di Roberto Carminati
È stata presentata nel corso di una tre-giorni di open days nello stabilimento di Amut, a Novara, la nuova linea che l’azienda piemontese ha realizzato in collaborazione con l’austriaca Erema e che consente di ottenere foglia per packaging alimentare dalle scaglie di bottiglie in PET post consumo. L’impianto è imponente e vanta una portata sino a 1400 kg/ora di materiale, lavorato a una velocità massima di 60 metri al minuto.
Dell’operazione è stata protagonista la divisione Amut Extrusion, con tutto il suo bagaglio di competenze nella progettazione e nello sviluppo di estrusori e attrezzature ausiliarie idonee alla produzione di foglia, lastra, film, membrane impermeabilizzanti, tubi e profili. Dal canto suo, Erema ha messo a disposizione la sua tecnologia per la decontaminazione del PET, ottenibile con il reattore della serie MPR.
Un processo certificato
Come ha spiegato a Plastix il sales area manager di Amut, Alessandro Zanzi, l’impianto può sì lavorare con polietilentereftalato post consumo, ma anche con materiale vergine o rimacinato da scarti. Quel che più conta è il risultato finale, rappresentato da un processo bottle-to-packaging conforme agli standard statunitensi della locale Food & Drug Administration (FDA) e, nell’UE, della European Food Safety Authority (EFSA).
Per quel che riguarda la soluzione brevettata di Erema, questa lavora in vuoto quasi assoluto e a una temperatura di 180 gradi centigradi, con un tempo di residenza – ovvero la permanenza del materiale nel reattore – pari a circa un’ora. Una volta terminate le attività di decontaminazione propriamente dette si passa direttamente, con flusso continuo, alla fase di estrusione.
Spessori ridotti, consumi contenuti
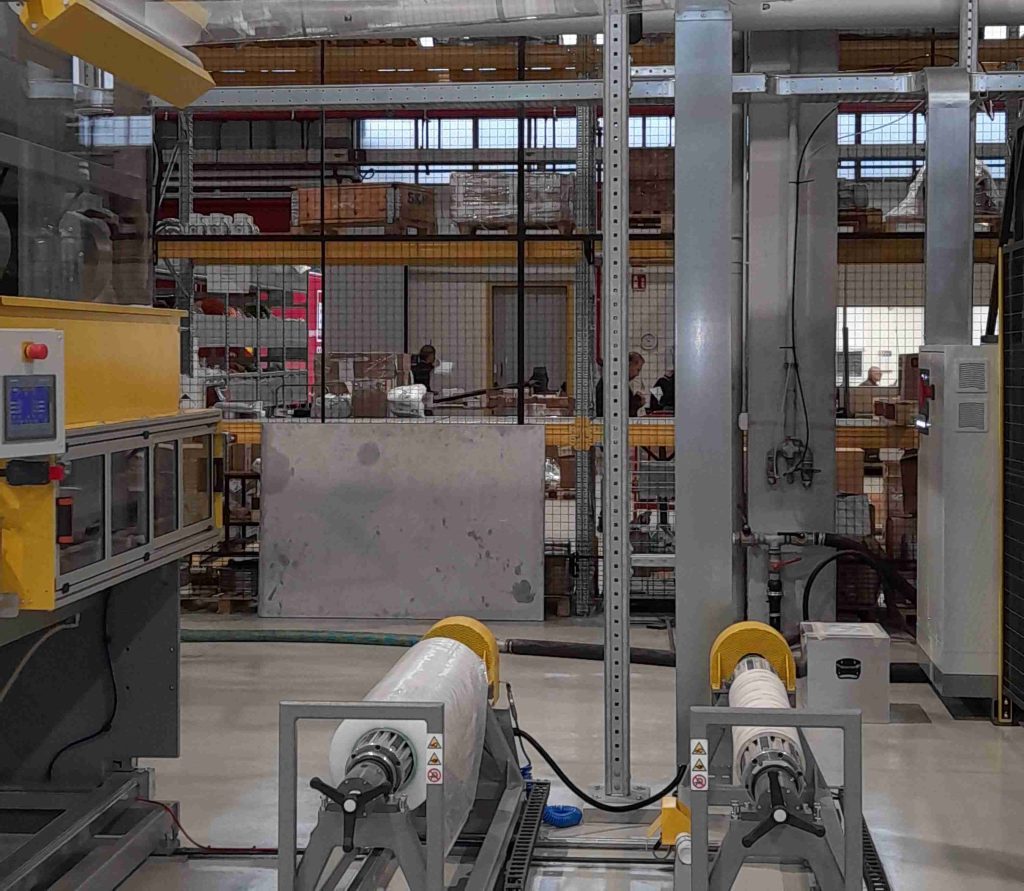
Al centro è, in questa fattispecie, l’estrusore monovite Amut di nuova generazione, con diametro di 130 millimetri e dotato di un sistema di alimentazione forzata che consente d’introdurre il materiale nella macchina in maniera ottimale e indipendentemente dalla forma fisica e dalla densità apparente del materiale stesso.
La linea è inoltre caratterizzata da un’unità per l’applicazione di un sottile strato di silicone sulle superfici della foglia, al fine di evitare l’adesione dei prodotti termoformati dopo il loro impilaggio (anti-blocking). A seconda delle richieste dei clienti, è possibile dare vita a configurazioni multistrato, fino a un massimo di tre strati.
La testa di estrusione permette di regolare in automatico lo spessore della foglia e la calandra, qui in versione orizzontale, garantisce la calibrazione e il raffreddamento della foglia estrusa.
La linea è avviata dagli addetti mediante una procedura software completamente automatica; automatizzati sono anche i cambi di spessore e i cambi di produzione. Per la saldabilità sui prodotti termoformati è stato predisposto un gruppo per la laminazione di film in polietilene. Con lo stesso gruppo è inoltre possibile accoppiare film multistrato con funzione barriera.
Taglio e rifilatura sono automatici e i rifili, dopo la macinatura in linea, sono reintrodotti nell’estrusore. Dall’intera lavorazione si ottiene una foglia che, nonostante il ridotto spessore, garantisce una resistenza meccanica ottimale grazie all’estrazione, durante il trattamento di decontaminazione, dell’umidità assorbita dal materiale in entrata al processo, prevenendo così la degradazione per idrolisi del PET. E “l’occhio di riguardo” verso la sostenibilità si esprime anche tramite i consumi energetici contenuti dell’impianto.