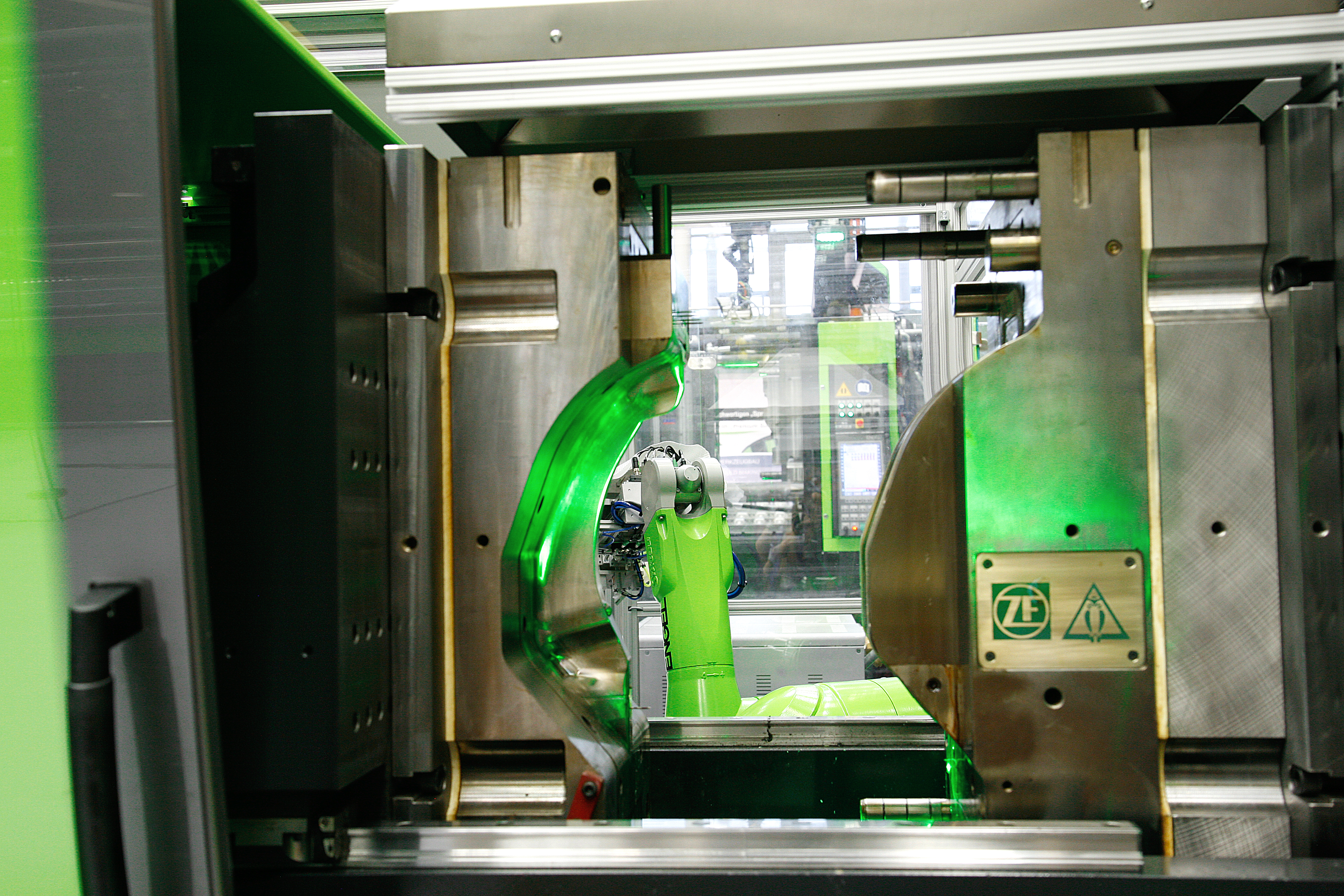
«Leggerezza. È questo il tema che ogni giorno deve affrontare uno stampatore che opera nel settore dell’automobile. Non c’è dunque da meravigliarsi se i produttori di macchine e di polimeri che intendono porsi come trendsetter puntino sul perfezionamento continuo di materiali e tecnologie, soprattutto in riferimento a componenti che dovranno sopportare carichi meccanici elevati» ha detto a Plastix Peter Egger, direttore del Centro tecnologico per i compositi leggeri di Engel Austria. L’abbiamo incontrato a Linz (Austria) in occasione del Simposio 2012 dove, tra i tanti dedicati al comparto del veicolo, è stato presentato un progetto ad alto contenuto innovativo: la polimerizzazione nello stampo. Egger ci ha illustrato i vantaggi di della tecnologia.
La polimerizzazione nello stampo
L’obiettivo, quindi, è lightweight o – con locuzione italiana – struttura leggera. Ma cosa significa? «Si parla di struttura leggera – spiega Peter Egger – quando si dispone nello spazio la minore quantità possibile di materia in modo tale da elevare le sue prestazioni al massimo livello raggiungibile». Per riuscire a far questo è necessario trovare un materiale in grado di offrire proprietà meccaniche eccellenti anche quando vengono realizzati i manufatti più leggeri. L’esperienza dimostra che le migliori prestazioni nascono dalla combinazione di materie prime diverse: perlopiù fibre di vetro o di carbonio ad alta resistenza, integrate in una matrice termoindurente o termoplastica. I materiali così ottenuti – i compositi – vengono impiegati in ambiti altamente tecnologici (per esempio, velivoli e auto da competizione), in cui spesso i lotti di produzione consistono in un unico pezzo. In questi casi, molte volte, i compositi fibrorinforzati termoindurenti vengono laminati manualmente in componenti piani, che vengono poi riscaldati in grandi forni e infine sottoposti a operazioni di post-lavorazione, taglio e assemblaggio. Insomma, un processo che richiede tempi di ciclo di ore».
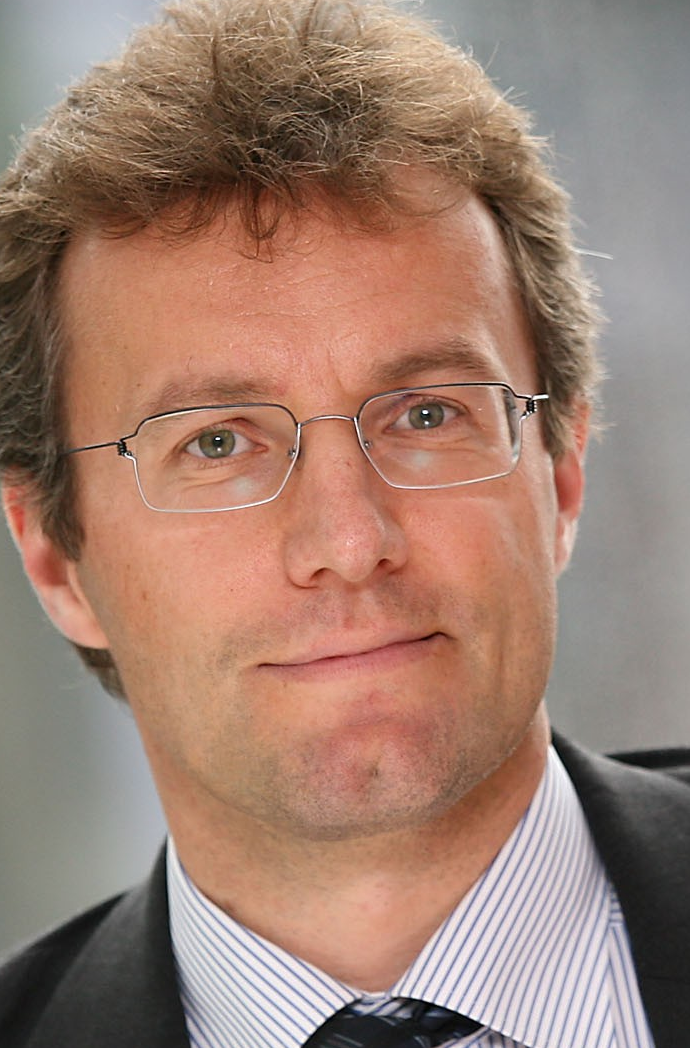
Peter Egger
Tempi incompatibili con la produzione di scala. La sfida è dunque ottimizzare una tecnologia completamente automatizzata, che permetta di produrre un pezzo finito in una sola stampata. «Qualche anno fa – continua Peter Egger – abbiamo sviluppato un processo per la trasformazione di una foglia organica nel supporto per la colonna dello sterzo, combinando la termoformatura con lo stampaggio a iniezione. Oggi, visto il risultato positivo dell’applicazione, stiamo lavorando alla produzione del pedale del freno utilizzando, anche in questo caso, una foglia organica come elemento di rinforzo. Ma fin qui niente di nuovo. La novità è la combinazione di tale tecnologia con la polimerizzazione della poliammide 6 (PA6) direttamente nello stampo. I vantaggi sono considerevoli: accanto a quello più immediato legato alla riduzione del peso del componente (che in questo caso arriva al 50% rispetto all’acciaio), ne troviamo un altro, forse ancora più sostanziale, cioè l’eccellente impronta energetica del processo. Infatti, le temperature e le pressioni necessarie per la polimerizzazione del caprolattame – la base della PA6 – nello stampo sono inferiori a quelle richieste dalla lavorazione della PA6. Inoltre, la temperatura massima raggiunta nello stampo durante la polimerizzazione è di 170 °C, e quindi ben al di sotto delle consuete temperature di trasformazione della PA6».
Quando la viscosità è un problema
A fronte della promessa di vantaggi consistenti, l’ottimizzazione del nuovo processo richiede la soluzione di non poche criticità. «Le foglie organiche, seppure siano un ottimo rinforzo e totalmente controllabili in un processo su scala industriale, possono presentare qualche problema in fase di impregnazione, perché quanto si utilizzano i termoplastici bisogna fare i conti con la viscosità – spiega Peter Egger –. Immaginate di inserire un materiale tessile in una matrice estremamente viscosa: non ci riuscirete mai. Riuscirete al massimo a retrostampare il tessuto, e per questa operazione, infatti, sono disponibili sistemi ben consolidati. Per infiltrare le strutture fibrose all’interno dello stampo di iniezione è necessario utilizzare materiali molto fluidi, caratterizzati da una viscosità simile a quella dell’olio per motori: per esempio, le resine epossidiche, ovvero sistemi termoindurenti. Se si desidera restare nel dominio dei termoplastici l’imperativo è cambiare l’approccio. Noi abbiamo deciso di utilizzare l’ε-caprolattame, dal momento che ha proprietà di scorrimento eccellenti. La sua viscosità estremamente ridotta consente di arrivare anche ai filamenti fibrosi più fini senza provocare danni: ciò apre le porte alla fabbricazione di strutture fibrose su misura, concepite in base al carico che la struttura dovrà sopportare. La viscosità relativamente elevata della PA6 renderebbe invece impossibile tanto il riempimento dello stampo quanto l’infiltrazione del tessile. Nel progetto presentato al Simposio, in virtù dell’elevato livello di formatura dell’inserto, abbiamo utilizzato un tessuto di vetro con buone caratteristiche di drappeggio. È stato quindi utilizzato un tessuto 2/2 con un peso di 280 g/m², la cui finezza delle maglie non ha ostacolato in alcun modo lo scorrimento del caprolattame».
[note color=”#FFCC00″]Meccanismo della polimerizzazione nello stampoL’ε-caprolattame – la base della poliammide 6 – viene alimentato sotto forma di granuli duri mediante due unità di iniezione allo stampo pre-riscaldato: la prima unità inietta caprolattame miscelato con un catalizzatore (sale metallico), mentre la seconda inietta una miscela di caprolattame e attivatore (diisocianato). Questo processo di polimerizzazione “anionica” richiede una temperatura massima di 170 °C, una caratteristica che aumenta l’efficienza energetica del processo. Va inoltre ricordato che il processo diretto rende superflua la fase di polimerizzazione in sede di produzione della materia prima. Contrariamente a quanto accade nel caso della polimerizzazione anionica nello stampo, la PA6 normalmente disponibile sul mercato viene prodotta tramite polimerizzazione idrolitica, un processo che richiede temperature comprese tra 240 e 270 °C, e tempi di attesa compresi fra le 12 e le 24 ore per il caprolattame. Una delle sfide più difficili da affrontare quando si lavorano i materiali a bassa viscosità, come il caprolattame, consiste nel garantire l’ermeticità dello stampo: la testa di miscelazione deve essere regolata in maniera adeguata e l’impronta dello stampo deve essere riscaldata.[/note]
Le fasi del processo
Sebbene progettato in ogni sua fase, il processo richiede ancora la messa a punto di numerosi dettagli prima di arrivare all’industrializzazione. Al Simposio Engel 2012, dove è stato presentato in anteprima, abbiamo visto in realtà solo un prototipo prototipo di sistema per la produzione su scala ridotta e un abbozzo del processo, articolato in un numero limitato di fasi. «La prima di queste – illustra Peter Egger – prevede che il tessuto tagliato a misura venga prelevato da un robot lineare con pinze ad ago, che lo trasferisce a una stazione per l’applicazione a spruzzo del legante e, successivamente, alla stazione di posizionamento. Giunti all’ultima stazione, i singoli strati di tessuto vengono posizionati su uno strato centrale riscaldato, fino a ottenere una preforma multistrato. Un robot multiasse, quindi, preleva la preforma e la posiziona nello stampo riscaldato predisposto per il processo di stampaggio a iniezione reattiva. Quando lo stampo si chiude comincia l’iniezione della miscela reattiva di caprolattame, e quindi la polimerizzazione al termine della quale il manufatto viene rimosso dallo stampo. Per asportare il materiale in eccesso sul contorno del componente finito è possibile utilizzare una taglierina laser CO2».
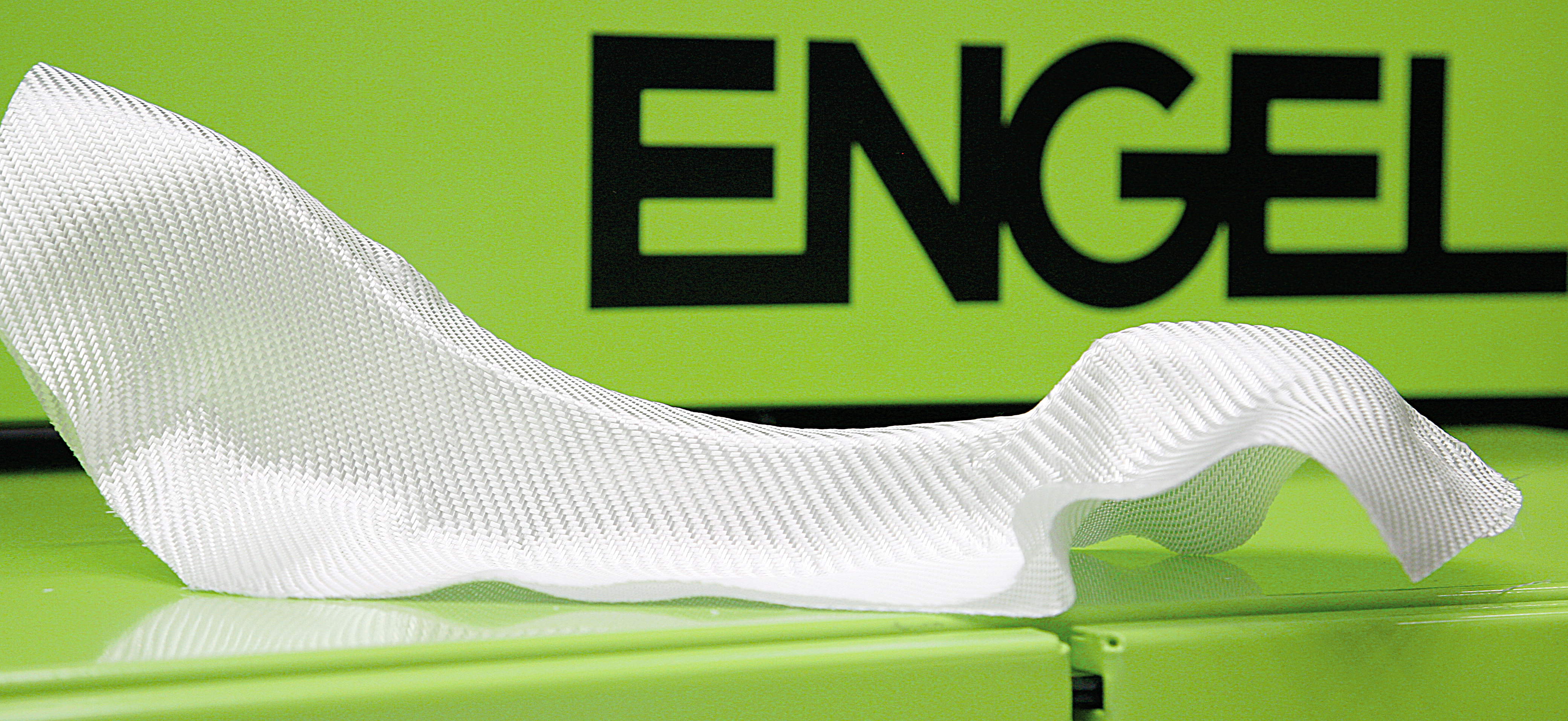
Le foglie organiche, grazie alle loro proprietà anisotrope (ovvero caratteristiche meccaniche identiche in tutte le direzioni), sono un rinforzo eccellente. Tuttavia, le strutture leggere – secondo la definizione fornita in precedenza – presuppongono l’utilizzo di un elemento di rinforzo soltanto laddove è necessario. «In realtà, quindi, una struttura leggera in senso stretto può essere ottenuta soltanto impiegando materiali con proprietà anisotrope – continua Peter Egger –. Questo significa che per la produzione di pedali del freno pronti per l’assemblaggio è necessario un passaggio ulteriore: gli inserti devono essere trasferiti in uno stampo per lo stampaggio a iniezione tradizionale, nel quale vengono realizzate nervature e altri elementi funzionali in poliammide rinforzata con fibre di vetro. Questa fase può essere integrata nella cella di produzione, in maniera tale da consentire la realizzazione, in un unico ciclo, di un componente termoplastico costituito da tessuto asciutto e ε-caprolattame rinforzato con fibre lunghe».
Elettrica e bi-iniettore
Fino a qualche anno fa, i processi nello stampo venivano eseguiti mediante sistemi speciali e presse per colata a reazione. «Nonostante questo, da sempre, il nostro obiettivo è quello di utilizzare, per quanto possibile, tecnologie di processo standard al fine di abbattere i costi legati alla produzione di componenti fibrorinforzati – incalza Egger –. Per questo, per il prototipo presentato durante il Simposio abbiamo deciso di utilizzare una pressa a iniezione Engel e-victory 120 combi standard, dotata di due unità di iniezione elettriche inclinate di 30° rispetto al piano orizzontale, modifica dettata dalla viscosità estremamente bassa del caprolattame. Questa soluzione si distingue dalle macchine bi-iniezione tradizionali per le unità di iniezione inclinate e per la combinazione dei canali in un’unica testa di miscelazione prima della fase di iniezione».
La riproducibilità della miscela delle due componenti a base di caprolattame, essenziale ai fini della polimerizzazione, viene garantita dall’elevata precisione delle unità di iniezione elettriche. Il ricircolo dei due componenti tra il recipiente di alimentazione del materiale e la testa di miscelazione risulta pertanto superfluo. In questo modo, diventa possibile ridurre al minimo il tempo di attesa del materiale all’interno dell’unità di plastificazione e, di conseguenza, il carico termico.
Le pressioni richieste sono inferiori rispetto a quelle necessarie per lo stampaggio della PA6, perché dipendono dalla viscosità molto bassa del caprolattame plastificato. E questo ha consentito, nonostante le dimensioni relativamente grandi del componente, di ridurre la forza di chiusura della pressa a un quarto del valore nominale. E un contributo in questa direzione è stato dato dal design senza colonne che contraddistingue i modelli Engel victory, in grado di garantire ampio spazio sia per lo stampo che per il robot.
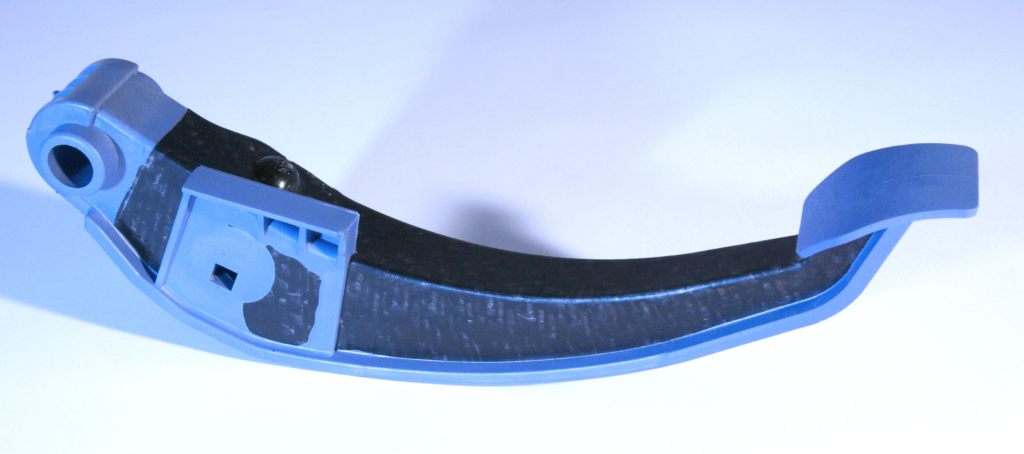
Il controllo del processo
Resta da chiedersi se un processo in apparenza così sofisticato possa essere governato facilmente dallo stampatore. «L’integrazione del sistema di automazione nell’unità di controllo CC 200 installata sulla pressa garantisce una programmazione estremamente rapida e semplice, e operazioni di impostazione assolutamente agevoli – assicura Egger –. L’integrazione della tecnologia di controllo è assicurata anche nel caso in cui il gruppo di iniezione integri le unità di una pressa a iniezione bicomponente standard modificate, o semplicemente un’unità aggiuntiva». In termini di controllo del sistema, la polimerizzazione nello stampo non differisce quindi dalle tradizionali applicazioni multicomponente. Inoltre, sono convinto che ogni trasformatore di silicone liquido o resine termoindurenti conoscerà perfettamente i componenti reattivi.
«Un’altra sfida importante è rappresentata dalla movimentazione del tessuto, che di per sé è instabile dal punto di vista dimensionale; tale operazione richiede infatti pinze adeguate e un controllo dei robot estremamente sensibile. I robot Engel viper ed easix, con i loro movimenti ad alta precisione, rappresentano la soluzione ideale per questa applicazione» sottolinea Egger.
Una variabile da ottimizzare
Come abbiamo già accennato, il processo è ancora in fase di prototipo e numerosi partner (Lanxess per il caprolattame, ZF Friedrichshafen AG per lo stampo, Trumpf Group per la taglierina laser, PD-Interglas Technologies AG per le foglia organica e Fraunhofer ICT per il supporto tecnologico) stanno collaborando alla sua ottimizzazione. Commentando questa fase di work-in-progress Peter Egger sottolinea che «Esistono ancora ampi margini di miglioramento, uno tra questi la durata del ciclo. Il nostro prototipo di sistema ha raggiunto tempi di ciclo di cinque minuti, brevi ma ancora non comparabili a quelli delle applicazioni dello stampaggio a iniezione standard in ambito automobilistico. Comunque, le possibilità del sistema non sono ancora state sfruttate appieno, e il nostro obiettivo, chiaramente, è continuare a migliorare l’efficienza del processo e arrivare a tempi di ciclo economicamente accettabili. E il breve tempo di attesa richiesto dal caprolattame, tra l’altro, è destinato proprio a favorire l’abbattimento dei tempi di ciclo».