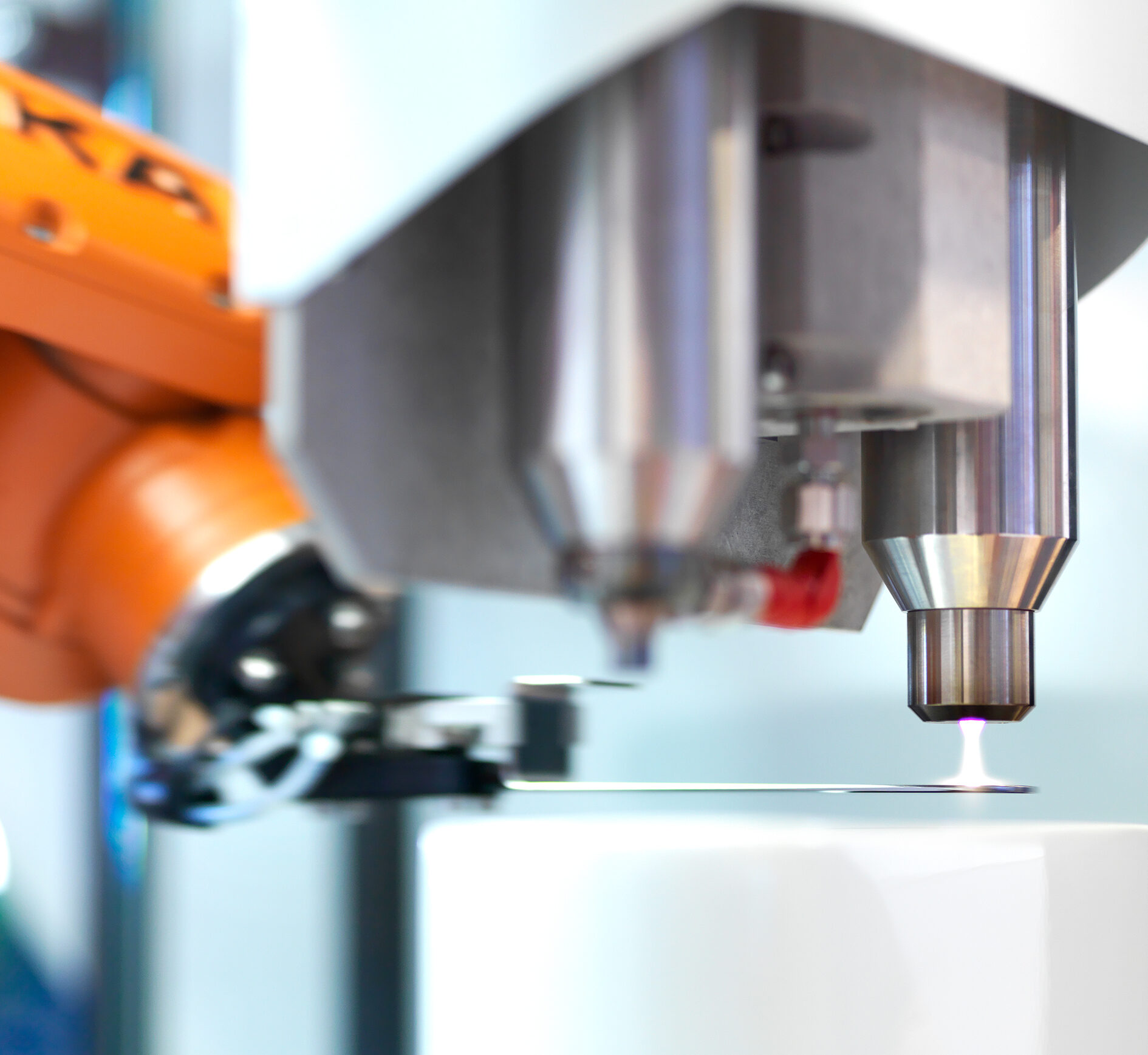
Molte applicazioni industriali richiedono l’incollaggio permanente di materiali e componenti diversi, con una tenuta tale da non compromettere la funzionalità del manufatto e da assicurare la protezione dagli agenti atmosferici. Questi risultati si possono ottenere funzionalizzando le superfici, un processo che comporta una modifica fisica e chimica della superficie stessa che consente di ottenere le proprietà desiderate. I fattori che influenzano il cambiamento sono da un lato la natura dei materiali e le caratteristiche dei componenti, dall’altro le sostanze che compongono i substrati, gli adesivi e i sigillanti. Il fattore determinante per ottenere l’adesione desiderata è dato dalla funzionalizzazione del substrato e dall’energia superficiale misurata (mN/m) che, in linea di principio, per il materiale da bagnare dovrebbe essere superiore a quella della sostanza bagnante. Nello specifico, l’energia superficiale dipende dall’interazione tra le molecole disperse e polari, la cui proporzione modifica completamente il risultato del contatto di un solido con liquidi diversi. Idealmente, per ottenere la bagnatura ottimale della superficie, il limite di fase di due materiali dovrebbe presentare in uguali proporzioni componenti disperse e polari.
Al contrario del vetro e dei metalli, le plastiche apolari non possiedono di natura un’elevata energia superficiale e pertanto sono difficilmente bagnabili. La bagnabilità delle plastiche rigenerate è generalmente diversa rispetto a quella delle resine vergini, poiché nel processo di riciclo possono verificarsi fenomeni di degradazione chimica o contaminazioni che ne alterano le proprietà.
La scelta del primer
Se l’energia libera della superficie del materiale da bagnare non è sufficiente, generalmente si ricorre all’impiego di agenti di accoppiamento (primer), anche se la procedura presenta svantaggi significativi. L’applicazione del primer richiede sempre la pulizia del substrato, seguita dall’applicazione del composto adesivo o sigillante, allungando inevitabilmente il tempo ciclo. A questo inconveniente si aggiungono le criticità nella gestione dei primer che, essendo a base di solvente, rappresentano una sfida in termini di stoccaggio e sicurezza nei luoghi di lavoro. Non solo. Anche la riclassificazione delle materie prime (ad esempio, in base al regolamento REACh) comporta spesso l’applicazione di norme più severe sull’etichettatura e quindi costi di gestione più elevati per i primer. Molto spesso, però, la sostituzione degli agenti di accoppiamento a base solvente con quelli ad acqua non è la soluzione ottimale: infatti, i primer all’acqua presentano svantaggi significativi a livello di processo a causa dei tempi di asciugatura più lunghi e della scarsa bagnabilità.
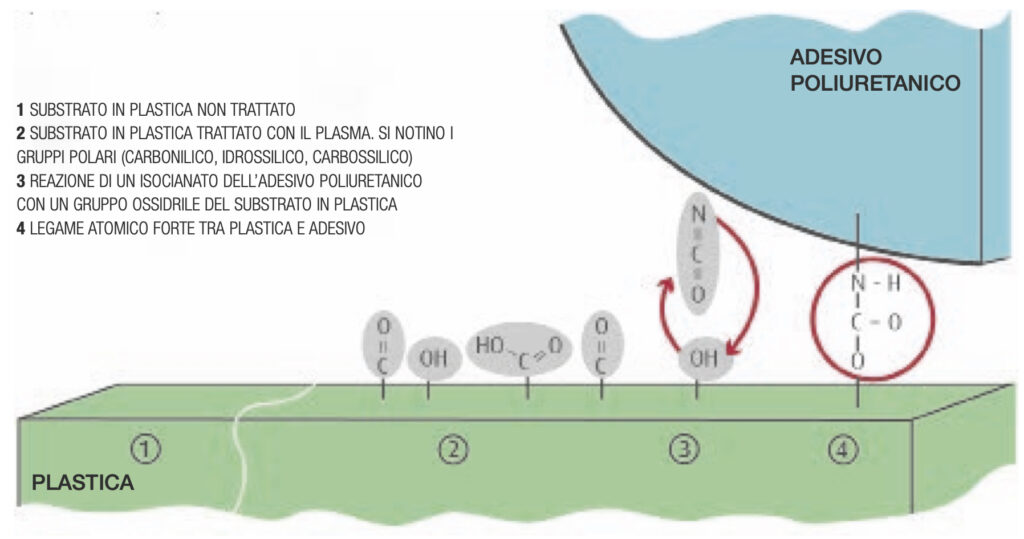
Il plasma a pressione atmosferica
Sebbene i primer rappresentino ancora la scelta prevalente quando è necessario creare giunzioni stabili nel tempo combinando materiali critici, le aziende stanno gradualmente abbandonando gli agenti di accoppiamento convenzionali a favore dei trattamenti al plasma a pressione atmosferica per motivi di produttività, costi e impatto ambientale. La tecnologia Openair-Plasma proposta da Plasmatreat, ad esempio, aumenta la bagnabilità delle superfici e l’adesione, consentendo così l’uso di materiali più convenienti e nuove combinazioni di materiali senza compromettere la qualità del prodotto finale: un vantaggio competitivo decisivo.
Il trattamento al plasma viene effettuato a secco e senza contatto, è selettivo e molto rapido. La superficie viene pulita con precisione e contemporaneamente attivata a livello molecolare in un unico passaggio. Totalmente compatibile con l’impiego di robot in linea, la tecnologia permette di ridurre l’incidenza della manodopera, quindi di errori, e al contempo di migliorare la produttività con una ricaduta positiva sui costi. A prescindere che si tratti di incollaggi strutturali in ambito automotive, sigillatura di componenti elettronici o etichettatura rapida a umido senza bolle d’aria con un’elevata resistenza iniziale, grazie al trattamento Openair-Plasma e ai moderni sistemi adesivi senza solventi oggi i processi di produzione possono essere eseguiti senza alcun spreco di prodotti chimici. Questo vale anche per la stampa e la verniciatura, perché l’elevata energia superficiale generata dal plasma garantisce una distribuzione uniforme della vernice e un ancoraggio ottimale.
Nanodeposizione di rivestimenti
In situazioni critiche o per soddisfare esigenze specifiche, le superfici dei materiali vengono rivestite ricorrendo a PlasmaPlus. Uno dei vantaggi più significativi consiste nel fatto che con i nano-rivestimenti generati con questa tecnologia è possibile funzionalizzare le superfici dei materiali più diversi quali, materie plastiche, vetro, acciaio, alluminio e tessuti con coating di varia natura chimica, che consentono di raggiungere prestazioni ad alto contenuto di innovazione. La tecnologia PlasmaPlus prevede l’introduzione del materiale di rivestimento (precursore) direttamente nell’ugello del plasma e rende possibili processi in linea a velocità irraggiungibili rispetto a quelli convenzionali con agenti di accoppiamento, riducendo al minimo l’impiego di sostanze chimiche.
Questa tecnologia offre due vantaggi chiave: il consumo è generalmente limitato a pochi grammi l’ora e, direttamente dopo il trattamento, è possibile effettuare ulteriori lavorazioni come la sigillatura, l’incollaggio e lo stampaggio a iniezione. Infine, vengono eliminati i tempi di attesa per l’evaporazione o l’asciugatura del primer.
Trattamento di più materiali con un solo impianto
Non importa quale sia il materiale del substrato, perché per creare un legame adesivo forte per mezzo del plasma viene modificata solo l’interfaccia del substrato. A differenza dei primer, l’intensità della variazione può essere controllata con grande precisione e questo significa che, semplicemente selezionando i parametri, è possibile trattare un’ampia varietà di materiali con un unico impianto: dai metalli, sui quali si utilizza plasma a elevata intensità ed energia, alle plastiche sensibili al calore, che richiedono meno energia. Inoltre, il processo di rivestimento PlasmaPlus consente di selezionare i precursori chimici più adatti ai singoli substrati. L’esperienza acquisita nella funzionalizzazione con il plasma di superfici in plastica, metallo o vetro può essere sfruttata in un’ampia varietà di applicazioni. Analogamente, funzionalizzazioni già note come idrofobia, idrofilia o adesione possono essere adattate a materiali nuovi partendo dalle applicazioni esistenti. Ed è proprio questa opportunità a rendere il plasma a pressione atmosferica così efficiente. Alcuni esempi illustrati nel seguito dimostrano l’ampiezza delle possibili applicazioni e processi al plasma.

Produzione di componenti elettronici
Il segmento emergente della mobilità elettrica e la conseguente integrazione di display touch, sistemi di sicurezza, sensori e telecamere hanno determinato un significativo incremento del numero di applicazioni che richiedono adesivi e sigillanti. Per garantire che i delicati componenti elettronici hi-tech funzionino in modo affidabile, è necessario preservarli dagli agenti esterni, come polvere e umidità. Il trattamento con Openair-Plasma rappresenta la soluzione ottimale per la protezione dalle condizioni ambientali e la compatibilità elettromagnetica (CEM), e per assicurare una giunzione stabile – e quindi la tenuta – tra l’alloggiamento in metallo o plastica.
Il plasma offre notevoli vantaggi anche nell’assemblaggio di display e interfacce operatore mediante incollaggio ottico. Oltre a rimuovere completamente tutte le impurità residue o le contaminazioni che si verificano nel corso del processo di produzione, al contempo innesca il processo di attivazione, grazie al quale i radicali liberi si legano alla superficie del materiale. In questo modo si garantisce l’incollaggio senza bolle d’aria dei componenti, poiché l’aumento della tensione superficiale consente di distribuire perfettamente l’adesivo liquido trasparente sulla superficie del vetro.
Un altro importante campo di applicazione della tecnologia Openair-Plasma nel comparto elettronico è il conformal coating, ovvero la sigillatura a tutta superficie di singoli componenti o perfino di interi gruppi di assemblaggio. Il processo di applicazione del conformal coating non è del tutto esente da inconvenienti, in quanto molte variabili possono esercitare un impatto negativo sulla qualità finale del rivestimento. Tra queste si segnalano la formazione di bolle o l’effetto buccia d’arancia, irregolarità e fenomeni di delaminazione. Il trattamento al plasma permette di ottenere superfici molto pulite e altamente attive, consentendo così la creazione di un legame stabile tra la superficie e il materiale di rivestimento.
Stampaggio bicomponente rigido-morbido
Per soddisfare i crescenti requisiti di funzionalità nelle applicazioni industriali, i componenti tecnici in plastica sono spesso realizzati con diversi materiali. Il binomio rigido-morbido è particolarmente richiesto, ad esempio, per manici di attrezzi o pannelli degli interni delle automobili. Se la combinazione dei diversi polimeri plastici avviene mediante stampaggio a iniezione multicomponente, per ottenere un legame adesivo è necessario che i materiali siano termicamente compatibili. Questo limita la scelta dei materiali, spesso con compromessi in termini di proprietà del componente morbido.
L’attivazione superficiale con plasma a pressione atmosferica, un processo ormai consolidato nella lavorazione delle materie plastiche, ha contribuito ad ampliare la gamma delle possibilità, riuscendo a legare stabilmente materiali precedentemente ritenuti incompatibili. Il processo InMould-Plasma compie un ulteriore passo avanti in questa direzione, con l’integrazione del trattamento al plasma direttamente nello stampo a iniezione. Vengono così eliminati i processi di assemblaggio manuali, anche i più complessi, spesso soggetti a errori. Un tipico esempio delle potenzialità della tecnologia è lo stampaggio di un coperchio in polipropilene (PP) con guarnizione in poliuretano termoplastico (TPU) prodotto con uno stampo rotazionale a tre stazioni. Il coperchio in PP viene stampato nella prima stazione e quindi trasferito nella seconda, dove è installata la sorgente plasma all’interno dello stampo. Quando lo stampo si chiude, l’impronta sul lato dell’ugello preme sul coperchio e isola una scanalatura sulla superficie, sulla quale successivamente viene iniettato il componente morbido. Il getto di plasma entra in funzione e il plasma scorre attraverso la scanalatura, attivando solo una precisa area del coperchio. Come gas di processo viene utilizzato l’azoto, che garantisce un’attivazione altamente efficace della superficie in plastica. Il processo richiede solo pochi secondi, quindi generalmente non influisce sul tempo ciclo. Terminato il trattamento al plasma, viene iniettato il componente elastomerico. Ogni volta che lo stampo si apre, viene estratto un coperchio bicomponente finito.
Senza trattamento al plasma, i compositi PP-TPU non potrebbero sviluppare proprietà adesive ottimali, in grado di resistere nel tempo. InMould-Plasma è efficace anche nell’incollaggio di elastomeri termoplastici, come TPE-S e TPE-V, a tecnopolimeri termoplastici come PC, PBT e PBT/ASA. Oltre alla possibilità di realizzare combinazioni di materiali inedite, la tecnologia permette di ridurre i tempi e i costi di produzione a fronte di un miglior controllo di processo.
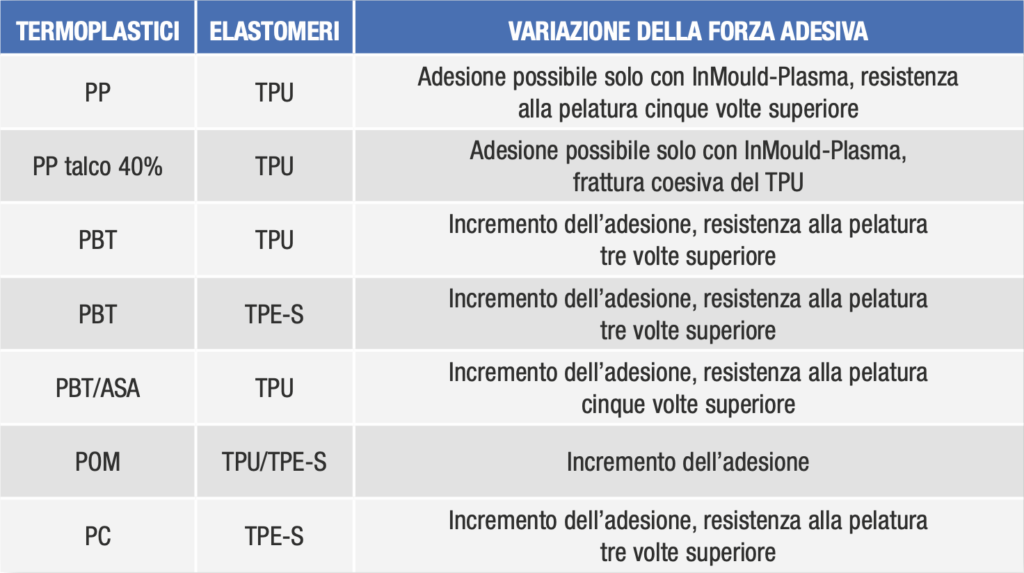
Componenti ibridi in metallo-plastica
I connettori elettrici devono assicurare un funzionamento assolutamente affidabile, perché i guasti possono avere gravi conseguenze. Ad esempio, una casa automobilistica ha dovuto richiamare oltre 8.000 SUV a causa di un connettore di cablaggio difettoso che creava una resistenza elettrica eccessiva. I guasti ai connettori possono comportare anche estesi blackout e incidenti aerei, e perfino la stazione spaziale Mir è quasi andata persa a causa di un connettore difettoso.
Le ragioni più comuni dei difetti tecnici sono i guasti meccanici e la corrosione dei contatti metallici. In questi casi, l’interfaccia metallo-plastica tra gli spinotti in metallo e l’alloggiamento stampato a iniezione gioca un ruolo rilevante, perché è particolarmente suscettibile alla penetrazione dell’umidità. Il processo di sigillatura Plasma-SealTight permette di evitare questi inconvenienti assicurando una tenuta ermetica. Dopo la pulizia e l’attivazione delle superfici dei contatti metallici, mediante la tecnologia PlasmaPlus viene applicato un nano-rivestimento, il quale funge da agente di accoppiamento che assicura l’adesione del polimero e previene la corrosione dei contatti causata dall’infiltrazione di umidità.
Nel progetto di sviluppo di un connettore multi-pin è emersa la capacità del plasma di aumentare la qualità dei connettori elettrici. Il trattamento superficiale consente di realizzare un gruppo di assemblaggio ad alta integrità e affidabilità contro la penetrazione dell’umidità, che è in grado di resistere all’acqua a una pressione fino a 5 bar. Anche la resistenza della giunzione meccanica tra metallo e plastica è notevole: mentre i processi convenzionali raggiungono una resistenza massima a trazione e taglio di 20 MPa, con Plasma-SealTight è possibile superare i 50 MPa.
Adesione stabile e duratura negli assemblaggi
PT-Bond è un’altra applicazione di PlasmaPlus specificamente studiata per l’incollaggio e la sigillatura. In questo caso, un composto organosilicio, la cui composizione chimica varia in relazione al materiale e all’applicazione, viene aggiunto al plasma come precursore. I rivestimenti PT-Bond aumentano la resistenza della giunzione adesiva e migliorano significativamente le proprietà di tenuta, anche in combinazioni di materiali ibridi caratterizzati da coefficienti di dilatazione termica diversi.
La tecnologia è stata scelta da un noto produttore di asciugatrici domestiche per un’applicazione che prevedeva l’incollaggio tra vetro e PP. In questo caso, i tecnici hanno deciso di utilizzare un sigillante in schiuma poliuretanica monocomponente. Il rivestimento PT-Bond ha permesso di ottenere una migliore stabilità a lungo termine della funzionalizzazione superficiale e il conferimento di funzionalità ai legami covalenti.
Quando l’adesivo aderisce senza legami covalenti, l’esposizione all’umidità e al calore provoca rapidamente la distruzione delle delicate interazioni dipolo-dipolo tra le molecole di idrogeno del substrato e i segmenti uretano/urea dell’adesivo: un’eventualità fatale per un’asciugatrice in cui i componenti sono esposti ad alte temperature e umidità per molti anni. Il trattamento al plasma, invece, crea legami covalenti e resistenti all’invecchiamento e consente anche l’applicazione di primer convenzionali a base di solventi.
Adesione senza primer e solventi
In quasi tutti i processi di produzione che richiedono un trattamento superficiale, la tecnologia al plasma rappresenta un’alternativa migliore dal punto di vista tecnico, meno costosa e più sicura. Prima di tutto, perché permette di effettuare la pulizia superficiale e l’applicazione di nano-rivestimenti funzionali in un unico passaggio, poi perché genera giunzioni adesive e rivestimenti funzionali stabili nel tempo. Inoltre, la possibilità di depositare nano-rivestimenti (PlasmaPlus) conferisce proprietà superficiali specifiche, come ad esempio l’idrofobia, un effetto anticorrosione o promotore dell’adesione. La sicurezza nei luoghi di lavoro è invece garantita dall’eliminazione pressoché totale di solventi e primer tossici.
Un altro problema legato ai primer riguarda i solventi, che reagiscono con le plastiche dando luogo a fratture da stress. A questo si somma il fatto che non è possibile realizzare un’adesione resistente all’invecchiamento senza che si verifichi una dissoluzione della plastica. Il plasma permette di eliminare tali inconvenienti, perché non utilizza solventi. A beneficiare del trattamento sono soprattutto i polimeri fortemente apolari come PP, EPDM o quelli molto difficili da sciogliere, in particolare quelli con superfici che possono essere modificate con l’innesto di radicali. Infine, i trattamenti di precisione sviluppati da Plasmatreat e la certificazione ISO 9001:2015 garantiscono un’alta qualità e una riproducibilità affidabile.