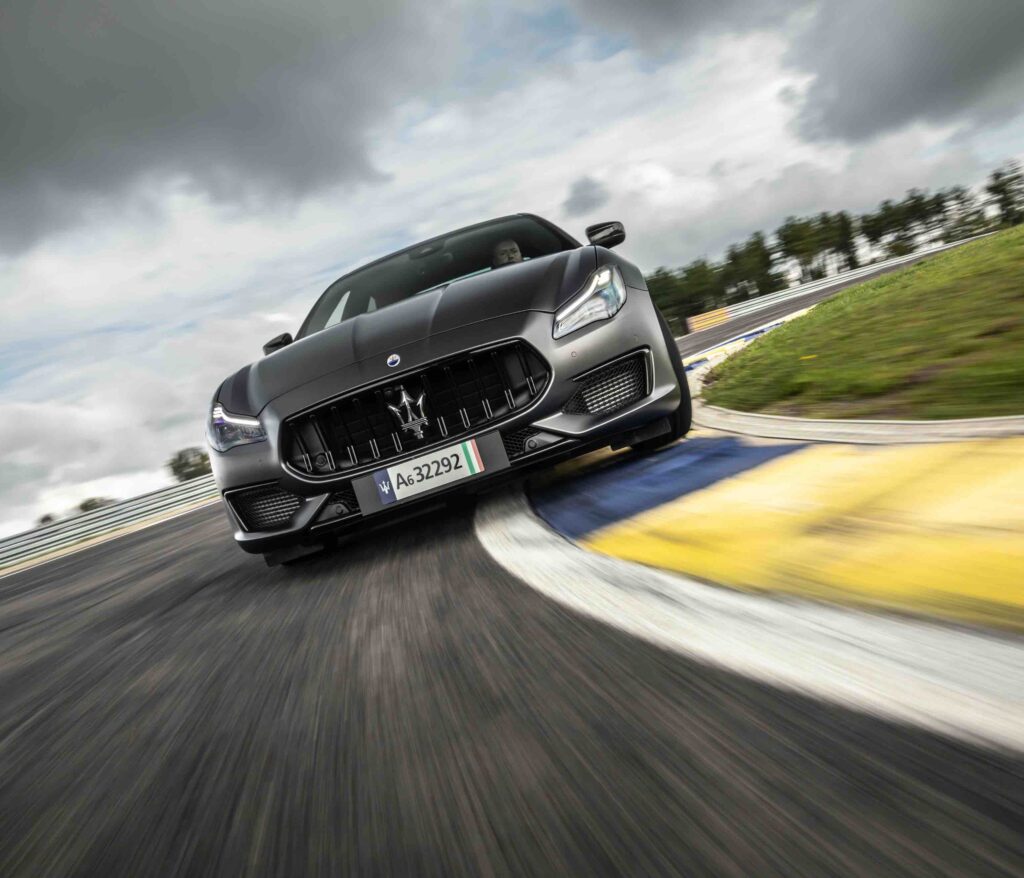
Rispetto al complesso panorama dei tanti componenti oggi presenti in vettura, quelli realizzati in polipropilene espanso (PPE) rappresentano una realtà poco percepita dal cliente finale, ma interessata da un trend di continua crescita e innovazione, specie con le moderne richieste di minor impatto ambientale e di alleggerimento.
Trattamento del PPE e processo produttivo
Il materiale arriva presso lo stabilimento in cui verrà trasformato mediante stampaggio sotto forma di granuli di PP già espansi dal fornitore di materia prima con l’impiego di anidride carbonica. I granuli vengono pretrattati prima dello stampaggio mediante l’insufflaggio lento di aria compressa dentro appositi serbatoi in pressione. Questa fase di impregnazione è fondamentale per permettere al materiale di raggiungere le condizioni termoigrometriche ideali per poter essere trasformato. Attraverso un sistema automatico di canalizzazioni in pressione, i granuli di PPE passano dai serbatoi di pretrattamento direttamente alle tramogge presenti a bordo di ciascuna pressa e, attraverso l’insufflaggio ulteriore di aria compressa, vengono caricati nelle cavità di ciascun stampo. All’interno dello stampo, riscaldato a circa 150 °C con l’utilizzo di vapore in pressione, le perle di PPE aderiscono tra di loro “sinterizzandosi” fino a riempire la cavità e dando origine al componente desiderato. Una seconda fase di vapore insufflato a pressione nella camera dello stampo permette di ottenere una buona finitura superficiale estetica della parte. Lo stampo viene poi raffreddato ad acqua e il componente viene estratto con l’ausilio dell’aria compressa. Il ciclo viene completato da una stazione di post trattamento termico che stabilizza i componenti e li asciuga. In alcuni casi specifici, ad esempio in presenza di costampaggi tra PPE e strutture metalliche o con inserti plastici ottenuti per iniezione, risulta necessaria un’ulteriore fase di conformatura post stampaggio per tenere sotto controllo il ritiro dei diversi materiali a contatto. Tutto il processo di espansione avviene pertanto solo con l’ausilio di anidride carbonica e di vapore, ovvero senza la presenza di espandenti chimici di rilevante impatto ambientale o di additivi pericolosi, quindi rappresenta, insieme alla materia prima poliolefinica riciclabile, un esempio di processo industriale pulito e il più possibile rispettoso dell’ambiente. A questo va aggiunto che le attrezzature per questa tecnologia produttiva sono molto più semplici di quelle richieste per lo stampaggio a iniezione, con conseguente risparmio economico.
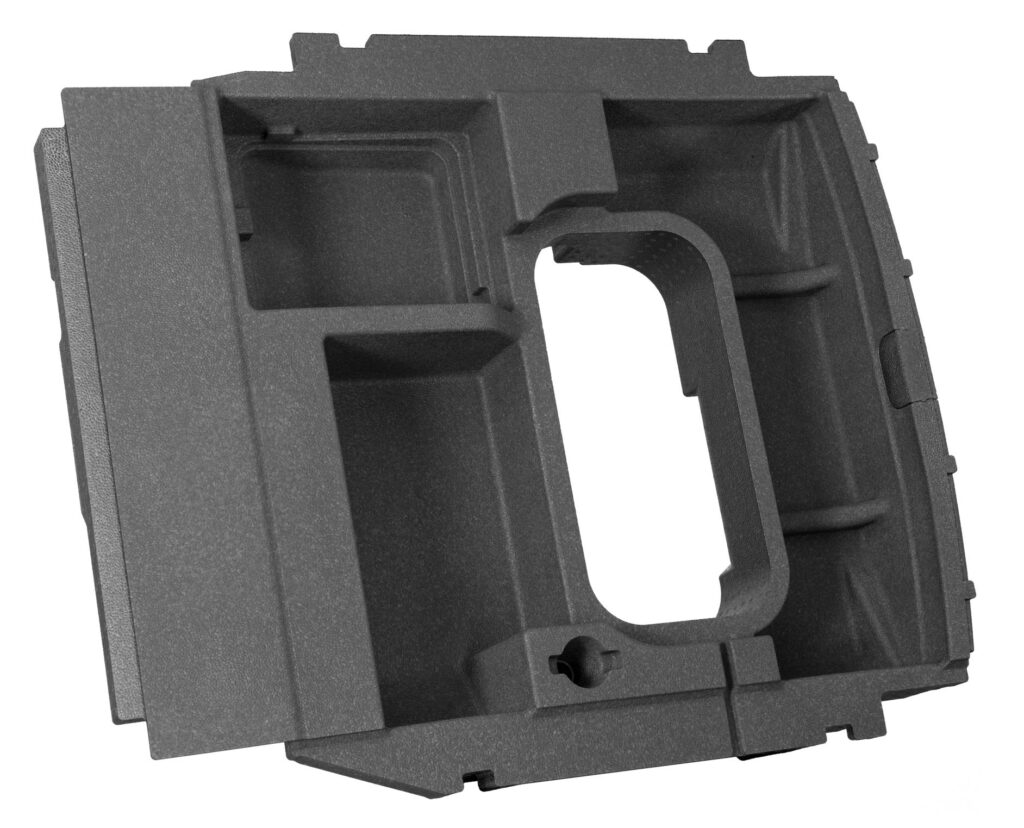
L’applicazione in vettura
L’estrema versatilità del materiale e le sue caratteristiche peculiari hanno permesso la sua applicazione storica sulle vetture di tutti i car maker mondiali per la produzione degli assorbitori urto posizionati dietro i paraurti e all’interno dei pannelli porta. Oltre al raggiungimento della prestazione finale in termini di assorbimento dell’urto e quindi di sicurezza, il materiale risulta molto economico, permette la realizzazione di componenti più leggeri rispetto a quelli simili in plastico rigido ed è facilmente customizzabile durante tutte le fasi di progetto di ciascun sistema complesso, perché permette, senza agire sullo stampo, di ottenere componenti con diverse performance meccaniche grazie alla sola modifica della densità del granulo inserito nello stampo invariato. Altre soluzioni, che utilizzano componenti in plastico rigido ottenuti tramite iniezione o termoformatura, si scontrano da sempre con costi di attrezzaggio più alti, specie nel caso di stampi a iniezione, e con costi e pesi più importanti, senza contare il fatto che tali tecnologie concorrenti richiedono una conoscenza preliminare in progetto delle sollecitazioni indotte nell’urto molto avanzate e non sempre disponibili, perché, in caso di errore, il costo di modifica delle attrezzature per l’iniezione o la termoformatura è oneroso.
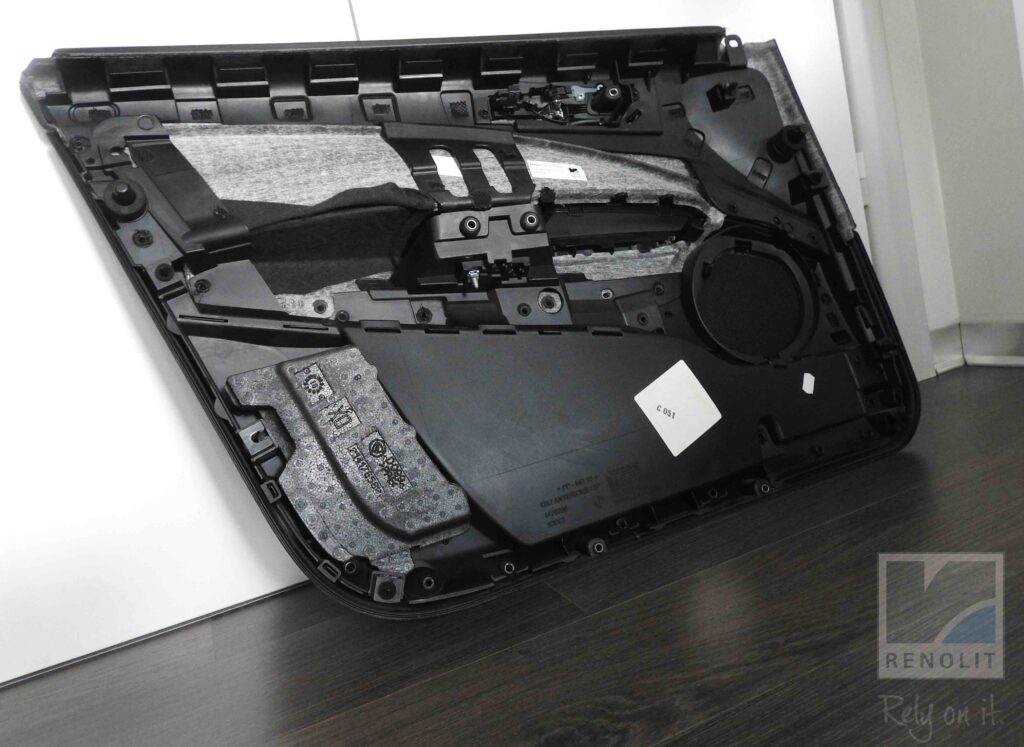
Un’altra applicazione del PPE, condivisa da tutti i costruttori di veicoli, è rappresentata dai moduli cargo box che accolgono i ruotini di scorta e gli altri attrezzi sotto il piano di carico del bagagliaio. Il materiale, oltre a vantare notevoli performance di assorbimento degli urti e acustico, permette di realizzare grandi componenti leggeri e con notevoli finiture estetiche, sorprendenti per un materiale espanso. Lo sviluppo di goffrature estetiche sempre più belle e coprenti permette di nascondere in modo veramente efficace la tradizionale superficie tecnica contrassegnata dalla presenza degli scarichi per il vapore e dall’inconfondibile vista delle perle unite tra di loro in sezione. Il successo del materiale in questi ambiti tradizionali ha permesso la sua introduzione via via su altri componenti, da cui storicamente era escluso. Si parla quindi di valve in PPE sotto la superficie estetica delle pantine para sole, di assorbitori per l’urto della testa sotto i rivestimenti del padiglione, di riempitivi del vano bagagliaio più o meno estetici, di sotto pedane e riempitivi sotto il tappeto dell’abitacolo. Il continuo affinamento della tecnologia di espansione del PP ha permesso, attraverso il costampaggio con inserti metallici o plastici, l’introduzione di moduli sotto sedile attrezzati, che permettono l’integrazione in un solo componente di più parti tradizionalmente realizzate con diversi materiali e processi, con la conseguente semplificazione del processo produttivo e un notevole risparmio economico, anche in presenza di parti soggette a vincoli omologativi.
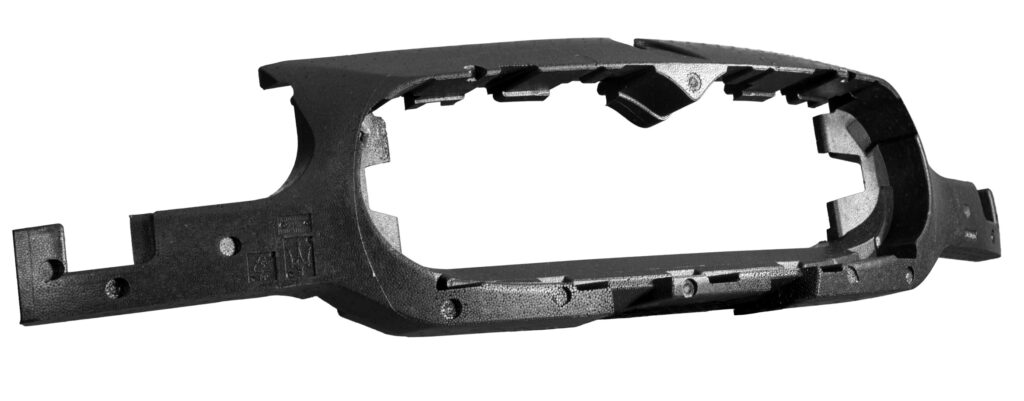
Confronto con altri materiali e tecnologie
Come abbiamo visto, il PPE costituisce un valido sostituto per la produzione di componenti rigidi compatti ottenuti per stampaggio a iniezione, perché il costo delle attrezzature di trasformazione risulta nettamente competitivo e il continuo affinamento delle tecniche di stampaggio permette il costampaggio del materiale espanso con inserti metallici, con conseguente aumento delle performance, degli ambiti di impiego e di una facile riciclabilità a fine vita del componente, aspetto oggi sempre più importante.
Il PP espanso è altresì competitivo e vincente anche rispetto ai tradizionali materiali espansi utilizzati in vettura. Nel confronto con il poliuretano espanso risulta in primo luogo migliorativo perché, in questo momento di grande attenzione ai temi ambientali, è completamente riciclabile. A questo dobbiamo poi aggiungere che, mentre il PUR è soggetto a fenomeni importanti di degrado e progressivo sbriciolamento, il PPE è stabile nel tempo con qualsiasi condizione termoigrometrica e ha assorbimenti di acqua pressoché nulli. L’applicazione del PUR resiste in situazioni dove il PPE oggi non può arrivare per motivazioni geometriche, come ad esempio i rivestimenti del padiglione, dove lo spessore del materassino schiumato è così sottile e leggero da non permettere la sua realizzazione in PPE. Il PUR espanso resiste anche per l’imbottitura di alcune pantine parasole, dove il mercato richiede una morbidezza tattile non raggiungibile con il PPE. Quest’ultimo, inoltre, ha praticamente sostituito il polistirene espanso perché presenta migliori performance termiche e meccaniche. Resiste meglio ai carichi e la superficie, interessata da un carico concentrato, si segna meno e permette un maggiore ritorno elastico del materiale dopo la rimozione del carico. A questo va aggiunta l’eliminazione completa della sgradevole rumorosità del polistirene, sia nel contatto con altri materiali, sia allo sfregamento. Le applicazioni del polistirene espanso permangono quindi solo nel campo dell’imballaggio o per vetture di segmenti bassi. Anche nel confronto con il polietilene espanso (PEE), il PPE sta via via guadagnando posizioni e sostituendo il materiale concorrente che, a parte il costo inferiore della materia prima e dell’attrezzatura, fornisce prestazioni termiche e meccaniche così limitate da pregiudicarne l’applicazione su molti possibili componenti. A fianco della tradizionale soluzione per la realizzazione delle canaline dell’aria sotto plancia e sotto tappeto, i manufatti in PEE sono poco resistenti e si segnano superficialmente sotto carichi modesti. L’inserimento del PPE ha pertanto ampliato l’applicazione dei materiali espansi.
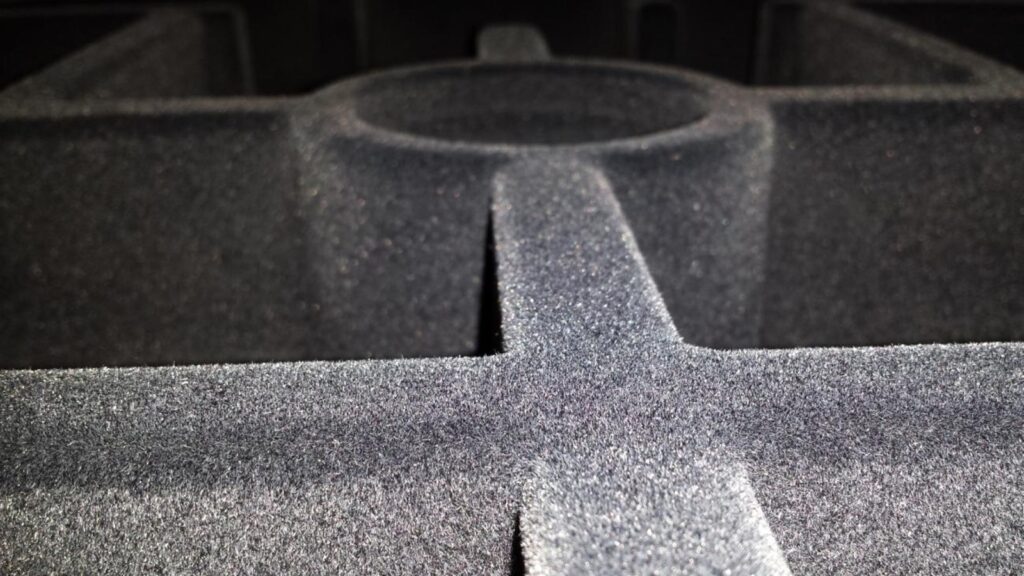
Trend di sviluppo dei veicoli e dei materiali
L’attuale crescente sensibilità verso i temi ambientali e la sostenibilità sta dando un forte impulso all’utilizzo del PPE. Oltre alla riciclabilità del materiale, da solo o in componenti costampati, la leggerezza è un’ulteriore carta vincente per l’impiego automobilistico e veicolare in genere. Se si aggiunge anche la possibilità di integrazione in un solo componente di più funzioni, gli sviluppi iniziano a diventare numerosi. Il PPE permette di proteggere lateralmente le batterie posizionate posteriormente sotto il piano di carico dell’autovettura con la sistemazione laterale di due assorbitori sicuri, non conduttori, leggeri e poco costosi. Presso molti costruttori si parla inoltre dello sviluppo futuro di pannelli porta in PPE integrale rivestiti esteticamente e in grado di sostituire i carrier posteriori con la realizzazione di tutti i fissaggi per il posizionamento del motorino alzacristalli, degli altoparlanti e del trattenimento dei cavi in un solo modulo attrezzato, con notevoli riduzioni di peso, complessità e costo. A questa soluzione va poi aggiunta l’applicazione del PPE ai pannelli retroschienali dei sedili posteriori, che oltre a superare le performance di sicurezza richieste, permettono una più agevole integrazione di molte funzioni, la facile assemblabilità con il resto del sedile e un tangibile risparmio di peso.
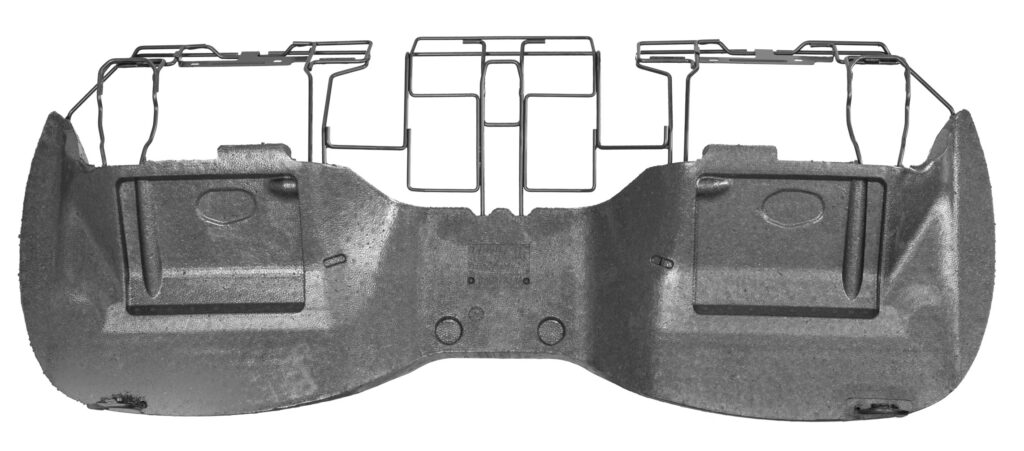
Accanto a queste interessanti opportunità nei componenti per l’interno della vettura, lo sviluppo del materiale lo sta spingendo verso aree più severe e sfidanti. Alcuni costruttori francesi lo hanno già applicato al sistema di inlet air del gruppo clima, che affaccia direttamente sul vano motore, permettendo integrazioni di sistema importanti e quindi semplificazioni nell’assemblaggio, riduzione del numero di sub componenti da attrezzare, riduzioni e di peso e di costi. La diffusione del PPE come materiale tecnico adatto anche ai costampaggi, tradizionalmente utilizzato solo come riempitivo e assorbitore, concorre quindi attivamente al raggiungimento dei nuovi target di peso imposti all’industria dell’auto dall’elettrificazione, con i non trascurabili benefici legati all’integrazione di componenti complessi in uno unico e a un contenimento sensibile dei costi di attrezzaggio. Se si aggiungono le proprietà di assorbimento acustico e meccanico, la completa riciclabilità e i notevoli risultati estetici ottenuti, vedremo in futuro un sensibile aumento del PPE in vettura con soluzioni sempre più ingegneristicamente avanzate.