Le aspettative suscitate dalla nuova serie di vetture elettriche BMW nel settore dei compositi in fibra di carbonio non destano alcuna sorpresa. Con volumi di produzione annua che si aggirano intorno alle 30.000 unità, la i3 è infatti la prima automobile prodotta in serie a fare largo uso di compositi rinforzati con fibre di carbonio (CFRP). E con un livello di produzione tale, ogni anno la sola i3 potrebbe necessitare di oltre 4.355 tonnellate di parti strutturali in CFRP. Cifre interessanti, ma che devono essere valutate nella giusta prospettiva. Tra circa 100 modelli di veicoli fabbricati in tutto il mondo, la i3 è l’unica a offrire di serie equipaggiamenti realizzati in compositi al carbonio che generalmente vengono montati su automobili di lusso o su modelli di nicchia come le supercar o le ipercar da un milione di dollari. Un segmento che assorbe approssimativamente 4.990 milioni di tonnellate (Mt) di parti strutturali in CFRP ogni anno in tutto il mondo. Dunque, nell’arco di due anni, il programma di produzione della i3, benché a volumi ridotti, potrebbe raddoppiare la domanda globale di CFRP per il comparto automotive. A questo punto la domande viene spontanea: quanti progetti simili a quello della i3 sono necessari per rivoluzionare il settore dei compositi avanzati? E quindi, l’industria automobilistica è davvero a un punto di svolta?
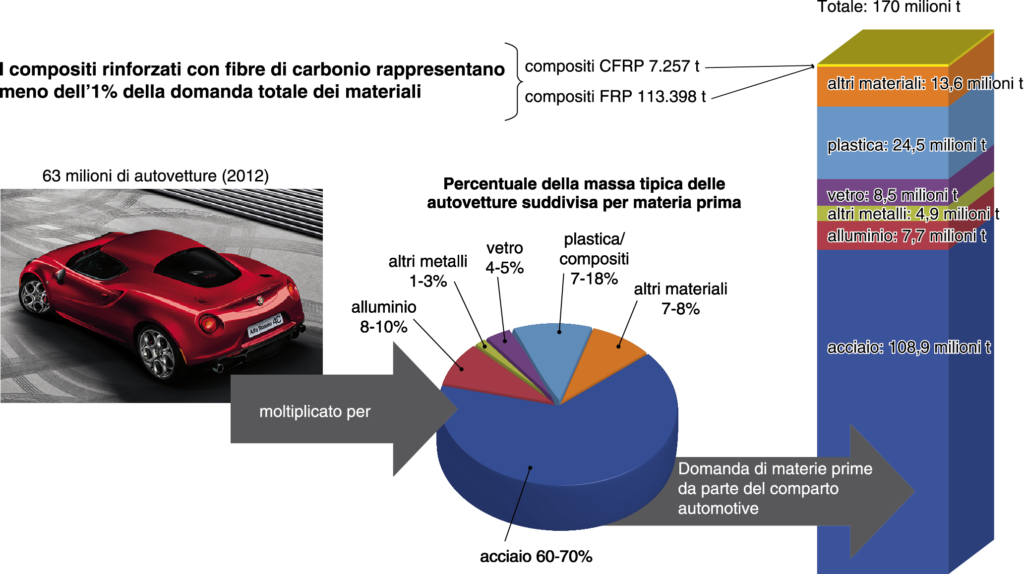
*Le supercar, meno di 1/10 dell’1% totale, non sono visibili nel grafico
Fonte Composites Forecasts and Consulting (luglio 2013)
L’automotive e le materie prime
Secondo l’Organizzazione internazionale dei costruttori di veicoli a motore (OICA, Francia), l’industria automobilistica ha prodotto a livello globale circa 63 milioni di autovetture e 21 milioni di veicoli commerciali nel 2012. Nel resto del decennio, la produzione annua potrebbe crescere fino a 100 milioni di veicoli l’anno, con la Cina che arriverebbe a rappresentare circa il 18-20% della produzione e della domanda totale. Più di 100 costruttori forniscono questi veicoli e offrono circa 1.500 modelli. Il tipico peso a vuoto delle autovetture varia tra 1.364 e 1.818 kg, mentre quello di SUV e crossover è generalmente maggiore di 227-454 kg. In funzione dei materiali, la loro massa può essere suddivisa in varie percentuali (grafico 1).
Secondo un rapido calcolo, ogni anno nel mondo vengono immessi sul mercato oltre 136 milioni di tonnellate (Mt) di automobili e autocarri nuovi. Per la produzione di questi veicoli nel 2012, l’OICA stima che l’industria siderurgica abbia fornito circa 108,86 Mt di acciaio alle case automobilistiche. La Aluminum Association di Arlington, Virginia (USA) ha calcolato che nel 2012 le vendite di alluminio destinato al comparto automotive ammontavano a circa 7,26-7,71 Mt. In confronto, il volume totale dei compositi associati alle autovetture rappresenta un mercato di circa 113.430 tonnellate, ossia solo un esile 1% del peso totale degli autoveicoli venduti. Nel 2013, i volumi di CFRP forniti agli OEM del settore automotive hanno raggiunto circa 7.484 tonnellate, vale a dire circa il 6,5% dei compositi automotive e un minuscolo 0,05% della domanda globale di materiali automotive.
La rivoluzione del design
Le normative in termini di riduzione dei consumi di carburante e di emissioni in vigore in Europa e negli Stati Uniti impongono ai costruttori di veicoli grandi cambiamenti nel design entro i prossimi 11 anni. Dal momento che la forte concorrenza internazionale ha abbreviato i cicli del design da nove a sei-sette anni circa, le case automobilistiche come potranno adeguarsi ai requisiti in costante evoluzione entro il 2025?
Una via percorribile da un OEM potrebbe essere la diminuzione dei consumi di carburante attraverso la sostituzione dei modelli di grandi dimensioni con altri più piccoli dalle prestazioni più elevate. Aston Martin, per esempio, ha recentemente introdotto Cygnet, un modello esclusivo che rappresenta la “versione elegante” della la city car Toyota iQ. La risposta del mercato al lancio della Cygnet è stata assai fredda, poiché rappresenta l’esatto opposto del modello di vettura ad alte prestazioni proposta per esempio da BMW. Nel segmento delle grandi berline, questa soluzione comporterebbe la riduzione delle dimensioni dei veicoli o la totale eliminazione dei modelli più grandi: per esempio, la Ford Crown Victoria e la GM Caprice hanno ceduto il posto, almeno temporaneamente, a modelli più compatti e accattivanti.
Una seconda strategia consiste nel sacrificare le prestazioni a favore di una maggiore efficienza dei consumi. Questa prospettiva sembra più verosimile per i modelli della fascia medio-bassa, dal momento che la potenza e la coppia del motore di molti veicoli di questa categoria sono aumentate del 25-50% nell’ultimo decennio. Pertanto, questa tendenza può essere invertita in modo relativamente semplice grazie all’impiego di motori più piccoli, ad alta efficienza, a GPL o diesel, che consentano inoltre di ridurre i costi di investimento necessari per migliorare il coefficiente MPGe (miglia per gallone di benzina equivalente). Tuttavia, questa idea potrebbe rivelarsi un deterrente per i clienti che cercano automobili di lusso dalle prestazioni elevate.
In realtà, nonostante gli indubbi vantaggi, nessuna di queste soluzioni pensate per abbattere i consumi attirerà mai l’attenzione dei costruttori specializzati in automobili di lusso.
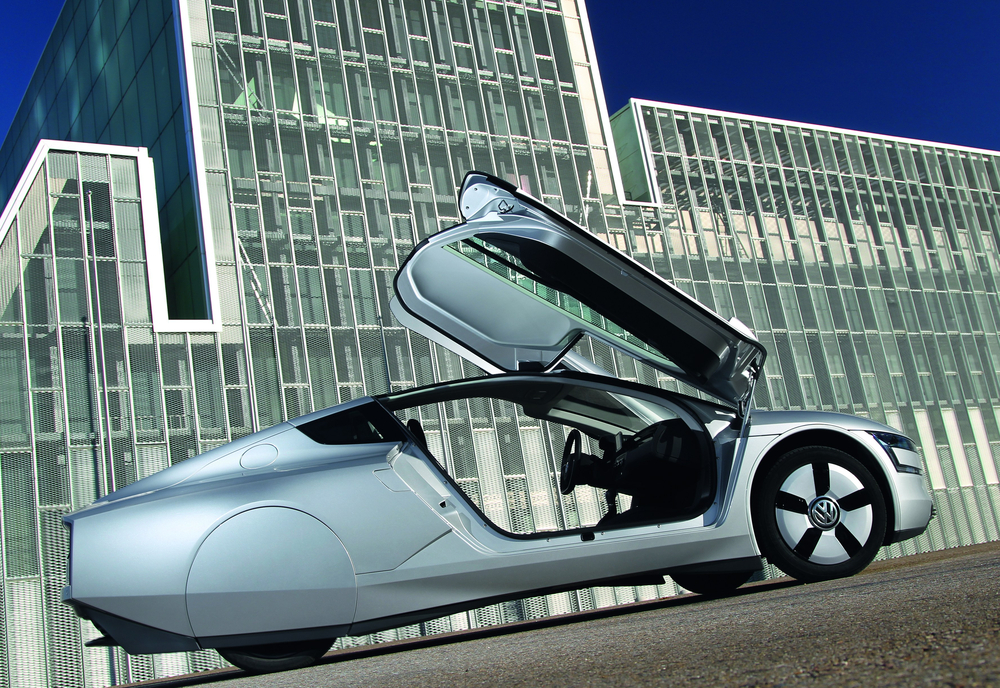
Pneumatici, aerodinamica e molto altro
Anche i costruttori delle automobili più compatte oggi in circolazione dovranno affrontare in modo più concreto le questioni legate ai consumi di carburante. Un obiettivo facilmente raggiungibile potrebbe consistere nella riduzione della resistenza al rotolamento, ossia l’attrito o perdita di energia che si verifica al contatto degli pneumatici con la strada. In generale, la resistenza al rotolamento aumenta di pari passo con il peso del veicoli.
Negli ultimi dieci anni, il gusto estetico dei clienti si è orientato verso ruote più grandi e pesanti (di pari passo con le dimensioni delle automobili). A tal fine, una soluzione potrebbe consistere nell’impiego di pneumatici ad alta pressione (50 psi), che a fronte del costo maggiore consentono di ridurre la resistenza al rotolamento del 25-35%. Per la maggior parte dei modelli attualmente sul mercato, il ritorno a pneumatici di minore diametro ma ad alta pressione porterebbe vantaggi limitati ma significativi. Questa opzione potrebbe essere accettata dalla maggior parte degli automobilisti, ma non dagli amanti del lusso e delle automobili sportive che faticherebbero ad adeguarsi all’inevitabile compromesso sullo stile e la tenuta di strada.
L’aerodinamica è un altro fattore importante in grado di migliorare l’efficienza del veicolo, soprattutto alle velocità raggiunte in autostrada. Per contrastare la resistenza aerodinamica, occorre adottare una duplice strategia: ridurre l’area frontale della vettura (ossia il rapporto tra altezza e larghezza del veicolo) e il coefficiente di resistenza aerodinamica. Ovviamente, vi sono dei limiti oltre i quali la riduzione di altezza e larghezza comprometterebbe lo spazio disponibile e la sicurezza.
Il coefficiente di resistenza aerodinamica delle utilitarie varia perlopiù tra 0,35 e 0,20 (minore è il coefficiente, migliori sono le prestazioni) e non è cambiato di molto negli ultimi 15 anni. Alcuni espedienti, come le griglie a lamelle della Ford Fusion Titanium e il migliore utilizzo delle carenature sottoscocca possono apportare miglioramenti in generale, tuttavia la possibilità di elaborare innovazioni sostanziali basate sulla tradizionale struttura a quattro ruote è piuttosto limitata.
La riprogettazione dell’impianto di alimentazione costituisce l’ambito di ricerca più promettente. Infatti, i veicoli ibridi-elettrici ed elettrici plug-in mostrano già notevoli benefici rispetto ai veicoli equipaggiati con motore a combustione interna. L’efficienza dei motori a combustione interna può essere incrementata mediante turbocompressori e una migliore aspirazione dell’aria nella camera di combustione. L’introduzione di camere di combustione senza valvole e un design innovativo dei motori permetterebbero altresì di ridurre gli attriti interni al motore, tuttavia si tratta di soluzioni ancora non mature dal punto di vista tecnico e commerciale, in alcuni casi vincolate a brevetti che ne riducono la potenziale diffusione. La riduzione dell’attrito interno degli organi della trasmissione e degli altri componenti coinvolti si traduce in un miglioramento dell’efficienza complessiva. Nel complesso, l’incremento dell’efficienza della trasmissione potrebbe contribuire per il 25-35% al miglioramento complessivo ottenibile fino al 2025.
Il fattore critico
Queste misure, sebbene efficaci, non sono tuttavia sufficienti. Tra gli elementi che influiscono sull’efficienza del veicolo, la massa è sicuramente quello più rilevante. La riduzione del peso non comporta necessariamente dei sacrifici significativi in fatto di comfort del guidatore e dei passeggeri: infatti, per le vetture ibride e plug-in, è un fattore essenziale al fine di raggiungere prestazioni paragonabili ai veicoli equipaggiati con i tradizionali motori a combustione interna.
Teoricamente, ogni nuova vettura introdotta sul mercato dovrà essere sottoposta a una “dieta dimagrante”. Una diminuzione di 45 chilogrammi, infatti, consente di ridurre i consumi di carburante di circa il 2-3%. Dal punto di vista del design del veicolo, tuttavia, una riduzione di 45 chilogrammi in una determinata area apre la strada a un’ulteriore riduzione del peso in altri componenti e sistemi, innescando così una spirale virtuosa. Un veicolo con scocca nuda interamente realizzata in composito potrebbe pesare il 50-70% in meno rispetto a un altro con scocca nuda in acciaio, con un guadagno netto di circa 113 chilogrammi. Inoltre, la spirale virtuosa consentirebbe agli ingegneri di ridurre le dimensioni di motore, trasmissione, freni, sospensioni, batterie e altro ancora, con un’ulteriore riduzione potenziale di 227 chilogrammi.
Benché i CFRP promettano risparmi significativi in termini di peso, vi sono fattori concorrenti che limitano il loro potenziale utilizzo nei veicoli. In primo luogo, il costo. Produrre i CFRP infatti costa 10 volte di più rispetto all’alluminio e al magnesio, ed è persino più oneroso dell’acciaio e delle materie plastiche rinforzate con fibre di vetro più avanzate e ad alta resistenza. Un aspetto altrettanto problematico è la produttività. Nonostante la recente introduzione di resine termoindurenti a vulcanizzazione rapida, di tecniche di lavorazione meno costose senza autoclave e matrici termoplastiche che consentono di abbattere i tempi di ciclo da oltre otto ore a circa 10 minuti, i tempi di ciclo limitano ancora l’impiego dei CFRP nei modelli prodotti in volumi pari o inferiori a 40.000 unità all’anno.
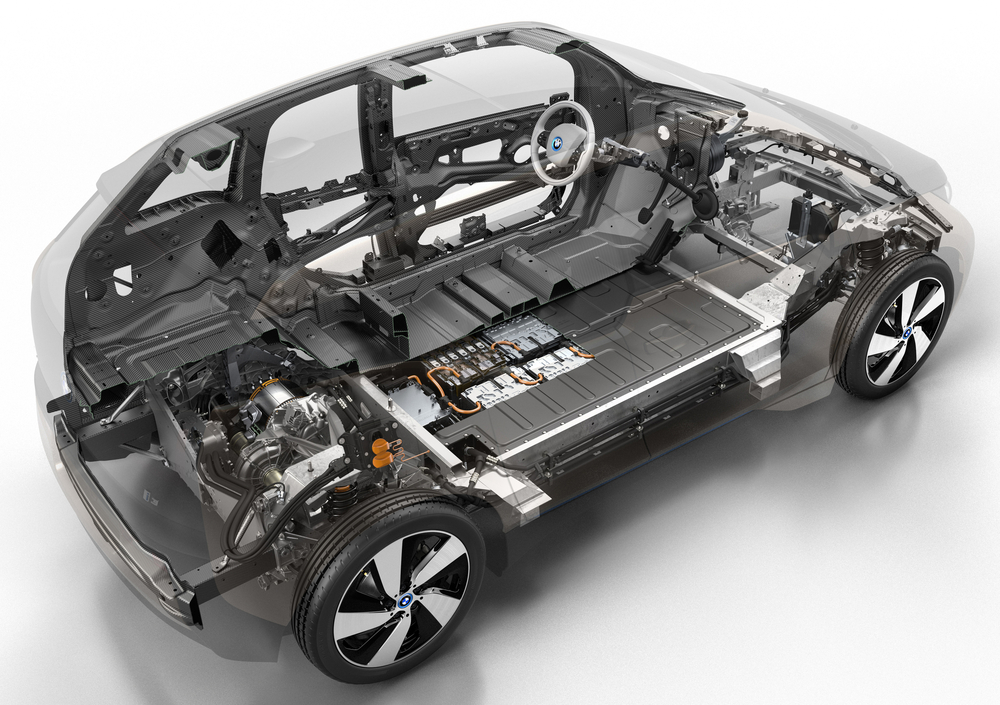
Il fine vita
Un altro fattore importante è rappresentato dalle normative sullo smaltimento a fine vita. I metalli sono facilmente riciclabili, ma non si può ancora dire lo stesso dei CFRP. Ciò determina un maggiore costo relativo dei materiali, costi di smaltimento in discarica, nonché la possibilità di incorrere in ulteriori sanzioni in alcuni luoghi. Inoltre, le tempistiche, i costi e la disponibilità limitata dei servizi di manutenzione dei CFRP pongono ulteriori ostacoli, così come i tassi di assicurazione più elevati. Alla luce di queste problematiche, i costruttori hanno optato per soluzioni meno rischiose e costose e continueranno su questa strada, a meno che non subentrino considerazioni legate ai fattori economici e al prestigio del marchio. La produzione di automobili che rispettino le normative in materia di consumi di carburante (CAFE) e di emissioni richiederà l’adozione di tutte le strategie precedentemente menzionate, con una serie di vantaggi per i CFRP. Acciaio, alluminio e magnesio avanzati ad alta resistenza rappresentano soluzioni valide per la maggior parte dei veicoli lanciati sul mercato. Tuttavia, nell’inflessibile mondo delle auto di lusso, si avverte sempre più la necessità di ridurre la massa, con costi aggiuntivi legati alle strategie di riduzione del peso più facilmente assorbibili. Proprio in questo mercato, quindi, i CFRP trovano le opportunità più interessanti.
Il mercato del veicolo e i CFRP
La discussione in merito all’incremento dell’efficienza dei veicoli, le opportunità in termini di materiali e gli ostacoli lungo questo percorso suggerisce che, nei prossimi 10-15 anni, le fibre di carbonio non saranno presenti in tutte le automobili. L’impiego nei veicoli è limitato da tempi e costi di trasformazione, con maggiori opportunità nelle applicazioni destinate ai modelli prodotti in volumi annui inferiori a 40.000 unità e venduti a un prezzo superiore a 50.000 euro, tranne la BMW i3 che rappresenta un’eccezione rispetto a queste indicazioni generali. Tenendo presente queste considerazioni, è ora possibile dare un’occhiata al mercato di questi tipologie di veicoli.
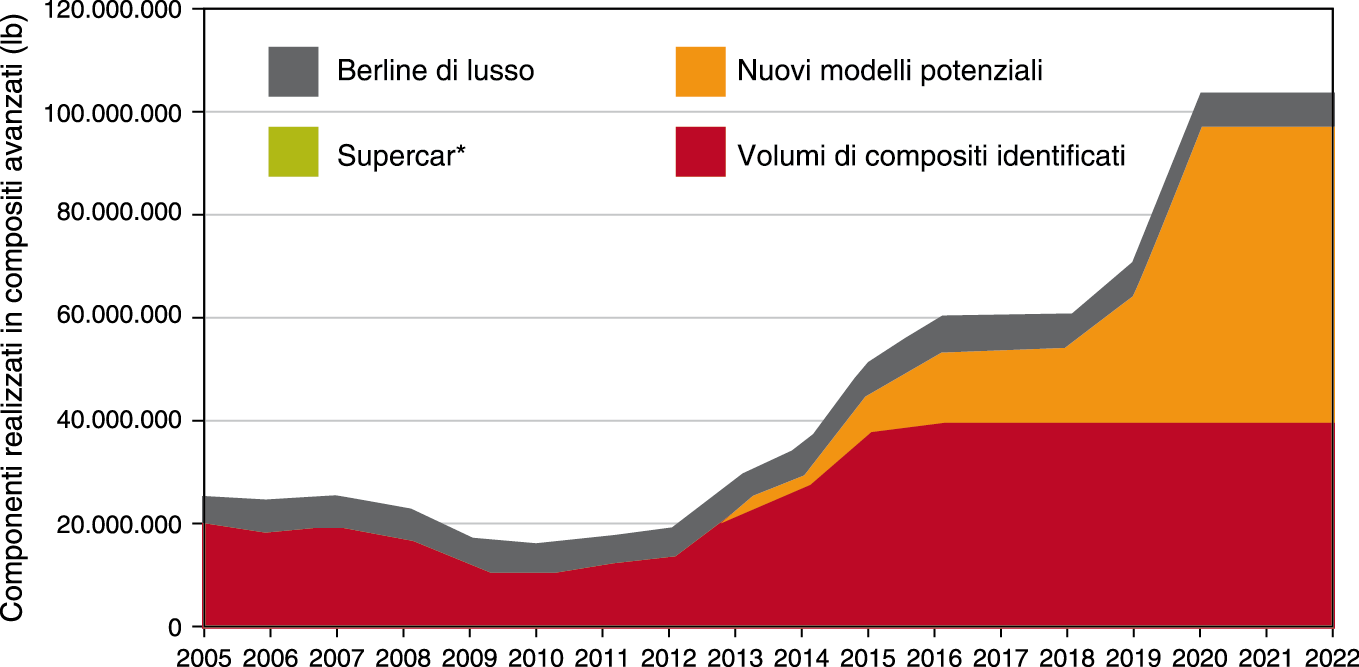
*Le supercar, meno di 1/10 dell’1% totale, non sono visibili nel grafico
Fonte Composites Forecasts and Consulting (luglio 2013)
La produzione globale di autovetture e autocarri leggeri ammonta attualmente a circa 63 milioni di unità all’anno. Di questo totale, le auto di lusso rappresentano approssimativamente il 9%. Questi 6 milioni si suddividono in 210 modelli, ampiamente diversificati per quanto concerne lo stile e configurazione della carrozzeria, comprese le coupé e le berline, autovetture di medie e grandi dimensioni, autocarri di lusso, SUV e crossover. Sorprendentemente, circa 100 modelli tra quelli appena realizzati o solamente previsti utilizzano i CFRP, quasi il quadruplo rispetto a 10 anni fa.
Sulla base delle informazioni relative a questi veicoli, nonché su alcune autovetture sportive e SUV disponibili a prezzi moderati che impiegheranno i CFRP, si stima che il peso totale dei componenti in CFRP passerà da 7.486 tonnellate nel 2013 a 16.334 tonnellate nel 2016. Calcolando nei CFRP le applicazioni che gli OEM del comparto automotive hanno annunciato per i prossimi tre anni (“volumi di compositi identificati”) o anticipato, nonché i “potenziali nuovi modelli” previsti per i prossimi sette anni e un piccolo numero di “supercar” e “berline di lusso” escluse da questa analisi, il grafico SOPRA evidenzia come entro il 2022 il peso totale dei compositi al carbonio utilizzati ogni anno per i veicoli potrebbe superare le 454.000 tonnellate. Ciò significa che la produzione di CFRP è destinata a crescere significativamente, incrementando inoltre le opportunità di espansione per gli altri compositi e metalli leggeri.
Per supportare la produzione di 454.000 tonnellate di componenti finiti in CFRP, la catena delle forniture del comparto automotive necessiterà di 39,225 Mt di fibre di carbonio grezze. Oggi l’industria automobilistica (comprese le scuderie delle auto da corsa e i fornitori di accessori aftermarket) assorbe circa il 3,5% della capacità globale di produzione di fibre di carbonio. Secondo questa tendenza, tale cifra potrebbe crescere fino a sfiorare il 25% entro il 2022.
Chi trainerà la crescita dei CFRP?
Considerato il numero di aziende che cercano di espandere la loro attuale attività nel campo dei compositi o che stanno pianificando il loro ingresso, non è sufficiente testimoniare l’incremento dei volumi. È piuttosto importante capire quali applicazioni stanno trainando questa crescita. Composites Forecasts and Consulting (Mesa, Arizona) ha recentemente pubblicato uno studio di mercato che elenca nel dettaglio le attività connesse all’interno della catena delle forniture. Sulla base dei dati pubblicati, si calcola che nel 2013 sono stati fabbricati e forniti ai costruttori circa 2,25 milioni di singoli componenti in composito. La produzione di tali componenti avviene in 35 aziende in tutto il mondo, con il 70% circa del volume complessivo originato in Europa. Componenti in composito sono presenti in quasi tutte le parti strutturali del veicolo, tra cui:
• componenti dello chassis;
• pannelli e accessori esterni;
• elementi interni strutturali ed estetici;
• sospensioni;
• trasmissione, impianto di scarico ed elementi decorativi nel vano motore;
• impianto frenante;
• sistema di alimentazione;
• pneumatici e altri componenti.
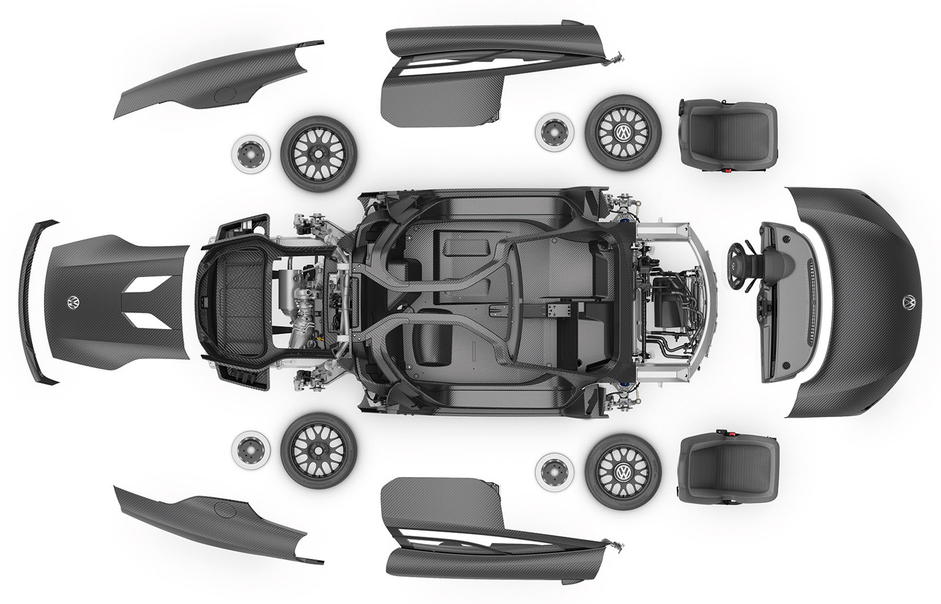
I fornitori che realizzano componenti per chassis, pannelli, dischi del freno e trasmissione sono attualmente i maggiori consumatori di CFRP e continueranno a trainare la crescita nel periodo di riferimento. Combinati tra loro, questi componenti rappresentano l’87% dei volumi dei compositi identificati e il 95% del peso identificato del materiale fornito. Tuttavia, come si evince dal rapporto stilato da Composites Forecasts and Consulting, gli attuali miglioramenti in termini di trasmissione, aerodinamica e riduzione del peso non sono sufficienti a raggiungere gli obiettivi sulle emissioni fissati per il 2025, aprendo così la strada ad alcune applicazioni precedentemente elencate.
L’anno scorso, per esempio, ruote in fibra di carbonio sono state montate per la prima volta su auto sportive di fascia alta, come la Koenigsegg Agera e la più accessibile Jaguar F-Type. I sedili realizzati in materiali compositi rappresentano un’altra applicazione con un notevole potenziale, mentre i componenti per le sospensioni costituiscono un obiettivo a breve termine, incluse balestre e molle. Inoltre, altri componenti delle sospensioni, tra cui barre antirollio, bracci e telai, potrebbero beneficiare delle odierne tecniche di lavorazione, come per esempio l’avvolgimento filamentare e lo stampaggio a trasferimento di resina (RTM), che consentono di ridurre di due terzi il peso di questi componenti rispetto alle attuali versioni metalliche. L’utilizzo di questi componenti innovativi da parte dei costruttori è destinato a crescere del 600% circa nel periodo preso in esame, con ulteriori opportunità per i fornitori dell’aftermarket.
Il futuro dei CFRP
Come si intuisce da questa previsione, numerosi fattori hanno esercitato un impatto significativo sui motivi e le modalità con cui i compositi in fibra di carbonio siano penetrati nell’industria automobilistica, determinando l’esito futuro di questa avanzata. Ovviamente, l’industria dei compositi dovrà superare alcune sfide se vuole essere competitiva in questo mercato. Prime fra tutte, le questioni legate ai costi e alla scalabilità. Nei prossimi anni, sarà possibile osservare alcuni esempi significativi di strutture importanti in composito nelle automobili prodotte su larga scala. L’impatto esercitato dai modelli prodotti in serie relativamente piccole influirà in modo sensibile ma circoscritto sulla domanda di beni e servizi legati ai CFRP.
Nel nostro decennio, solo un numero limitato di automobili di lusso e sportive si getteranno nella mischia, esercitando un impatto proporzionalmente importante sulla catena delle forniture dei compositi avanzati.
Alla luce delle precedenti considerazioni, probabilmente è troppo presto per affermare che i CFRP sostituiranno i materiali tradizionali nelle automobili come è già avvenuto nell’industria aerospaziale, tuttavia è lecito affermare che tutti gli indizi puntino in quella direzione. Come già osservato in precedenza, vi sono ancora quasi due cicli completi di design da oggi al 2025. Pertanto, le case automobilistiche e la catena delle forniture di materiali compositi hanno a disposizione molto tempo per elaborare delle soluzioni congiunte con l’obiettivo di sfruttare al meglio questa opportunità.
Ogni anno, le norme CAFE recentemente riviste per ciascuna categoria di veicolo tendono a inasprirsi, aumentando la pressione sulle case automobilistiche affinché producano veicoli conformi agli standard, in caso contrario i clienti saranno costretti a pagare imposte elevate sui veicoli meno efficienti dal punto di vista dei consumi di carburante.