Lo smaltimento degli scarti in gomma vulcanizzata è da sempre un problema di difficile soluzione, perché la loro struttura reticolare rende le convenzionali tecnologie di riciclo antieconomiche e non rispettose dell’ambiente. Non solo. Il materiale ottenuto è spesso di scarsa qualità, perché il trattamento di rigenerazione altera e indebolisce le principali catene polimeriche dell’elastomero. Queste difficoltà hanno spinto verso la ricerca di soluzioni alternative, come l’impiego degli scarti nella produzione di campi da gioco sintetici, barriere insonorizzanti, bitume per asfalti e altre applicazioni dove la qualità non è un elemento differenziante. Sviluppare un processo di recupero capace di produrre un materiale ad alte prestazioni, al contempo sostenibile dal punto di vista ambientale ed economico, è pertanto una grande sfida. Sfida con cui ha deciso di misurarsi il Gruppo Oldrati di Villongo (Bergamo), una delle realtà più interessanti nel panorama italiano del comparto degli elastomeri e dei termoplastici.
Un’idea sostenibile
La storia del gruppo inizia nel 1964 con la Oldrati Guarnizioni Industriali, uno dei tanti produttori di guarnizioni in elastomero attivi nella Rubber Valley, area che si estende tra le province di Bergamo e Brescia. Con il passare dei decenni l’azienda cresce acquisendo realtà imprenditoriali che apportano nuovi know-how e specializzazioni, diventando oggi una multinazionale che integra al proprio interno l’intera filiera produttiva, spaziando dalla creazione delle mescole al confezionamento del prodotto finito. «Gomma vulcanizzata ed elastomeri termoplastici sono da sempre nel nostro DNA» racconta a Plastix Manuel Oldrati, amministratore delegato del Gruppo.
«Già negli anni Ottanta, mio padre Vanni – il fondatore – ha tentato di risolvere il problema introducendo la gomma micronizzata nelle mescole. La tecnologia, però, aveva dei vincoli intrinsechi perché presentava limiti significativi in termini di qualità del prodotto finale». L’idea di riportare allo stato di materia prima lo scarto, seppure perseguita a fasi alterne, non è mai stata abbandonata. «Nel 2000, in tempi non sospetti, il reparto di ricerca si è rimesso al lavoro e ha sviluppato materiali e processi innovativi legati alla gomma rigenerata. A partire dal 2010, quando le politiche ambientali hanno cominciato a manifestarsi come una tendenza sempre più incontrovertibile, è iniziata la fase di vero e proprio trial di mercato e industrializzazione di tali soluzioni, che culminano oggi in Ogreen, la prima gomma ecosostenibile ottenuta da gomma rigenerata» continua Oldrati.
Segui l’intervento di Paolo Morandi di Oldrati alla tavola rotonda “Il new norma della plastica” organizzata da Plastix
Come nasce Ogreen
Negli stabilimenti Oldrati sono al lavoro centinaia di presse a iniezione operative a ciclo continuo, che trasformano un volume enorme di elastomeri. «La linea di produzione delle guarnizioni per gli oblò delle lavatrici, ad esempio, lavora 7-8.000 chilogrammi al giorno di gomma vulcanizzata, generando uno scarto di circa il 10% tra materozze, sfridi perimetrali ed eventuali parti fuori specifica. Una quantità che si aggira intorno a 180.000 chilogrammi all’anno, troppo elevata per non pensare di recuperarla» precisa Oldrati. La nuova gomma ecosostenibile nasce proprio da questa consapevolezza e arriva da un processo altamente complesso, costituito da molteplici fasi e soluzioni tecnologiche interamente sviluppate e gestite all’interno del gruppo. Il primo passo per ottenere un prodotto di seconda vita della massima qualità passa attraverso un’accurata selezione degli scarti. «Le tipologie di gomma lavorate nei nostri impianti vengono separate dagli addetti e, una volta smistate, conferite nei contenitori dedicati. Si tratta di un’operazione delicata, perché solo attraverso il corretto smistamento e gestione dello scarto si possono evitare contaminazioni della futura mescola da riutilizzo» continua. «Gli scarti differenziati vengono quindi triturati e ridotti in granuli di circa un centimetro, dimensione che ci consente di mantenere elevata l’efficienza del processo. Lungo la linea per il trasporto dei granuli è installato un metal detector che rileva la presenza di particelle metalliche – anche di grammatura minima – e le rimuove dal sistema. Il materiale viene quindi convogliato in un masterizzatore a temperatura controllata nel quale subisce tutti i cambiamenti che lo porteranno a uno stadio di pre-vulcanizzazione».
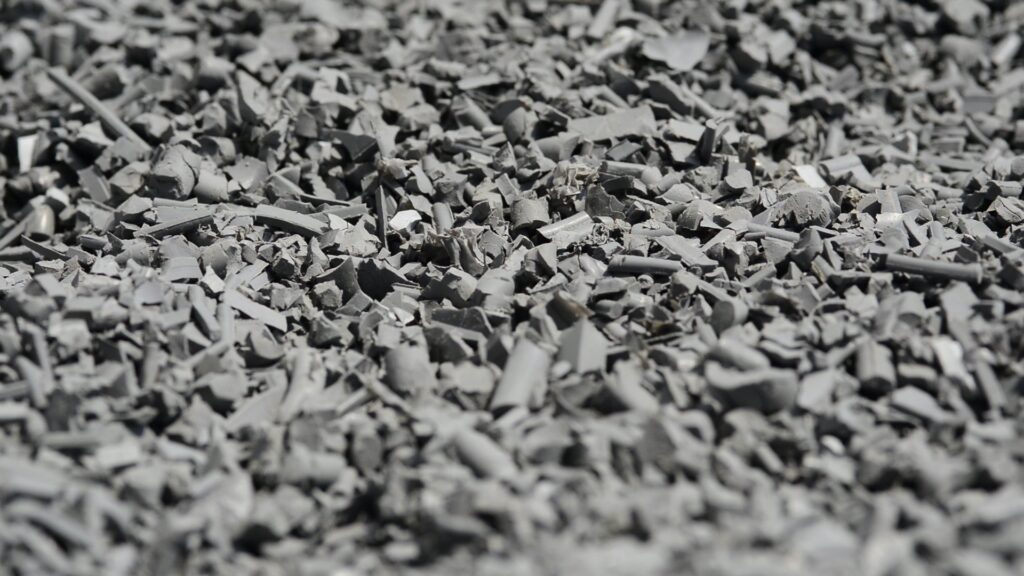
Una tecnologia complessa
Il processo utilizzato dai ricercatori di Oldrati non prevede l’aggiunta di reagenti chimici, ma è di natura termomeccanica. In particolare, combina stress meccanico e termico per ottenere il breakdown dei legami che costituiscono il reticolo dell’elastomero, senza però compromettere la lunghezza delle catene polimeriche. La diminuzione del peso molecolare comporterebbe infatti un inevitabile decadimento delle proprietà fisico-meccaniche del polimero. «Abbiamo definito “masterizzatore” la parte dell’impianto in cui avviene la rigenerazione perché il processo trasforma una gomma vulcanizzata in un master contenente cariche e additivi, ovvero una delle materie prime che, in base alle performance richieste, verrà “compoundata” con altri ingredienti per creare una mescola della famiglia Ogreen» precisa Oldrati. Il masterizzatore – di fatto – è un estrusore evoluto, con tecnologia molto complessa, costituito da differenti elementi ciascuno caratterizzato da una sua specificità.
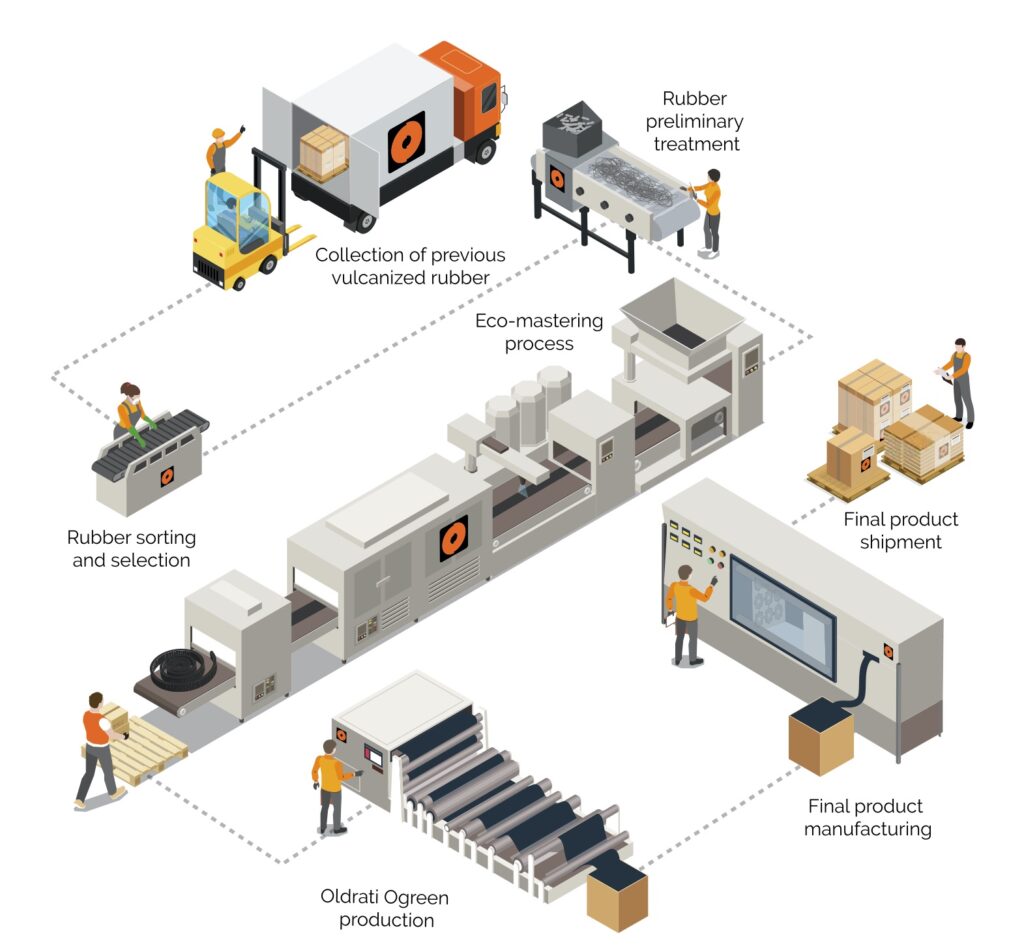
«Lo sviluppo della geometria della vite adeguata ci ha consentito un salto di qualità, non solo in termini di prestazioni del materiale ottenuto, ma anche di passaggio dalla scala di laboratorio alla produzione industriale, per la quale occorre un processo sufficientemente robusto, in grado di sopportare le oscillazioni delle caratteristiche dei materiali trattati. Al momento l’impianto riesce a garantire una produttività di circa 1.500 tonnellate annue, ma la capacità può essere raddoppiata in base alle esigenze» continua. «La tecnologia, oltre a essere molto complessa, è caratterizzata da un’elevata specificità: sono infatti stati progettati e definiti elementi meccanici e processi (diverse condizioni di temperatura, velocità degli elementi, portate…) per ogni tipo di polimero trattato, al momento otto. In questo modo riusciamo a ottenere un prodotto con prestazioni simili a quelle della materia prima “vergine”» sottolinea l’imprenditore.
I vantaggi della sostenibilità
«Dieci anni fa, quando abbiamo deciso di intensificare gli sforzi in ricerca e sviluppo, non eravamo certi che la gomma rigenerata potesse riscuotere l’interesse dei nostri clienti, anche perché i prodotti in commercio non garantivano prestazioni adeguate alla produzione di articoli tecnici» continua Oldrati. «Abbiamo comunque deciso di investire nel progetto, perché siamo convinti che utilizzare una gomma ecosostenibile porti con sé importanti vantaggi, come la riduzione del consumo di risorse fossili, degli sprechi e dell’utilizzo di discariche. Il tutto finalizzato alla riduzione dell’impatto ambientale». Per combattere lo scetticismo degli OEM sulla nuova gomma a basso impatto ambientale – soprattutto nel comparto dell’household e del riscaldamento –, il gruppo bergamasco ha deciso di puntare sulla massima collaborazione con gli end user, attraverso prove sperimentali mirate e lo sviluppo di progetti in codesign. E, a giudicare dai primi approcci con i principali costruttori di grandi elettrodomestici, il materiale sembra riscuotere un grande interesse, tanto che è in fase di costituzione un consorzio di realtà industriali internazionali disposte a creare le condizioni per esplorarne le potenzialità applicative.
Una differenza contenuta se si considera il volume di rifiuti sottratti alla discarica a favore di un processo circolare, un valore etico che può essere facilmente trasformato in strumento di marketing vista la crescente attenzione del consumatore verso la sostenibilità. «Il vero salto di qualità per l’ambiente, però, potrà avvenire solo quando la nostra innovazione riuscirà a travalicare i confini del Gruppo Oldrati, per essere applicata a tutti gli scarti di elastomeri. E su questo fronte siamo aperti alla collaborazione con nuovi attori disposti a trasformare in realtà il nostro sogno di sostenibilità» conclude Oldrati.