La tendenza alla miniaturizzazione, ormai trasversale a molti settori porta con sé l’esigenza di componenti funzionali dalle dimensioni sempre più ridotte e dal design eccellente. Si pensi all’estrema precisione richiesta dalla strumentazione per la chirurgia mininvasiva e dall’elettronica di consumo, ma anche dai settori del lusso come l’orologeria, dove è in aumento l’impiego di minuscoli ingranaggi e supporti dei movimenti in resina termoplastica o di piccole guarnizioni in silicone liquido (LSR). Un materiale, quest’ultimo, che sta rapidamente conquistando quote di mercato grazie alle sue proprietà specifiche e che, secondo le previsioni, dovrebbe essere sempre più richiesto dall’industria automobilistica sulla scia dello sviluppo dei veicoli elettrici.
Le sfide del microstampaggio
La tecnologia utilizzata per la produzione di componenti così piccoli è il microstampaggio a iniezione, con il quale si riescono a ottenere parti del peso decisamente inferiore a un grammo, anche se alcuni stampatori riescono addirittura a scendere sotto il milligrammo. In un simile campo di ordini di grandezza esistono tuttavia grandi differenze nella produzione di pezzi in termoplastico a basso peso specifico e in silicone liquido, in genere più pesanti ma di dimensioni più contenute, quindi più difficili da realizzare. Prima di procedere con l’analisi delle differenze tra le due famiglie di polimeri è opportuno considerare che le complessità ingegneristiche del processo sono esclusivamente da ascrivere al peso e alle dimensioni minuscole degli oggetti da stampare. Si pensi al componente stampato in LSR illustrato nell’immagine di apertura: è lungo 1,7 millimetri, ha un diametro di 0,9 millimetri e pesa 0,0005 grammi. Se viene prodotto con uno stampo a 32 impronte, il peso della stampata sarà quindi 0,125 grammi (pari, ad esempio, a 125 granelli di zucchero; per dare un’idea delle proporzioni, una zolletta ne contiene da 20.000 a 30.000, nda). Quantità di materiale tanto piccole, come ad esempio quelle necessarie per produrre i perni di fissaggio dei componenti di strumenti diagnostici oftalmologici, devono essere distribuite in maniera uniforme e ripetibile in tutte le impronte dello stampo. Il gruppo di iniezione, la materozza e la termoregolazione del processo sono estremamente importanti per la qualità, la precisione e la ripetibilità dei microcomponenti. Un esempio che illustra quanto know-how richieda il microstampaggio è rappresentato dal volume della materozza, che deve essere bilanciato in rapporto al volume del pezzo stampato. Oltre a richiedere l’ottimizzazione del processo in generale, ciò impone di considerare le interazioni tra varie condizioni limite, che a loro volta sono determinate dalla gestione del processo, dalla quantità di scarti e dai consumi di energia, dal costo del materiale e dal tempo ciclo. Tutto questo comporta sfide rilevanti sia per il costruttore della macchina, sia per il produttore dei microcomponenti.
Precisione e ripetibilità, due fattori essenziali
Il passaggio a volumi elevati di microparti rappresenta una sfida tra le più impegnative. Ponendo che i processi siano stati preventivamente testati con successo in laboratorio, al momento di avviare la produzione su scala commerciale i costruttori e gli utilizzatori delle tecnologie di microstampaggio si trovano spesso a risolvere problemi del tutto inediti. A titolo di esempio, si pensi alla precisione, un aspetto decisivo per decidere se scartare o meno un componente: errori di pochi millesimi di millimetro o di qualche decina di milligrammi possono anche essere tollerati su articoli di dimensioni normali, ma hanno un impatto importante sui microcomponenti e di conseguenza sulla loro affidabilità d’uso. In questo contesto, è indispensabile assicurare la massima precisione nelle interazioni tra le varie unità del sistema di stampaggio.
Nella versione completamente elettrica e senza colonne, la pressa a iniezione e-motion serie TL di Engel rappresenta un’ottima piattaforma per i processi di microstampaggio, non solo in fase di sviluppo, test di laboratorio e prototipazione, ma anche nelle grandi produzioni in serie. Queste macchine si caratterizzano per l’elevata precisione e per il nuovo gruppo di micro-iniezione flessibile (vedi riquadro Precisione nel LSR), sviluppato dal costruttore austriaco, in collaborazione con ACH Solution, specificamente per il microstampaggio del silicone liquido.
Lo stampaggio di alta qualità, preciso e ripetibile di microcomponenti non è tuttavia solo una questione di gruppo di iniezione: l’intera macchina, infatti, deve offrire il grado di precisione richiesto. Per entrambi i materiali, LSR e termoplastici, le presse completamente elettriche dotate di servomotori rappresentano quindi la scelta migliore, perché la ripetibilità dei movimenti di iniezione ha un’enorme influenza anche sulla precisione e ripetibilità dei manufatti. La tecnologia senza colonne, invece, assicura un eccellente parallelismo tra i piani portastampo e una distribuzione uniforme delle forze di chiusura. Inoltre, dato che i microcomponenti spesso vengono prodotti in camera bianca, una macchina dal design compatto ma con piani di grande superficie consente di ridurre gli ingombri. Infine, la pulizia intrinseca di questa tipologia di pressa, senza azionamenti idraulici, con i meccanismi della ginocchiera incapsulati e con le guide lineari, consente al trasformatore di soddisfare le specifiche GMP.
Automazione e controllo della qualità
La movimentazione dei microcomponenti richiede particolare attenzione nell’automazione e nei controlli di qualità. Prima di tutto, per non danneggiare parti così delicate è necessario evitare l’estrazione dallo stampo mediante pinze o per gravità. Inoltre, le cariche elettrostatiche fanno aderire i minuscoli pezzi alle superfici lisce come se fossero magnetizzati e, infine, le piccole dimensioni impediscono la movimentazione manuale dei pezzi. Per queste ragioni, i microcomponenti stampati a iniezione vengono spesso prelevati per aspirazione e depositati con un soffio dentro piccoli contenitori di raccolta.
Il conteggio e la pesatura, operazioni decisamente semplici nello stampaggio tradizionale, diventano impossibili per i pezzi microstampati date le loro dimensioni estremamente ridotte. L’ispezione con videocamera in fase di controllo della qualità, pertanto, deve essere effettuata in linea, sul percorso che va dall’impronta al contenitore di raccolta, oppure direttamente sull’impronta prima dell’estrazione. La videocamera viene quindi installata sullo stampo, in una posizione idonea per permettere di valutare la qualità in relazione alle singole impronte.
Differenze tra LSR e termoplastici
Le differenze più significative nel microstampaggio di termoplastici e LSR sono determinate dalle tecniche di termoregolazione dei due materiali fino alla plastificazione o alla vulcanizzazione (si veda la tabella a pagina 66).
Confronto tra il microstampaggio di silicone liquido (LSR) e resine termoplastiche
Nel caso dei termoplastici, non esistono particolari differenze rispetto allo stampaggio tradizionale: i granuli vengono alimentati al cilindro riscaldato e, una volta al suo interno, le regolazioni della vite e della temperatura consentono una fusione uniforme del materiale, che quindi può venire alimentato alle impronte stampata dopo stampata tramite la valvola a otturazione e i deflettori. Terminato il riempimento, il fuso viene raffreddato e i pezzi, una volta freddi, vengono estratti dallo stampo. Un controllo accurato del processo è essenziale per assicurare una produzione di microcomponenti ai livelli di precisione e qualità richiesti.
Nello stampaggio del LSR, i due componenti che lo costituiscono vengono conservati in serbatoi di dosaggio il cui volume non supera i 0,5-0,7 litri e miscelati a temperatura ambiente dalla vite all’interno del cilindro. L’alimentazione nel cilindro avviene seguendo il percorso più breve possibile in condotti di piccolo diametro, mentre la distribuzione è gestita da una valvola a otturazione e attraverso piccoli deflettori. Il silicone liquido vulcanizza nello stampo a 170-190 °C formando parti caratterizzate da grande elasticità. Lo stampo e il relativo sistema di termoregolazione devono quindi essere progettati per operare a temperature elevate.
Per poter effettuare il microstampaggio del LSR occorre assicurare una perfetta separazione termica tra il cilindro e lo stampo al fine di impedire la vulcanizzazione prematura della miscela liquida all’interno del cilindro. Al momento dell’estrazione dallo stampo i componenti in silicone sono ancora molto caldi. È necessario tenere conto di questo aspetto nella progettazione del sistema di automazione per la movimentazione, e quindi utilizzare materiali costruttivi e strumenti di misura resistenti alle temperature elevate.
Inoltre, occorre variare il flusso d’aria in base alle temperature di processo. I fumi che si generano a causa del calore tendono a dirigersi soprattutto verso l’alto durante l’estrazione dei pezzi, pertanto l’aria va evacuata dal disopra dello stampo in caso di produzioni in camera bianca. Nel microstampaggio delle resine termoplastiche, invece, il sistema di evacuazione dei fumi è posizionato sotto lo stampo e i pezzi vengono raffreddati dall’alto con un flusso laminare d’aria.
I vantaggi del silicone liquido
Accanto alle difficoltà operative, il silicone liquido presenta interessanti vantaggi in termini di estrazione dei pezzi dallo stampo e libertà di design: l’elasticità del materiale previene infatti la possibilità di deformazioni durante l’estrazione e quindi possibili problemi di qualità, con il risultato di offrire una maggiore flessibilità nella progettazione dei componenti; è perfino possibile realizzare piccoli sottosquadri. Al contrario, nel microstampaggio di termoplastici occorre mettere in atto misure specifiche per non danneggiare, durante l’estrazione, i pezzi che, una volta raffreddati, sono perfettamente rigidi.
Una sola macchina per due materiali
Nonostante i requisiti che la pressa a iniezione deve rispettare appaiano a prima vista molto diversi, Engel è in grado di soddisfarli con una sola macchina, assicurando al trasformatore una maggiore flessibilità e la possibilità di ottimizzare il proprio parco attrezzature. La soluzione proposta si basa su una e-motion serie TL nella versione completamente elettrica e senza colonne, equipaggiata con la nuova unità per il microstampaggio di LSR. La configurazione può essere modificata per la lavorazione dei tecnopolimeri in circa 30 minuti grazie a un sistema a innesto rapido.
Ma non è tutto: la medesima pressa è utilizzabile anche per la produzione di pezzi di dimensioni maggiori semplicemente sostituendo il cilindro del gruppo di iniezione con un altro da 15 o da 18. Il flusso del materiale di alimentazione può essere integrato senza problemi nell’unità di controllo della macchina grazie alle interfacce standardizzate (OPC-UA) in dotazione. Tutto questo trasforma l’attrezzatura in un’isola altamente flessibile per la produzione di piccole parti e microcomponenti in LSR o resina termoplastica.
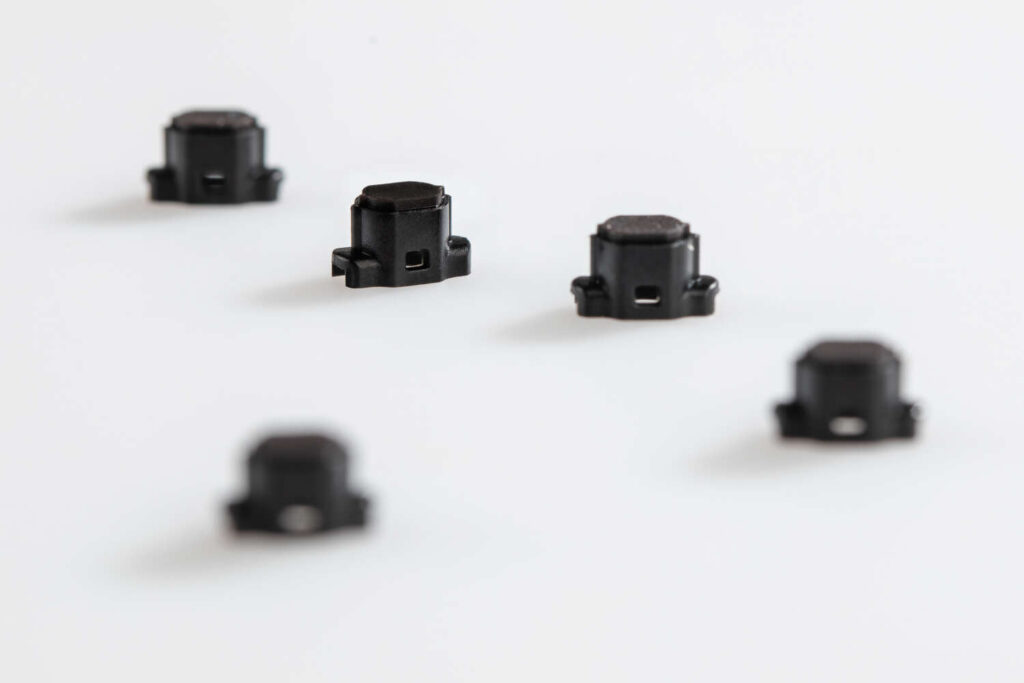
Tecnologie per componenti multimateriale
Un’alternativa al cambio di configurazione della macchina è la produzione in un’unica stampata di microcomponenti bimateriale. L’austriaca Sei Woo Hi-Tech Polymer, specializzata in microtecnologie, sfrutta questo principio per realizzare i microcomponenti di una valvola dell’aria che comanda la funzione massaggio dei sedili per auto (si veda il riquadro PA e LSR in unica stampata).
Il processo prevede prima lo stampaggio dei corpi valvola in poliammide con uno stampo con tavola rotante index da 16+16 impronte montato su una pressa Engel e-victory 140 combi. Nella seconda postazione, il silicone liquido viene iniettato istantaneamente mentre in simultanea vengono stampati altri 16 corpi valvola. In questo modo poliammide e LSR formano un compound chimico. Dal momento che la superficie di contatto è molto ridotta, per ragioni di sicurezza i componenti finiti vengono sottoposti a rinvenimento a 200 °C dopo lo stampaggio allo scopo di creare un legame permanente tra la resina termoplastica e il silicone. Infine, i pezzi passano su una postazione a videocamera che esegue il controllo di qualità sul 100% dei pezzi.
Stabilità, massima ripetibilità e precisione del processo rappresentano i requisiti soddisfatti dalla pressa Engel e-victory nella produzione della valvola. La macchina, dotata di gruppo di iniezione elettrico e gruppo di chiusura servoidraulico senza colonne, combina un’elevata precisione con un ottimo rapporto tra prezzo e prestazioni. La tecnologia senza colonne, infatti, si rivela particolarmente vantaggiosa nelle applicazioni multimateriale perché permette di sfruttare l’intera superficie dei piani portastampo fino al bordo, quindi di montare stampi grandi e ingombranti con tavola rotante index integrata anche su macchine di tonnellaggio relativamente ridotto.
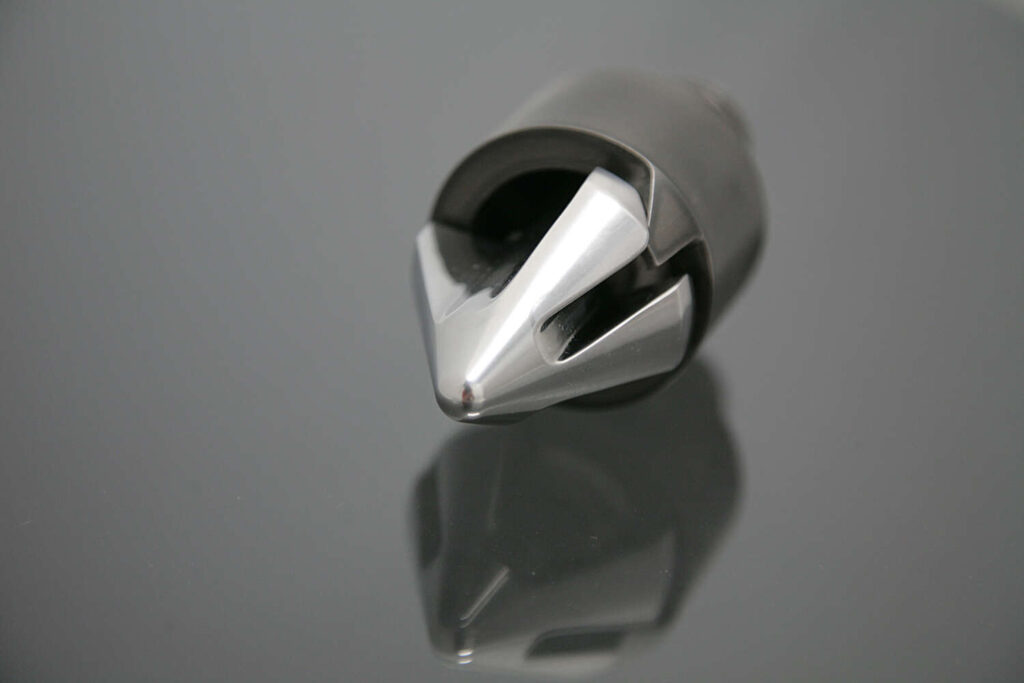
Una precisione ancora maggiore
Come già accennato, uno dei problemi più rilevanti nel microstampaggio è il controllo del peso dei pezzi. È quindi necessaria la massima precisione in tutte le fasi del processo, anche in relazione al peso delle stampate. Un progetto attualmente in corso prevede la realizzazione di connettori in polimero a cristalli liquidi (LCP) con un peso della stampata di 0,484 grammi e un tempo di iniezione di 0,018 secondi. Lo stampatore sta ottenendo ottimi risultati con l’impiego della valvola di non ritorno ad anello scorrevole Smart-shut, grazie alla quale la tolleranza di peso viene ridotta a ±0,0005 grammi (±0,1%). Il funzionamento del dispositivo si basa su un principio semplice: la chiusura della valvola viene comandata attivamente dall’inversione di rotazione della vite e questo significa che quando inizia la fase di iniezione la valvola è già perfettamente chiusa. Engel propone la valvola Smart-shut per la lavorazione di fusi a bassa viscosità, con brevi tempi ciclo, al fine di ottenere la massima riproducibilità dei pesi delle stampate. L’impiego della valvola si sta rivelando particolarmente vantaggioso in applicazioni con corse di iniezione molto corte e velocità di iniezione ridotte.
Processi più semplici
Il silicone si sta diffondendo sempre di più anche nello stampaggio a iniezione di microcomponenti, imponendo ai trasformatori di tecnopolimeri nuove sfide progettuali e tecnologiche, ma anche un parco macchine adeguato. La soluzione proposta da Engel concilia queste esigenze, semplificando – nei limiti del possibile – le criticità del processo.