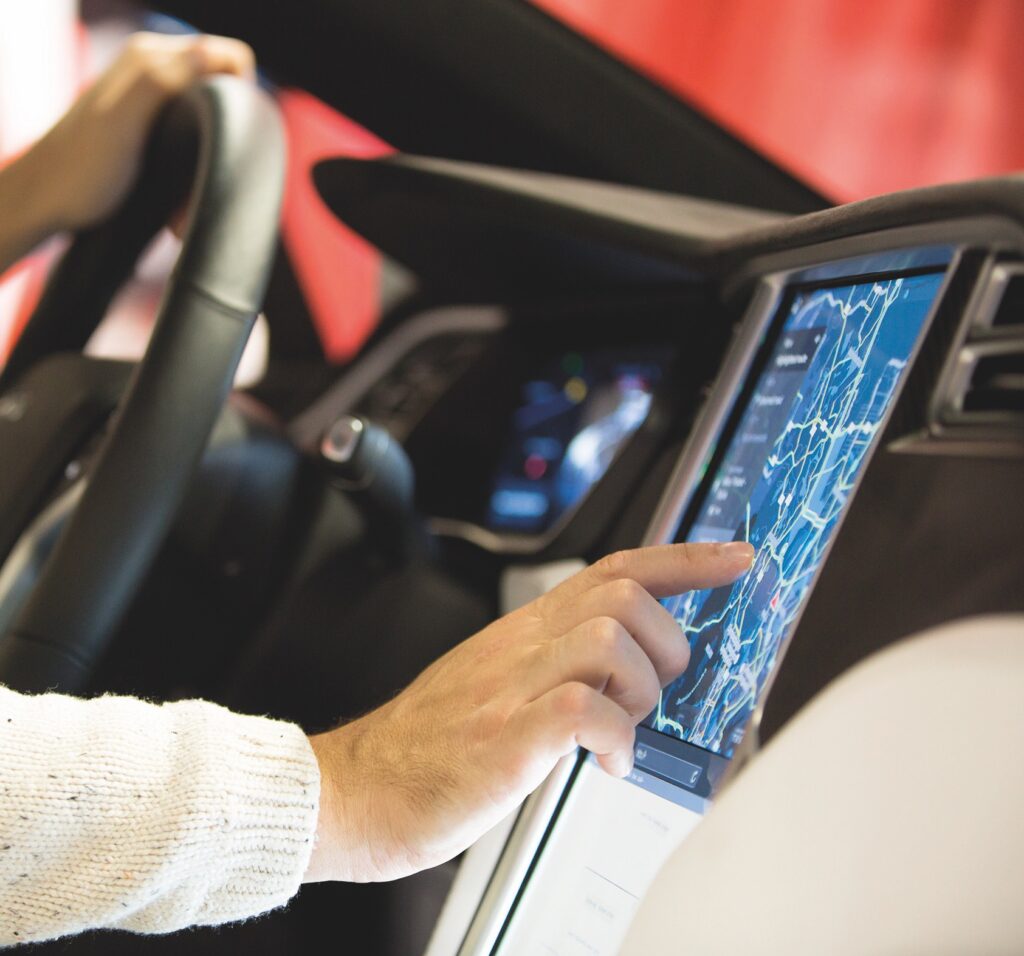
La maggior parte dei componenti degli interni dei veicoli viene realizzata con materie plastiche o compositi metallo-plastica che richiedono un accurato trattamento superficiale per ottenere incollaggi e rivestimenti resistenti nel tempo. E, considerati i volumi di produzione, è fondamentale disporre di processi rapidi, efficienti ed economici per ottenere il risultato. La tecnologia al plasma è una soluzione possibile perché, oltre a superare molti degli svantaggi legati ai trattamenti superficiali tradizionali, permette di creare legami adesivi molto forti anche tra materiali ritenuti del tutto o in parte incompatibili, offrendo così opportunità inedite ai car designer.
I trattamenti fiamma, ad esempio, tradizionalmente utilizzati per aumentare l’energia superficiale dei manufatti in plastica, presentano effetti indesiderati come la deformazione, soprattutto sulle sezioni a pareti sottili, oppure il danneggiamento della superficie lucida di alcune resine. Dal punto di vista operativo, invece, richiedono laboriose procedure per proteggere le aree che non devono essere sottoposte al trattamento, mentre una sovraesposizione può compromettere le proprietà adesive finali. Gli svantaggi legati ad altri trattamenti convenzionali quali i promotori di adesione a solvente (primer) riguardano invece l’emissione in atmosfera di composti organici volatili dannosi per l’ambiente.
Adesione ottimale
Requisito fondamentale per ottenere un’adesione ottimale è la perfetta pulizia delle superfici in plastica seguita dall’attivazione per aumentarne la bagnabilità. Il trattamento al plasma permette di ottenere ottimi risultati in entrambe le situazioni.
Il flusso di atomi e ioni attivati che compone il plasma (si veda il riquadro) si comporta come una sabbiatura in grado di frantumare le particelle organiche contaminanti, che vengono nuovamente vaporizzate durante la lavorazione. La maggior parte di questi sottoprodotti consiste in piccole quantità di gas, quali biossido di carbonio e vapore acqueo, contenenti tracce di monossido di carbonio e altri idrocarburi. Oltre a pulire rimuovendo gli agenti contaminanti, il plasma attiva anche la superficie di molti materiali plastici perché ne modifica la composizione chimica sostituendo molecole relativamente inerti con particelle più reattive. Ciò incrementa l’energia superficiale complessiva, riuscendo a migliorare l’adesione. La rimozione completa o meno del materiale organico può essere valutata misurando l’angolo di contatto. In presenza di particelle organiche contaminanti, infatti, l’angolo di contatto tra l’acqua e il dispositivo risulta elevato. Una volta rimosso il materiale contaminante, l’angolo di contatto si riduce fino a risultare pari al valore caratteristico misurato per il contatto con il solo substrato. L’energia UV è in grado di spezzare efficacemente la maggior parte dei legami chimici organici (ovvero C–H, C–C, C=C, C–O e C–N) tipici degli agenti che contaminano la superficie dei manufatti.
Un secondo meccanismo di pulizia viene messo in atto dalle particelle di ossigeno che si vengono a creare all’interno del plasma, che reagiscono con gli agenti contaminanti organici formando CO, CO2, H2O e idrocarburi a basso peso molecolare. La tensione di vapore di questi composti organici consente loro di sfuggire al processo, lasciando una superficie sensibilmente più pulita.
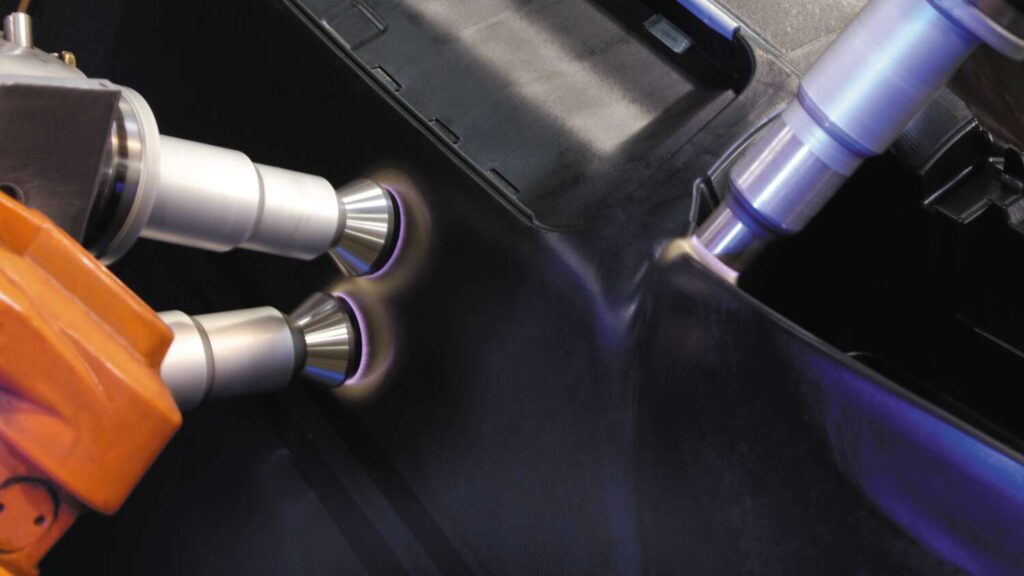
Il plasma a pressione atmosferica
In passato, quando veniva utilizzato per il trattamento superficiale di componenti industriali, il plasma era impiegato quasi sempre a bassa pressione. Ciò significa che i componenti dovevano essere trattati in una camera a bassa pressione (plasma in vuoto), separata dalla linea di produzione principale. Di conseguenza, il processo si rivelava molto dispendioso in termini di tempo ed era poco adatto per il trattamento di parti di grande volume. Lo sviluppo della tecnologia Openair-Plasma, avvenuta negli anni Novanta da parte del CEO di Plasmatreat dr. Christian Buske, ne ha permesso l’integrazione nelle linee di produzione, perché – operando a pressione atmosferica – non richiedeva più il confinamento dei componenti all’interno di camere a bassa pressione.
Oggi, molte case automobilistiche e i loro fornitori si avvalgono della tecnologia Openair-Plasma e Plasma-Plus per la pulizia, l’attivazione e la funzionalizzazione chimica delle superfici di componenti da assemblare per interno o esterno vettura, riuscendo così a produrre parti di qualità più elevata. L’intensità dell’attivazione ottenuta con il plasma, infatti, può essere adattata con precisione alle esigenze della singola applicazione e un simile livello di controllo consente di creare le condizioni ottimali per assicurare un forte legame adesivo tra due superfici da assemblare. È proprio questo uno degli aspetti che distinguono il plasma dai trattamenti superficiali che utilizzano primer, che invece non consentono alcun controllo. Il processo, inoltre, è più snello, economico e sostenibile in virtù del risparmio su prodotti chimici e altri ausiliari.
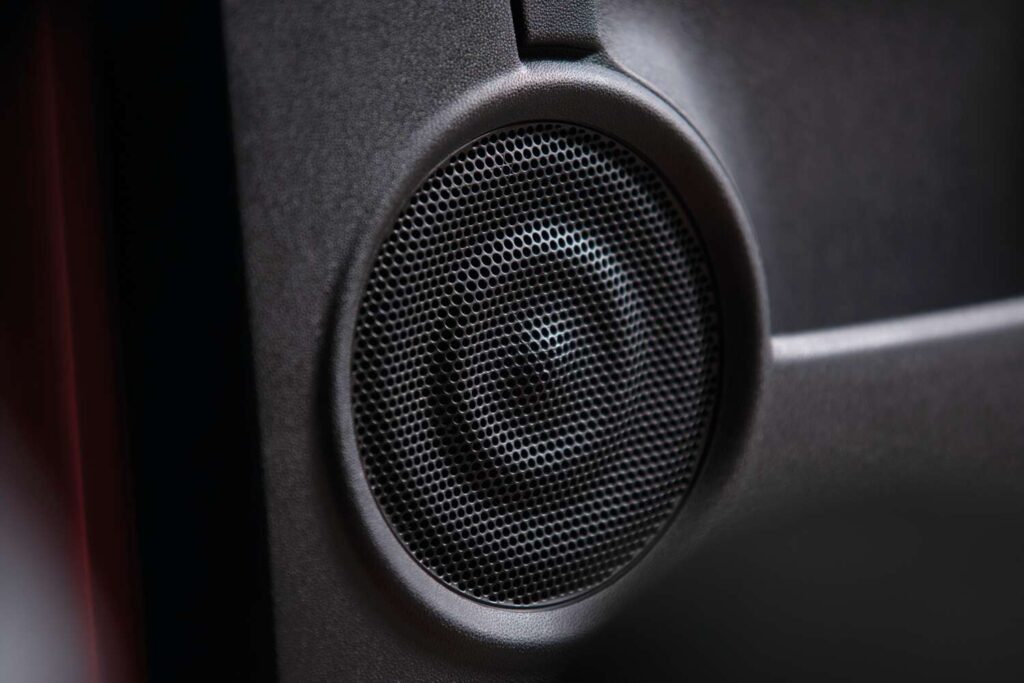
Processi più affidabili
I sistemi Openair-Plasma offrono un’ottima affidabilità e stabilità del processo, perché possono essere dotati di un triplice monitoraggio che assicura una protezione ottimale contro i guasti. In particolare, durante le fasi di trattamento, un sensore ottico rileva la presenza del plasma nell’ugello e analizza in continuo lo spettro della luce emessa dal plasma stesso, nell’intervallo operativo del sistema. Un rilevatore di movimento, invece, monitora la rotazione dell’ugello assicurando l’affidabilità del processo produttivo e una qualità costante del prodotto. Infine, il monitoraggio dell’alimentazione del plasma assicura la riproducibilità dei parametri specifici del processo (potenza e intensità del plasma), elementi indispensabili per ottenere la massima qualità del trattamento nelle produzioni di massa su scala industriale. Per questa ragione Plasmatreat ha sviluppato unità di monitoraggio adatte a tutte le applicazioni.
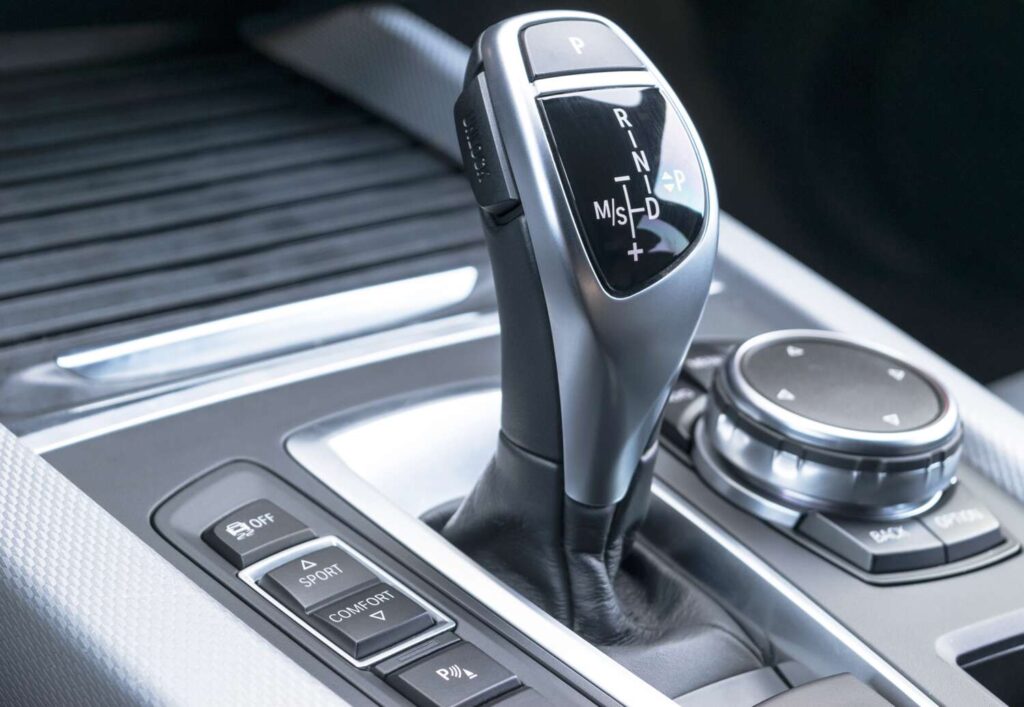
Superfici perfettamente pulite
Altoparlanti, display, tessuti, decorazioni in pelle e comandi sono solo alcune delle finiture per interni auto che richiedono lavorazioni di incollaggio e verniciatura resistenti nel tempo. Nella produzione di display, ad esempio, per migliorare l’effetto della retroilluminazione e ridurre significativamente i riflessi si ricorre alla tecnologia di optical bonding. Il processo prevede l’applicazione di un adesivo bicomponente in silicone trasparente (RTV) al display in polimetilmetacrilato (PMMA) secondo uno schema predefinito e utilizzando uno speciale sistema di dosaggio. Nella realizzazione di altoparlanti, invece, è importante ottenere un assemblaggio dell’alloggiamento e della membrana resistente nel tempo. La pulizia accurata delle superfici rappresenta un requisito essenziale anche per il successivo rivestimento e stampa di elementi di comando come gli interruttori. In caso contrario, non vi sarebbe alcuna garanzia che il rivestimento o gli inchiostri da stampa aderiscano in modo affidabile alle superfici.
Micropulizia per giunzioni resistenti nel tempo
Il processo Openair-Plasma offre prestazioni interessanti anche nelle operazioni di pulizia profonda delle superfici o micropulizia. In particolare, l’elevato livello di energia del plasma frammenta in modo mirato la struttura delle sostanze di qualunque natura presenti sulla superficie del materiale. Inoltre, l’effetto deionizzante del fascio del plasma neutralizza le particelle di polvere e le rimuove dalla superficie. La micropulizia consente di ottenere superfici definite con precisione, che garantiscono un’applicazione impeccabile di adesivi e rivestimenti. A differenza di altri processi come la sabbiatura, il plasma deterge il materiale a livello strutturale senza richiedere reagenti di consumo necessari per altri processi di pulizia, poiché il processo si basa esclusivamente sull’utilizzo di aria compressa ed elettricità.
L’attivazione incrementa la capacità adesiva
Durante la pulizia viene contemporaneamente attivata la superficie del materiale. L’attivazione aumenta l’energia superficiale, migliorandone le caratteristiche adesive. Un aspetto, questo, particolarmente importante per le plastiche utilizzate negli interni dei veicoli, poiché trattandosi in prevalenza di materiali apolari risulterebbero molto difficili da incollare o rivestire. Durante l’attivazione al plasma, i gruppi funzionali contenenti ossigeno o azoto incorporati nella matrice polimerica determinano un aumento dell’energia superficiale dei materiali trattati. La bagnabilità viene significativamente migliorata quando l’energia superficiale del materiale solido è superiore a quella del liquido applicato (ad esempio, adesivo o vernice).
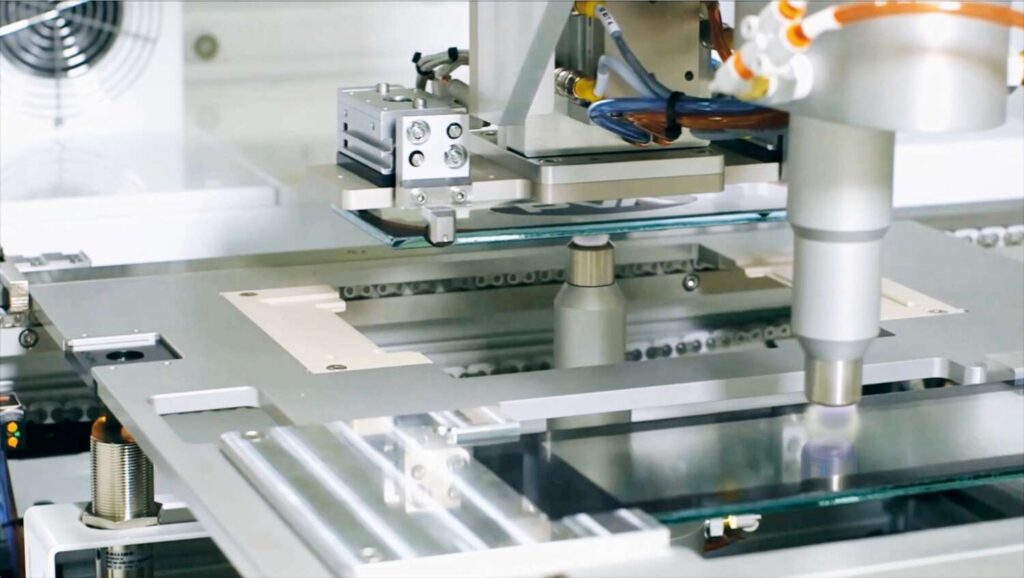
Una tecnologia sostenibile
L’attivazione mediante il processo Openair-Plasma fissa i radicali liberi alla superficie del materiale, prevenendo anche la formazione di bolle nello strato di adesivo che può verificarsi utilizzando le tecnologie tradizionali e che, nel caso specifico, impedisce l’incollaggio ad alta adesione del modulo LCD e del display o dello schermo protettivo. Inoltre, diversamente dai trattamenti superficiali con prodotti chimici, la pulizia e l’attivazione al plasma non causano rotture da stress chimico.
Nella produzione di altoparlanti, ad esempio, il plasma elimina la necessità di ricorrere ai primer chimici a solvente, più costosi e dannosi per l’ambiente. Una delle soluzioni per garantire un’adesione affidabile della vernice sui comandi auto è la pulizia preventiva mediante ghiaccio secco (CO2). Anche in questo ambito la tecnologia al plasma offre ai car maker interessanti vantaggi, come un livello qualitativo più elevato, una maggiore economicità e la possibilità di sostituire le vernici a solvente con quelle a base d’acqua.
Rivestimenti funzionali
Oltre ai sistemi per la pulizia e l’attivazione delle superfici, Plasmatreat offre la tecnologia di rivestimento PlasmaPlus. Il sistema deposita sulle superfici strati funzionali, ad esempio con proprietà anticorrosione sui metalli oppure con funzionalità chimica idonea a promuovere l’incollaggio delle plastiche o dei componenti ibridi metallo-plastica. Molte case automobilistiche e i loro fornitori hanno già riconosciuto il potenziale di questa tecnologia.
Industry 4.0 ready
Le proprietà superficiali dei rivestimenti funzionali possono essere adattate a tutte le applicazioni. I trattamenti al plasma offrono numerosi vantaggi all’industria automobilistica e ai loro fornitori in quanto semplificano i processi, riducono i costi di produzione e proteggono l’ambiente. Inoltre, questi trattamenti possono essere completamente automatizzati e integrati nelle linee di produzione esistenti. I componenti di sistema, sapientemente abbinati, e la trasmissione dei dati di processo tramite interfacce aperte offrono ampie opportunità per il controllo e la tracciabilità dei processi.