La richiesta di polimeri sostenibili è in costante ascesa e non ha trovato impreparate le aziende che già da tempo investono in ricerca per sviluppare nuove formulazioni anche in questo campo. Negli ultimi anni si sta però assistendo a un importante salto di qualità, come conferma a Plastix Stefano Scaglioni, Technical Assistance di Poliblend di Mozzate (Como). «Il mercato ha sempre richiesto compound ottenuti partendo da basi riciclate, macinati o materiali fuori specifica – quasi esclusivamente derivati da scarti post industriali – allo scopo di contenere i costi in applicazioni di minor valore aggiunto.
Le recenti politiche green hanno però determinato un cambio di passo che ha portato all’emanazione di normative di riferimento, ma anche a richieste più puntuali da parte degli utilizzatori, che desiderano essere rassicurati dal punto di vista sia delle prestazioni, sia della quantità effettiva di scarti contenuta nel materiale». Poliblend si è attivata in questa direzione e alla fine dell’anno scorso ha ottenuto la certificazione Plastica Seconda Vita dei Polimid Green, una linea di compound a base poliammide con un contenuto variabile dal 30% al 95% di polimeri derivati da rifiuti provenienti da raccolta differenziata e/o industriali. Plastica Seconda Vita è un marchio di IPPR (Istituto per la Promozione delle Plastiche da Riciclo), il primo in Italia e in Europa a garantire un sistema di certificazione ambientale di prodotto dedicata ai materiali e ai manufatti ottenuti dalla valorizzazione dei rifiuti plastici.
C’è plastica e plastica
«I processi di recupero partono prevalentemente da polietilene, polipropilene e PET, le classiche commodities da imballaggio, vista la maggior disponibilità di scarti post industriali e post consumo, sebbene questi ultimi siano più difficili da riciclare. Poliblend è invece focalizzata sui tecnopolimeri, in particolare le poliammidi 6 e 66» spiega Scaglioni. «Trattare rifiuti polimerici caricati con fibre di vetro non crea particolari problemi nel processo di recupero, ma la riduzione della lunghezza delle fibre durante il processo di ritrafilatura si ripercuote inevitabilmente sulle caratteristiche meccaniche del prodotto finito. Il problema si risolve aggiungendo al compound un rinforzo a base di polimero e fibra di vetro vergini, che permette di ottenere discrete performance tecniche, seppure lievemente inferiori rispetto al materiale di prima scelta». Un’altra difficoltà è legata alla colorazione.
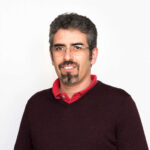
La spinta del settore pubblico
Il principale mercato per i primi prodotti certificati Plastica Seconda Vita di Poliblend è quello legato alla produzione di sedie, mobili e prodotti da ufficio. Una scelta mirata. Da alcuni anni, infatti, il Codice degli appalti ha reso obbligatoria l’applicazione del GPP-Green Public Procurement, definito a livello europeo come l’approccio in base al quale le Pubbliche Amministrazioni (PA) integrano i criteri ambientali in tutte le fasi del processo di acquisto. Partendo da qui, il Ministero dell’ambiente ha definito i Criteri Ambientali Minimi, cioè i requisiti per le varie fasi del processo di acquisto delle PA, volti a individuare la soluzione progettuale, il prodotto o il servizio migliore sotto il profilo ambientale lungo il ciclo di vita, elencando una serie di manufatti che contengono materiali di scarto. «Poter contare sul marchio Plastica Seconda Vita, così come sul marchio Remade in Italy, anch’esso dedicato alla certificazione del contenuto di riciclato in un prodotto, è oggi per un’azienda la garanzia di rispetto dei Criteri Ambientali Minimi previsti dalla normativa italiana e, di conseguenza, un “lasciapassare” per fornire la PA. Il limite, attualmente, è la scarsa conoscenza di questi marchi all’estero» puntualizza Scaglioni.
Nuove opportunità per i rigenerati
Se le Pubbliche Amministrazioni guardano agli acquisti verdi perché il Codice degli appalti ha reso obbligatoria l’applicazione del GPP-Green Public Procurement, altri settori iniziano a mostrarsi interessati alle plastiche sostenibili, con una spinta fortemente innescata dal desiderio di mostrare un’immagine di attenzione ai temi ambientali che attualmente prevale rispetto a una scelta industriale netta. Il comparto dell’abbigliamento è oggi tra i primi “imputati” per quanto concerne l’emissione di gas serra e per invertire o quantomeno arginare la tendenza, l’unica strada che non sia quella di ridurre le produzioni è l’introduzione di nuove fibre che contengano materiali di recupero, a partire dal poliestere e dalle gomme termoplastiche. Altro settore nel quale l’attenzione si sta alzando è quello della grande distribuzione: molti marchi, dopo aver puntato sugli imballaggi di cartone riciclato, stanno finalmente rivolgendo la propria attenzione ai prodotti venduti, al contenuto più che al contenitore. È quanto avviene nel comparto dell’arredamento, dove è facile immaginare che, nell’arco di pochi anni, tutto ciò che sarà tecnicamente realizzabile verrà orientato sulla produzione con plastica da fonte riciclata.
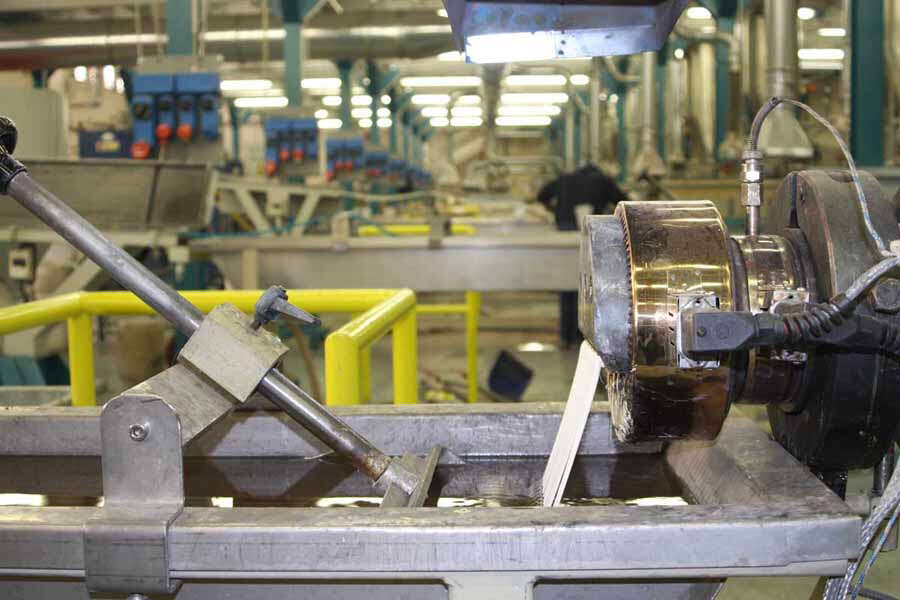
Rigenerati, un problema di prezzo
«Probabilmente non vi è ancora una piena consapevolezza del fatto che i processi produttivi rendono i materiali rigenerati più costosi rispetto a quelli ottenuti da polimero vergine» precisa Scaglioni. Già, il costo. «È maggiore perché la catena di produzione è complicata: raccogliere, selezionare, trasportare, pulire, analizzare, riestrudere, analizzare nuovamente. Al costo di queste operazioni si somma anche la disponibilità di “materia prima”, con i prezzi destinati a salire quando sempre più aziende si dimostreranno interessate. Ecco perché, oggi, chi può contare su una fonte di fornitura continua di scarti tende a fidelizzare i propri canali di approvvigionamento» sottolinea Scaglioni.
Il valore della certificazione all’estero
La parcellizzazione delle normative e delle relative certificazioni di paese in paese è un limite oggettivo. «Con un calcolo approssimativo, oggi si possono contare oltre 20 percorsi certificativi che fanno riferimento ad altrettanti standard differenti, alcuni dei quali genericamente rivolti a tutti i settori industriali» precisa Scaglioni. Difficile, inoltre, trovare normative tecniche comuni in un contesto così frammentato. «Essere al passo con le certificazioni più diffuse in Italia apre molte opportunità a livello locale, e non solo nelle pubbliche amministrazioni. È però più difficile approcciarsi a potenziali clienti in Europa e nel resto del mondo, ai quali ci stiamo avvicinando con un lavoro di comunicazione e internazionalizzazione, ma sarebbe opportuno poter contare, almeno a livello comunitario, su un sistema armonizzato» continua. Le differenze di protocollo tra il nostro paese e l’estero influiscono inevitabilmente anche sulla catena di fornitura. «In Italia si segue il percorso del rifiuto con una tracciabilità codificata e regolata dal Formulario di Identificazione dei Rifiuti, che lo classifica in base al catasto europeo, ne individua la fonte di provenienza e quindi il transito attraverso l’eventuale intermediario che lo movimenta e le aziende che, come noi, lo ricevono per lavorarlo». Chiunque tratti rifiuti è obbligato a tenere un registro di carico e scarico, che costituisce prova della tracciabilità, dalla produzione all’invio a recupero o smaltimento, fino alla rigenerazione. «In molti paesi esteri questo percorso avviene con modalità simili attraverso il cosiddetto Allegato 7, che permette anche alle aziende italiane di ricevere e trasformare materiale di provenienza straniera purché dotato di precisi requisiti. Finora Poliblend ha preferito approvvigionarsi da realtà italiane che consegnano materiali già separati per tipologia e colore, permettendoci così di realizzare anche gradi di tinta neutra. Attualmente ci stiamo focalizzando su poliammidi 6 e 66 non caricate per semplicità di lavorazione e soprattutto per omogeneità del prodotto finito. Le poliammidi rappresentano da sempre il nostro core business, quindi possiamo contare su una fitta rete di contatti che ci garantisce una fornitura di scarti continua» precisa.
In cerca di lotti omogenei
I limiti tecnici più evidenti, in questo momento, sono rappresentati dalla maggior variabilità del prodotto finito che, realizzato con fonti differenti, non potrà mai vantare le specifiche ristrette ottenibili utilizzando sempre e solo lo stesso polimero vergine. «Quando acquistiamo un lotto di rifiuti, che generalmente si aggira intorno alle 20 tonnellate, ci accertiamo che sia effettivamente a base poliammide 6 o 66 con minime percentuali di altre componenti. Dopo la caratterizzazione, si procede con la triturazione e l’omogeneizzazione, effettuando nuove analisi per appurare le quantità di materiali estranei» continua Scaglioni. «L’uniformità è pressoché garantita all’interno del singolo lotto ed è maggiore più lo stesso è grande, ma evidentemente lo è meno da lotto a lotto. Le variabili in gioco sono davvero numerose e le criticità, parlando di poliammidi, si rilevano subito in termini di differenza di viscosità e fluidità rispetto a un prodotto di prima polimerizzazione. Il “mestiere” del compounder, però, è proprio quello di effettuare continue variazioni e prove migliorative per ottenere il miglior risultato possibile» sottolinea.
I materiali certificati Plastica Seconda Vita si differenziano rispetto ai rigenerati da sempre proposti da Poliblend per una serie di caratteristiche. «Innanzitutto, sono rispondenti alle norme tecniche previste dallo standard UNI 10667 che definisce parametri minimi per il materiale. Inoltre, il contenuto minimo di rifiuto è del 30% e, come detto, il sistema di tracciabilità delle fonti garantisce l’effettivo recupero da rifiuto. «Le differenze in termini di prestazioni tecniche non sono sostanziali, ma la maggior richiesta del mercato è oggi rivolta ai compound certificati e questa discriminante sarà sempre più decisiva negli orientamenti degli end user» sottolinea.
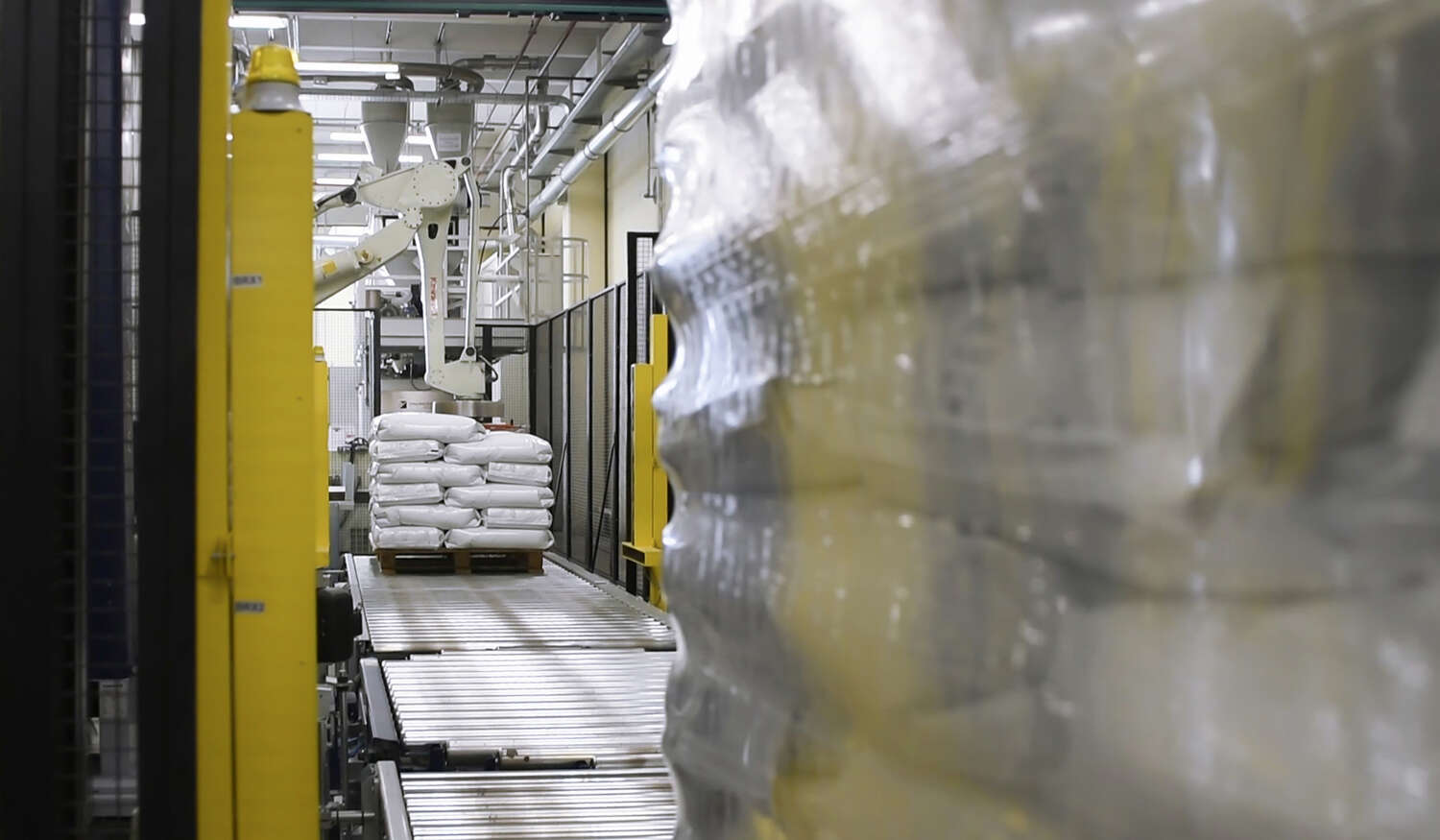
Polimeri e limiti
Per il settore della plastica la discriminante tra il recupero e l’avvio in discarica rimane certamente un fattore complesso, molto più che per altri comparti industriali. Ciò è dovuto a una serie di variabili, come il contenuto di additivi di varia origine che rendono estremamente complesso il trattamento del materiale per destinarlo a nuova vita. Valga l’esempio dei polimeri autoestinguenti, utilizzati in applicazioni per le quali la sicurezza finale del prodotto e di chi lo utilizza sono un fattore determinante. Alla complessità del processo di recupero si sommano il calo delle prestazioni di sicurezza oppure la contaminazione da additivi oggi non più consentiti, che possono compromettere il compound di seconda vita. Similmente, anche prodotti prettamente tecnici, come gli autolubrificanti, sono difficilmente gestibili in un’ottica di recupero e riutilizzo. «Oggi buona parte di questi materiali finisce in discarica» continua Scaglioni. «Ciò non toglie che siano allo studio, anche da parte del nostro settore ricerca, soluzioni per utilizzare autoestinguenti da destinare a nuovi compound di seconda vita. Al momento è tecnicamente possibile utilizzare scarti in plastica per creare polimeri ritardanti di fiamma, anche se si tratta di un progetto con un ampio orizzonte temporale, perché vanno valutate attentamente le prestazioni a lungo termine del compound finale e l’appetibilità commerciale. La domanda del mercato dovrebbe tendere a crescere sia perché si tratta di materiali davvero indispensabili in applicazioni elettriche ed elettroniche, sia per la spinta legata allo sviluppo futuro della mobilità elettrica».
Superare i limiti tecnici
È difficile generalizzare le differenze in termini prestazionali tra i compound rigenerati e quelli ottenuti con polimero vergine, perché sono inevitabilmente determinate dalla natura e dalla quantità del rifiuto utilizzato. «In termini di proprietà meccaniche si può parlare di una perdita del 15-20%, che in alcuni casi può arrivare anche al 40%» sottolinea Scaglioni. «È pur vero, però, che moltissime applicazioni non richiedono proprietà meccaniche così spinte da non consentire l’impiego di un polimero rigenerato, anche perché la sostituzione è sempre accompagnata da opportuni correttivi in fase di progettazione. Si pensi, ad esempio, alle pale di un ventilatore: basterebbe aumentarne lo spessore per compensare la perdita di prestazioni». Questo approccio è esportabile in diversi settori applicativi, anche se realizzare una sostituzione che permetta di impiegare gli stampi esistenti senza un eccessivo decadimento delle prestazioni, con differenze di prezzo contenute, non è sempre tecnicamente possibile, soprattutto nel settore automotive, soggetto a standard molto stringenti. «Ma non sarà sempre così, perché è proprio nelle applicazioni più complesse che si gioca una delle sfide più interessanti per la ricerca nel settore delle materie plastiche» conclude Scaglioni.