Quest’articolo propone un esempio di come uno stampo sviluppato per la produzione di un manufatto composto da due materiali diversi assicuri notevoli vantaggi funzionali e tecnici.
In questa fase di mercato, scombussolata da eventi esterni e dinamiche spesso poco chiare, l’unica strada per rimanere competitivi è quella di offrire soluzioni e tecnologie sempre più efficienti, al fine di ottimizzare spese e costi di produzione. Il mercato richiede sempre di più manufatti realizzati con due o più polimeri con un’unica stampata, grazie alla costruzione di stampi cosiddetti “bimateria” (o, meglio, per stampaggio bicomponente, ndr) e all’utilizzo di presse a ciò destinate. Abbiamo indagato il tema con un esempio concreto che ci offre la società Plastmeccanica di Correggio (Reggio Emilia), che fu fondata nel 1967 e che oggi rappresenta una realtà di riferimento nel settore della progettazione e della costruzione di stampi a iniezione e nello stampaggio di componenti in materiali termoplastici.
Omar Mantoan, responsabile commerciale del gruppo Plastmeccanica-Plaber-Union Stampi, ci propone un caso interessante: “Uno dei nostri clienti costruisce pompe speciali per la distribuzione di prodotti chimici per il trattamento delle coltivazioni intensive in ambito agricolo”.
All’interno di queste pompe, sino ad alcuni mesi fa, erano presenti componenti tecnici costituiti da un particolare in polietilene adatto a resistere al contatto con gli acidi, che tuttavia poteva dare problemi di tipo meccanico-funzionale, nel senso che l’uso intensivo poteva innescarne la rottura, soprattutto nella parte esterna. “Ci venne chiesto”, riprende Mantoan, “se il prodotto in questione potesse essere migliorato, soprattutto al fine di evitare rotture indesiderate. La soluzione proposta dai nostri specialisti, sulla base di pregresse esperienze, fu quella di ipotizzare un pezzo realizzato tramite stampaggio ma con due materiali diversi, lasciando il polietilene originario all’interno, mantenendo invariata la resistenza agli acidi, e inserendo nella parte esterna un polipropilene rinforzato con fibre di vetro, dunque molto più resistente e in grado di contrastare le sollecitazioni d’esercizio, aumentando quindi la robustezza e la durata del componente nel tempo”.
Una progettazione accurata
I progettisti dell’ufficio tecnico di Plastmeccanica eseguono sempre un’analisi preliminare accurata delle caratteristiche dell’oggetto da realizzare, con definizione delle proposte da sottoporre al cliente in base alle caratteristiche meccaniche, estetiche e funzionali specifiche dell’utilizzo del prodotto. “Noi seguiamo il cliente dalle prime fasi progettuali fino alla consegna del prodotto finito”, precisa Omar Mantoan. “All’occorrenza, effettuiamo la prototipazione rapida, estetica e funzionale del componente finale, utilizzando i materiali più idonei per le verifiche. In questo caso, l’aspetto più “ostico” fu proprio quello di far comprendere al nostro cliente che l’investimento in una nuova attrezzatura, e più precisamente in uno stampo “bimateria” ben più evoluto e complesso rispetto a uno “stampo medio”, avrebbe prodotto un grande vantaggio sul lungo periodo”.
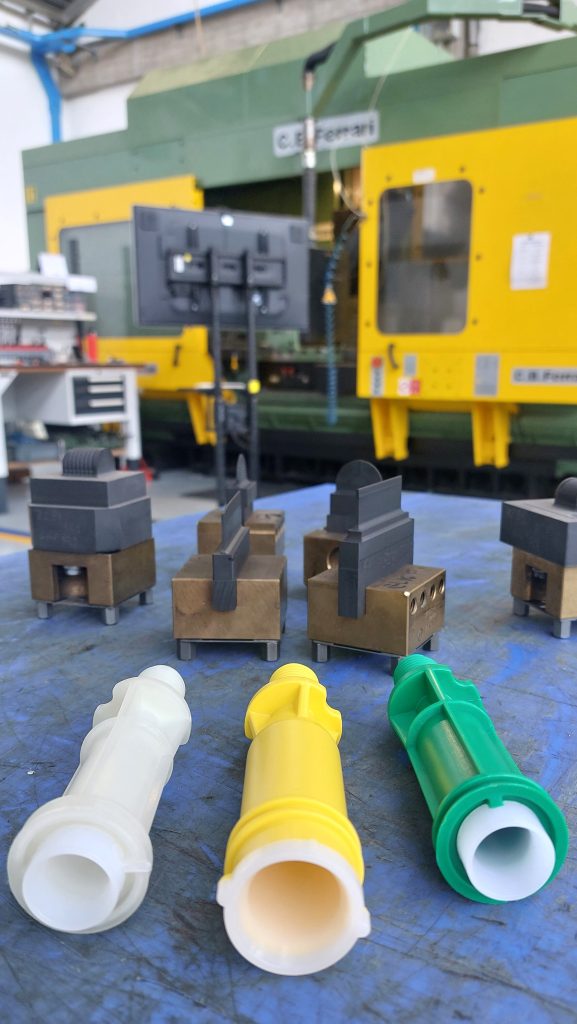
Una volta che il cliente diede il suo benestare, i progettisti dell’ufficio tecnico di Plastmeccanica si misero subito al lavoro. Mantoan: “I nostri specialisti utilizzano CAD/CAM d’ultima generazione, quali SolidWorks per la modellazione spinta e Cimatron per la progettazione 3D degli stampi, e software che permettono di simulare la fase di riempimento dello stampo, come Moldex3D. Nel caso in questione, furono in effetti svolte alcune simulazioni di riempimento dello stampo al fine di determinare i corretti spessori e la migliore posizione dei punti d’iniezione, in modo da evitare interferenze tra i due componenti. Furono svolte anche diverse prove chimiche di compatibilità tra i due materiali per evitarne il mancato “aggrappaggio”. Difatti, alle volte si verificano incompatibilità nel contatto tra i diversi materiali accoppiati, che possono dare luogo a reazioni non prevedibili, innescando per esempio mancate adesioni”.
Furono perciò utilizzati altri stampi “bimateria” presenti in casa Plastmeccanica e, con essi, svolte prove empiriche per testare il comportamento del polietilene a contatto con il polipropilene rinforzato con fibre di vetro. “I salti di spessore determinavano criticità nell’aderenza tra i due materiali”, spiega Mantoan. “Uniformando gli spessori, riuscimmo a risolvere il problema e a ottenere che fossero perfettamente adesi”.
Stampo e stampaggio con piastra rotante
Dopo all’incirca tre settimane di sviluppo dell’attrezzatura (fase comprensiva delle simulazioni), di prove empiriche e delle necessarie modifiche e revisioni, la matematica dello stampo fu definita e la commessa passò all’attrezzeria. L’impresa emiliana dispone di cinque centri di lavoro CB Ferrari, di cui uno a 5 assi, uno a 4 assi e tre a 3 assi, tre macchine Charmilles per l’elettroerosione, due a tuffo e una a filo, oltre a macchine più tradizionali quali torni, rettificatrici ecc. Mantoan: “Uno stampo come quello in esame, per “sopportare” lo stress di un doppio stampaggio in sequenza, deve essere realizzato con materiali altamente duri: scegliemmo quindi un acciaio temprato ad alta percentuale di carbonio, che lavorammo per asportazione di truciolo sui nostri migliori centri di lavoro, al fine di garantire la più alta precisione possibile”.
Una volta costruito e assemblato, attività durata all’incirca sei settimane, lo stampo passò al reparto stampaggio, dove l’azienda emiliana dispone di 22 presse a iniezione (BMB, Negri Bossi ed Engel) con forze di chiusura da 70 sino a 1200 tonnellate, di cui due dedicate al costampaggio di materiali o colori diversi. In particolare, questo stampo fu installato su una pressa BMB da 280 tonnellate, dotata di piastra rotante indexata, quindi ideale per i processi automatici di costampaggio o per l’esecuzione di pezzi con due materiali.
“La pressa in questione”, sottolinea Mantoan, “presenta un gruppo di plastificazione orizzontale e uno verticale, ognuno alimentato dai due diversi materiali. La rotazione della piastra permette di eseguire il riempimento in fasi successive e sovrapposte, in modo da generare il pezzo bicomponente”.
La produzione del componente in questione, entrata a regime da poche settimane, prevede un tempo di ciclo complessivo di 40 secondi circa e una taratura precisa delle due camere calde che compongono lo stampo, al fine di assicurare un flusso dei materiali costante e omogeneo. Omar Mantoan entra nel dettaglio: “Le camere calde lavorano a una temperatura di circa 240°C, i due materiali vengono fusi e sono introdotti nello stampo a una temperatura di circa 210°C e l’intero stampo, sotto esercizio, viene mantenuto a una temperatura compresa tra i 30 e i 40°C”. I componenti, una volta stampati, passano le fasi di verifica e controllo dimensionale, dopodiché vengono spediti al cliente.
Massima soddisfazione
La messa in produzione con successo di questo componente “bimateria”, migliorativo rispetto a quello che era già presente sul mercato, è stata accolta con ampia soddisfazione da parte del committente che ha capito l’importanza d’investire in uno stampo e in attrezzature tecnologicamente più avanzate a fronte di un beneficio sul lungo periodo in termini di affidabilità e qualità dei propri prodotti. “E anche noi di Plastmeccanica”, conclude Omar Mantoan, “siamo molto soddisfatti di aver portato a termine tale progetto approfondendo così il campo dello stampaggio bicomponente, che è una tecnologia, a nostro avviso, dalle grandi potenzialità e dal futuro radioso”.
Vittorio Pesce