Simulazioni numeriche avanzate permettono una previsione accurata degli stati di sollecitazione e deformazione dei componenti, consentendo di prevedere difettosità che non possono essere trascurate soprattutto se presenti in applicazioni lightweight, dove i coefficienti di sicurezza sono ridotti al minimo
La sostituzione di parti strutturali metalliche con soluzioni realizzate in plastica rinforzata con fibre di vetro consente di ottenere una significativa riduzione di peso e di costo, grazie all’efficienza del processo di stampaggio a iniezione. Nel settore automotive, questa sostituzione è anche nota con il termine metal replacement e porta a una diminuzione dei consumi e delle emissioni delle autovetture con motore a combustione interna. Per i veicoli elettrici, i benefici in termini di aumento dell’autonomia sono ancora più consistenti.
Tuttavia, il processo di stampaggio a iniezione influenza direttamente le proprietà meccaniche del componente stampato, agendo sull’orientazione delle fibre e causando indebolimenti localizzati in discontinuità strutturali legate all’eventuale presenza di linee di giunzione e porosità. Tali difettosità non possono essere trascurate, soprattutto se presenti in applicazioni lightweight, dove i coefficienti di sicurezza sono ridotti al minimo. Per questo motivo è necessario ricorrere a simulazioni numeriche avanzate che permettono una previsione accurata degli stati di sollecitazione e deformazione dei componenti.
Lo stampaggio a iniezione di termoplastici rinforzati con fibre discontinue
I materiali termoplastici rinforzati con fibre discontinue sono ampiamente utilizzati per la produzione di parti in plastica perché possono essere stampati utilizzando presse a iniezione con cicli rapidi e automatizzati, ma presentano proprietà meccaniche molto elevate e basso costo. Tuttavia, le fibre si orientano durante il processo di riempimento dello stampo a causa delle tensioni indotte dal fuso polimerico che si generano lungo il percorso di riempimento prima della solidificazione. Di conseguenza, l’orientamento delle fibre varia da una posizione all’altra del pezzo stampato, determinando proprietà meccaniche anisotrope, cioè fortemente dipendenti da come le fibre sono orientate all’interno del componente stampato rispetto alla direzione d’applicazione dei carichi. In altre parole, il comportamento meccanico del materiale è funzione della direzione del carico rispetto all’orientazione delle fibre.
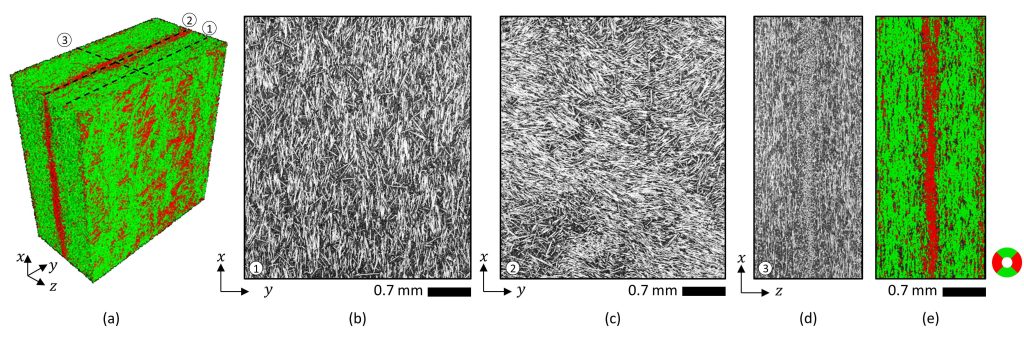
L’orientazione della fibra all’interno dei componenti stampati può essere prevista utilizzando software di simulazione del processo di stampaggio, ma è anche misurabile attraverso scansioni tomografiche. In figura 1 è riportato un esempio di scansione, nella quale è possibile apprezzare non solo la direzione preferenziale delle fibre, ma anche la variazione dell’orientazione lungo lo spessore della parete.
Il componente stampato a cui si fa riferimento in figura 1 è una placca di spessore costante, in cui il flusso di riempimento è allineato alla direzione X. È perciò possibile notare che la zona più soggetta a stress tangenziali (il cosiddetto shear layer) presenta un’orientazione preferenziale nella direzione del flusso, mentre nella zona centrale l’orientazione è casuale. Infatti, le tensioni di taglio raggiungono il valore massimo in prossimità della parete dello stampo e si trasferiscono dal fuso alle fibre causandone l’allineamento al flusso.
Tale orientazione preferenziale, come già anticipato, ha una forte influenza sulle proprietà meccaniche del materiale. Una prova di questo si può osservare in figura 2, in cui sono riportate le curve di trazione per provini ricavati da placca a diverse orientazioni rispetto alla direzione di riempimento. Si può notare come le curve per provini tagliati a 45° e 90° si allontanino notevolmente dalla curva a 0°, sia in termini di modulo elastico (pendenza della curva) sia in termini di tensione a rottura. Inoltre, in figura 2, per confronto, è stata inserita la curva relativa al comportamento elastico lineare del materiale dichiarata dal produttore nella scheda tecnica del materiale.
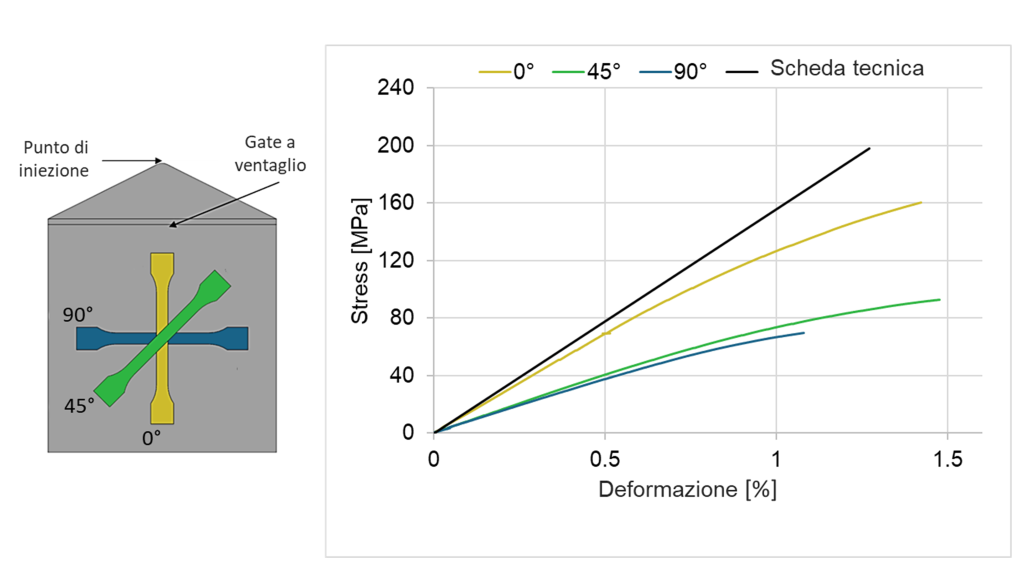
Appare evidente che le proprietà dichiarate sono molto superiori a quelle misurate sul pezzo stampato. Qual è il motivo di tale differenza? Le proprietà meccaniche dichiarate in scheda tecnica sono determinate da prove effettuate su provini stampati direttamente nella forma prevista dalla normativa. Tale geometria consente di avere un’elevata orientazione delle fibre perché le tensioni di taglio elevate in prossimità delle quattro pareti e la geometria convergente del provino orientano maggiormente il rinforzo. Tutto questo si traduce in un più elevato modulo elastico e in una tensione a rottura maggiore.
Perciò, quando acquistiamo un materiale, sarà necessario tenere conto del fatto che nel nostro componente non avremo mai una perfetta orientazione delle fibre e, di conseguenza, nemmeno le proprietà dichiarate in scheda tecnica. Questo vale per tutti i materiali. Le proprietà dichiarate in scheda tecnica sono ottenute con prove normate e consentono di confrontare i materiali tra loro in fase di selezione. Per la progettazione sarà necessario utilizzare proprietà misurate da provini ricavati in modo analogo a quanto mostrato in figura 2.
La marcata anisotropia è il limite principale dei materiali rinforzati con fibra, ma ulteriori criticità sono causate dalla presenza dei seguenti difetti indotti dallo stampaggio:
- Linee di giunzione: le linee di giunzione si vengono a formare nei componenti stampati quando il flusso di materiale si separa e poi si ricongiunge in presenza di fori o aperture. Con riferimento alla figura 3, si può notare come nella linea di giunzione le fibre si orientino perpendicolarmente al flusso e non si compenetrino, formando una discontinuità in cui solo la matrice polimerica funge da legante strutturale. Questo indebolimento localizzato rispetto al resto della struttura è tanto più marcato quanto maggiore è la concentrazione del rinforzo. Un polipropilene caricato con il 40% di fibra di vetro corta può presentare linee di giunzione aventi solo il 20% della resistenza nominale.
- Porosità: Durante la fase di raffreddamento, il materiale all’interno della cavità stampo subisce ritiri volumetrici caratteristici, che sono però contrastati dalla presenza di strati superficiali molto rigidi, a causa della presenza delle fibre di rinforzo. Questo porta alla formazione di pericolose porosità e cavità di ritiro all’interno del componente in corrispondenza di variazioni di spessore, non visibili a un primo esame del componente stampato. Tali difetti agiscono come intensificatori degli sforzi, o come inneschi di cricca, e possono portare a rottura una parte strutturale apparentemente progettata in modo corretto.
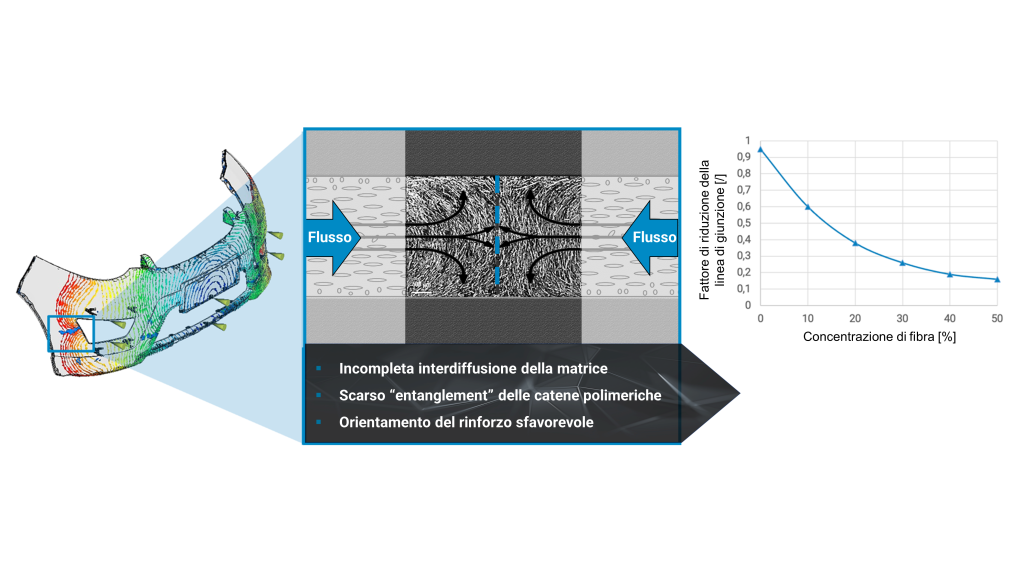
Mappatura delle proprietà locali e analisi strutturali avanzate
Le analisi numeriche strutturali condotte attraverso software dedicati, sono largamente utilizzate per la previsione della rigidezza e della resistenza di componenti ai quali sono richieste performance meccaniche elevate. Tuttavia, quando si simula il comportamento di plastiche fibrorinforzate stampate a iniezione, la morfologia locale e le proprietà meccaniche del materiale vengono spesso approssimate: comportamento elastico lineare e isotropo, assenza di linee di giunzione e porosità.
Tali ipotesi rendono però i risultati meno attendibili, costringendo il progettista ad adottare coefficienti di sicurezza più elevati, i quali si traducono in pareti più spesse e quindi in componenti più pesanti.
Lo stato dell’arte dell’analisi numerica per componenti polimerici fibrorinforzati permette di tener conto della morfologia locale. Attraverso software di mappatura, è possibile trasferire i risultati dell’analisi di processo (orientazione delle fibre, linee di giunzione e stress residui) nell’analisi strutturale. Con riferimento alla figura 4, il software di mappatura associa agli elementi del modello strutturale specifiche proprietà provenienti dai risultati dell’analisi di processo, creando un file di input per l’analisi strutturale agli elementi finiti (FEA). Grazie a questo passaggio intermedio, i risultati dell’analisi strutturale terranno conto delle proprietà del materiale derivanti dal processo produttivo.
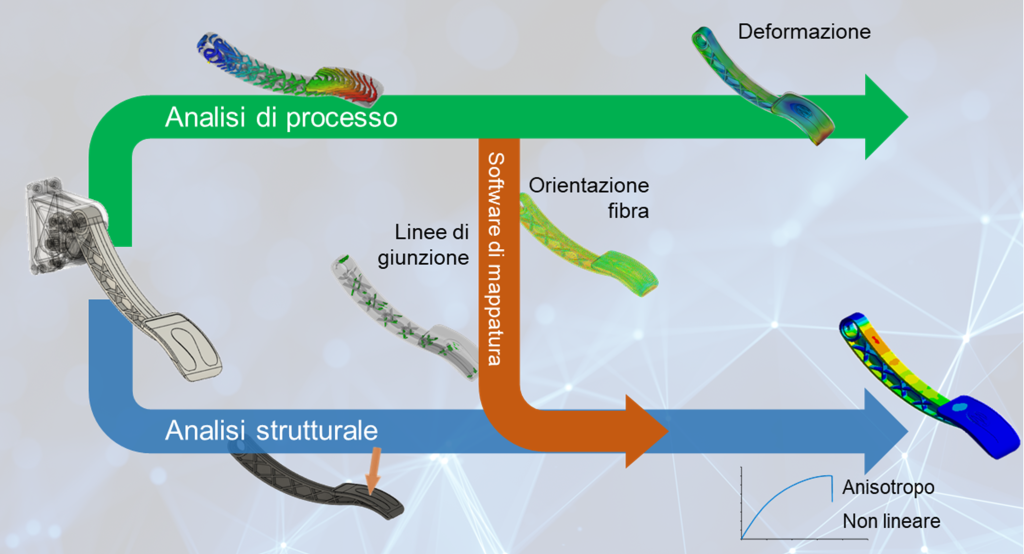
Applicazione a un caso studio
Per dimostrare la sensibilità della simulazione strutturale alla morfologia locale del materiale, la metodologia descritta è stata applicata a un caso studio. Il componente considerato è un provino a farfalla per prove a trazione, realizzato con doppio gate in modo da ottenerne una linea di giunzione nella regione centrale (figura 5). Il materiale utilizzato è un polipropilene rinforzato con il 50% di fibra di vetro.
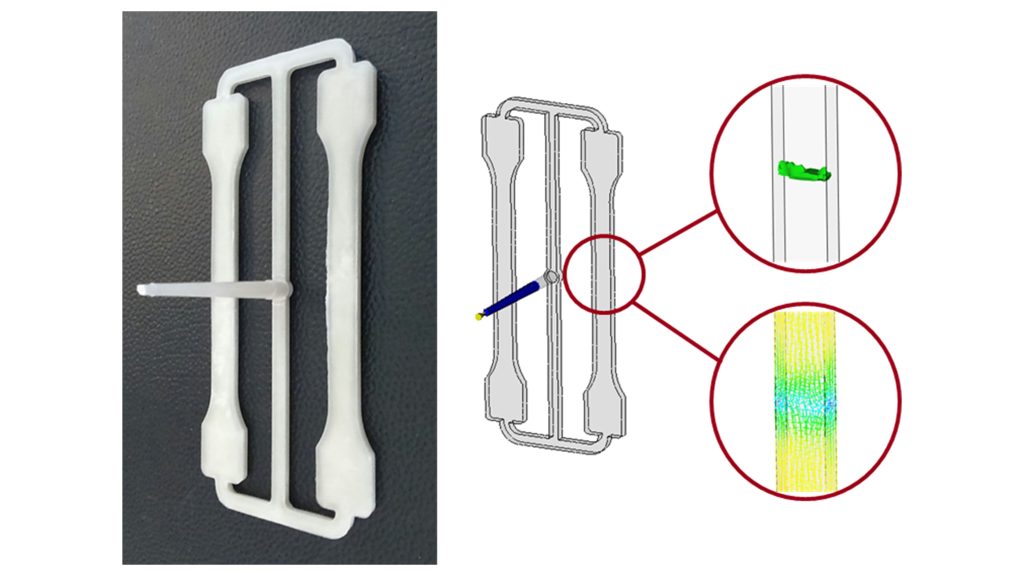
Seguendo lo schema logico di figura 4, la simulazione del processo di stampaggio a iniezione è stata condotta per prevedere in ogni punto del componente l’orientazione delle fibre e l’eventuale presenza di difetti strutturali. Per tradurre tali risultati in proprietà meccaniche, la caratterizzazione meccanica del materiale è stata condotta su provini ricavati da placche per diverse orientazioni (figura 2).
Per valutare i risultati ottenuti, sono state confrontate le curve forza-spostamento registrate nella prova di trazione. In figura 6a è possibile notare come, seguendo le due strade differenti di modellazione (tradizionale e avanzata), si otterranno risultati nettamente diversi. La prima cosa che salta all’occhio è la non omogeneità delle tensioni e delle deformazioni presente nell’analisi avanzata, che non viene colta da quella tradizionale. Tale comportamento fa risaltare i picchi di tensione che potrebbero essere fatali per il componente; ciò significa che, lavorando con la metodologia tradizionale, si è in “sfavore di sicurezza”, trascurando fenomeni che potrebbero crearsi e inspiegabilmente portare a rottura il componente.
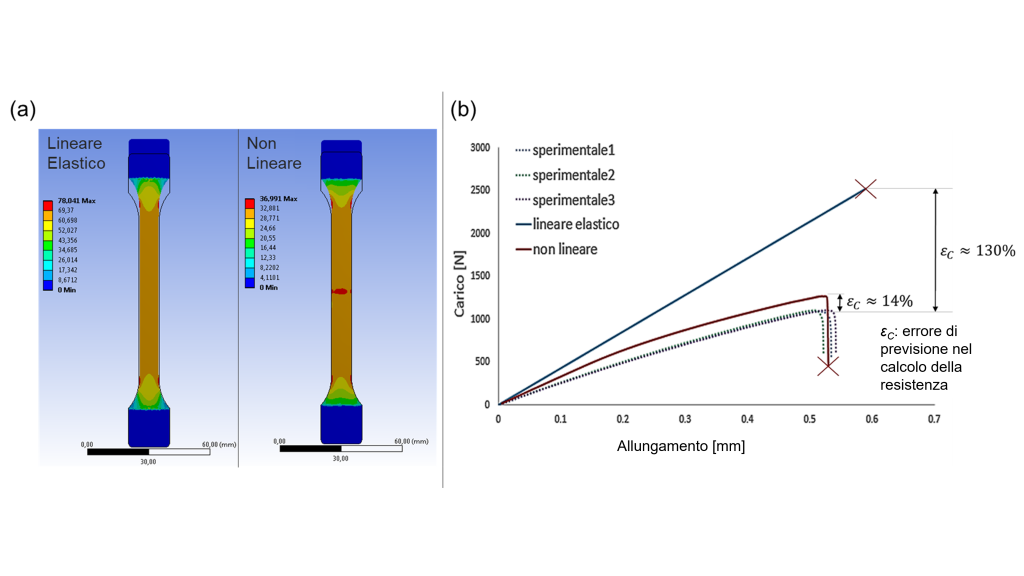
In figura 6b è possibile osservare lo scostamento tra i dati sperimentali (linee tratteggiate) e le curve numeriche (linee continue). In particolare, è possibile notare come l’andamento dell’analisi tradizionale (linea blu) sia più lontano dai dati sperimentali rispetto all’analisi avanzata (linea rossa). Inoltre, è possibile apprezzare la migliore previsione della rigidezza del provino, grazie alla modellazione delle curve del materiale e del carico a rottura per effetto della modellazione della linea di giunzione.
In conclusione, la simulazione strutturale avanzata, che integra le informazioni ottenute dall’analisi numerica del processo di stampaggio, è uno strumento fondamentale nello sviluppo di elementi strutturali leggeri e nella progettazione affidabile di componenti rilevanti per la sicurezza. Consente di ridurre i coefficienti di sicurezza (e di conseguenza gli sprechi di materiale) prevedendo accuratamente gli effetti del processo produttivo e il conseguente comportamento anisotropo del materiale sul componente.
Riccardo Ivan e Giovanni Lucchetta (Università degli Studi di Padova),
rivista Plastix n. 5, giugno 2023