Si può dire che Enrico Bonetti sia nato e cresciuto tra presse, stampi e prodotti in plastica. Nel 1969 il nonno aprì un’azienda a Telgate (Bergamo), specializzata in produzioni per il settore della prima infanzia e dei giocattoli, successivamente condotta e riconvertita dallo zio per realizzare sedie e tavoli. Un’attitudine di famiglia che Bonetti ha deciso di alimentare in prima persona quando, nel 1991, acquistò due presse usate per fondare la propria ditta individuale. Muoveva così i primi passi quella che oggi è EB Plast, moderna e dinamica realtà specializzata nella produzione di componenti in plastica a servizio di una clientela attiva in numerosi settori, a partire da quello dei dispositivi di protezione individuale che rappresenta il core business aziendale. Nella sede di Chiuduno (Bergamo), operativa dal 2006 e ulteriormente ampliata nel 2015, lavorano su tre turni giornalieri circa 20 addetti.
Come è articolata la vostra attività? E quali sono i campi di specializzazione?
Il nostro cliente principale produce caschi sportivi – da equitazione, sci e mountain bike – e per gli ambienti di lavoro, e si avvale della nostra collaborazione per la fornitura sia delle calotte sia di componenti accessori come griglie per le prese d’aria, pulsanti scorrevoli, decorazioni… Questo segmento assorbe circa il 70% della nostra produzione e ci impegna nello stampaggio di componenti ad alto valore aggiunto, caratterizzati non solo da un aspetto estetico impeccabile, ma anche da prestazioni capaci di soddisfare le più stringenti norme di omologazione specifiche per le diverse specializzazioni. La nostra capacità attuale sfiora i 400.000 caschi all’anno, con un andamento in continuo sviluppo per accompagnare le richieste del nostro cliente, che detiene una posizione di leadership nel settore. Una crescita che ci stimola alla continua ricerca, progettazione e co-progettazione di soluzioni innovative per accessori, agganci, tipologie di visiera… Per ora non ci occupiamo dell’assemblaggio dei componenti, anche se è nei nostri programmi futuri pensare di allestire una linea dedicata.
Accanto al nostro core business, seguiamo con interesse il settore agricolo e della moda, ma anche degli articoli per l’infanzia, al quale oggi forniamo milioni di pezzi di biberon di diverso formato in polipropilene alimentare.
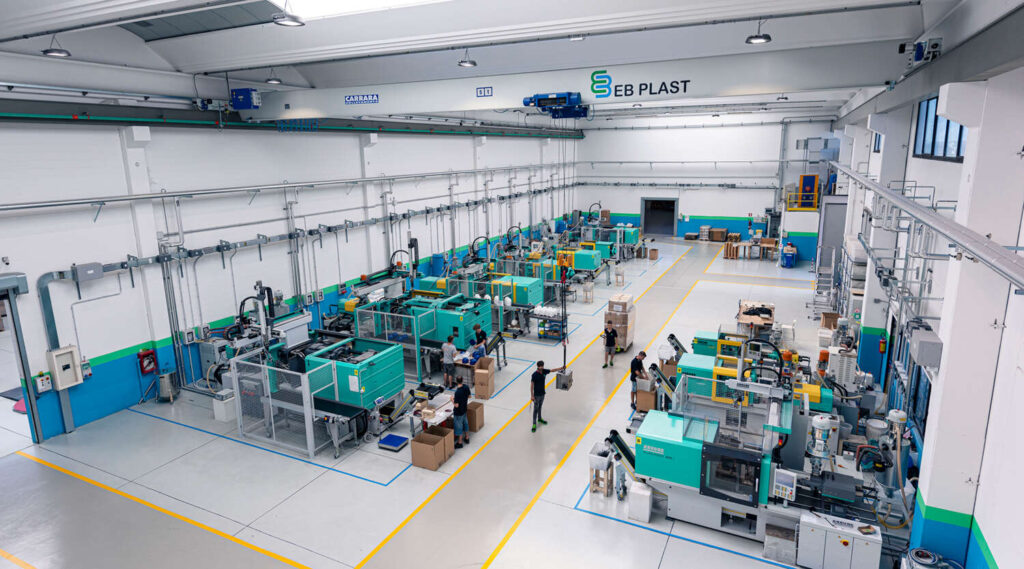
Come è organizzato il reparto di stampaggio?
Disponiamo di dieci moderne presse a iniezione di diverso tonnellaggio – tutte dello stesso marchio – alle quali nei prossimi mesi se ne aggiungerà un’altra recentemente acquistata. La prima Arburg è entrata nello stabilimento nel 2010 e da allora il rapporto con il costruttore tedesco si è fatto sempre più esclusivo, perché ritengo sappia offrirci le migliori garanzie in termini di qualità, affidabilità e servizio di assistenza.
Ogni macchina è dotata delle attrezzature necessarie per operare come un’isola di lavoro autonoma, ma soprattutto del sistema con computer centrale ALS di Arburg.
Piccoli ma digitalizzati…
Considero il sistema gestionale ALS come uno degli acquisti più utili e sensati effettuati negli ultimi anni, perché ci permette di ottimizzare la pianificazione della produzione già dall’inserimento dell’ordine, del rispetto dei tempi di consegna e delle politiche di acquisto. Dal momento che il sistema è interfacciato con l’ERP aziendale, riusciamo a gestire il magazzino sia delle materie prime sia dei pezzi finiti, classificati e stoccati in base alla tipologia e ai tempi di consegna. Quando un ordine non previsto influisce sulla gestione dei materiali è il sistema stesso a generare degli alert, aiutandoci a risolvere qualsiasi problema di fornitura e approvvigionamento. In reparto, invece, il MES Arburg aggiorna costantemente l’operatore sui valori di riferimento delle presse, sull’avanzamento degli ordini, sui turni e la qualità della produzione. Il flusso di lavoro è gestito nella massima trasparenza e tracciabilità, consentendo l’accesso ai dati non solo a bordo macchina, ma sempre e ovunque, sia da PC sia da dispositivi mobili. Da questo punto di vista, disporre di un parco macchine monomarca è certamente di grande aiuto.
Il collegamento di tutte le presse con l’ALS ci permette di pianificare anche un anno di lavoro, ma ovviamente preferiamo affinare la gestione di settimana in settimana e, con l’aggiunta dell’elasticità e della fantasia che fanno la fortuna di tanti piccoli stampatori italiani, riusciamo a soddisfare le immancabili esigenze last minute che in assenza degli strumenti adeguati spesso di rivelano destabilizzanti per l’organizzazione del lavoro. La volontà di continuare ad alzare il tasso di automazione ci porterà a dotarci di touchpad interfacciati a bordo macchina per poter meglio gestire gli scarti di lavorazione, che rappresentano una voce fondamentale per l’equilibrio del magazzino e soprattutto del conto economico.
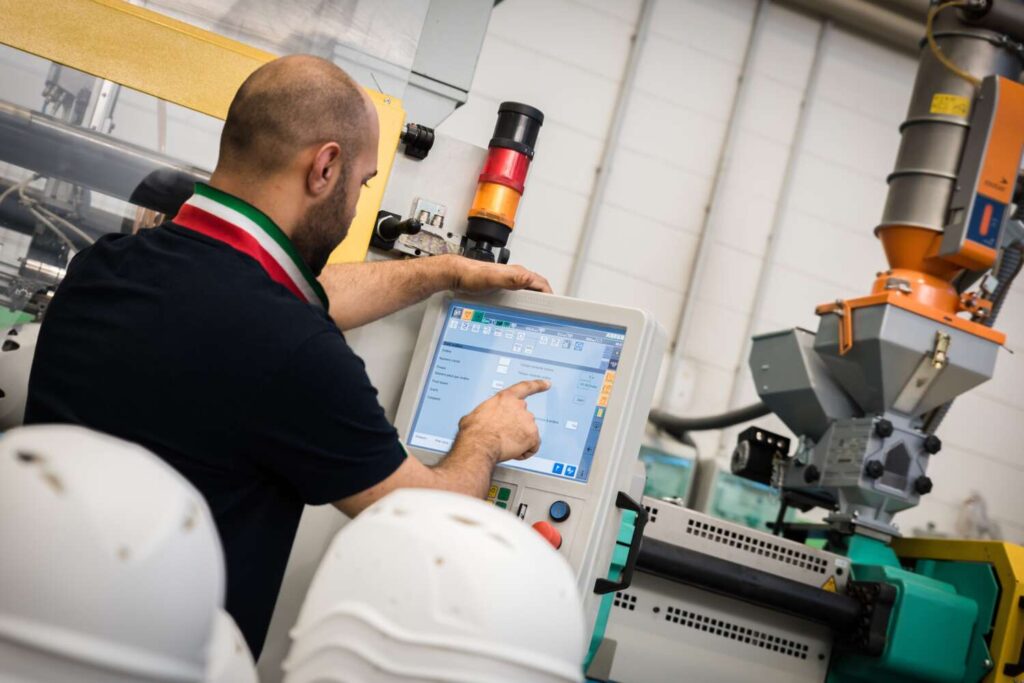
Applicate queste logiche anche in altri ambiti della fabbrica?
Il nostro parco stampi comprende oltre duecento attrezzature, tutte praticamente attive nelle rotazioni di produzione e dotate di identificatore mediante QR code. Attraverso il sistema ALS possiamo curarne con precisione i tempi di manutenzione, sia direttamente sia – in caso di interventi più complessi – attraverso un costruttore di stampi con cui collaboriamo. Un altro obiettivo è dotare l’azienda di un piccolo ma efficiente reparto interno per queste operazioni.
Ritiene che la digitalizzazione sia un passo indispensabile anche per le PMI?
Sono davvero convinto che l’automazione sia il futuro del manifatturiero, un obiettivo che perseguiamo investendo costantemente in tal senso. Siamo sempre stati molto attenti alle politiche di incentivazione, utilizzando al meglio le diverse opportunità di finanziamento – dall’iper-ammortamento per Industria 4.0 alla Sabatini, al 50% sul credito di imposta – offerte alle imprese per migliorare il proprio tasso tecnologico e produttivo. In questi ultimi anni non ci siamo limitati a rinnovare il parco macchine, ma abbiamo investito anche su un server dedicato alla gestione dei big data da quattro terabite – indispensabile per la gestione delle più moderne macchine – che abbiamo installato in una stanza dedicata.
Come si razionalizza la gestione delle materie prime quando si producono milioni di pezzi?
Nella lavorazione dei caschi gli scarti di lavorazione assumono un’importanza non secondaria: trattandosi di un prodotto che deve soddisfare requisiti estetici elevati tendiamo infatti a eliminare anche i pezzi con difetti davvero minimi, quasi impercettibili. E questo, soprattutto per le calotte, comporta la perdita di discrete quantità di materia prima (ABS, PC e HDPE), dal momento che non può essere riutilizzata in blend e miscele, pena il decadimento della resistenza meccanica. Per questo, scherzando con i miei collaboratori, dico che il mio socio di minoranza si chiama, per l’appunto, scarto. È un socio invadente ma silenzioso, che va limitato per non perdere efficienza oltre che denaro. Uno dei nostri obiettivi, pertanto, è riuscire a operare a “zero difetti” attraverso un controllo rigoroso dei processi aziendali, la manutenzione preventiva delle macchine e degli stampi, la formazione degli operatori e la pulizia del reparto. Per ottimizzare questi processi, all’inizio del 2020 abbiamo inserito nel nostro organico un giovane perito chimico che segue costantemente i nostri protocolli di controllo della qualità e affianca gli operatori in produzione per acquisire una conoscenza ancora più approfondita delle insidie dello stampaggio a iniezione.
Come è organizzato il controllo di qualità?
I nostri operatori verificano attentamente ogni parte, dalle calotte ai componenti più piccoli, come viti, rotelle, ingranaggi… Per quanto riguarda le calotte, l’addetto effettua un attento controllo visivo e al contempo interviene manualmente – ove necessario – su minime sbavature. I pezzi più piccoli, invece, vengono prelevati a campione ogni ora, classificati in sacchetti numerati e quindi inviati al laboratorio, dove il tecnico ne verifica il peso e le caratteristiche al microscopio, e interviene sulla produzione qualora emergessero situazioni non conformi agli standard di qualità. La procedura riveste un’importanza crescente sui prodotti di fascia alta, per i quali è necessario mantenere la massima attenzione.
E gli scarti come vengono gestiti?
Oggi, in un momento critico per shortage e caro polimeri, gli scarti di lavorazione assumono un’importanza strategica, diventando una merce molto richiesta e apprezzata. Per questa ragione dedichiamo la massima attenzione alla loro gestione: dopo averli separati per tipologia di polimero e colore, vengono macinati, insacchettati ed etichettati, quindi ritirati da compounder specializzati, che li rigenerano nella massima trasparenza in una logica di filiera completamente tracciata e rispettosa di tutte le normative.
La filosofia della qualità richiede risorse umane formate in modo adeguato. È facile trovare addetti per le vostre esigenze?
Lo dico con rammarico, ma l’esperienza ci insegna quanto oggi sia sempre più difficile trovare giovani motivati e ambiziosi. I nostri addetti sono solitamente selezionati tramite un’agenzia di lavoro interinale, che ci presenta candidati necessariamente under 30, che abbiamo modo di valutare e formare con contratti a tempo determinato. Nell’arco di quattro mesi, siamo in grado di decidere se investire a lungo termine su una risorsa, alla quale offriamo un contratto di ulteriori sei mesi, che successivamente può essere trasformato in assunzione per tre anni o a tempo indeterminato.
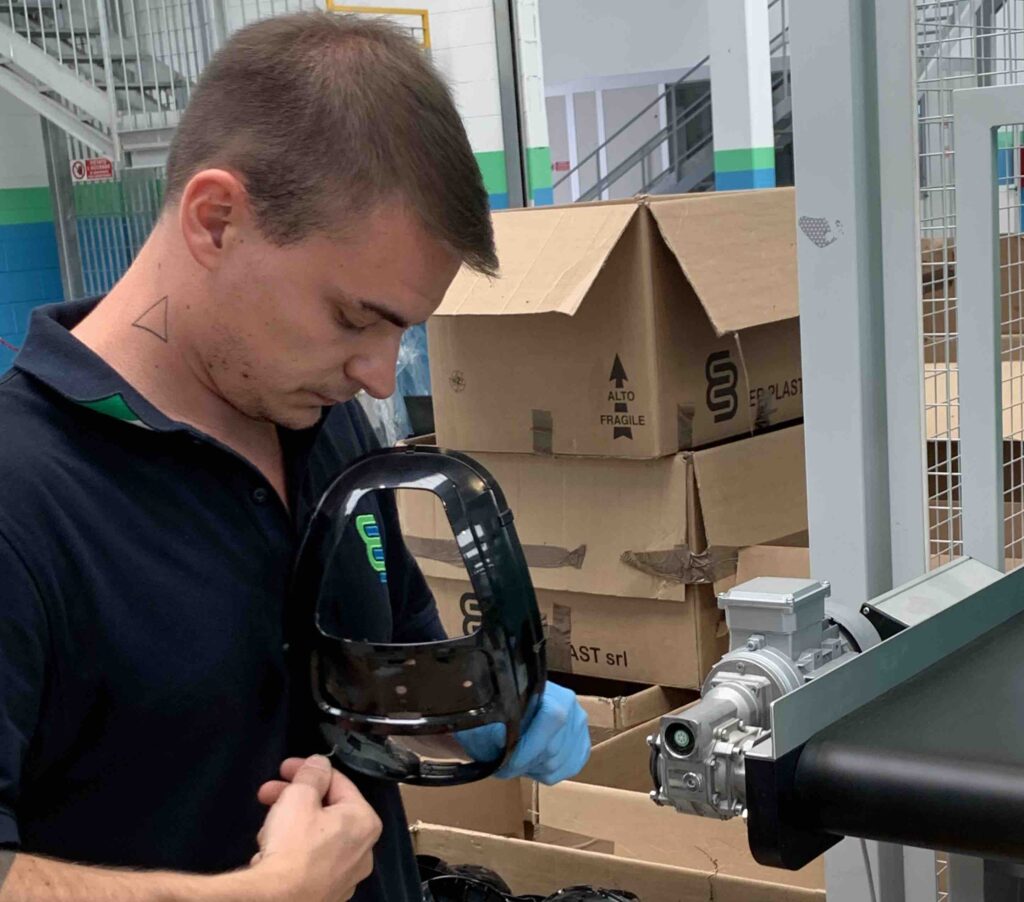
Ha fatto cenno allo shortage. Come avete affrontato la penuria di materie prime?
Come quasi tutti, abbiamo subito l’impatto della crisi di approvvigionamento, tanto che lo scorso marzo abbiamo dovuto rallentare le produzioni basate sul polipropilene. Quando le forniture si sono sbloccate siamo stati costretti a rinegoziare il prezzo del prodotto finito con il nostro cliente, che ci ha riconosciuto percentuali di aumento variabili in funzione del peso dei componenti. Fortunatamente ha compreso la situazione eccezionale: parliamo, infatti, oltre che di difficoltà di reperimento delle materie prime, di un vero raddoppio delle quotazioni per alcuni materiali.
Quanto incidono nella vostra quotidianità le attuali dinamiche di mercato?
Il settore della subfornitura plastica è sottoposto a pressioni e concorrenza ai limiti del sostenibile, spesso basate su politiche di prezzo al ribasso che ormai non riguardano più solo le produzioni asiatiche, perché sono evidenti anche in distretti come quello in cui operiamo, che contano decine di realtà per dimensioni simili alla nostra. Non dobbiamo però dimenticarci di essere aziende italiane ed europee che fanno della qualità e del servizio caratteristiche distintive. Ritengo pertanto che qualunque impresa voglia crescere e strutturarsi abbia il diritto di essere remunerata per quanto vale e, conseguentemente, offre. Un obiettivo che perseguiamo rispettando standard qualitativi altissimi, investendo non solo in tecnologia, ma anche in formazione continua dei dipendenti e sicurezza. Se un’azienda non calcola queste voci può certamente offrire al mercato prodotti di qualità in fasce basse a prezzi molto più contenuti. Non ci si deve però stupire se non riesce ad conseguire i margini necessari per acquistare una nuova macchina, nemmeno beneficiando degli incentivi più vantaggiosi offerti dal Governo.
Come ha impattato la pandemia sul vostro settore?
La produzione dei caschi sportivi è stata ovviamente fortemente ridotta, se non azzerata, mentre l’edilizia ha fatto registrare una crescita importante anche nel 2020. È però al futuro che guardiamo con l’intenzione di non farci trovare impreparati.
I 250 miliardi di fondi del Recovery plan che arriveranno in Italia saranno giocoforza in gran parte dirottati su lavori di adeguamento e crescita infrastrutturale, strategia che per noi significa produrre caschetti.
Progetti per il futuro?
Nonostante sia fermamente convinto che il futuro del nostro settore non potrà mai prescindere dallo stampaggio a iniezione, credo che non si debbano sottovalutare le potenzialità dell’additive manufacturing. Non nascondo che nei prossimi anni è mia intenzione esplorare direttamente questa opportunità, offrendo ai nostri clienti la possibilità di realizzare produzioni di nicchia, speciali, o un servizio di prototipazione rapida. Le peculiarità della manifattura additiva, unita a programmi CAD sempre più performanti ci potranno inoltre consentire di effettuare prove, modifiche e correzioni anche su prodotti che poi verranno realizzati in serie attraverso gli stampi.
L’obiettivo a più breve termine, da conseguire entro la fine di quest’anno o al massimo entro la metà del 2022, è quello di ottenere la certificazione ISO 9000 che, oltre a rappresentare un importante biglietto da visita, è un passaggio che riteniamo imprescindibile dal momento che i nostri standard di lavoro sono di fatto già in linea con i parametri richiesti. È un ulteriore passo avanti per EB Plast, una piccola realtà che vuole continuare a fare della qualità la sua caratteristica per distinguersi sul mercato.