Per migliorare l’efficienza produttiva l’industria dell’imballaggio deve puntare su processi veloci, consumi di energia e materie prime ottimizzati salvaguardando la stabilità degli imballi. A queste “vecchie” esigenze, l’attenzione crescente per l’ambiente ne ha aggiunte di nuove, come una migliore riciclabilità e la riduzione delle emissioni di anidride carbonica. Obiettivi – questi ultimi – condivisi anche da molte aziende del settore alimentare. È il caso di Ennstal Milch, un caseificio austriaco che si è rivolto a Greiner Packaging di Kremsmünster (Austria) per migliorare ulteriormente la sostenibilità dei suoi vasetti per yogurt greco a pareti sottili, realizzati in polipropilene monomateriale ed etichettati nello stampo.
I vantaggi dell’in mold labeling
«Dato l’elevato valore “green” del vasetto di partenza, il progetto ha posto diverse sfide che abbiamo affrontato rivedendo sia il design del manufatto, sia il processo per stamparlo a iniezione» spiega Andreas Ecker, tecnico applicativo di Greiner Packaging. «Il risultato ottenuto è ottimo: siamo riusciti a ridurre del 20% il consumo di materiale utilizzato e ad abbassare di 0,1 millimetri lo spessore delle pareti, portandolo a 0,3 millimetri sui lati e 0,35 millimetri alla base. L’alleggerimento non ha pregiudicato le prestazioni, perché l’etichetta in mold labeling (IML), agendo come un rinforzo, ha conferito una maggiore stabilità al contenitore che, nonostante lo spessore davvero ridotto, non crea alcuna difficoltà durante il consumo dello yogurt».
Test approfonditi hanno inoltre rivelato che il nuovo design permette di impilare i vasetti in modo sicuro anche da pieni, senza creare inconvenienti nella logistica. Altro vantaggio, sono adatti per il riempimento sia a freddo sia a caldo fino a 85 °C, aspetto importante per Greiner che ha adottato gli stessi criteri per realizzare contenitori a pareti sottili in una grande varietà di forme per molti altri alimenti, capaci di soddisfare le richieste dei mercati di tutto il mondo. «Bordo sigillato, base rotonda o quadrata: ogni produttore ha il proprio design specifico per gli imballaggi e noi dobbiamo adattarci con la massima flessibilità» afferma Engelbert Pranzl, responsabile impianti dell’azienda di Kremsmünster. «Obiettivo che la tecnologia di stampaggio a iniezione ci permette di perseguire, perché consente di ottenere una notevole libertà di forme e assicura tolleranze di produzione ristrette».
Pressa ibrida ad alta velocità
I nuovi vasetti per lo yogurt vengono stampati con una pressa a iniezione Engel e-speed con forza di chiusura di 380 tonnellate, entrata in reparto appositamente per soddisfare le necessità imposte dal processo messo a punto per ridurre lo spessore delle pareti.
«Sfruttiamo a nostro vantaggio la potenza idraulica di questa macchina ad azionamento ibrido» spiega Andreas Ecker. «Abbiamo bisogno di dinamiche estremamente elevate in fase di iniezione, che spingono al limite le nostre unità di iniezione elettriche. Nella produzione dei vasetti per yogurt, abbiamo un rapporto tra lo spessore della parete e il percorso del fuso di 1:240, mentre la pressione di iniezione raggiunge i 1.700 bar».
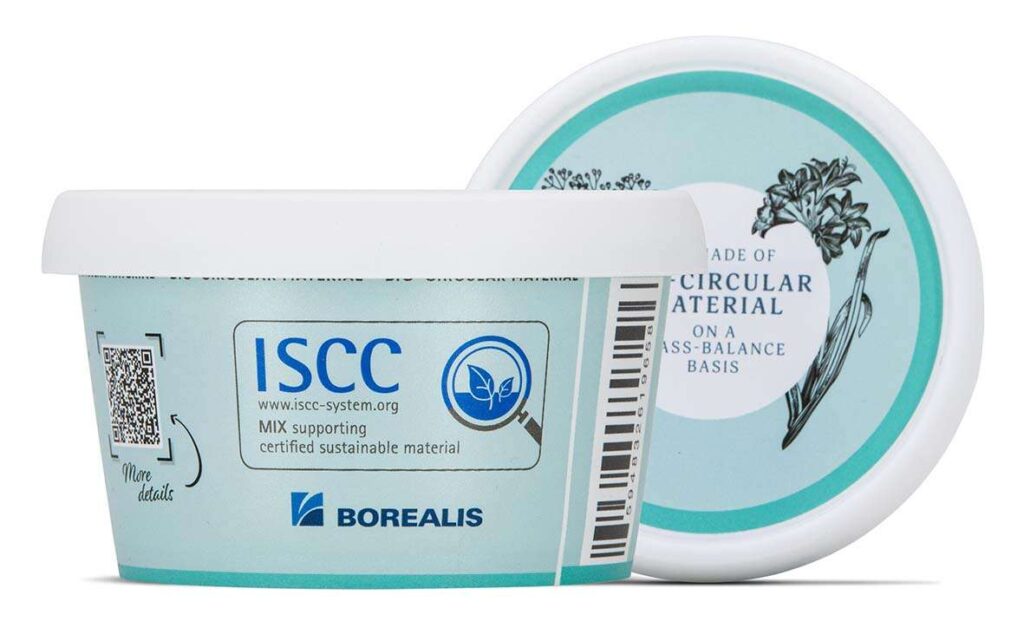
Tenendo conto delle elevate sollecitazioni meccaniche che si generano, Engel ha progettato le presse di questa serie (che combinano un gruppo di chiusura elettrico con un gruppo di iniezione ibrido) specificamente per applicazioni a pareti sottili e ad alta velocità. Inoltre, per garantire il livello di pulizia richiesto dall’industria alimentare, la ginocchiera è incapsulata. L’espansione della serie, nel corso dell’ultimo anno, ha comportato l’ulteriore miglioramento delle prestazioni in tutti i tonnellaggi. Il gruppo di iniezione idraulico in linea con l’azionamento elettrico per la plastificazione offre ora prestazioni ancora migliori: infatti, è progettato per velocità di iniezione fino a 1.200 millimetri al secondo.
Anche il basamento della macchina e i piani portastampo sono stati adattati in modo ancora più puntuale alle esigenze dell’imballaggio a pareti sottili e all’utilizzo di stampi a più impronte, con o senza sistema di etichettatura nello stampo. L’obiettivo principale, comunque, resta quello di garantire la precisione dei movimenti della pressa e, soprattutto nell’IML, la ripetibilità. Senza trascurare, infine, la lunga durata della macchina.
Qualità “zero difetti”
I vasetti per lo yogurt sono prodotti in modo completamente automatico in uno stampo a sei impronte. La pressa è dotata di un robot del costruttore olandese IML Brink, che preleva le etichette wrap around dal caricatore e le inserisce nello stampo, e – terminata la fase di stampaggio – rimuove i vasetti decorati, li trasferisce al controllo di qualità e quindi li impila su un nastro di uscita. Infine, le pile di contenitori vengono imballate in scatole attraverso un successivo processo automatizzato.
Il controllo di qualità è di tipo visivo e viene effettuato mediante una telecamera. Oltre alle dimensioni e ad altri parametri, viene controllata la corretta posizione dell’etichetta per garantire un’adeguata protezione del contenuto ed eventuali fuoriuscite. Ennstal Milch è particolarmente attenta alla qualità ed esige una garanzia “zero errori”.
Cresce l’efficienza energetica
La pressa, i sistemi di automazione e per il controllo della qualità sono stati progettati con un’attenzione particolare alla flessibilità, in modo da assicurare che la forma del contenitore e dell’etichetta possano essere cambiate con brevi tempi di riattrezzaggio. Un’ulteriore priorità – per tutti i prodotti – è la massima efficienza energetica. Per ottimizzare i consumi anche nelle operazioni ad alta velocità, la pressa e-speed 380 è dotata di un sistema che assorbe l’energia di frenata del piano portastampo e la restituisce al motore per favorire la riaccelerazione del piano stesso. «L’efficienza energetica della macchina ha rappresentato un aspetto chiave nel processo decisionale di acquisto, perché il miglioramento costante delle prestazioni dei nostri impianti è da sempre legato alla riduzione del consumo energetico» sottolinea Engelbert Pranzl. «Non solo le vecchie presse a iniezione idrauliche vengono gradualmente sostituite con macchine ibride o completamente elettriche, ma è stato nominato un responsabile aziendale dell’efficienza energetica che monitora da vicino tutti i progetti, prestando particolare attenzione ai processi produttivi» precisa.
Sviluppo in partnership
La prima pressa elettrica è entrata nello stabilimento di Kremsmünster quasi vent’anni fa e da allora Greiner ha sempre seguito da vicino l’evoluzione della tecnologia all electric di Engel, instaurando una collaborazione in numerosi progetti tecnologici. «I nostri suggerimenti sono stati presi in considerazione per sviluppare sia il supporto del piano portastampo della linea e-speed, sia la versione Speed dei robot lineari Engel viper» sottolinea Engelbert Pranzl. «Nella versione Speed, i robot viper riescono a ridurre al minimo i tempi di estrazione dallo stampo, riducendo al contempo anche i tempi di ciclo complessivi» conclude.