Sembrano un prodotto banale, ma le salviettine umidificate riescono facilmente risolvere problemi di disinfezione e detergenza in assenza di acqua. Un vantaggio che la recente emergenza sanitaria ci ha insegnato ad apprezzare e a cui difficilmente riusciremo a rinunciare nonostante le polemiche “plastic free”. I produttori del settore healthcare e dell’imballaggio sono infatti sempre più orientati verso la ricerca e sviluppo di soluzioni green che riguardano sia il tessuto, che oggi punta sul biodegradabile, sia la confezione, che deve essere facilmente riciclabile e soprattutto garantire la perfetta conservazione del contenuto. Da questo punto di vista, la tenuta del coperchio richiudibile gioca un ruolo essenziale nel preservare le salviette umide dall’essiccazione, pertanto deve essere in grado di soddisfare precisi requisiti tecnici che, trattandosi di una commodity, devono conciliarsi inevitabilmente con efficienza produttiva e aspetto economico.
Una linea completamente automatizzata
Una soluzione degna di nota dal punto di vista tecnico e della produttività è stata sviluppata dallo stampista tedesco roth mold + automation di Auma-Weidatal, che ha costruito un’attrezzatura a due piani a 12+12 cavità per lo stampaggio di coperchi richiudibili in polipropilene, da installare su una linea completamente automatizzata. Cuore dell’unità produttiva, che occupa un’area di 100 metri quadrati, è una pressa a iniezione Sumitomo SHI Demag Elexis con forza di chiusura di 580 tonnellate. Il coperchio, incernierato in unico pezzo, viene etichettato direttamente in fase di stampaggio. Un sistema di manipolazione lineare posiziona l’etichetta all’interno dello stampo in una frazione di secondo e, al termine del processo di iniezione, rimuove il pezzo chiudendo contemporaneamente il coperchio per riuscire a ottenere un imballo più compatto. Questa operazione deve avvenire rapidamente, mentre il polipropilene è ancora modellabile. Dopo un’ispezione con visore, che controlla il 100% dei pezzi, 38 coperchi richiudibili vengono impilati e fasciati in unità di imballaggio. Nove di queste unità vengono inserite in sacchetti e, sempre automaticamente, in scatole di cartone.
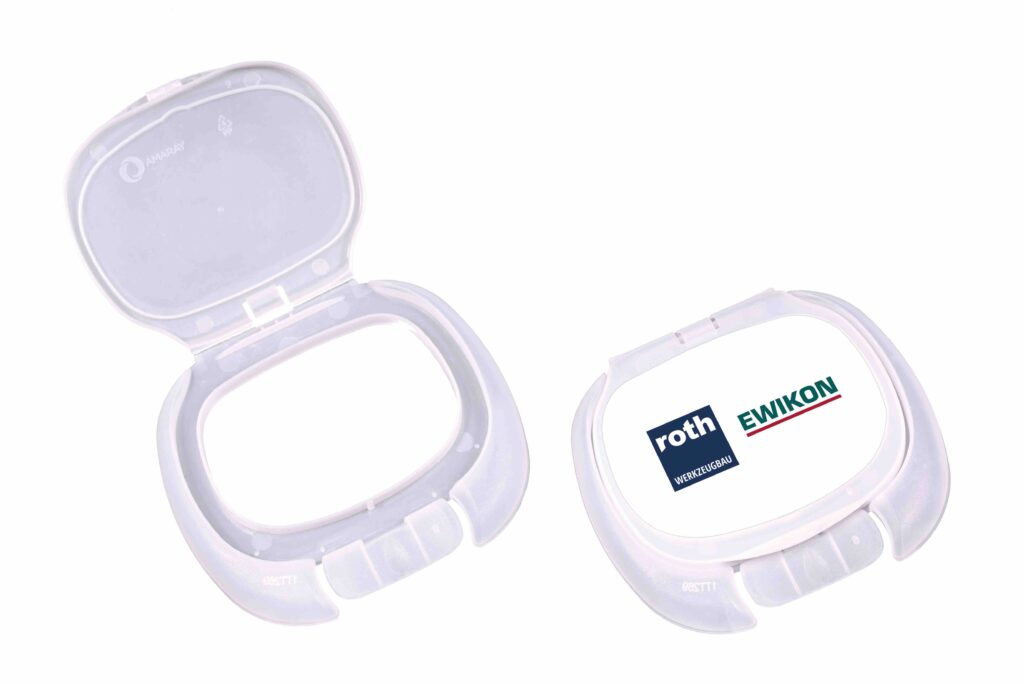
Dimensioni e peso sotto controllo
Dal momento che la taglia della pressa a iniezione, e quindi le dimensioni dello stampo, sono state definite dal committente, per ottenere la massima produttività, roth mold + automation ha dovuto pensare a una soluzione stack mold a 12+12 cavità ottimizzata in base allo spazio disponibile. «Sebbene fossimo riusciti a progettare uno stampo compatto, con altezza di 1.250 millimetri, era necessario sviluppare un allestimento speciale, poiché le dimensioni sono inferiori di soli 4 millimetri al passaggio tra le colonne» spiega Benjamin Noack, Project Manager di roth. «Lo stampo è quindi caratterizzato da un design modulare, con speciali connettori a spina per i collegamenti elettrici tra le piastre per garantire facilità di smontaggio e manutenzione, anche quando eseguita direttamente sulla pressa a iniezione».
I tecnici del team roth + automation non hanno affrontato restrizioni solo sulle dimensioni, ma anche sul peso. A causa delle limitate capacità della gru disponibile nello stabilimento del committente, otto tonnellate – su un peso totale dello stampo di 12 tonnellate – sono state assegnate al blocco centrale con il canale caldo. Questa esigenza ha richiesto una progettazione ottimizzata in termini di peso dell’intera struttura dello stampo, alla quale ha contribuito anche il produttore di camere calde Ewikon (Frankenberg, Germania).
Canali completamente bilanciati
«Era fondamentale che la riduzione del peso dello stampo non andasse a discapito della sua robustezza» sottolinea Benjamin Noack. «Ewikon è riuscita a risolvere il problema proponendo una speciale configurazione del distributore. La tecnologia a elementi utilizzata permette di realizzare canali di colata molto compatti, su più livelli e completamente bilanciati. Questo ha favorito l’integrazione di supporti addizionali attraverso il distributore. La disposizione molto compatta degli attuatori ha contribuito anche alla riduzione delle dimensioni e del peso del blocco centrale dello stampo. Di fatto, questa flessibilità si è rivelata il fattore decisivo per la scelta Ewikon». Nonostante la riduzione del peso, sono state necessarie misure aggiuntive per stabilizzare lo stampo, azionato da quattro cremagliere sulla macchina. Ad esempio, il blocco centrale è guidato nel basamento rinforzato della pressa e supportato da una traversa regolabile.
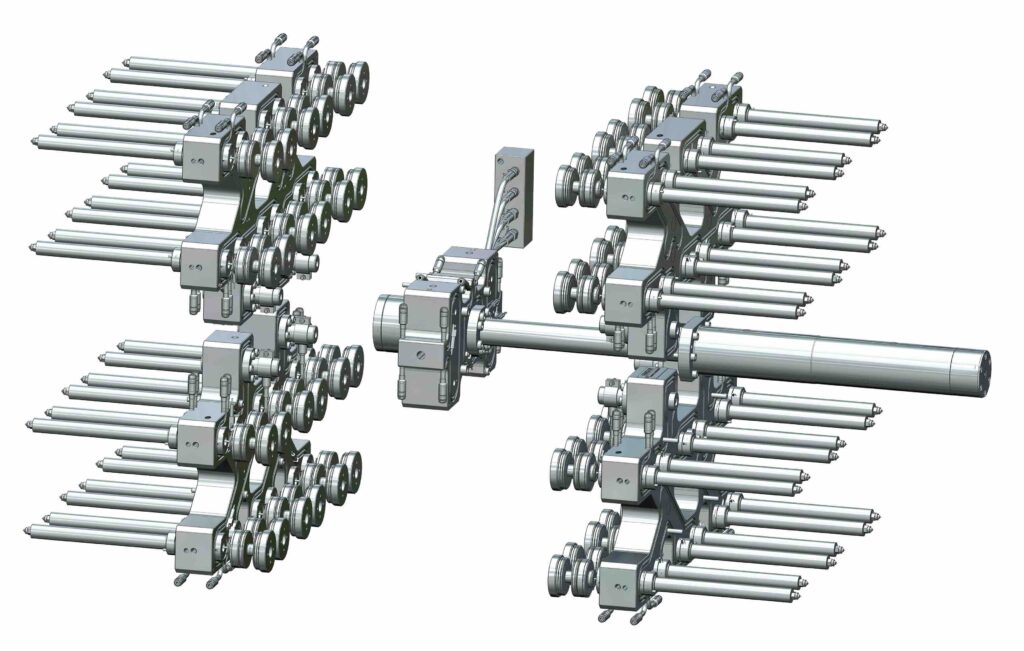
Otturatori ad azionamento sequenziale
Per consentire una più agevole rimozione delle salviettine umide anche con una sola mano, il coperchio incernierato funziona con un meccanismo a pressione. Per garantire un’apertura e una chiusura affidabili durante l’intero ciclo di vita, il coperchio – del peso di circa 7,4 grammi e con pareti dello spessore di 0,8 millimetri – deve essere prodotto con un’elevata precisione dimensionale. Tale obiettivo può essere raggiunto grazie a un buon riempimento delle impronte. I test iniziali, basati su un solo punto di iniezione e condotti con uno stampo pilota a singola cavità realizzato dal cliente finale, hanno mostrato condizioni di riempimento insoddisfacenti; pertanto si è deciso di ricorrere a due punti di iniezione per cavità. Per determinare le posizioni ottimali del punto di iniezione, roth ed Ewikon, in stretta collaborazione, hanno effettuato un’analisi di riempimento mediante il software MoldFlow, calcoli della caduta di pressione e sforzo di taglio del canale caldo. I risultati sono stati convalidati su uno stampo pilota a una cavità, iniettando il componente su un gate del diametro di 1,2 millimetri in un tempo di riempimento di 0,15 secondi. Il primo punto di iniezione è posizionato centralmente sulla superficie del coperchio, il secondo sulla struttura della cornice di apertura. Per ottenere la massima stabilità possibile del pezzo, gli otturatori delle valvole vengono aperti sequenzialmente, in modo da spostare la linea di giunzione 5 millimetri oltre la cerniera a film. In ogni faccia dello stampo, i 12 pezzi sono distribuiti in quattro file orizzontali di tre pezzi ciascuna. Per ogni fila, gli otturatori del primo e secondo punto di iniezione vengono attivati in gruppo, attraverso linee di alimentazione realizzate nelle piastre. Questa configurazione richiede 16 circuiti di controllo pneumatici, attivati dal sistema di controllo pneumatico della pressa.
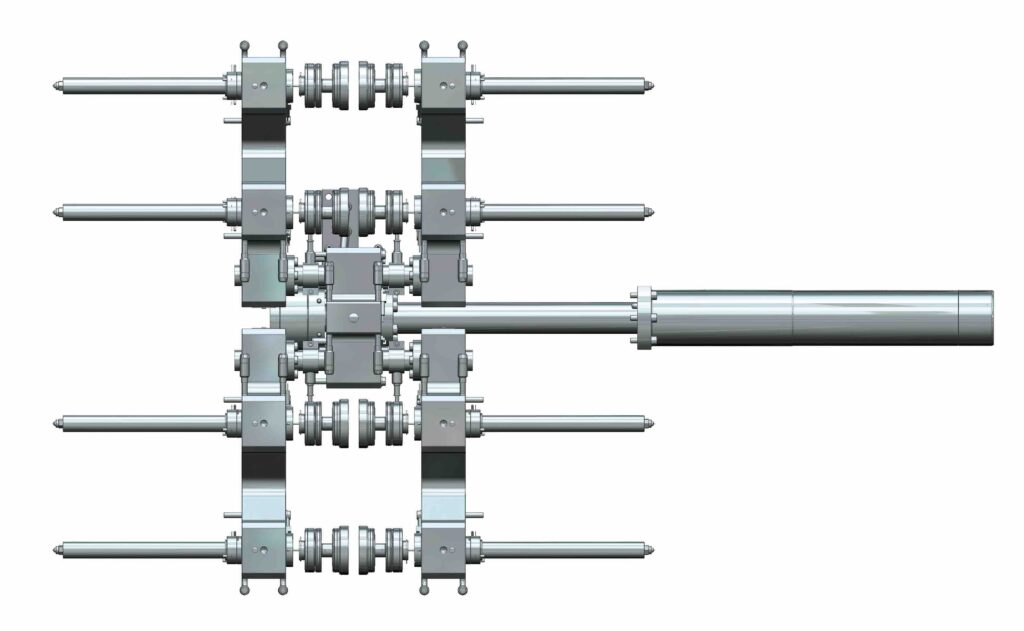
78 zone di controllo e 58 circuiti di raffreddamento
Per ogni faccia dello stampo, la distribuzione prevede due collettori dotati di due ingressi del materiale. Ciascun ingresso alimenta sei ugelli, ovvero tre cavità dello stampo. Ogni distributore richiede quindi due gruppi da sei punti completamente indipendenti e bilanciati, disposti in maniera da rendere semplice la realizzazione di supporti stampo attraverso il collettore. Un distributore ponte posizionato centralmente, con uscite su ogni lato, trasferisce il fuso a tutti i distributori. Il trasferimento del fuso senza perdite dall’ugello della macchina viene effettuato utilizzando una barra di colata con otturazione pneumatica raffreddata, avvitata sul distributore ponte. La lunghezza dell’otturatore è di 1.000 millimetri e il diametro di 6 millimetri. I 48 ugelli installati hanno una lunghezza variabile di circa 10 millimetri, a seconda della posizione del punto di iniezione. Gli attuatori pneumatici, integrati nelle due piastre centrali in una soluzione coassiale molto compatta, non solo ottimizzano il tempo ciclo, ma assicurano anche un miglioramento della qualità del punto di iniezione. Lo stampo ha un totale di 78 zone di controllo e 58 circuiti di raffreddamento.
Tempo ciclo ottimizzato, produttività elevata
Terminato lo stampo, i tecnici roth hanno ottimizzato il tempo ciclo, che si aggira intorno ai 10 secondi. Le caratterisitiche costruttuttive e i materiali impiegati garantiscono una capacità di oltre 50 milioni di pezzi all’anno. Considerando che gli stack mold con etichettatura nello stampo costruiti finora per il settore dell’imballaggio sono stati realizzati al massimo in 8+8 cavità, la soluzione sviluppata da roth è tra le più avanzate e sofisticate proposte in Europa. Il design compatto dello stampo e del canale caldo, l’elevata produttività e l’alto livello di automazione, che permette di produrre i componenti in condizioni altamente igieniche e senza contatto umano in ogni fase del processo, si delineano come i principali vantaggi della soluzione.