L’aumento dei prezzi delle materie prime, le specifiche di qualità sempre più elevate e la ricerca di una maggiore sostenibilità richiedono nuove tecnologie per rendere più efficienti ed economici i processi di trasformazione dei polimeri plastici, anche quelli rigenerati che attualmente sono oggetto di un forte interesse. Nel 2019 il consumo di materiali riciclati ha infatti sfiorato i 1,9 milioni di tonnellate, con un aumento del 10,2% rispetto al 2017 [1]. E il valore, secondo le previsioni, è destinato a crescere, raggiungendo quote importanti.
Plasma, una tecnologia sostenibile
La selezione dei materiali basata su criteri economici e ambientali può influenzare l’intero processo di lavorazione in termini di stampabilità, adesione e molto altro. Negli ultimi anni, la tecnologia al plasma si è affermata come una soluzione affidabile, efficiente ed ecologica a molti di questi problemi in diverse applicazioni industriali, perché riuscendo a modificare le superfici migliora l’adesione di vernici e adesivi, ma anche tra materiali originariamente incompatibili. Gli operatori possono quindi beneficiare di una più ampia scelta di materie prime, oppure sostituire i tecnopolimeri con commodity meno costose. «Anche l’impronta ambientale può essere migliorata mediante un adeguato trattamento della plastica riciclata per i processi a valle o l’applicazione di rivestimenti e adesivi privi di solventi» spiega Alexander Knospe, responsabile dell’innovazione presso Plasmatreat, produttore di tecnologia al plasma a pressione atmosferica.
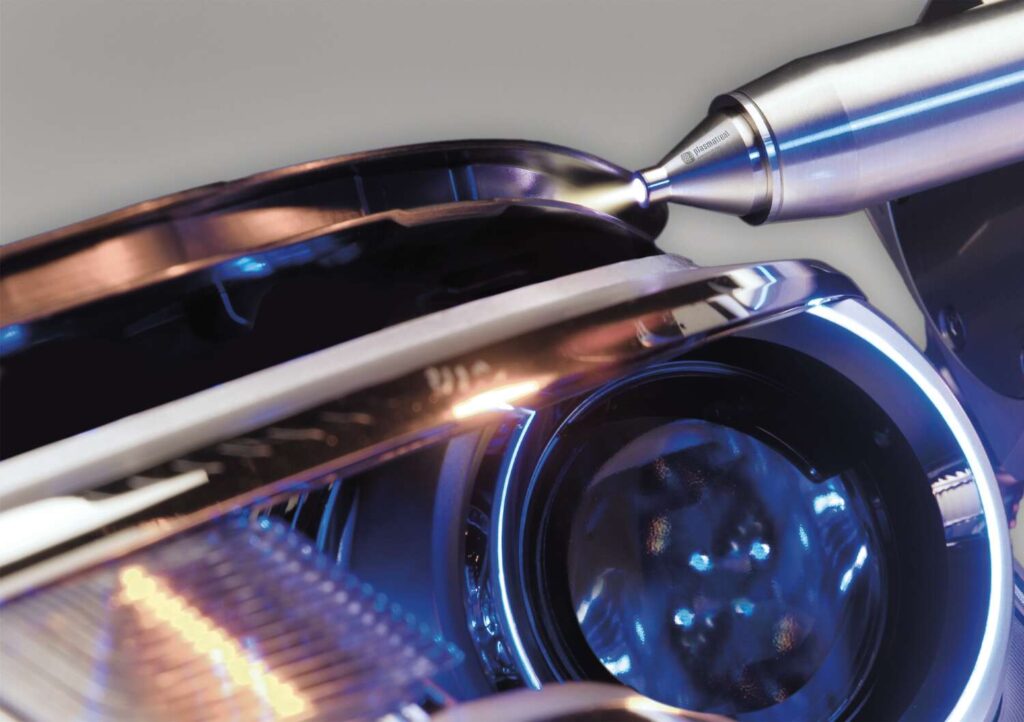
Attivazione rapida e adesione più stabile
Per ottenere prodotti finali di alta qualità e garantire un processo affidabile, i parametri critici devono essere tenuti costantemente sotto controllo. Per questa ragione, i sistemi Plasmatreat integrano una varietà di funzioni di controllo e monitoraggio per assicurare l’elevata qualità e riproducibilità del trattamento al plasma. Ad esempio, la velocità, la distanza tra l’ugello e il substrato e l’intensità del fascio del plasma vengono regolati con precisione in modo da applicarlo soltanto sull’area da trattare. L’individuazione dei parametri e degli ugelli più adeguati fanno parte del bagaglio di competenze di Plasmatreat a garanzia di un processo affidabile.
Nel trattamento Openair-Plasma, i gruppi contenenti ossigeno e azoto vengono (generalmente) applicati a plastiche apolari per incrementare l’energia superficiale, migliorandone in tal modo la bagnabilità e quindi consentendo un’adesione stabile nel tempo di adesivi, vernici e rivestimenti. Attraverso la tecnologia PlasmaPlus, invece, è possibile applicare nano-rivestimenti per creare superfici con funzioni specifiche che le rendono, ad esempio, altamente idrofobe o idrofile.
Tutti i processi al plasma sono privi di solventi, selettivi in relazione all’area da trattare e possono essere integrati in una linea di produzione. «Numerose applicazioni industriali con diverse materie plastiche dimostrano sia un significativo aumento di ossigeno sulla superficie del polimero dopo il trattamento al plasma, sia la stabilità a lungo termine dell’attivazione a seguito della conservazione a temperatura ambiente. I test effettuati dai nostri ricercatori mostrano una migliore adesione delle materie plastiche anche in condizioni estreme» commenta Alexander Knospe.
Più tenuta nei fanali auto
La tecnologia al plasma si è dimostrata efficace e vantaggiosa in molte applicazioni nel settore automobilistico. Una delle più consolidate per Plasmatreat riguarda il montaggio delle lenti sugli alloggiamenti dei gruppi ottici delle vetture – generalmente realizzati in polipropilene –, dove è fondamentale garantire un incollaggio affidabile e una tenuta ermetica contro l’umidità. La scanalatura sulla circonferenza dell’alloggiamento viene sottoposta al trattamento Openair-Plasma, che attiva in modo uniforme il materiale apolare nelle aree critiche. Grazie all’elevata reattività del fascio del plasma, sia il fondo che le pareti laterali della scanalatura vengono funzionalizzate, assicurando così un incollaggio affidabile e una tenuta stabile a lungo termine delle parti assemblate. Nel complesso, il processo è caratterizzato da un’elevata precisione e da un costo competitivo. Anche le lenti dei fanali in policarbonato, che devono garantire un’altissima resistenza ai graffi e agli urti, vengono sottoposte al trattamento al plasma. Le delicate superfici delle lenti sono dotate di una finitura antigraffio, di solito a base acrilica, per essere protette dall’abrasione meccanica. Prima del processo di rivestimento, lo strato di policarbonato viene attivato mediante il trattamento Openair-Plasma. L’operazione garantisce un flusso di rivestimento uniforme, riducendo di conseguenza il numero di parti di scarto causate da contaminanti che aderiscono alla superficie. Infine, l’applicazione di un nano-rivestimento PlasmaPlus sulla superficie interna delle lenti impedisce l’appannamento provocato alla condensa che potrebbe essere presente all’interno del fanale.
Anche per guarnizioni in EPDM
La tecnologia al plasma è ormai una pratica standard non solo presso i principali produttori di gruppi ottici, ma anche in molte case automobilistiche e i loro fornitori, che la utilizzano per la pulizia, l’attivazione e la funzionalizzazione chimica delle superfici di componenti per interno o esterno vettura, ottenendo un prodotto di qualità più elevata. Un’applicazione interessante riguarda le guarnizioni delle portiere delle autovetture prodotte con compound a base di EPDM. Queste parti, in esercizio, devono garantire buone proprietà riempitive e insonorizzanti, essere visivamente gradevoli, piacevoli al tatto, e poco costose, e inoltre non devono congelarsi alle basse temperature. Per soddisfare tutti questi requisiti, vengono applicati rivestimenti floccati o antiscivolo. In passato, le guarnizioni venivano pretrattate con spazzole rotanti a filo metallico per ottenere una buona adesione del rivestimento. Un processo più semplice, pulito, veloce e riproducibile è offerto dalla tecnologia Openair-Plasma, che può agire sulle guarnizioni già dopo l’estrusione per prepararle alle successive fasi di processo. Il trattamento al plasma non genera polvere e assicura un’adesione elevata e uniforme. Inoltre, la qualità del rivestimento antiscivolo o floccato viene migliorata in modo più sostenibile, più economico ed ecologico.
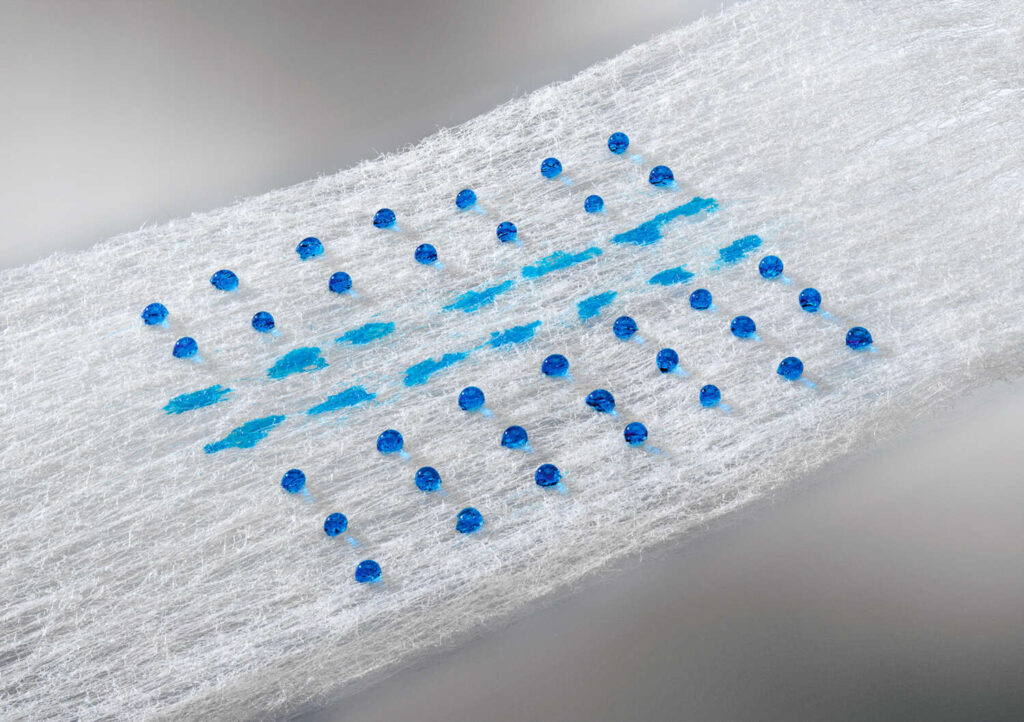
Dai nonwoven tessili ai compositi legno-plastica
La tecnologia al plasma offre interessanti vantaggi anche nei prodotti per l’igiene realizzati in tessuto-non-tessuto sintetico. La bagnabilità dei pannolini, ad esempio, può essere migliorata grazie al trattamento Openair-Plasma a vantaggio della possibilità di utilizzare impregnanti a base d’acqua in sostituzione di quelli di natura chimica. Il trattamento, inoltre, può ridurre i consumi di adesivi fino al 40%. Un sottile rivestimento PlasmaPlus, invece, conferisce nuove caratteristiche superficiali, ad esempio antimacchia e proprietà barriera contro acqua, ossigeno e anidride carbonica.
Dai profili delle finestre alla pavimentazione di porticati, il trattamento al plasma apre nuove possibilità di design anche nel settore edile. Nella produzione di serramenti è possibile utilizzare compositi in legno-plastica (WPC). Si tratta di materiali apolari, spesso di riciclo, che richiedono un trattamento superficiale efficiente come Openair-Plasma per assicurare incollaggi affidabili, ad esempio, tra il profilo della finestra, il vetro laminato o il bordo. Il trattamento rende i WPC adatti a scopi decorativi e consente inoltre di utilizzare materiali di riciclo nella produzione di articoli ad alto valore aggiunto.
Ottime prestazioni anche con POM, PU e PA
Come anticipato, il plasma ha rivelato la propria efficacia con molti materiali plastici. Grazie al bassissimo coefficiente di attrito, il poliossimetilene (POM) rappresenta un materiale eccellente per i sistemi rotativi, come ad esempio le rotelle di regolazione degli inalatori. Per garantire il corretto uso di questi dispositivi, le scritte o le immagini stampate su di essi devono essere chiare e permanenti. Tuttavia, questo materiale è difficile da stampare a causa della sua bassa energia superficiale e la conseguente inadeguata bagnabilità. Il trattamento Openair-Plasma attiva la superficie e garantisce un’adesione dell’inchiostro da stampa che resiste nel tempo.
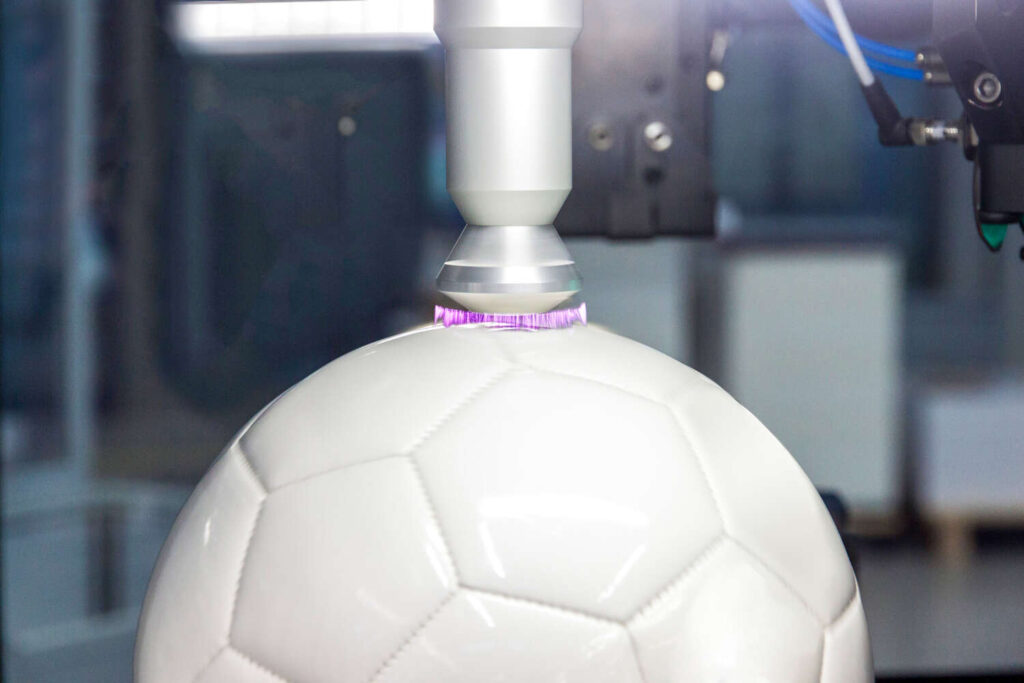
Il poliuretano (PU), invece, è il materiale privilegiato ogniqualvolta sono richieste proprietà come resistenza all’abrasione, elevata estensibilità e buona elasticità. I palloni da calcio, ad esempio, sono costituiti da diversi strati di elastomero PU saldati insieme; questo rende la superficie elastica, resistente all’usura e durevole. Il trattamento con Openair-Plasma garantisce una pulizia profonda di questo materiale difficile da stampare e lo attiva per le successive fasi di lavorazione. Grazie all’elevata bagnabilità conferita alla superficie trattata, gli inchiostri possono aderire molto meglio, rendendo più facile ed economico stampare immagini in maniera permanente su oggetti esposti a elevate sollecitazioni meccaniche come i palloni da calcio.
Nella produzione della scocca di uno smartphone 5G in poliammide 12, invece, il plasma ha evidenziato grandi potenzialità nel miglioramento delle capacità di adesione della superficie che, a seguito di un rivestimento con un ritardante di fiamma, rendeva difficoltoso il successivo l’incollaggio. Sostituendo la pulizia a umido dopo lo stampaggio a iniezione con il plasma, il produttore è riuscito a ottenere le prestazioni desiderate.
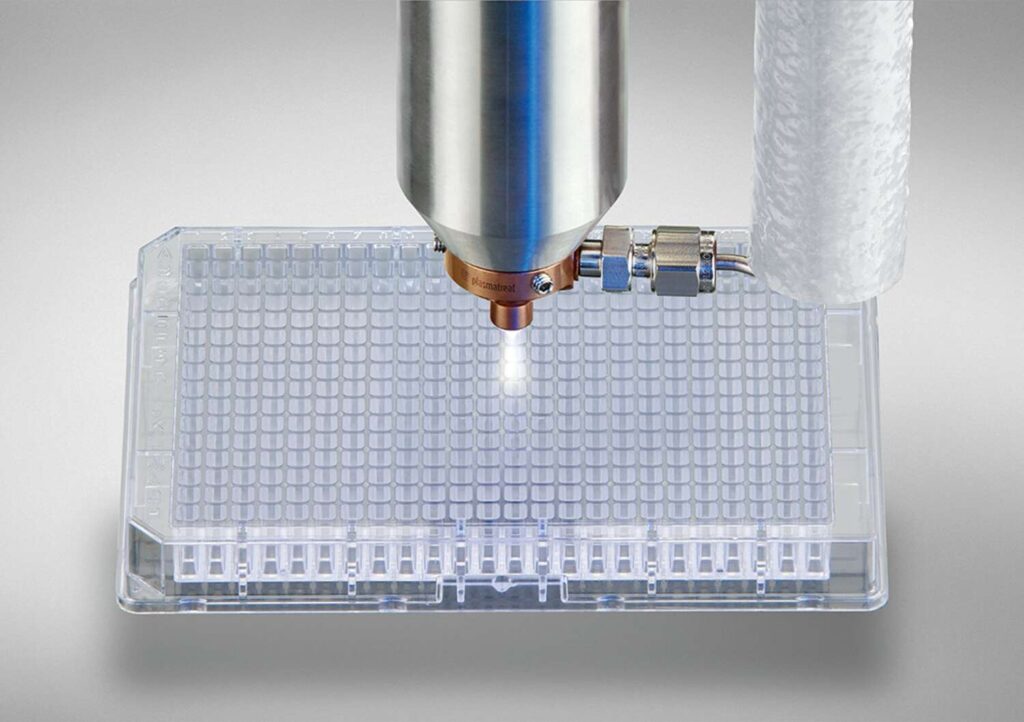
Analisi più efficienti
Nel corso dell’emergenza pandemica da Covid-19 il consumo di dispositivi medici è aumentato sensibilmente, in particolare la domanda di kit diagnostici e per analisi di laboratorio. Un requisito chiave per queste applicazioni consiste nell’utilizzare il supporto analitico più piccolo possibile per aumentare la resa e al contempo ridurre al minimo il costo di ciascun test. Applicando un trattamento al plasma altamente idrofobo, che soddisfa i più elevati standard di laboratorio in termini di tenuta e trasparenza, soltanto sull’area che entra in contatto con il fluido di analisi è possibile utilizzare il fluido fino l’ultima goccia, riducendo così la quantità di reagenti necessaria.
Bibliografia
1 Conversio Market & Strategy GmbH: Stoffstrombild Kunststoffe in Deutschland 2019.