Il flusso laminare e il flusso a fontana influenzano la qualità superficiale dei componenti e consentono lo stampaggio di parti cave e la coiniezione di materiali diversi.
di Giovanni Lucchetta, Università di Padova
“Panta rei”, tutto scorre, diceva il filosofo greco Eraclito, sottolineando il carattere mutevole e dinamico della realtà. Questo concetto trova una perfetta applicazione nel mondo delle materie plastiche, dove il flusso dei polimeri allo stato fuso è un fenomeno talmente complesso da essere oggetto di studio di una branca della fisica: la reologia.
Comprendere come la plastica fusa si muove a contatto con le attrezzature di produzione, come matrici di estrusione, stampi a iniezione e sistemi a canali caldi, è di cruciale importanza per ottimizzare i processi e garantire la qualità dei prodotti finali. Il flusso della plastica fusa, infatti, influenza direttamente caratteristiche come la finitura superficiale, la distribuzione del materiale e la formazione di eventuali difetti.
Flusso laminare, turbolento e transitorio
Prendiamo innanzitutto in considerazione un flusso isotermo, in cui la temperatura è uniforme in ogni punto del fluido: a contatto con la parete del condotto, così come al centro dello stesso. Questa situazione è rappresentativa delle condizioni che ritroviamo nel passaggio attraverso una matrice di estrusione e nei sistemi a canali caldi di uno stampo a iniezione.
Secondo la fluidodinamica, il comportamento dei fluidi all’interno dei condotti può essere classificato in tre regimi principali: laminare, turbolento e transitorio. La comprensione di quale tra questi regimi caratterizzi ciascun specifico processo di lavorazione è fondamentale per interpretare diversi fenomeni, quali ad esempio la miscelazione, lo scambio termico e l’inglobamento d’aria.
Il flusso laminare, illustrato in figura 1a, è caratterizzato da strati di fluido (lamine) che scorrono parallelamente l’uno all’altro, senza mescolarsi. In questo regime, il fluido si muove in modo ordinato, con velocità maggiori al centro del condotto e minori vicino alle pareti. In molti casi si può assumere che la velocità del fluido a contatto con la parete sia nulla o, in altre parole, che non ci sia slittamento. Questo tipo di flusso è tipico dei fluidi viscosi a basse velocità e in condotti di ristretti, come ad esempio i polimeri allo stato fuso che fluiscono nelle matrici di estrusione.
Il flusso turbolento, visibile nella figura 1b, presenta invece un comportamento caotico. Le particelle di fluido si muovono in modo irregolare, con fluttuazioni di velocità sia parallele che perpendicolari alla direzione principale del flusso. Questo regime si verifica generalmente con fluidi meno viscosi (ad es. acqua), a velocità più elevate o in condotti con sezione più ampia.
Tra questi due estremi si colloca il flusso transitorio, una condizione intermedia che presenta caratteristiche di entrambi i regimi precedenti. La transizione da laminare a turbolento può verificarsi in funzione di vari parametri, come la velocità del flusso, la viscosità del fluido e la geometria del condotto. Questi fattori sono sintetizzati in un parametro adimensionale fondamentale nella fluidodinamica: il numero di Reynolds (Re). Questo parametro mette in relazione le forze inerziali e le forze viscose agenti sul fluido ed è definito come:
dove ρ è la densità del fluido, v è la velocità media del flusso, D è il diametro della sezione del condotto (o una sua dimensione caratteristica) e η è la viscosità del fluido. Valori bassi del numero di Reynolds (tipicamente Re < 2300) indicano un regime laminare, mentre valori elevati (Re > 4000) sono associati a un flusso turbolento. La zona intermedia (2300 < Re < 4000) corrisponde al regime di transizione.
Il calcolo del numero di Reynolds è abbastanza semplice e permette di capire, ad esempio, come un polimero fuso fluisca all’interno di uno stampo a iniezione. Proviamo a calcolarlo utilizzando valori tipici. Un polimero termoplastico fuso ha una densità nell’ordine di 1 g/cm³ e scorre in una cavità spessa circa 1-3 mm. La viscosità del fuso varia tra i 10 e i 1000 Pa·s a seconda del polimero e della velocità d’iniezione, che possiamo stimare dividendo gli ordini di grandezza della lunghezza tipica di un pezzo (10 cm) per il tempo di riempimento (1 s), ottenendo circa 0,1 m/s.
Inserendo questi valori nella formula del numero di Reynolds, otterremo un risultato che per alcuni potrà essere sorprendente: Re varia tra 0,01 e 0,0001 ed è di gran lunga inferiore alla soglia di 2300. In altre parole, il flusso di riempimento nello stampaggio a iniezione è invariabilmente laminare. Pensateci la prossima volta che qualcuno vi parla erroneamente di vorticosità. Nello stampaggio a iniezione, il flusso di riempimento è laminare e, a maggior ragione, lo è il flusso in una matrice di estrusione, dato che la viscosità è in genere più elevata e la velocità molto più bassa.
Flusso a fontana
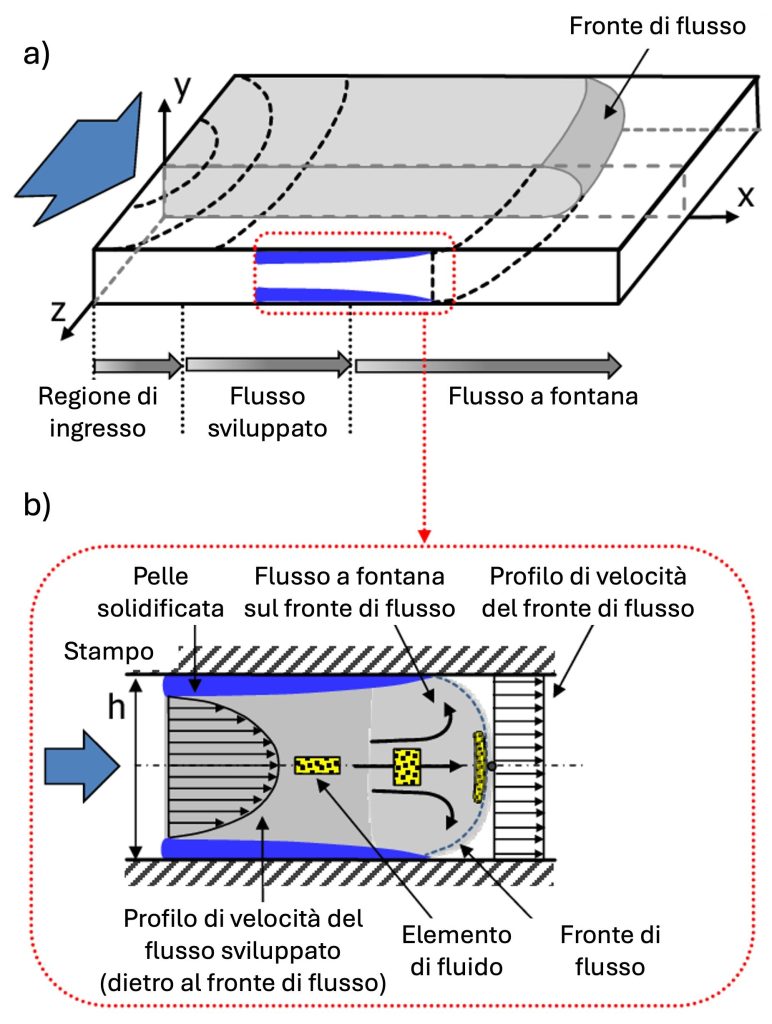
Il riempimento di uno stampo durante il processo di iniezione è caratterizzato da un flusso non isotermo, come illustrato in figura 2a. Al centro della sezione, il fuso polimerico mantiene una temperatura elevata, ma questa diminuisce progressivamente avvicinandosi alle pareti dello stampo. A una certa distanza dalle pareti, la temperatura scende al di sotto del punto di cristallizzazione (o di transizione vetrosa per i polimeri amorfi), causando la solidificazione del polimero e la formazione di uno strato chiamato “pelle” (skin). Questo strato solidificato restringe la sezione di flusso e modifica il profilo di velocità, particolarmente evidente in prossimità del fronte di flusso.
In questa zona, si osserva una divergenza del flusso dovuta al passaggio dalla sezione ristretta, limitata dalla pelle, a quella più ampia dello stampo (vedi figura 2b). Questo fenomeno provoca un cambio di direzione delle molecole del polimero: dal cuore del flusso, dove la temperatura è più alta e il materiale è ancora fuso, si spostano verso la pelle, dove si arrestano solidificandosi. Il processo continua con l’arrivo di nuovo polimero fuso che, transitando nel cuore del pezzo, raggiunge il fronte e va a formare nuova pelle. Questo meccanismo, noto come flusso a fontana, è chiaramente visibile nell’ingrandimento di figura 2b, dove si può apprezzare il profilo di velocità caratteristico e il movimento del materiale dal centro verso le pareti dello stampo.
Questo spostamento laterale del polimero che raggiunge il fronte di flusso ha importanti implicazioni in termini di qualità superficiale del componente stampato. Infatti, può portare alla formazione di difetti noti come “sfiammature”, che si manifestano come striature lucide sulla superficie del pezzo. Queste imperfezioni sono causate dalla presenza di sostanze volatili nel fuso polimerico, che possono derivare dall’umidità residua nel materiale, dalla degradazione di additivi o del polimero stesso, o da gas iniettati nel cilindro per “schiumare” la plastica (nello stampaggio microcellulare, noto anche come MuCell).
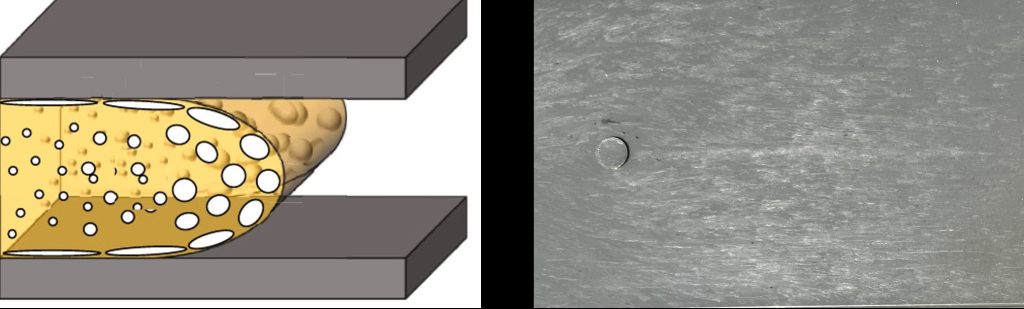
In prossimità del fronte di flusso, la pressione diminuisce e le sostanze volatili, che erano in soluzione nel polimero, fuoriescono formando numerose bolle che il flusso a fontana allunga e porta sulla pelle (figura 3). Molte di queste bolle possono rimanere intrappolate tra la superficie dello stampo e il fuso plastico, impedendo al polimero di aderire perfettamente e replicare la finitura della superficie della cavità, creando aree dall’apparenza lucida o argentea sul pezzo finale.
Il flusso a fontana determina una distribuzione specifica della plastica nel pezzo finale, come illustrato in figura 4. Questo fenomeno può essere compreso visualizzando il fuso plastico nel cilindro d’iniezione come suddiviso in quattro sezioni colorate rispettivamente di rosso, grigio, giallo e nero.
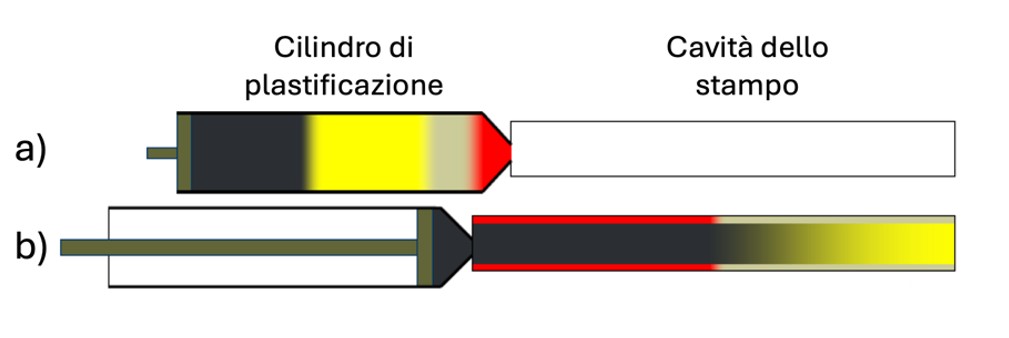
Durante la fase di riempimento, la plastica entra nello stampo a una velocità relativamente alta. Le sezioni rossa e grigia, che sono le più vicine all’ugello, sono le prime a entrare nello stampo e vanno a formare la pelle del componente stampato. Questo significa che la superficie del pezzo è sempre costituita dal materiale che fluisce per primo all’interno della cavità.
Man mano che il riempimento procede, le sezioni successive (grigia, gialla e nera) entrano nello stampo, con le sezioni più interne (gialla e nera) che rimangono nel cuore del componente. La fase di compattazione e mantenimento, che segue il riempimento, serve a compensare il ritiro che avviene dopo la fase di iniezione. Durante questa fase, il materiale aggiunto proviene principalmente dalla sezione nera, che entra in cavità per ultima.
Questa distribuzione del materiale, causata dal flusso a fontana, ha importanti implicazioni tecnologiche. Consente infatti di realizzare componenti cavi, o con una suddivisione di diversi materiali tra pelle e cuore.
Varianti tecnologiche basate sul flusso a fontana
Lo stampaggio a iniezione assistito da gas (GAIM) è una tecnologia innovativa che sfrutta il principio del flusso a fontana per creare componenti cavi con caratteristiche uniche. Il processo si basa su due principi fondamentali.
Il primo principio prevede il riempimento parziale dello stampo con polimero fuso (figura 5a), seguito dall’iniezione di un gas inerte (tipicamente azoto) nel cuore del fuso (figura 5b). Il gas, seguendo il percorso di minor resistenza, si dirige verso il fronte di flusso dove la pressione è più bassa. Questo crea una rete di canali cavi nelle sezioni più spesse del pezzo, spostando il polimero fuso ancora caldo verso le pareti dello stampo, per completare il riempimento e la compattazione della cavità.
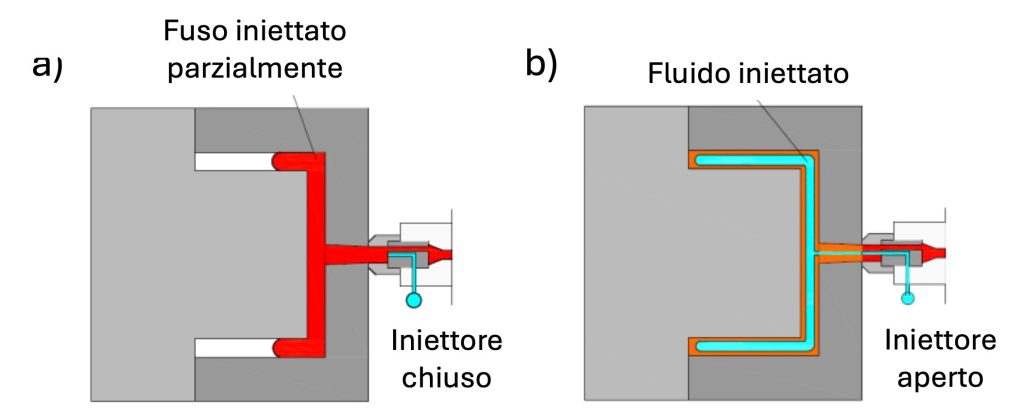
Il secondo principio prevede invece il riempimento quasi completo o totale della cavità, seguito dall’evacuazione del cuore fuso in una cavità secondaria. Questa può essere una cavità laterale da scartare dopo lo stampaggio, una cavità che formerà un pezzo aggiuntivo, o il cilindro di plastificazione della pressa, dove il materiale verrà riutilizzato nel ciclo successivo.
La figura 5 illustra chiaramente il primo principio, mostrando come il gas iniettato crei una bolla all’interno del polimero parzialmente iniettato, spingendolo contro le pareti dello stampo. È importante notare che il GAIM fa parte di una categoria più ampia di tecnologie di stampaggio assistito da fluidi. Un’altra variante è lo stampaggio assistito da acqua, che sfrutta l’incomprimibilità e l’alta capacità termica dell’acqua per ridurre significativamente i tempi di ciclo. Le tecnologie di stampaggio assistito da fluidi offrono numerosi vantaggi, tra cui la riduzione del peso dei componenti, il miglioramento della stabilità dimensionale, la riduzione dei tempi di ciclo, il miglioramento della qualità superficiale e la riduzione della forza di chiusura richiesta.
Il flusso a fontana è anche il principio chiave che permette la coiniezione di due materiali diversi in un unico componente: uno sulla pelle (skin) e l’altro nel cuore (core). Questo processo, noto anche come stampaggio sandwich, è una tecnica avanzata di stampaggio multicomponente che utilizza lo stesso sistema di gate e runner per entrambi i materiali. Il processo prevede tipicamente che i due materiali vengano iniettati in sequenza, sfruttando una macchina con due unità d’iniezione separate e controllabili individualmente, collegate a un blocco ugello comune con una testa di commutazione.
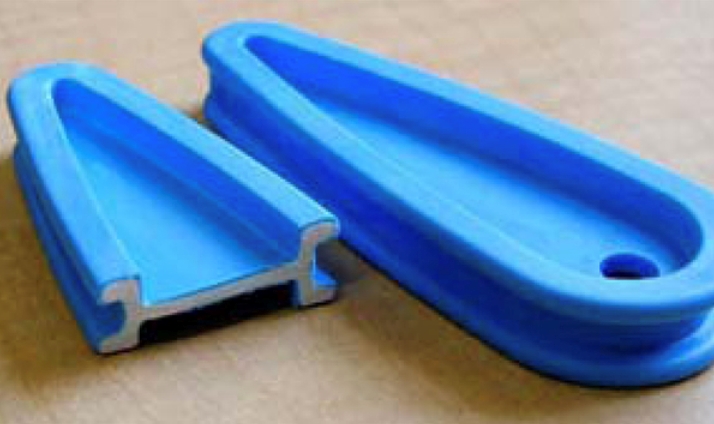
Durante l’iniezione, il comportamento di flusso dei polimeri fusi e la solidificazione del materiale della pelle creano uno strato congelato che cresce dalle pareti fredde dello stampo verso l’interno. Il polimero al centro della cavità rimane fuso. Quando viene iniettato il materiale del cuore, questo fluisce all’interno degli strati congelati della pelle, spingendo il materiale della pelle ancora fuso verso le estremità della cavità. Grazie all’effetto del flusso a fontana sul fronte di avanzamento del fuso, il materiale della pelle al fronte di flusso si deposita nella regione adiacente alle pareti dello stampo (figura 6).
Questa tecnologia offre notevoli vantaggi in termini di design e funzionalità dei pezzi, permettendo di combinare le proprietà di materiali diversi in un unico componente, ottimizzando così le prestazioni e l’estetica del prodotto finale.
(Articolo tratto dalla rivista Plastix di marzo 2025)