Due giornate intense per Arburg Italia, che il 18 e il 19 maggio ha festeggiato presso la propria sede di Peschiera Borromeo (Milano) i cent’anni della casa madre di Lossburg insieme a circa 200 clienti e operatori dello stampaggio a iniezione, intervenuti per un’open house incentrata soprattutto su temi tecnici.
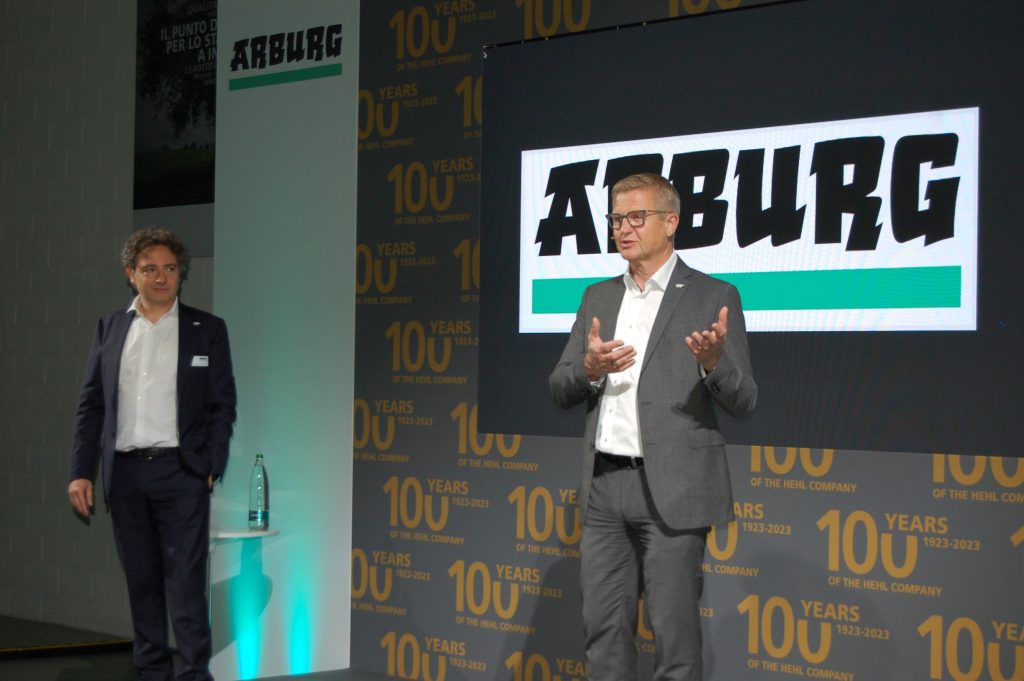
Entrambe le mattine di giovedì e venerdì sono infatti iniziate con gli interventi di Raffaele Abbruzzetti (AD di Arburg Italia), Gerhard Böhm (AD di Arburg) e Luca Fasoli (sales operation manager), volti a presentare la nuova “macchina dell’anniversario” Allrounder 470H, nelle due varianti Comfort e Premium già disponibili sul mercato, a cui seguirà la variante “Ultimate”.
Ridotto consumo energetico, elevata produttività e facilità d’uso
La Allrounder 470H 1000 290 Comfort in esposizione montava uno stampo di Gammaplast e produceva un porta biglietti da visita in ABS a base biologica di Versalis, proveniente da riciclo chimico. Come hanno ben spiegato Raffaele Abbruzzetti e Gerhard Böhm, questa “macchina dell’anniversario” consente di risparmiare energia e di preservare le risorse, produce in modo efficiente ed è facile da usare e affidabile nello stesso tempo.
La perfetta combinazione di gruppo di chiusura elettrico e unità d’iniezione idraulica riduce notevolmente i costi d’acquisto e d’esercizio, nonché l’impronta di carbonio. Tra i fattori che hanno contribuito a ottimizzare i consumi energetici e a ridurre i tempi di ciclovi sono la nuova concezione di gestione dell’olio, la suddivisione della portata del flusso per i movimenti simultanei degli assi secondari idraulici e l’uso esteso del sistema servoidraulico Arburg.
Se confrontata con una macchina idraulica di caratteristiche simili, l’impronta energetica della Allrounder 470 H è migliorata fino al 50% e, a seconda dell’applicazione, è possibile risparmiare fino a 12000 kg di CO2 ogni anno. Una riduzione fino al 33% del tempo di ciclo a vuotosi traduce infine in un’efficienza produttiva significativamente maggiore.
La nuova Allrounder 470 H è quindi particolarmente interessante per quegli stampatori che sono alla ricerca di un’alternativa che consumi meno energia rispetto alle macchine idrauliche, ma che vogliano comunque beneficiare dei loro comprovati vantaggi.
Sistema servoidraulico e funzioni particolari del controllo Gestica
Il sistema servoidraulico Arburg (ASH), già collaudato nelle Allrounder idrauliche ed elettriche, è stato integrato anche nei modelli Allrounder 470 H Comfort e Premium. Grazie all’ASH, il servomotore a velocità controllata e raffreddato ad acqua adatta continuamente il sistema d’azionamento al fabbisogno di potenza effettivo. Ciò consente di risparmiare fino al 50% d’energia, soprattutto nei processi con lunghi tempi di raffreddamento. Inoltre, anche il livello di rumorosità della macchina viene notevolmente ridotto.
Luca Fasoli ha inoltre spiegato che il sistema di controllo Gestica dispone di diverse funzioni utili per lo stampatore. La funzione “aXw Control FillAssist”, per esempio, consente la simulazione del riempimento e, se supportata dall’intelligenza artificiale di Cadmould, può “apprendere” quali effetti hanno le modifiche dei parametri di processo. La funzione “aXw Control PressurePilot” ottimizza la regolazione della pressione per evitare il riempimento insufficiente, o la formazione di bave. La funzione “aXw Control MeltAssist” permette di calcolare automaticamente l’utilizzo della capacità di plastificazione e i tempi di permanenza. Tutte queste “caratteristiche digitali”, insieme, garantiscono un processo altamente affidabile e un modo di lavorare comodo e veloce.
Isola produttiva completamente automatizzata e stampante 3D
All’interno dell’open house, una pressa verticale Allrounder 375 V, con stampo a 1+1 cavità, costituiva il cuore di una compatta cella di produzione dedicata al sovrastampaggio d’inserti con PA66/6 riciclata, ma rinforzata al 50% con fibre di vetro. In un tempo di ciclo di 45 secondi, la cella produceva particolari leve per la facile rimozione dei copertoni dai cerchioni delle biciclette.
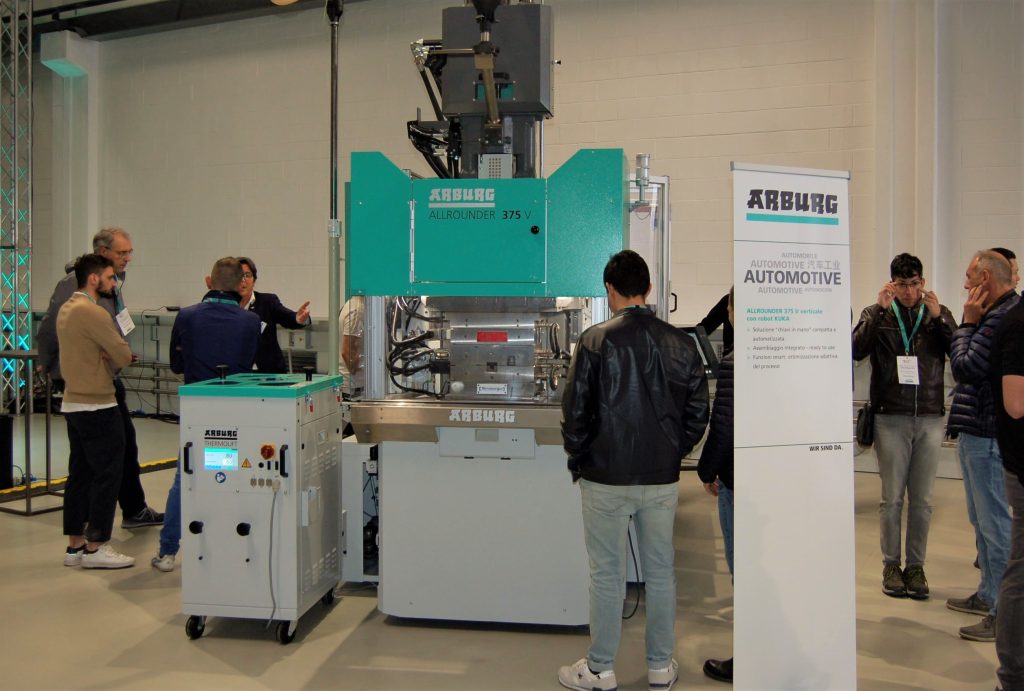
Un robot a sei assi di Kuka era montato in una posizione “sospesa” salvaspazio e integrato nel sistema di controllo Gestica. Tale robot alimentava le parti stampate a una stazione laser, dove ricevevano un codice DM per la tracciabilità, completava un manuale operativo e assemblava le due parti della leva per copertoni, in modo che questa fosse pronta all’uso non appena uscita dall’isola produttiva. L’impianto era completamente automatizzato e la pressa era dotata delle più moderne soluzioni digitali per l’ottimizzazione adattiva dei processi in linea; il tutto per una produzione davvero “smart”, efficiente e tracciabile.
Nel corner dedicato alla produzione additiva è stata esposta in funzione anche una stampante 3D TIQ5 di innovatiQ (brand di Arburg), a tecnologia FFF (Fused Filament Fabrication).
Gli interventi degli esperti
Le presentazioni del 18 maggio riguardavano le opportunità attualmente in essere affinché le imprese dello stampaggio plastico possano beneficiare di incentivi finanziari nazionali e locali (a cura di Simone Blanzieri, area manager della società Vendor) e i nuovi trend nella gestione e nell’attrazione del personale: relazione dal titolo “Talent Challenge” di Claudio Fasola, senior partner di Modulo Group.
Gli interventi del 19 maggio spaziavano invece dagli esempi di IoT e Digital Twin applicati allo stampaggio a iniezione, illustrati da Giovanni Lucchetta (professore in Sistemi di produzione e tecnologie di lavorazione dei materiali polimerici presso il Dipartimento d’Ingegneria Industriale dell’Università di Padova), fino alle tecniche TPM (Total Productive Maintenance) per recuperare capacità produttiva e ridurre gli sprechi nei sistemi produttivi capital intensive, descritte da Fabio Salomone, direttore generale di Staufen Italia.
Prima di concludersi con un simpatico aperitivo con lounge music, entrambe le giornate prevedevano infine la possibilità di visitare l’Area Service, dedicata al servizio d’assistenza tecnica e ai pezzi di ricambio, e di sperimentare il portale clienti arburgXworld.