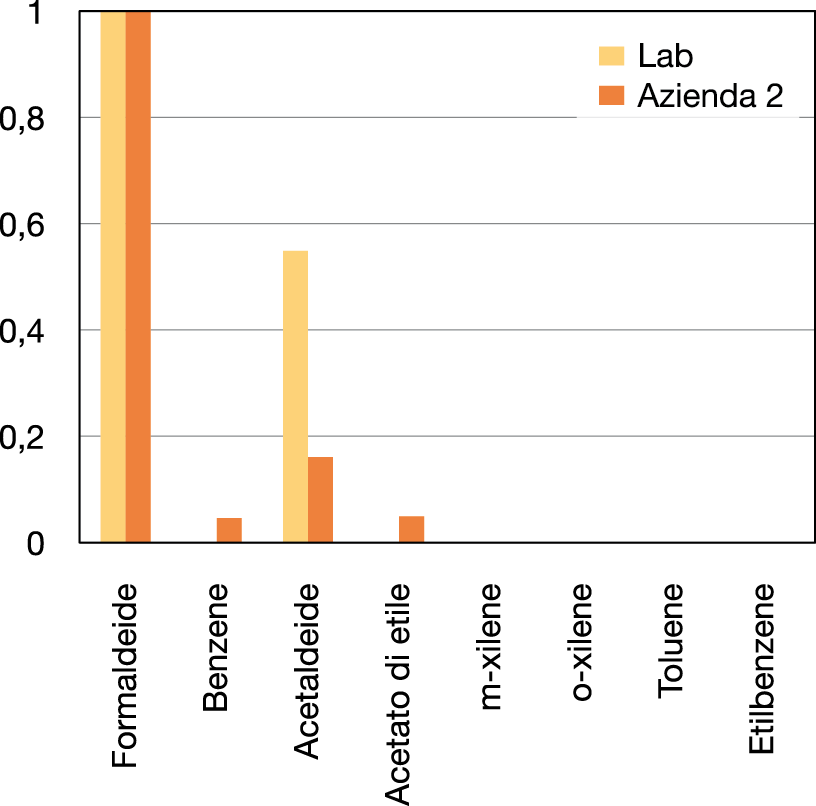
Le figure 2 e 3, inoltre, evidenziano che le tendenze generali dei fattori di emissione e dei valori di concentrazione misurati nell’ambiente di lavoro sono abbastanza simili, confermando in tal modo la validità dell’equazione 1, e quindi la validità della procedura proposta.
Nel corso dei test di laboratorio sono state identificate specie chimiche non rilevate dai campionamenti nell’ambiente di lavoro. Tale discrepanza si spiega considerando che, in laboratorio, le condizioni operative possono essere controllate e mantenute uniformi più facilmente, e che i campionamenti non vengono compromessi da un’indesiderata diluizione in aria delle sostanze volatili emesse.
In conclusione, i risultati ottenuti dalla sperimentazione supportano l’approccio conservativo alla base della procedura di screening sviluppata, oltre a evidenziare una potenziale immissione di inquinanti anche molto pericolosi (per esempio formaldeide) nell’ambiente di lavoro, rendendo obbligatoria la presenza di un sistema di ventilazione idoneo a ridurre l’esposizione degli operatori (e quindi il rischio nell’ambiente di lavoro) entro un livello accettabile.