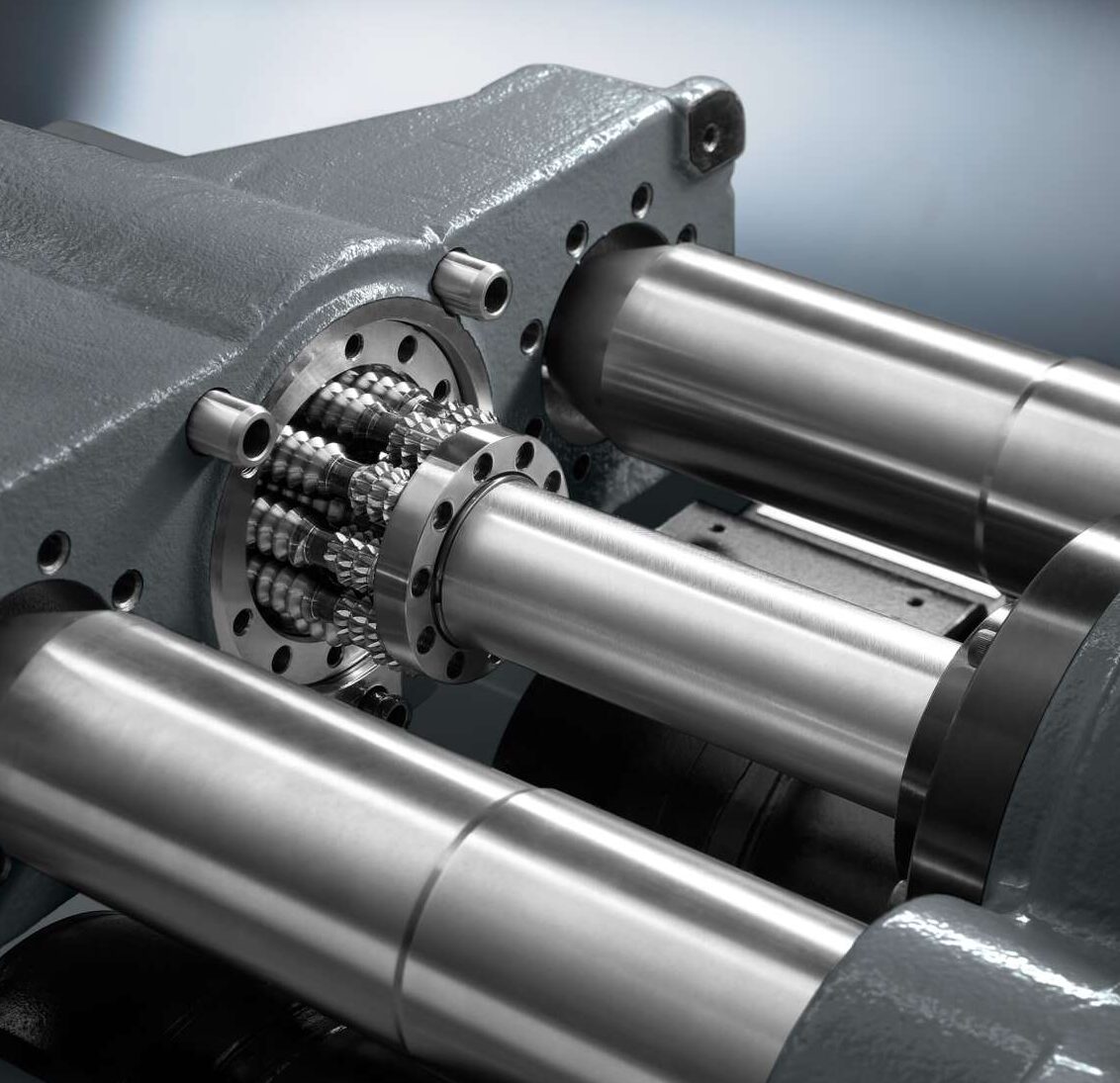
Qual è la macchina a iniezione migliore per un’applicazione specifica? Deve essere veloce e al contempo efficiente? E a quale prezzo? Chiunque cerchi di rispondere a queste domande basandosi sui dati delle schede tecniche è destinato a rimanere deluso, perché a volte i costruttori riportano parametri misurati in condizioni diverse e non confrontabili tra loro. Oltre al volume di iniezione e alla velocità di iniezione, nella scelta di una macchina sono importanti anche il tempo di riempimento e il peso delle parti da stampare.
Nel seguito spiegheremo perché le prestazioni sulla carta e nella realtà cambiano, al contrario della fisica. Il concetto può essere illustrato pensando al veicolo che dovrebbe scegliere un automobilista in partenza per una vacanza Oltralpe avendo a disposizione un potente SUV, una decappottabile sportiva e un rimorchio. Entrambe le vetture hanno all’incirca la stessa potenza di 250 kW, ovvero circa 350 CV. Quale gli permetterebbe di attraversare le Alpi con una guida rilassata e quale invece di inerpicarsi sulle montagne nel modo più divertente? È meglio caricare il SUV sul rimorchio e guidare l’auto sportiva fino a destinazione, oppure il contrario?
Per molti è facile rispondere alla domanda, ma sarebbe più difficile ottenere risposte chiare trasferendo il concetto al mondo dello stampaggio a iniezione. Una delle ragioni è il cambiamento nella tecnologia degli azionamenti e nel background tecnico dei costruttori, che sempre più spesso provengono dal settore delle macchine utensili. Di conseguenza, la velocità dell’asse di iniezione viene specificata in alcuni casi con un’unità di misura lineare (mm/s) e in altri volumetrica (cm3/s). Altri dati solitamente presenti nelle schede tecniche riguardano il diametro della vite, il volume della stampata e la pressione di iniezione. I valori comprovati e riconosciuti sono quelli che si ottengono a pieno carico a 2.000 bar di contropressione e corsa della vite pari a 1 D. In Europa, la maggior parte degli stampi e delle viti si basa su questi valori di carico meccanico.
Dati teorici e valori reali
Le note a piè di pagina nelle schede tecniche che citano regimi al minimo “teorici”, senza però tenere conto della pressione o con tempi di mantenimento limitati, sono poco significative. Ed è addirittura impossibile stabilire se tali valori – così come quelli nelle unità di controllo – siano sufficienti a garantire i tempi di iniezione desiderati in condizioni operative reali. Ad esempio, una velocità al minimo “teorica” di 1.000 mm/s indicata nella scheda significa semplicemente che il motore può girare abbastanza velocemente da raggiungere, teoricamente, la velocità specificata su tutta la corsa della vite, senza tuttavia tenere conto della contropressione nello stampo, all’interno del quale il fuso non scorre certo spontaneamente. Più veloce è il movimento di iniezione, maggiore è la contropressione e di conseguenza la pressione richiesta per effettuare l’iniezione. Inoltre, ovviamente, non è possibile passare alla pressione di mantenimento alla massima velocità, perché se non ci fosse un rallentamento lo stampo andrebbe inevitabilmente in sovraccarico. Il valore teorico, quindi, non verrà mai raggiunto in condizioni di processo reali.
Unità di iniezione idrauliche ed elettriche
Nelle schede tecniche si legge che le moderne unità di iniezione idrauliche richiedono una limitata pressione di sistema sovralimentata per poter utilizzare l’intera pressione di iniezione (2.000 bar) alla massima velocità programmata. Per assicurare un’iniezione rapida e precisa, le unità di iniezione ad azionamento idraulico sono solitamente dotate di una servovalvola, e di conseguenza non esistono differenze tra l’una e l’altra in termini di prestazioni dinamiche. Mentre in questo caso è possibile utilizzare l’energia eventualmente immagazzinata nell’accumulatore e un’elevata potenza di picco, la potenza richiesta per gli azionamenti elettrici viene sempre fornita dalla rete direttamente all’asse di iniezione e al puntale della vite. Inoltre, con le unità di iniezione idrauliche attualmente disponibili in commercio la massa inerziale della struttura non svolge praticamente alcun ruolo, a differenza invece di quanto accade per le soluzioni elettromeccaniche. Un altro fattore cruciale nei sistemi elettromeccanici è l’inerzia intrinseca, che deve essere superata al fine di accelerare gli organi di azionamento come l’albero motore, il riduttore o il servomotore, fino a raggiungere la velocità prevista. A tale scopo, di norma, occorre utilizzare almeno il 50% della potenza motrice installata e della coppia disponibile. Le prestazioni dinamiche degli azionamenti servoelettrici diretti dipendono fortemente dal design della parte meccanica. Arburg sviluppa e produce internamente azionamenti con vite a rulli planetari, particolarmente resistenti all’usura e ai carichi di lavoro (figura 1), che installa sulle sue presse delle serie Alldrive e Hidrive.
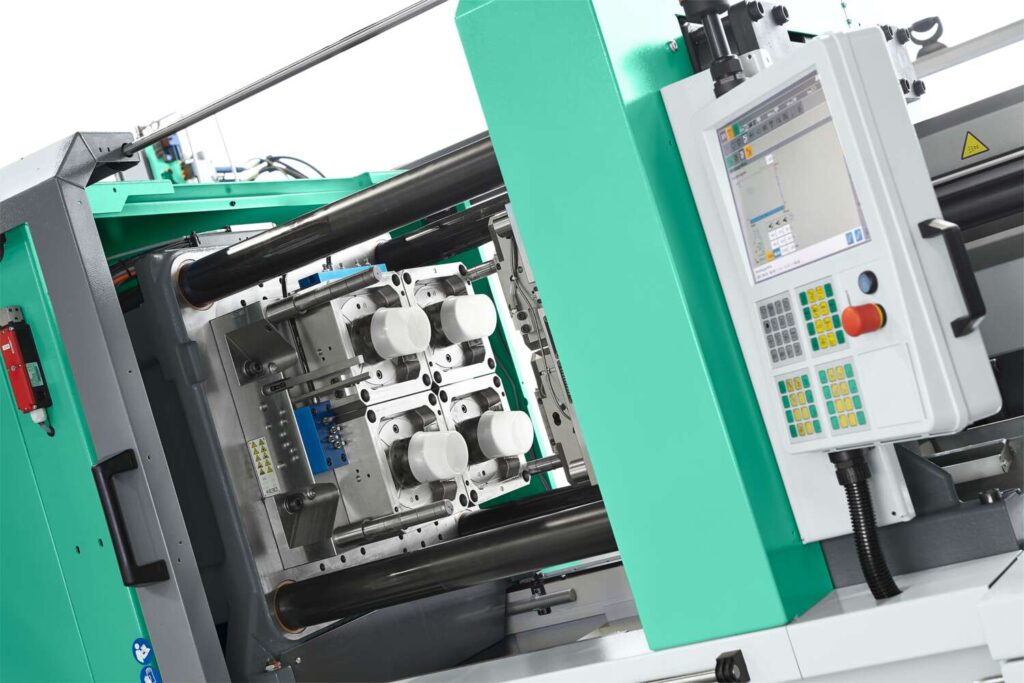
Senza perdersi nei dettagli tecnici, la progettazione meccanica e i principi costruttivi – e di conseguenza il design finale – svolgono un ruolo chiave nelle unità di iniezione elettriche. Le prestazioni dinamiche e la potenza di picco che si possono raggiungere hanno un’incidenza significativa sul prezzo della pressa e sulle potenzialità tecniche del processo di stampaggio a iniezione. Chiarendo il concetto ricorrendo all’esempio dell’automobilista, scopriamo che un’auto sportiva del peso di 800 chilogrammi che movimenta un rimorchio sul quale è caricato un SUV da 2,5 tonnellate non può accelerare da 0 a 100 km/ora in tre secondi e nemmeno mettersi in marcia con il rimorchio a traino su una pendenza del 15% senza far slittare le gomme.
Le diverse classi di prestazioni
Prendendo come riferimento il tempo di riempimento, le applicazioni e le presse a iniezione possono essere suddivise in tre grandi classi (si veda la tabella nella pagina seguente). La maggior parte delle applicazioni rientra nel gruppo dei componenti tecnici stampati con un tempo di riempimento dello stampo a partire da 0,3 secondi. Le macchine idrauliche standard ad azionamento diretto sono generalmente concepite per operare in questa fascia. Le situazioni che richiedono tempi di riempimento estremamente brevi, inferiori a 0,1 secondi, rappresentano la nicchia delle presse a iniezione speciali, che non tutti i costruttori offrono. Queste macchine sono ideali per stampare componenti ad alta temperatura e a pareti sottili realizzati in PEEK per il mercato dell’elettronica e dei beni di consumo; un tipico esempio sono le spine per la ricarica degli smartphone.
Applicazioni | Tempo di riempimento (1 D) | Materiale tipico |
Componenti tecnici a parete spessa stampati a iniezione | > 0,3 secondi | PA12, PBT |
Componenti a parete sottile | 0,1-0,3 secondi | PP, PE |
Applicazioni speciali | < 0,1 secondi | PEEK |
I tempi di riempimento per i componenti a parete sottile sono solitamente compresi tra 0,1 e 0,3 secondi. Fonte Arburg
Tra le classiche lavorazioni che prevedono tempi di riempimento tra circa 0,1 e 0,3 secondi rientra la trasformazione delle poliolefine in imballaggi a pareti sottili, bicchieri (figura 2), secchielli o capsule a vite, con un rapporto tra la lunghezza del canale di adduzione e lo spessore della parete variabile da 100:1 a 300:1. In questi casi sono necessarie elevate prestazioni dinamiche, pertanto sono generalmente preferite le macchine idrauliche con tecnologia ad accumulatore idraulico. Le ultime tendenze in questo comparto sembrano tuttavia preferire le presse elettriche o ibride ad azionamento diretto ad alte prestazioni. “Alte prestazioni” è però un termine assai elastico e relativo.
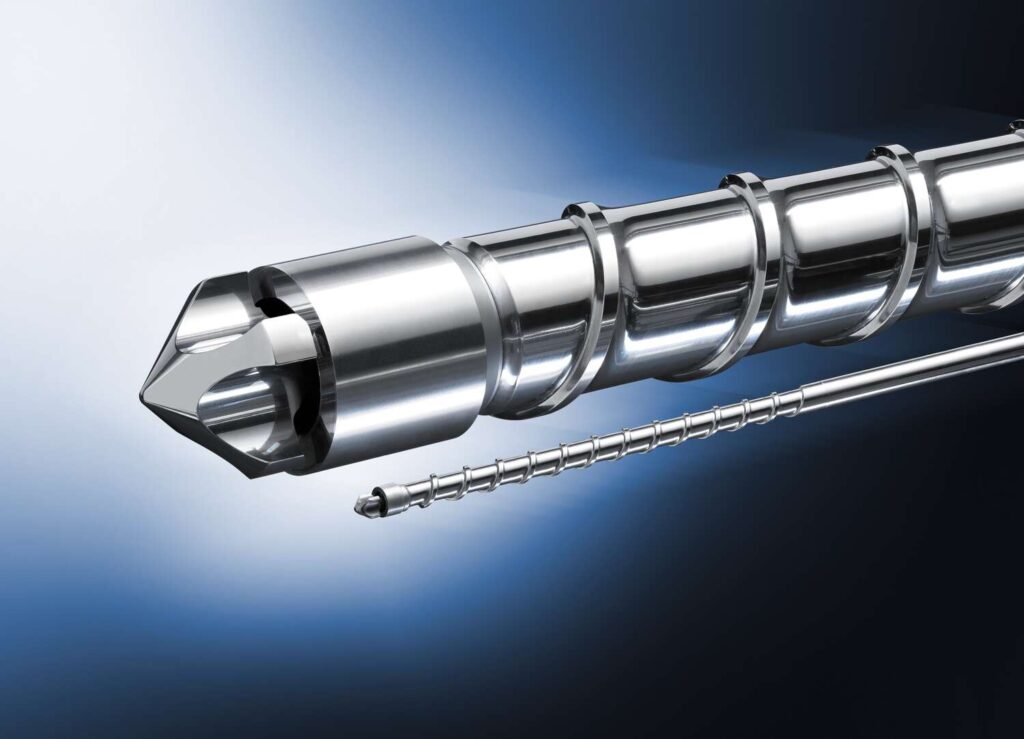
La velocità massima di iniezione espressa in mm/s rappresenta uno degli indicatori caratteristici delle prestazioni tecniche di una pressa a iniezione. Questa unità di misura, in realtà, è mutuata dal settore delle macchine utensili, dove descrive la velocità di avanzamento lineare di un asse. Nella dimensione dei km/h è un’unità di misura che si adatta bene alla velocità massima raggiungibile da un veicolo a motore, ma non da una pressa a iniezione perché le condizioni sono fondamentalmente diverse. Il movimento lineare non descrive esattamente il comportamento dell’unità di iniezione della pressa che, attraverso uno spostamento lineare, inietta nelle impronte dello stampo un volume di plastica fusa. Diventa quindi necessario prendere in considerazione le dimensioni della vite (figura 3).
Pensare in tre dimensioni
Una pressa a iniezione può essere dotata di viti diverse. Alla medesima velocità di iniezione si possono quindi ottenere flussi di volume differenti per unità di tempo, fino ad arrivare al volume di iniezione richiesto. In Europa i diametri delle viti sono generalmente disponibili in misure progressive di 5 mm, cioè 25, 30, 35 mm…, ma alcuni costruttori applicano misure standard diverse (ad esempio, 28, 32 e 46 mm). È quindi evidente l’impossibilità di effettuare un confronto diretto delle prestazioni del processo basandosi solo sulla velocità di iniezione.
Il tempo di riempimento come parametro
In definitiva, ciò che è importante dal punto di vista pratico è il volume del fuso che può essere iniettato nell’unità di tempo prima che il materiale si solidifichi. Il processo di riempimento è caratterizzato dal tempo di riempimento, sul quale si basano le simulazioni di riempimento. In questo contesto, la variabile rilevante è il volume di iniezione per unità di tempo, ovvero la portata volumetrica (Q).
Fin dallo sviluppo dei primi sistemi di controllo alla fine degli anni ‘70, Arburg utilizza il parametro della portata volumetrica (in cm3/s) nelle proprie schede tecniche relative alle presse a iniezione. Una pietra miliare in tempi più recenti è stata l’introduzione del sistema di controllo Gestica, nel 2016 (figura 4), al quale possono essere trasferiti anche i dati per le simulazioni di riempimento. Oggi, la simulazione di riempimento può essere effettuata direttamente sullo schermo tramite la funzione aXw Control FillAssist (figura 5).
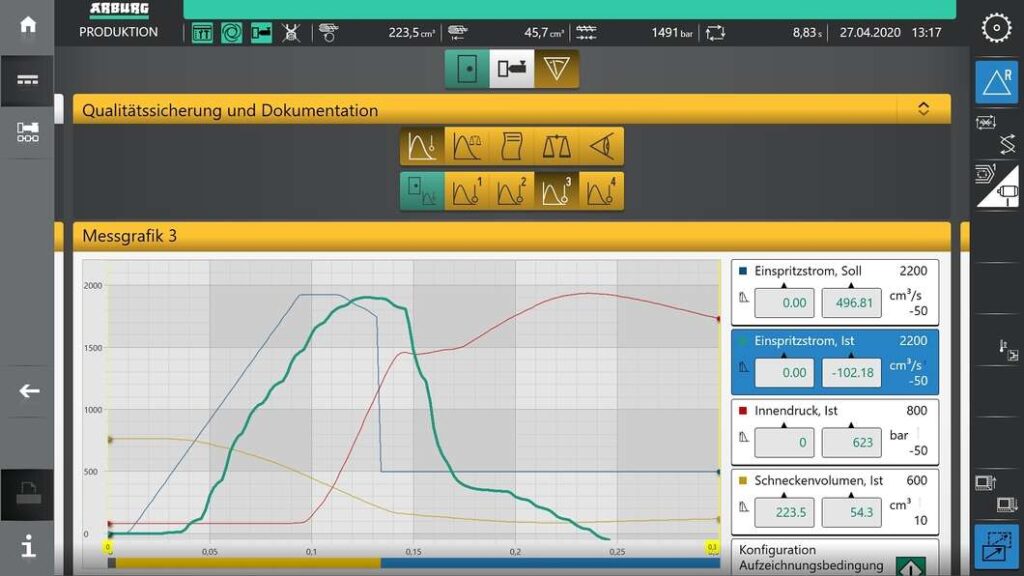
La maggior parte delle presse è in grado di operare con una corsa massima della vite compresa tra 3,5 e 4,5 D, ma questo aspetto è importante solo per i componenti a parete spessa e per tempi di riempimento superiori al secondo. In particolare, nelle applicazioni a parete sottile, una corsa della vite pari a circa 1 D può solitamente essere utilizzata come riferimento per determinare il volume di iniezione generato da una normale vite a tre zone, e di conseguenza il livello di produttività raggiungibile. Il tempo di riempimento che si ottiene in presenza di una corsa della vite di 1 D rappresenta quindi una caratteristica importante per classificare le prestazioni di una pressa a iniezione, indipendentemente dal materiale utilizzato e dalla varietà degli articoli da produrre. Oltre il 95% del fuso deve essere iniettato nello stampo durante il tempo di riempimento. Per il processo di riempimento, il fattore cruciale per una data macchina e unità di iniezione è la quantità di fuso che arriva nello stampo durante il tempo di riempimento a disposizione. Questo costituisce un motivo in più per indicare nelle schede tecniche la portata volumetrica in cm3/s al posto della velocità di iniezione in mm/s. La portata volumetrica, infatti, è correlata al diametro della vite e può essere calcolata facilmente per ogni componente in plastica.

Ad esempio, a un materiale della densità di 1 g/cm3, un volume della parte di 50 cm3 e un tempo di riempimento richiesto di 0,1 s, corrisponde una portata volumetrica di almeno 500 cm3/s. Qualora si utilizzassero azionamenti elettrici, che devono essere accelerati e frenati attivamente con masse inerziali non trascurabili, tale valore deve essere moltiplicato per 2 (operazione triangolare). Il valore da inserire nella scheda tecnica di una pressa adatta a questa applicazione dovrebbe quindi aggirarsi intorno ai 1.000 cm3/s. Senza note a piè pagina.
Portata volumetrica e velocità di iniezione
Per una data velocità di iniezione e diametro della vite (in cm), la portata volumetrica (figura 6) può essere calcolata con l’equazione:
Q = Pi × ¼ D2 × v
dove Q è la portata volumetrica (cm3/s), D il diametro (cm) e v la velocità (cm/s). Se la velocità di iniezione è, ad esempio, 200 mm/s (ovvero 20 cm/s), in presenza di viti con diametri di 35 e 28 mm si ottengono le seguenti portate:
35 mm: 3,14 × ¼ x 3,52 cm2 x 20 cm/s = 192,33 cm3/s
28 mm: 3,14 x ¼ x 2,82 cm2 x 20 cm/s = 123,09 cm3/s
Per ottenere una portata volumetrica di 192 cm3/s anche con una vite da 28 mm, la velocità di iniezione dovrebbe essere di 313 mm/s invece di 200 mm/s, vale a dire circa 1,5 volte quella della vite da 35 mm. In conclusione, più piccola è la vite, maggiore è la velocità di iniezione (mm/s) necessaria per iniettare il medesimo volume di fuso (cm3/s). Al fine di individuare l’unità di iniezione più adatta per una determinata applicazione, si devono quindi conoscere il tempo di riempimento, il peso del componente o della stampata e, se necessario, la densità del materiale. Per questa ragione, quasi tutti i tecnici dello stampaggio a iniezione utilizzano correntemente un piccolo dinamometro a molla. Infatti, a differenza del peso specifico del fuso, è abbastanza semplice determinare il peso effettivo di un componente stampato. Come regola generale, per valutare in modo empirico l’idoneità di una pressa in base alle informazioni riportate nella scheda tecnica, il peso del componente può essere equiparato al volume da iniettare a una densità di 1 g/cm3 (ad esempio, le poliolefine). Nelle macchine moderne, il calcolo esatto secondo il diagramma pressione-volume-temperatura (PVT) viene effettuato direttamente dal sistema di controllo.
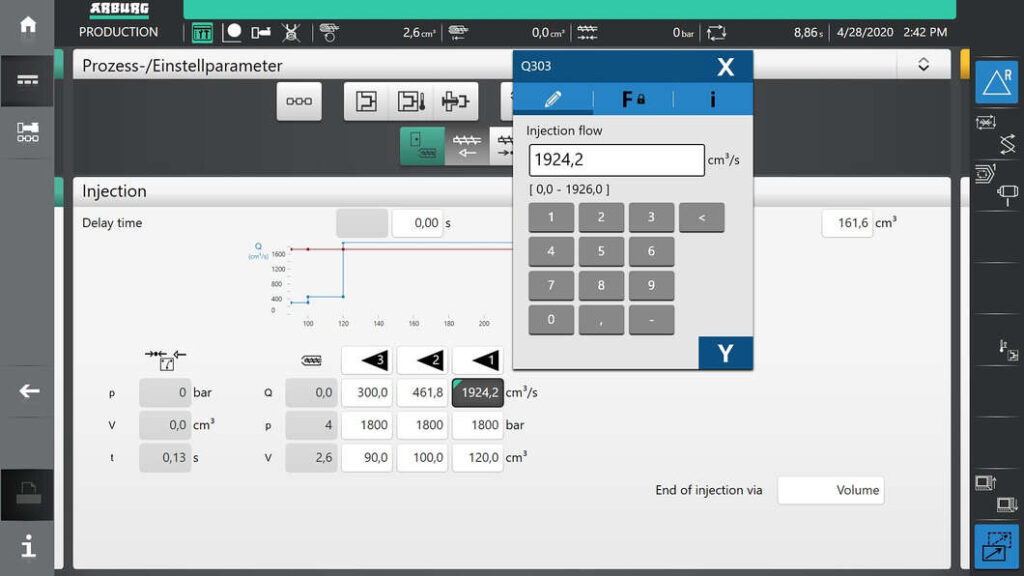
La scelta dell’unità di iniezione più adatta
Proviamo ora a individuare l’unità di iniezione attraverso un semplice calcolo, ipotizzando di produrre una penna a sfera del peso di 5 grammi. Moltiplicando il peso del componente per il numero di impronte (ad esempio otto) e aggiungendo il peso della materozza (ad esempio 30 g) otterremo un peso della stampata di 70 g. Un tempo di riempimento di 0,5 s si traduce in una portata volumetrica di circa 70 cm3/0,5 s, che in caso di azionamenti elettrici, secondo la regola empirica sopra menzionata, corrisponde a circa 2 x 70/0,5 = 280 cm3/s. Dalla scheda tecnica è facile evincere quale unità di iniezione può raggiungere un volume della stampata di 70 cm3 e una portata volumetrica di almeno 280 cm3/s con una corsa della vite di 1 D. In questo modo, è possibile individuare in modo semplice l’unità di iniezione più adatta. Tuttavia, se la brochure indica le velocità in mm/s anziché le portate volumetriche in cm3/s è necessario utilizzare una calcolatrice.
Unità di iniezione in dimensioni standardizzate
La classificazione Euromap 1 delle unità di iniezione si è ormai affermata come uno standard. Il parametro, che si ottiene moltiplicando il volume massimo della corsa (in cm3) per la pressione massima di iniezione (in kbar), viene utilizzato anche per il confronto tra prezzo e prestazioni della macchina. Ad esempio, un’unità di iniezione Euromap 800 è caratterizzata in molti casi da un diametro della vite di 50 mm, una corsa di 200 mm e una pressione massima di iniezione di 2.000 bar.
Dato che nel caso degli azionamenti elettrici la corsa risulta un parametro più economico rispetto alla potenza, diversi costruttori utilizzano viti di diametri più piccoli per un determinato codice Euromap. Di conseguenza, in base al rapporto dell’area quadrata, con un azionamento elettrico sarà necessario prevedere una corsa più lunga, un maggiore rapporto L/D e una velocità di iniezione più elevata per riuscire a produrre il medesimo componente con un dato volume di iniezione e un dato tempo di riempimento. Ad esempio, per un’applicazione a parete sottile con un volume della stampata di 100 cm3 (corsa di circa 1 D) e un tempo di riempimento di 0,2 s, si ottiene una portata volumetrica massima di 1.000 cm3/s in operazione triangolare. Con una vite dal diametro di 50 mm, invece, si otterrebbe una velocità di iniezione di 510 mm/s, mentre con un diametro di 45 mm la velocità di iniezione sarebbe 630 mm/s. Tuttavia, nonostante sulla scheda tecnica venga riportato un valore della velocità superiore di circa il 23%, con un impatto indubbiamente migliore sull’acquirente, in termini di tecnologia di processo non comporta alcuna differenza.
Potenza al massimo sul puntale
Sfortunatamente, la classificazione Euromap 4 della potenza effettiva dell’unità di iniezione non si è ancora affermata come uno standard nelle schede tecniche delle presse, e questo forse perché la potenza di picco dinamica effettiva della vite potrebbe incidere in modo significativo sul prezzo delle unità di iniezione ad azionamento diretto.
Per valutare la potenza, si applica la seguente formula:
L = P/10 × Q
dove L è la potenza (W), P la pressione (bar) e Q la portata volumetrica (cm3/s).
Nel caso riportato in precedenza, indipendentemente dal diametro della vite, il risultato che si ottiene è 200 kW. Per arrivare a questa potenza di picco sul puntale della vite, l’intero sistema deve prima accelerare. Come già accennato, il design gioca un ruolo chiave negli azionamenti elettrici diretti. È qui che la fisica entra di nuovo in gioco, e con essa il principio di inerzia di Newton. Per accelerare una massa inerziale, tutti i progetti tecnici oggi conosciuti richiedono una forza aggiuntiva che varia da 0,5 a 1 volta la forza di carico. Quindi, in presenza di un’applicazione a parete sottile come quella menzionata, la potenza di picco di 400 kW per il motore viene raggiunta rapidamente. Per comprendere meglio torniamo all’esempio delle vacanze e la domanda su quale delle combinazioni abbia davvero senso.
Con una vite più piccola, e di conseguenza una superficie più piccola, è necessario applicare una forza minore con la medesima pressione. Un altro problema da considerare è se si possa erogare la pressione massima durante l’intera fase di iniezione. Le unità di iniezione concepite puramente per le applicazioni a parete sottile, con tempi di riempimento brevi alla potenza di picco, sono meno adatte a gestire i tempi di riempimento di 10 s richiesti per un componente ottico a pareti spesse. In questo caso, l’unità di iniezione comincerebbe a vibrare o a surriscaldarsi a causa del fatto che la pressione di iniezione e di mantenimento devono essere mantenute a lungo periodo, in maniera simile alla decappottabile sportiva che si blocca per un ingorgo in prossimità di un passo con la frizione che slitta alla ripartenza. La questione di quanto della potenza meccanica raggiunga effettivamente il puntale della vite alla velocità richiesta è quindi particolarmente interessante. E, nelle applicazioni a parete sottile, è interessante anche la misura in cui tale potenza possa essere modulata dinamicamente o staticamente.
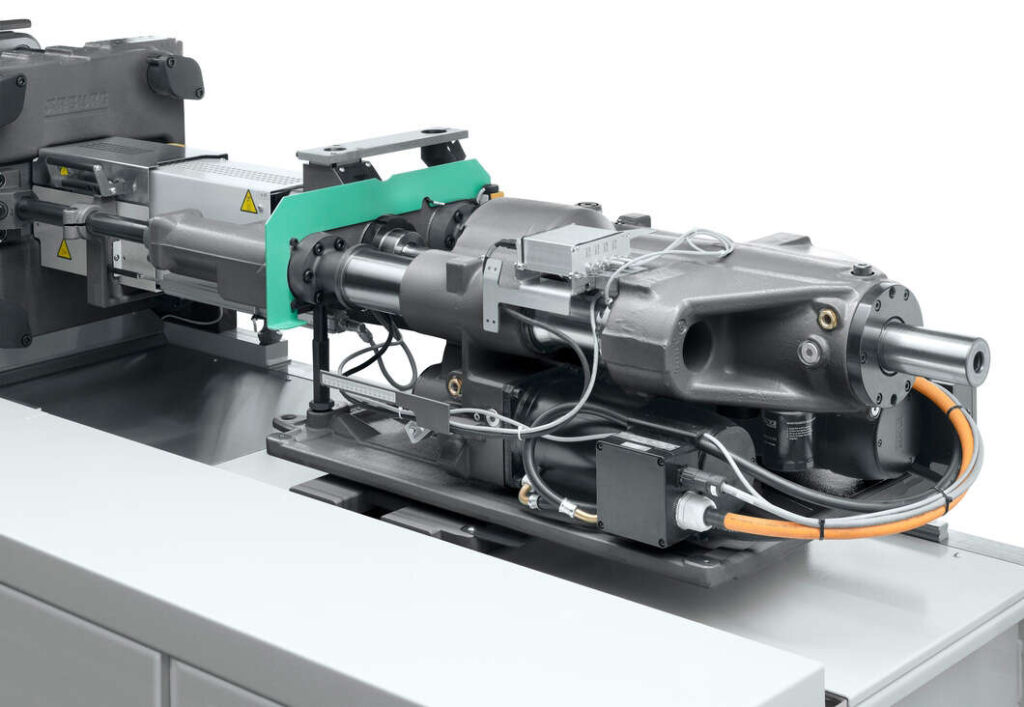
Nel caso delle collaudate unità di iniezione idrauliche, la tecnologia degli accumulatori si è andata sviluppando nel corso del tempo di pari passo con le servovalvole a bassissima inerzia. Nel nostro esempio, sarebbero necessari solo circa 20 kW di potenza di ricarica continua. In riferimento invece ai moderni azionamenti elettrici diretti, sono attualmente in atto alcuni tentativi tecnologici per risolvere il problema della potenza di picco con l’utilizzo di un accumulatore intermedio di energia meccanica o elettrica. Tuttavia, ad oggi, si è davvero affermata solo la soluzione di utilizzare allo scopo la “rete di alimentazione”. Questa potenza extra ha un effetto sul costo degli azionamenti elettrici tanto da collocarli in una fascia di prezzo totalmente diversa. Inoltre, al di sopra di una certa dimensione, l’inerzia “consuma” davvero la potenza di picco, motivo per cui le unità di iniezione elettriche non sono disponibili in qualsivoglia dimensione. Almeno non ancora (figura 7). Nonostante tutte queste sfide, emerge una tendenza a favore degli azionamenti elettrici anche nelle applicazioni con tempi di riempimento compresi tra 0,1 e 0,3 s (imballaggio). In senso figurato, ciò significa non solo scalare un passo con un pesante rimorchio al traino, ma guidare in queste condizioni per centinaia di migliaia di chilometri.
L’opzione migliore
Il volume della stampata e il tempo di riempimento sono parametri importanti per lo stampaggio a iniezione. L’indicatore associato è la portata volumetrica in cm3/s, misurata di regola alla contropressione di 2.000 bar. La portata volumetrica può essere facilmente calcolata partendo dall’applicazione e dai dati dell’unità di iniezione selezionata sulla base della scheda tecnica mediante l’applicazione di alcune regole empiriche.
Di contro, non esiste una scheda tecnica che indichi come siano progettate le unità di iniezione elettriche. Inoltre, è importante anche la questione della tipologia di macchina richiesta: è meglio una pressa progettata per operare a un regime continuo o alla potenza di picco? Puntare su entrambe le caratteristiche non avrebbe senso.
Fondamentalmente, vale l’esempio del mondo automobilistico: una decappottabile sportiva e un SUV possono avere i medesimi cavalli, ma solo l’auto sportiva accelera da 0 a 100 km/h in meno di 5 s. Con una vettura sportiva è anche possibile trainare un carico pesante, ma a soli 40 km/h costanti, perché – come tutti ben sanno – non è un modello progettato per questa funzione. D’altra parte, ecco a cosa servono i SUV.
Una macchina elettrica ad alte prestazioni, ovvero “la sportiva del mondo dello stampaggio a iniezione” è necessaria solo nelle situazioni in cui si devono raggiungere alte velocità e alte dinamiche a causa dei tempi di riempimento molto brevi. Quindi per la maggior parte delle applicazioni, una macchina standard affidabile rappresenta molto spesso l’opzione migliore e più economica.
Traduzione della pubblicazione originale da Kunststoffe/Kunststoffe international, per gentile concessione di Carl Hanser Publishing.
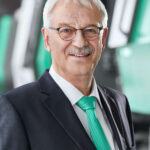