Lo stampaggio a iniezione di compositi fibrorinforzati a matrice termoplastica sta diventando sempre più importante nella produzione in serie di componenti “leggeri” per l’industria automobilistica. Prima di tutto perché questa tecnologia permette di integrare in modo efficiente la formatura e la funzionalizzazione di preimpregnati rinforzati con fibre (reinforced pre-preg) riducendo i costi unitari, e poi perché l’impiego esclusivo di polimeri termoplastici semplifica il riciclo dei pezzi a fine vita. La risposta di Engel all’alleggerimento è organomelt, un processo che prevede il riscaldamento, la formatura e il sovrastampaggio – in un unico stampo – di laminati termoplastici rinforzati con fibra (organosheet).
L’evoluzione del processo organomelt
Il processo, ormai consolidato, viene già impiegato con successo nella produzione di massa, ma il costruttore di macchine è sempre attivo nello sviluppo di soluzioni per migliorarlo. Attualmente, sta collaborando con clienti partner su alcuni aspetti della progettazione e produzione di componenti in composito con una distribuzione del carico mirata e differenziata. Ne è un esempio il processo presentato al K2019, sviluppato in collaborazione con Brose, importante fornitore di molte case automobilistiche. Secondo Engel, il sistema è oggi l’unico in grado di lavorare contemporaneamente tre organosheet di forma e spessore diverso in un processo completamente automatizzato. Le diverse sollecitazioni sulle singole aree dei componenti possono essere affrontate grazie alla selezione mirata di organosheet sulla base della distribuzione del carico, un risultato che Brose ha contribuito a garantire attraverso una varietà di processi di simulazione. Ad esempio, il modulo porta dimostrativo prodotto al K2019 è più rigido nella zona della cornice rispetto a quella centrale.
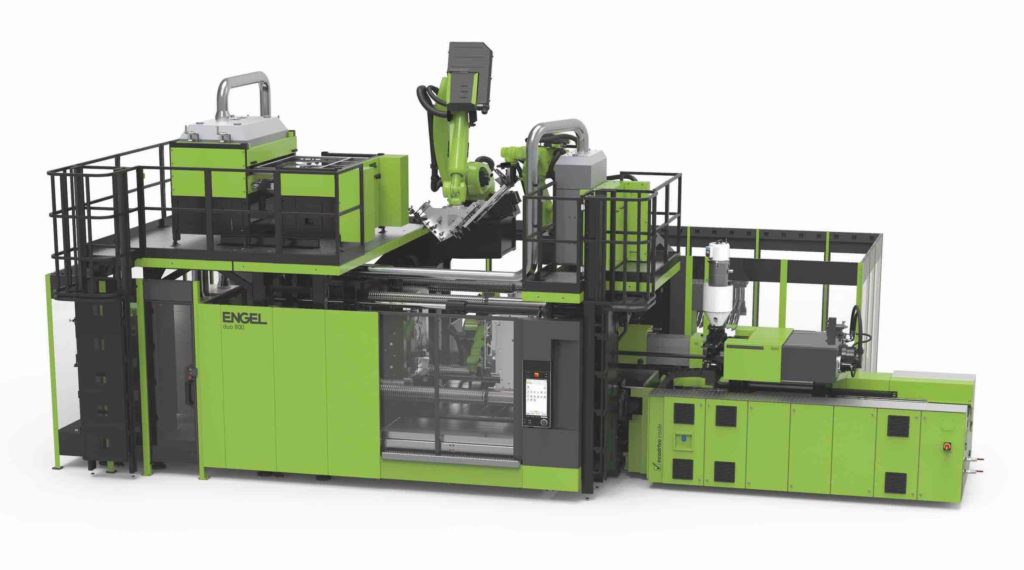
Integrazione del forno IR ultra-compatto
Una delle sfide da affrontare nella lavorazione degli organosheet è il riscaldamento. Il tempo di riscaldamento e raffreddamento dipende dal loro spessore. Un fattore di fondamentale importanza è la velocità: il riscaldamento del materiale deve avvenire rapidamente per evitare che si danneggi, così come il trasferimento del preimpregnato caldo nello stampo. Gli organosheet utilizzati nel processo dimostrativo (forniti dalla cinese Kingfa) sono costituiti da una matrice in fibra di vetro impregnata con polipropilene. L’unità di produzione comprende una macchina a iniezione Engel duo 3660/800, due forni a infrarossi (IR) e tre robot antropomorfi Engel easix.
Il primo forno è verticale e viene utilizzato per riscaldare un organosheet di spessore inferiore (0,6 mm); per ridurre al minimo il tempo di trasferimento del materiale allo stampo è collocato sopra l’unità di chiusura della pressa. Il secondo, utilizzato per gli organosheet più spessi (1 mm e 2,5 mm), è un tradizionale forno orizzontale. Posizionato su un supporto sopra il piano mobile della macchina a iniezione, permette di ridurre la distanza tra il forno e lo stampo e al contempo di risparmiare spazio, perché non richiede alcun ingombro a terra. Entrambi i forni IR sono stati progettati e prodotti da Engel.
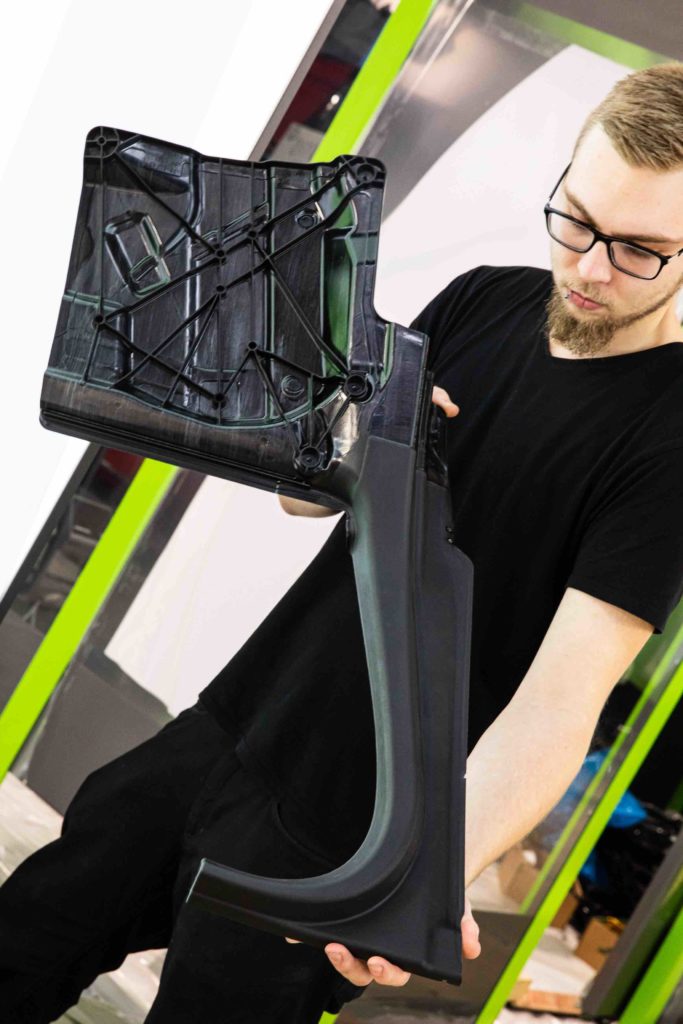
Tre robot, grande sincronizzazione
Il processo prevede che tre organosheet vengano riscaldati simultaneamente. La loro movimentazione è gestita da due robot, posizionati l’uno accanto all’altro sopra l’unità di chiusura della pressa. Mentre il primo robot si occupa delle due foglie organiche di spessore maggiore, il secondo è dedicato a quella più sottile. Un terzo robot ha il compito di rimuovere il pezzo stampato e, al contempo, di spostare una delle tre lastre organiche nello stampo per il processo di stampaggio a iniezione. Questo terzo robot è situato accanto all’unità di chiusura.
Quando lo stampo – costruito dalla svizzera Georg Kaufmann Formenbau – si chiude, le lastre organiche ancora calde vengono formate e quindi sovrastampate con polipropilene rinforzato con fibra di vetro. Le nervature di rinforzo vengono stampate sul retro del componente, mentre sul lato visibile viene impressa una grana con effetto pelle che garantisce una finitura superficiale di elevata qualità.
Processo complesso, facile gestione
La tecnologia, sviluppata presso Center for Lightweight Composite Technologies di Engel, si distingue per elevata efficienza ed economicità, requisiti essenziali per la produzione di massa. Un altro aspetto rilevante della soluzione è la completa integrazione di forni e robot nell’unità di controllo CC300 della pressa, attraverso la quale possono essere gestiti facilmente. La massima integrazione delle attrezzature garantisce una logica operativa uniforme per l’intero processo. Inoltre, poiché pressa, robot e periferiche accedono allo stesso database, il rischio di errore diminuisce e l’efficienza aumenta.