Le poliammidi (PA) alifatiche sono materiali termoplastici semicristallini caratterizzati da una fase cristallina e una amorfa. La prima è responsabile dell’elevata resistenza meccanica, stabilità termica, resistenza chimica e resistenza al creep, mentre la seconda ne caratterizza la tenacità (resistenza all’impatto) e l’elevato allungamento a trazione, ed è responsabile dell’assorbimento di umidità da parte delle catene polimeriche. La polarità dei gruppi amminici tende infatti a creare legami idrogeno con le molecole di acqua presenti nell’atmosfera, conferendo un effetto plasticizzante sulle catene polimeriche con la conseguente modifica delle proprietà meccaniche. L’assorbimento di umidità comporta anche la variazione dimensionale del manufatto dovuta a un processo di rigonfiamento. Dal momento che il gruppo amminico (o carboamminico) è il diretto responsabile dell’assorbimento di umidità, tutte le poliammidi tendono a incorporarla all’interno delle proprie catene polimeriche in quantità proporzionale al rapporto tra il numero di gruppi metilenici e carboamminici presenti nel monomero di base. Maggiore è questo rapporto, minore sarà il contenuto di umidità assorbito dal polimero. Per questa ragione, la PA12 (con 11 gruppi metilenici per ogni gruppo carboamminico) è la poliammide che meno risente dell’assorbimento di umidità, mentre la PA4.6 (con catena monomerica corta) presenta il maggior assorbimento di umidità tra le poliammidi, con percentuale di saturazione superiore al 13%. Per contro, all’aumentare della distanza tra i gruppi CH2 e i gruppi CO-NH, le forze intermolecolari diminuiscono, provocando l’abbassamento del punto di fusione. La temperatura di fusione delle poliammidi è quindi inversamente proporzionale alla loro tendenza ad assorbire umidità (tabella 1).
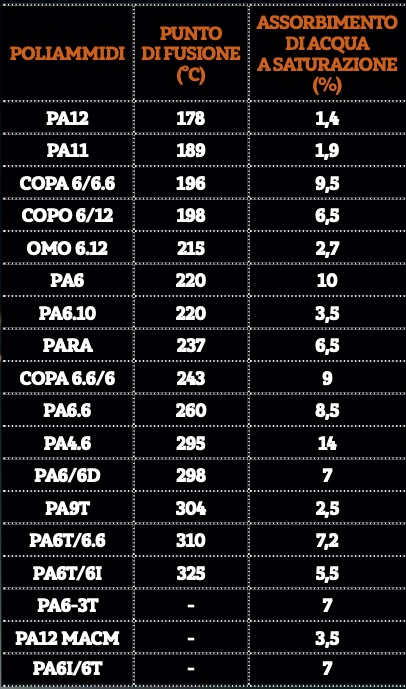
Il ritiro e il post ritiro delle poliammidi
Come tutti i materiali semicristallini, anche le poliammidi (in particolare le alifatiche) hanno un comportamento al ritiro di tipo anisotropo, cioè presentano differenti valori di ritiro parallelo e trasversale all’iniezione. Inoltre, sono soggette a un effetto di post ritiro quando esposte a temperature elevate. Durante lo stampaggio a iniezione, pertanto, è necessario tenere in considerazione questi fattori, soprattutto nel caso in cui il manufatto dovrà essere sottoposto ad alte temperature di esercizio.
È importante sottolineare che il comportamento al ritiro e al post ritiro delle diverse classi di poliammidi non è generalizzabile, perché le prestazioni di gradi simili di produttori diversi possono variare a seconda del livello di cristallinità, della presenza di agenti nucleanti, di agenti stabilizzanti al calore…
Sulla base del comportamento al ritiro di due capostipiti della famiglia delle poliammidi – PA6 e PA6.6 – è possibile delineare una linea guida per prevedere tale variabile. Come riportato nella tabella 2, il rapporto tra il ritiro totale trasversale (somma del ritiro e del post ritiro) e il ritiro totale longitudinale è poco superiore all’unità per entrambi i gradi di PA6 (base e nucleato), mentre arriva a 1,60 per il grado di PA6.6 base e 2,12 per quello di PA6.6 nucleato. Da questi valori, dunque, emerge che la PA6 ha un comportamento maggiormente isotropo rispetto alla PA6.6. Tale differenza è dovuta principalmente alla natura maggiormente amorfa della PA6, che impartisce una migliore stabilità dimensionale. In generale, si può quindi sostenere che una PA con un alto valore di cristallinità (che può variare tra il 10% e il 60%) avrà un comportamento al ritiro maggiormente anisotropo rispetto a una PA a bassa cristallinità. In fase di stampaggio a iniezione è importante non trascurare questo concetto: infatti, un materiale trasformato utilizzando uno stampo condizionato a temperature elevate (tra 80 °C e 120 °C) darà origine a un manufatto caratterizzato da una cristallinità maggiore rispetto a uno ottenuto mediante uno stampo a una temperatura inferiore a 40 °C, con il conseguente ritiro differenziato. Va sottolineato che non è mai consigliabile impostare la temperatura dello stampo a un valore simile a quello di transizione vetrosa Tg (circa 50 °C) per evitare comportamenti non facilmente prevedibili.
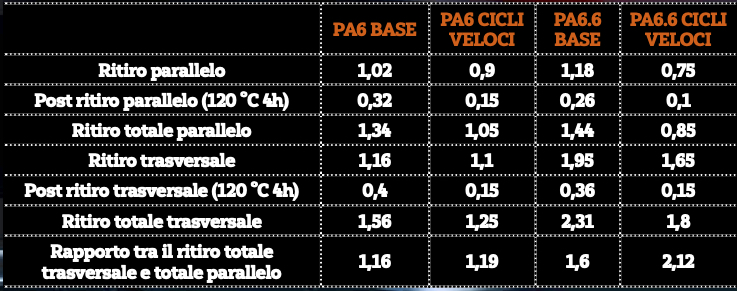
L’assorbimento di umidità
Come accennato in precedenza, la fase amorfa è responsabile della duttilità del materiale e della sua tendenza all’assorbimento di umidità, con conseguente effetto plasticizzante. In generale, una PA ad alta cristallinità assorbirà meno umidità di una PA a elevato contenuto amorfo. Basandoci su questa analisi, una PA6.6 sarà più rigida di una PA6. Analizzando i valori di modulo a trazione determinati su provini appena stampati emerge che non sono molto diversi per i due polimeri, mentre terminato il condizionamento (assorbimento di umidità controllata) i provini in PA6 mostrano una più marcata riduzione del modulo di Young rispetto a quelli in PA6.6, dovuta appunto alla maggior presenza di umidità nella fase amorfa (tabella 3).
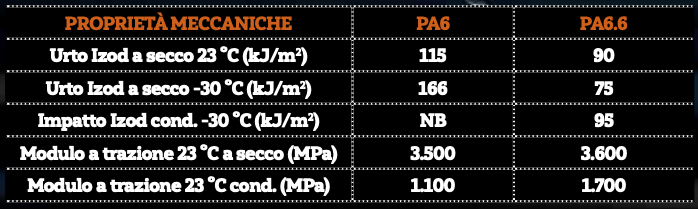
La tendenza all’assorbimento di umidità da parte della matrice è influenzata anche dalla presenza di rinforzanti. Ad esempio, un grado contenente il 30% di fibra in vetro assorbirà solo il 70% dell’umidità incorporata dal corrispettivo grado non rinforzato. Analizzando le proprietà meccaniche di tali materiali in funzione del contenuto di fibra in vetro e di umidità (figura 1) si osserva che le due poliammidi presentano modulo di Young pressoché simile allo stato secco, che diminuisce drasticamente nel corrispettivo grado condizionato. Il decadimento delle proprietà meccaniche è più pronunciato nel caso della PA6 rispetto alla PA6.6 proprio a causa del maggiore contenuto di umidità. Dal grafico emerge inoltre che è possibile ottenere gli stessi valori di modulo di Young della PA6.6 condizionata utilizzando una PA6 con un contenuto di fibra in vetro superiore del 5%. Tale aggiunta comporta tuttavia un incremento della densità della PA6 di circa il 3,5%.
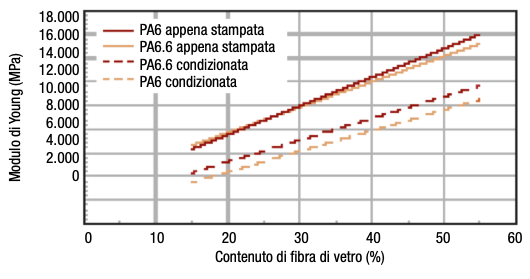
L’influenza della carica
Le proprietà del polimero sono fortemente influenzate dalla struttura monomerica di base. Abbiamo visto che all’aumentare della distanza tra i gruppi metilenici e i gruppi carboamminici le forze di interazione intermolecolari diminuiscono, con la conseguente riduzione della temperatura di fusione del polimero. Inoltre, la presenza di gruppi aromatici (nelle PPA e PARA) incrementa la temperatura di fusione del polimero. La famiglia delle poliammidi è quindi caratterizzata da temperature di fusione che partono da circa 180 °C (anche da valori inferiori per le poliammidi speciali) e raggiungono picchi anche superiori a 300 °C (tabella 1). Questo ampio intervallo ne permette l’utilizzo in differenti applicazioni tecnologiche in funzione della temperatura di esercizio. Pertanto, la scelta della poliammide adeguata a soddisfare le esigenze di un progetto specifico parte dall’analisi delle temperature di fusione e delle proprietà meccaniche alle temperature di esercizio e, conseguentemente, della stabilità termica del materiale.
Come noto, le proprietà di un polimero possono essere modificate mediante l’utilizzo di speciali additivi e stabilizzanti studiati ad hoc. Tra questi, si distinguono le nanocariche (particelle con almeno una delle dimensioni compresa tra 1 e 100 nanometri) perché, soprattutto nel caso delle PA6, permettono di ottenere prestazioni meccaniche, fisiche e reologiche di assoluto interesse. È stato infatti scientificamente dimostrato che moltissime proprietà intrinseche (conducibilità elettrica, conducibilità termica, resistenza meccanica…) aumentano notevolmente quando ci si sposta nella scala nanometrica, conferendo particolari caratteristiche al composito finale, non altresì raggiungibili tramite l’utilizzo di filler tradizionali. I principali vantaggi offerti dai nanofiller sono legati alla possibilità di ottenere la loro dispersione ottimale anche a basse concentrazioni, con la conseguente riduzione della distanza particella-particella. Inoltre, presentano maggior area interfacciale per volume di particella, alta densità di particella per volume di materiale, bassa soglia di percolazione con interazione particella-particella anche a bassa quantità di carica (inferiore al 5% per la PA6).
I vantaggi dei nanofiller
Le nanocariche si differenziano in base a forma e dimensione, e possono essere classificate come lamellari, fibrose, sferoidali e cilindriche. Le nanoparticelle maggiormente utilizzate a livello industriale e a scopo di ricerca per la fabbricazione di nanocompositi a matrice polimerica sono le argille modificate organicamente (ad esempio, montmorillonite organoclays o MMT), le nanofibre e i nanotubi di carbonio, gli ossidi metallici in dimensione nanometrica (ad esempio, TiO2 e Al2O3) e altre nanocariche, come nanografite, grafene e nanosilice. Una volta individuata la matrice adeguata all’applicazione, lo sviluppo del materiale nanocomposito ottimale deve superare alcune criticità. In particolare, è necessario ottenere una buona compatibilità e/o interazione interfacciale tra la nanoparticella e la matrice polimerica, e quindi sviluppare una tecnica di produzione capace di disperdere in modo uniforme e omogeneo le nanoparticelle all’interno della matrice. Tutto questo senza dimenticare che anche la quantità di nanoparticelle gioca un ruolo significativo nelle proprietà del nanocomposito finale.
Generalmente, i materiali inorganici non hanno una buona interazione con le molecole organiche, pertanto è necessario intervenire sulle nanoparticelle con dei trattamenti superficiali. Filler inorganici, come la montmorillonite, presentano una struttura lamellare a più strati (multi layer) dove ogni layer è caratterizzato da uno spessore nanometrico e dimensione laterale che possono arrivare fino al millimetro. Per ottimizzare l’interazione particella-molecola, i cationi presenti sulla superficie della specie inorganica (tipicamente ioni sodio) vengono scambiati chimicamente con molecole organiche contenenti gruppi cationici (generalmente gruppi amminici quaternari) con conseguente incremento della distanza layer-layer. I materiali così ottenuti, detti organo-clay, hanno una miglior affinità con le molecole polimeriche e in particolare con le poliammidi, in virtù della presenza dei gruppi amminici. Le macromolecole possono così penetrare all’interno delle particelle, con conseguente esfoliazione e formazione di materiali nanocompositi con caratteristiche meccaniche, reologiche e a barriera notevolmente migliorate, anche rispetto a un materiale altamente caricato.
Stabilità dimensionale e assenza di deformazione
I ricercatori del Gruppo Maip, negli anni, hanno sviluppato una nuova generazione di poliammidi caricate con nanoparticelle – la linea Nanil – in grado di sostituire materiali come la PA6 rinforzata con fibre o carica minerale, ottenendo un importante alleggerimento del manufatto stampato, mantenendo al contempo inalterata la resistenza termica. Analizzando le proprietà meccaniche di compound caricati con basse percentuali di nanomateriale, si nota che raggiungono valori di allungamento a trazione decisamente superiori rispetto a un’analoga PA6 rinforzata con elevate quantità di carica minerale, e che presentano valori di sforzo a trazione e flessione simili a fronte di una resistenza all’urto superiore (tabella 4).
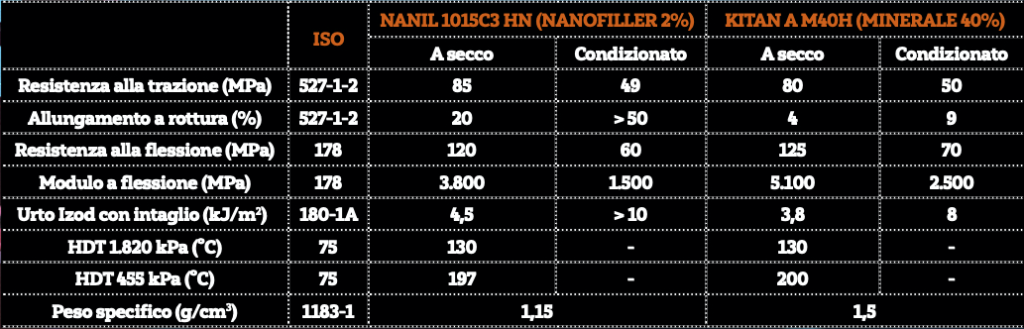
Come evidenziato in precedenza, le poliammidi presentano un forte ritiro asimmetrico con conseguente deformazione del pezzo stampato. Le PA6 nanocomposite, invece, evidenziano una migliore stabilità dimensionale e assenza di deformazione. Inoltre, il loro coefficiente di espansione termica lineare, nell’intervallo di temperatura tra -30 °C e +80 °C, varia da 67 a 78 x 10-6 mm/K rispetto a valori tipici della PA6 di circa 100-110 x 10-6 mm/K, garantendo quindi una miglior stabilità dimensionale del pezzo durante il suo ciclo vita. La migliore stabilità dimensionale è anche dettata da un minor assorbimento di umidità da parte delle poliammidi nanocomposite, che, in determinate composizioni, può arrivare anche al 30-35% in meno rispetto a una PA6 tradizionale.
Migliori proprietà reologiche
Contrariamente al normale andamento dei polimeri rinforzati, i nanocompositi mostrano migliori proprietà reologiche. Una delle tecniche più utilizzate per valutare la fluidità di un compound è lo stampaggio a iniezione all’interno di uno stampo a spirale. Maggiore è la fluidità, maggiore sarà il percorso compiuto dal materiale all’interno dello stampo. Confrontando le prestazioni di una PA6 e della stessa caricata con il 30% di fibra in vetro e con il 5% di nanofiller emerge che le nanoparticelle disperse non influiscono sulla fluidità della matrice al contrario delle fibre di vetro, che riducono il percorso del compound di 2-3 volte rispetto agli altri due casi. L’analisi del melt flow rate (MFR, indice di fluidità) evidenzia invece che il valore relativo a una normale PA6 diminuisce da 110-150 g/10 min fino a 40-50 g/10 min quando viene rinforzata con il 15% di fibra in vetro. La stessa PA6 caricata con nanofiller presenta invece valori di MFR che possono arrivare fino a 200 g/10 min. A livello applicativo, l’elevata fluidità permette di ridurre quasi al limite lo spessore della parete dei componenti, a vantaggio dell’alleggerimento, ma anche di ottenere una miglior riproduzione della texture superficiale dello stampo, migliorando l’aspetto estetico. In funzione della finitura dello stampo sarà quindi possibile realizzare manufatti con superficie glossy, goffrata o con effetti particolari, evitando così la necessità di verniciatura e di altri trattamenti secondari con conseguente cost saving.
Scarica il pdf dell’articolo pubblicato su Plastix di giugno
Più resistenti agli UV
È ben noto che tutti i filler tendono ad assorbire parzialmente gli additivi inseriti nel compound (ad esempio, gli stabilizzanti agli UV) limitandone la capacità protettiva. L’inconveniente risulta più marcato in presenza di nanocariche in virtù della superficie più elevata. La maggior parte degli studi sperimentali riporta che la presenza di nanoclay di montmorillonite diminuisce l’efficienza dei convenzionali stabilizzanti agli UV a causa non solo dell’interazione tra questi due composti, ma anche dell’effetto catalitico promosso dalle impurità metalliche presenti nei nanomateriali. Inoltre, la fotodegradazione dei gruppi amminici presenti negli organoclay accelera i processi di degradazione del polimero, rendendo di fatto impossibile l’impiego di questo tipo di cariche nelle applicazioni che richiedono un’elevata stabilità agli UV.
Partendo da un normale stabilizzante agli UV per poliammidi, attraverso un’accurata sperimentazione per individuare il giusto mix tra additivi e parametri di processo, i ricercatori del Gruppo Maip sono riusciti a sviluppare speciali gradi di PA nanocomposite capaci di superare i più severi test SAE J 2425 per esterni, dimostrando la piena compatibilità con le applicazioni legate alla componentistica per l’esterno dell’autovettura. Le prove prevedono l’impiego di una luce allo xeno per simulare l’invecchiamento accelerato all’esposizione della luce solare in continuo; la radiazione totale irradiata è pari a 2.500 KJ/m3 per una durata di 1.894 ore.
Permeabilità ai gas e resistenza alla fiamma
Un’altra caratteristica rilevante dei nanocompositi è la scarsa permeabilità ai gas (O2, CO2…) e ai liquidi, essenzialmente imputabile alla tortuosità del percorso che una molecola deve compiere per attraversare il materiale. Lo stesso meccanismo è responsabile anche delle proprietà di resistenza alla fiamma. I metodi più utilizzati per valutare il comportamento al fuoco dei polimeri plastici sono il cono calorimetrico, la misura del minimo quantitativo di ossigeno disponibile per supportare la combustione (limit oxigen index LOI) e i test UL-94. Tra questi, il cono calorimetrico è giudicato il più attendibile e riproducibile.
Diversi studi compiuti tramite il cono calorimetrico rivelano una miglior resistenza alla fiamma dei nanocompositi associata alla diminuzione di calore rilasciato a seguito della combustione (heat release rate). Quando una matrice polimerica viene riscaldata genera composti volatili che, a contatto con l’ossigeno sulla superficie dell’oggetto, prendono fuoco. La combustione attiva la formazione di una crosta carboniosa molto compatta, detta “char”, che agisce come una barriera protettiva riducendo gli scambi gassosi del comburente (ossigeno) con il combustibile. Le nanoparticelle disperse all’interno del polimero, invece, inibiscono la diffusione di specie radicaliche volatili e inoltre promuovono la ricombinazione polimerica, con la formazione di “nuove” catene. Nonostante questo, i polimeri nanocaricati non hanno effetto di autoestinguenza, pertanto è sempre necessario aggiungere un’adeguata percentuale di ritardanti di fiamma convenzionali.
Nano e anche green
Rispetto a quanto si è portati a pensare, i materiali nanocompositi possono essere definiti “green” in termini sia di economicità, sia di ecosostenibilità. Una tipica poliammide rinforzata con carica minerale o fibra di vetro utilizzata in applicazioni automotive da sottocofano è caratterizzata da un peso specifico variabile tra 1,36 e 1,55 g/cm3. I tecnici del Gruppo Maip sono riusciti a ridurre il peso specifico di alcuni gradi speciali di poliammidi nanocomposite a 1,15 g/cm3 (fino a 25% in meno), mantenendo inalterate le proprietà termiche e meccaniche del manufatto finale. Tale caratteristica, unita alla maggior fluidità tipica della linea Nanil – come già accennato – permette di ridurre lo spessore dei componenti, con ovvi benefici sulla riduzione del peso dei veicoli e sull’estetica.
Attualmente, questi speciali gradi di PA nanocomposite vengono utilizzati in differenti applicazioni automotive, ad esempio le mostrine dello scarico caldo sul paraurti posteriore o la cover del motore. In queste situazioni i materiali hanno dimostrato la capacità di soddisfare gli stringenti requisiti di stabilità dimensionale e termica, di inerzia chimica, nonché le proprietà estetiche, reologiche e di processo richieste dall’applicazione finale, riducendo al contempo il peso del manufatto fino al 25%. Grazie alla dispersione ottimale delle nanoparticelle all’interno della matrice polimerica, questa linea di nanocompositi presenta proprietà superiori e/o migliorate rispetto ai polimeri di base e ai compositi convenzionali, tra cui minor peso specifico, migliori proprietà fisico-meccaniche e barriera, ma anche migliore stabilità termica e al ritardo di fiamma. È però da sottolineare che queste proprietà vengono migliorate tramite l’aggiunta di concentrazioni ridotte di un solo filler nanometrico, che quindi agisce come un additivo multifunzionale.
Scarica il pdf dell’articolo pubblicato su Plastix di giugno