di Giovanni Lucchetta, Università di Padova
Il mercato globale dello stampaggio a iniezione, stimato in 285,5 miliardi di dollari nel 2023, prevede una crescita annuale composta del 4,9% fino al 2030. Questo incremento è sostenuto dalla crescente domanda di componenti per le industrie automobilistica e biomedicale, dove sicurezza, precisione e qualità sono requisiti imprescindibili. La regione Asia-Pacifico, che ha rappresentato il 40,8% del fatturato globale nel 2023, vedrà una notevole crescita grazie all’espansione dell’industria automobilistica.
Le sfide future
In questo contesto, l’industria italiana dello stampaggio a iniezione dovrà affrontare sfide significative per mantenere o aumentare la propria competitività nei prossimi anni:
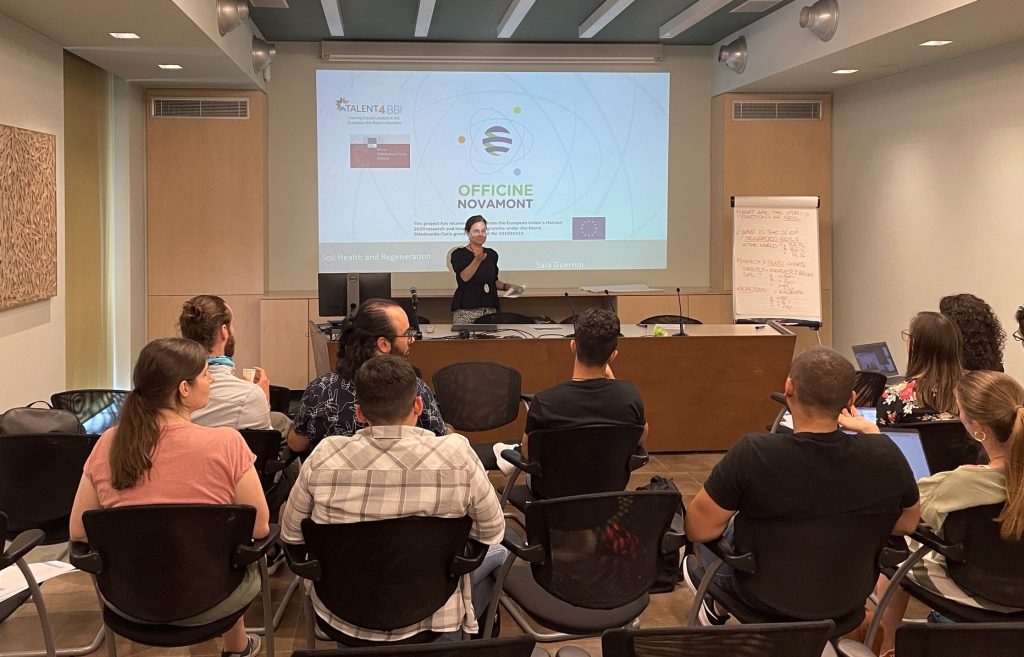
- Aumento dell’efficienza attraverso l’innovazione tecnologica. La sfida principale è rappresentata dall’aumento dell’efficienza per ridurre i costi operativi e diventare più competitivi nel mercato globale. L’introduzione di tecnologie avanzate, come l’automazione e l’intelligenza artificiale (IA), può contribuire a minimizzare gli sprechi e i consumi energetici, che sono particolarmente rilevanti data l’esposizione dell’Italia sul mercato energetico. Queste azioni non solo migliorano la competitività sul mercato globale, ma contribuiscono anche a migliorare la sostenibilità.
- Sostenibilità. L’adozione di materiali sostenibili come le plastiche riciclate (vedi foto d’apertura, ndr), i polimeri di origine non fossile, biodegradabili o compostabili, rappresenta una sfida significativa per l’industria dello stampaggio a iniezione. Questi materiali possono avere proprietà diverse dalle materie plastiche tradizionali, influenzando il processo di stampaggio e richiedendo l’adattamento delle macchine e delle tecnologie esistenti. Inoltre, per questi nuovi materiali è spesso necessaria una tracciabilità accurata dei lotti produttivi per identificare e gestire eventuali non conformità; il che richiede sistemi di gestione e controllo qualità avanzati per monitorare il processo produttivo lungo tutta la catena di fornitura.
- Formazione e competenze. In Italia, l’invecchiamento della popolazione e la riduzione della forza lavoro giovane influenzano notevolmente le strategie di formazione nel settore dello stampaggio a iniezione. La carenza di lavoratori qualificati e la riluttanza della forza lavoro giovane a lavorare in ciclo continuo, spesso necessario per il settore dello stampaggio a iniezione, spingono le aziende a investire maggiormente nella formazione continua dei dipendenti esistenti e nel trasferimento di conoscenze tra generazioni. Questo scenario rende fondamentale l’aggiornamento costante delle competenze tecniche per gestire nuove tecnologie e materiali, e per mantenere la competitività industriale in un mercato in rapida evoluzione.
- Riduzione dei lotti produttivi. La riduzione dei lotti produttivi, allineata ai principi della Lean Production, è essenziale per minimizzare i costi di magazzino. Questo approccio richiede una maggiore flessibilità produttiva e l’abilità di cambiare rapidamente lo stampo per adattarsi alle diverse produzioni senza compromettere efficienza e qualità. Gli operatori esperti giocano un ruolo cruciale in queste fasi, riducendo gli sprechi di materiale e garantendo un avvio di produzione più rapido ed efficiente. Questo enfatizza ulteriormente l’importanza della formazione continua e del trasferimento di competenze.
Le sfide che il settore dello stampaggio a iniezione deve affrontare possono essere efficacemente superate sfruttando i vantaggi offerti dalla digitalizzazione, che non solo consente di mantenere la competitività, ma apre anche nuove opportunità per migliorare l’efficienza, la sostenibilità e la flessibilità dei processi produttivi. L’adozione di tecnologie avanzate e di nuove metodologie di lavoro può permettere alle aziende di navigare con successo tra le complessità del mercato globale, garantendo al contempo efficienza e sostenibilità. In questo contesto, emergono sei aree chiave che saranno maggiormente interessate dalla rivoluzione digitale e che rappresenteranno il fulcro del cambiamento: queste aree non solo ottimizzeranno i processi esistenti, ma introdurranno anche innovazioni radicali che trasformeranno il modo in cui operiamo e gestiamo i processi produttivi.
Le sei aree interessate dalla rivoluzione digitale
Tre aree rappresentano la naturale evoluzione di risorse esistenti (presse, stampi e operatori), mentre le altre tre saranno basate su strumenti di intelligenza artificiale completamente nuovi per il settore (sistemi di visione, Digital Twin e Copilot):
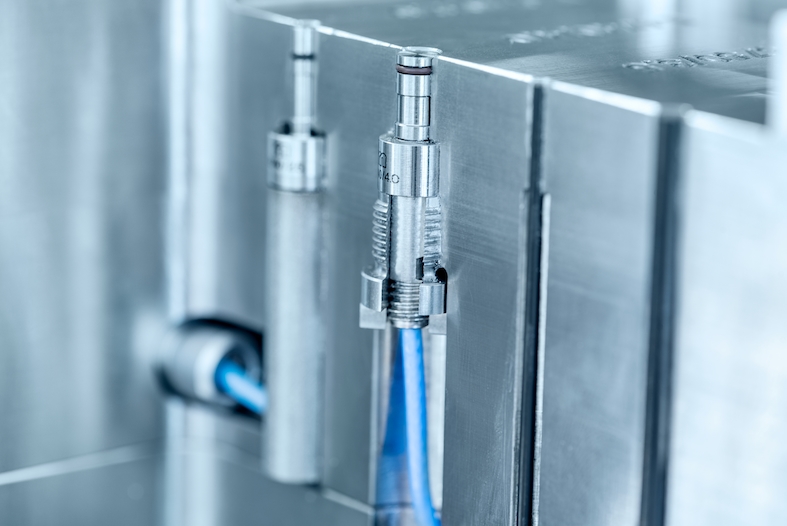
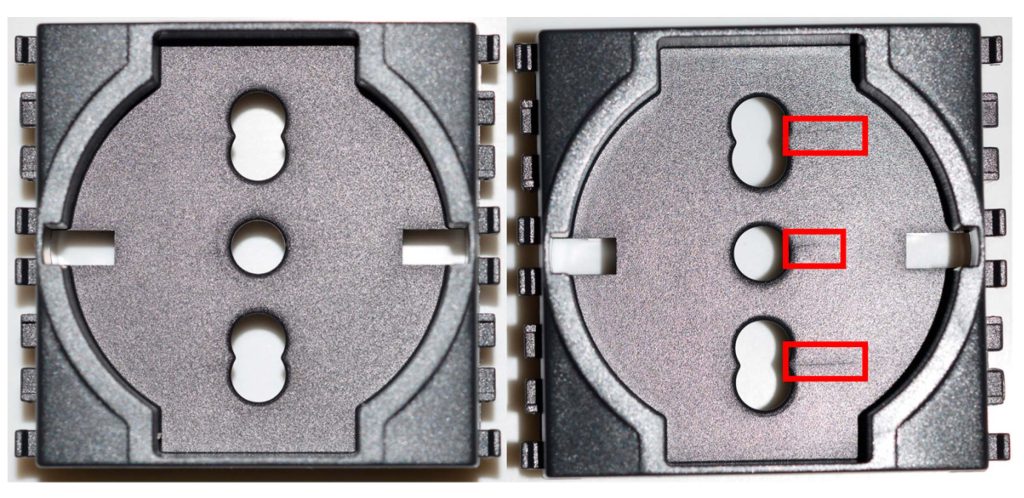
- Stampi sensorizzati. L’utilizzo di sensori avanzati per monitorare i dati di pressione, temperatura e portata in tempo reale facilitano la manutenzione predittiva e la diagnosi di eventuali problemi di stampaggio. Questo si traduce rispettivamente in un’estensione della durata degli stampi e nella minimizzazione dei fermi macchina.
- Sistemi di visione basati su IA. L’impiego di telecamere a bordo pressa e di algoritmi di intelligenza artificiale permettono di rilevare i principali difetti di stampaggio e monitorare la qualità dei pezzi stampati. Questo approccio è perfettamente complementare all’utilizzo di sensori integrati negli stampi, perché permette di rilevare difetti non correlabili con le grandezze fisiche monitorate dai sensori posizionati in cavità. L’efficacia delle telecamere è strettamente legata alla disponibilità di sistemi robotizzati per la manipolazione dei pezzi stampati. Alcuni difetti di stampaggio (ad es.: linee di giunzione e risucchi) sono infatti riconoscibili soltanto se il componente viene orientato in una maniera specifica rispetto alla luce.
- Industrial Internet of Things (IIoT). L’impiego di dispositivi IoT a bordo pressa consente di raccogliere tutti i dati relativi alla pressa e ai suoi ausiliari a ogni ciclo di stampaggio e di associarli ai dati provenienti dagli stampi e dai sistemi di visione. In altre parole, un difetto rilevato dai sensori in stampo e/o dalle telecamere viene direttamente associato a una specifica combinazione di parametri di stampaggio.
- Digital Twin. Sfruttando l’integrazione e l’associazione dei dati al punto precedente, si possono addestrare diversi algoritmi di Machine Learning a riconoscere relazioni di causa-effetto tra i dati misurati dalle presse mediante i dispositivi IoT e quelli rilevati sui pezzi stampati attraverso i sensori negli stampi e i sistemi di visione. L’addestramento di tali algoritmi può essere svolto raccogliendo i dati nel corso dei setup degli stampi, quando questi sono condotti da operatori esperti. In questo modo gli interventi correttivi effettuati sulla pressa da operatori esperti, a seguito dell’osservazione di un difetto, possono essere “catturati” e codificati nell’algoritmo. L’algoritmo così “addestrato” rappresenta un gemello digitale del processo fisico, una replica virtuale che può essere utilizzata offline per simulare e analizzare il processo di stampaggio in condizioni diverse senza dover necessariamente stampare plastica e tenere occupata la pressa. Questo approccio digitale consente di aumentare significativamente l’efficienza complessiva del sistema (OEE) e di condurre un maggior numero di prove virtuali grazie all’elevata velocità di calcolo dell’algoritmo.
- Copilot. Nell’industria della plastica, l’intelligenza artificiale può essere applicata essenzialmente in due modi: il Machine Learning, usato per sviluppare Digital Twin predittivi e simulativi (descritti al punto precedente), e più recentemente i Large Language Model. Un Copilot basato su un Large Language Model può rivoluzionare la gestione della conoscenza in un reparto produttivo. Questo sistema IA apprende dalla documentazione aziendale (ad es. manuali delle macchine, istruzioni operative e guide di risoluzione problemi) e permette agli operatori di interagire in modo conversazionale per ricevere assistenza specifica. Mitiga il rischio tecnico legato alla perdita di conoscenza quando gli esperti vanno in pensione e assicura che l’expertise sia condiviso equamente tra turni o stabilimenti differenti, eliminando disparità informative. Addestrando un’IA con tutte le informazioni disponibili, ogni dipendente può avere un assistente intelligente che parla la sua lingua e fornisce informazioni tecniche, indipendentemente dal turno o dalla sede di lavoro. L’IA migliora continuamente attraverso il feedback degli esperti e può elaborare procedure complesse da video, rendendo le informazioni accessibili in diverse lingue e migliorando l’efficienza operativa.
- Gestione delle persone e della conoscenza. Nella visione di Industria 5.0, l’elemento umano deve essere centrale e valorizzato pienamente nella capacità di gestire queste nuove soluzioni tecnologiche. I Digital Twin e i Copilot costituiranno uno strumento potente per acquisire e codificare una conoscenza veramente condivisibile. Tuttavia, il loro addestramento dovrà essere seguito direttamente dagli operatori di stampaggio più esperti, le cui competenze dovranno essere estese all’uso dei sensori, delle telecamere, dei robot e delle applicazioni software dedicate all’addestramento degli algoritmi. Operatori meno esperti potranno beneficiare dei suggerimenti forniti dai Digital Twin e dai Copilot. Si prevede che la diffusione di questi ausilii possa contribuire significativamente alla condivisione della conoscenza e anche alla riduzione della disparità di genere. Investendo nella formazione continua e promuovendo una cultura della digitalizzazione, le aziende possono garantire che i loro dipendenti siano abili nell’utilizzare le nuove tecnologie. La collaborazione e il trasferimento di conoscenze all’interno dell’organizzazione migliorano le capacità di risoluzione dei problemi e stimolano il miglioramento continuo. Le competenze digitali sono essenziali per la prossima generazione di professionisti dello stampaggio a iniezione e possono contribuire a modernizzare l’immagine dell’intero settore, rendendolo più attraente per le nuove generazioni che stanno abbandonando progressivamente il comparto della meccanica tradizionale, perché percepita come scarsamente avanzata.
Il caso Vimar
Il progetto di ricerca avviato dalla società Vimar, denominato “TWIST”, rappresenta un esempio pionieristico di come l’intelligenza artificiale possa essere integrata nei processi di stampaggio a iniezione per affrontare le sfide del futuro e trarre vantaggio dalla rivoluzione digitale. In collaborazione con SMACT Competence Center, Università di Padova e Maxfone, Vimar sta implementando una serie di tecnologie avanzate che rispecchiano alcune delle sei aree chiave della trasformazione digitale delineate in precedenza.
- Sistemi di visione e Object Detection. Uno degli aspetti più innovativi del progetto TWIST è l’addestramento e l’implementazione in linea di algoritmi di Object Detection, sviluppati con il supporto del Dipartimento di Ingegneria Industriale dell’Università di Padova. Questi algoritmi, utilizzati in combinazione con telecamere comuni, permettono di identificare difetti nei pezzi stampati durante il processo di produzione. Tale sistema rappresenta un’applicazione diretta dei sistemi di visione basati su IA, una delle sei aree critiche della rivoluzione digitale. L’uso delle telecamere e di avanzati algoritmi di Object Detection per monitorare la qualità dei prodotti consente di rilevare difetti che non sarebbero altrimenti visibili con i soli sensori fisici posizionati nelle cavità degli stampi. Questa capacità di identificare rapidamente e oggettivamente eventuali imperfezioni (cioè indipendentemente dall’operatore e dalle condizioni ambientali) migliora significativamente la qualità del prodotto finale e riduce gli sprechi di materiale.
- Industrial Internet of Things (IIoT). Il progetto TWIST incorpora anche elementi dell’IIoT, utilizzando dispositivi IoT per raccogliere e analizzare in tempo reale i dati provenienti dalle presse, dagli stampi e dai sistemi di visione. Questa integrazione di dati multisorgente permette di monitorare ogni aspetto del processo produttivo, ottimizzando le operazioni e riducendo i tempi di fermo macchina. L’adozione di tali sistemi IIoT rende possibile un controllo più preciso e immediato dell’intero ciclo produttivo, facilitando interventi correttivi tempestivi e migliorando la tracciabilità e la qualità dei prodotti.
- Digital Twin. Un altro pilastro del progetto TWIST è lo sviluppo di un Digital Twin del processo di stampaggio. Questo gemello digitale permette di simulare e analizzare il processo produttivo in tempo reale, fornendo previsioni accurate degli esiti della produzione e semplificando le operazioni di avvio delle macchine. Il Digital Twin è alimentato dai dati raccolti attraverso i sistemi di visione e i dispositivi IoT sulle presse, rappresentando una replica virtuale che può essere utilizzata per ottimizzare il processo di stampaggio senza dover necessariamente interrompere la produzione. Questo sistema, basato sugli algoritmi di IA e sulle capacità di Object Detection, agisce come un vero e proprio copilota che guida gli operatori meno esperti durante le fasi di avvio del processo di stampaggio. L’assistente virtuale riduce significativamente il margine di errore umano, garantendo che le operazioni vengano eseguite secondo i più alti standard di precisione e qualità. Questo approccio non solo migliora l’efficienza, ma consente anche agli operatori meno esperti di beneficiare delle conoscenze codificate dagli esperti, avviando più rapidamente le presse e riducendo la dipendenza dall’esperienza individuale e aumentando la flessibilità operativa. Avviare più rapidamente le presse e, soprattutto, poterlo fare anche nei turni notturni, cioè in assenza di operatori esperti, è essenziale per migliorare significativamente l’efficienza di un reparto caratterizzato da frequentissimi cambi stampo.
Il caso Vimar dimostra chiaramente come l’adozione di tecnologie avanzate come l’IA, i sistemi di visione, il Digital Twin e l’IIoT possano rivoluzionare il settore dello stampaggio a iniezione. Grazie a queste innovazioni, Vimar non solo migliora l’efficienza e la qualità della produzione, ma crea anche un ambiente di lavoro più sicuro e stimolante per gli operatori, garantendo una maggiore sostenibilità e competitività nel mercato globale. Questo progetto non è solo un esempio di successo tecnologico, ma rappresenta anche un modello per altre aziende italiane che cercano di affrontare le sfide della trasformazione digitale.