Le poliammidi (PA) a catena lunga PA 6.10 e PA 6.12, storicamente impiegate per la produzione di monofili, sono oggi utilizzate per innumerevoli applicazioni che richiedono un’elevata resistenza chimica e una buona stabilità dimensionale.
La poliammide 6.10 si ottiene dalla policondensazione di esametilendiammina e acido sebacico. Quest’ultimo è ricavato dai semi della pianta dell’olio di ricino ed entra come costituente della PA 6.10 per più del 60% in peso. Possiamo quindi definire la PA 6.10 come un prodotto in parte proveniente da fonte rinnovabile (figura 1).
La poliammide 6.12, invece, è il prodotto della policondensazione ottenuta da esametilendiammina con acido dodecandioico. In questo caso si ottiene un polimero con materie prime al 100% di origine fossile.
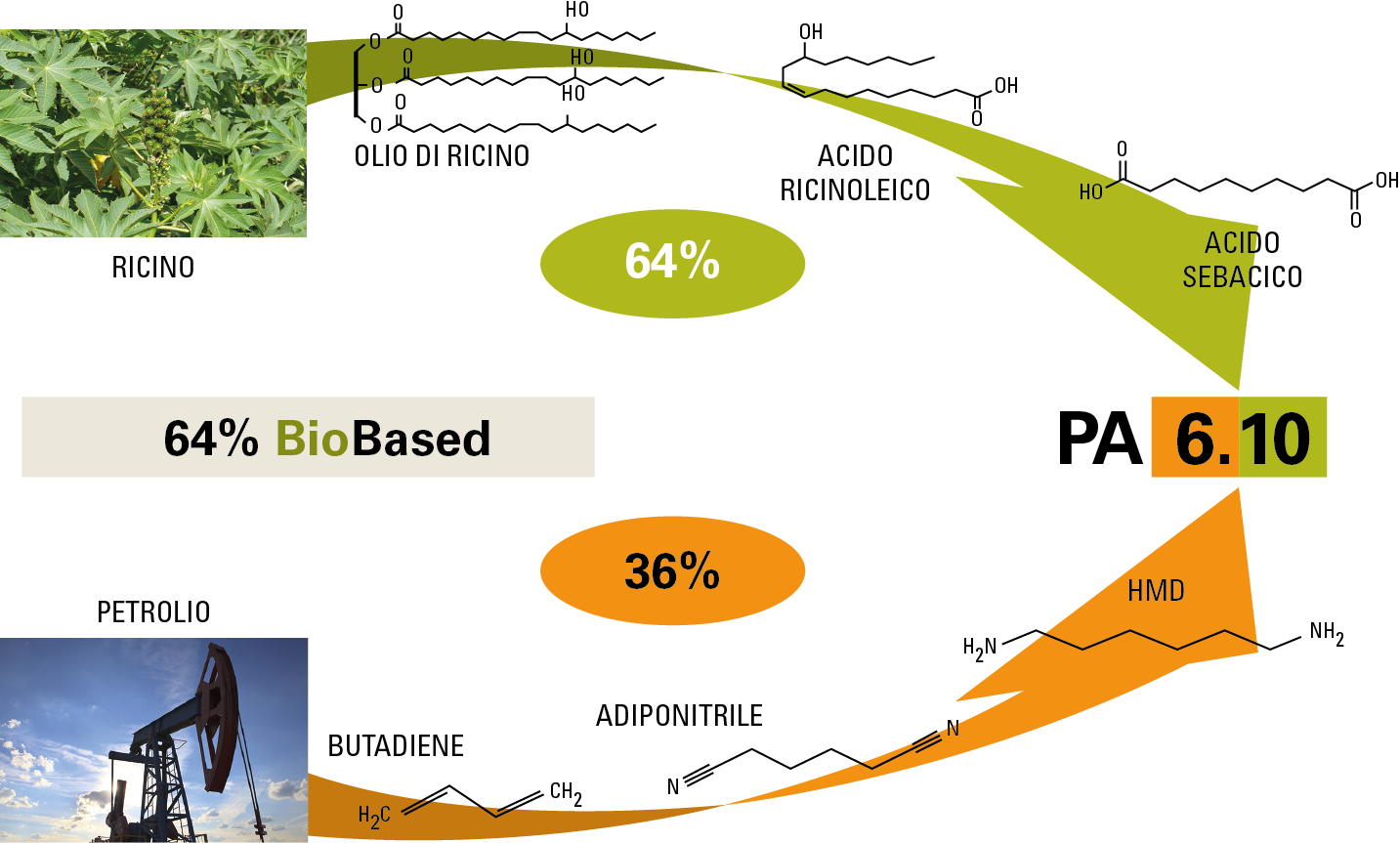
Le caratteristiche distintive delle PA 6.10 e PA 6.12 rispetto ad altre poliammidi possono essere così riassunte:
1 Basso assorbimento di acqua rispetto a PA 6, PA 66, poliftalamide (PPA) e PA 46, e conseguentemente maggiore stabilità dimensionale e minore variazione delle proprietà in caso di variazione del tasso di umidità ambientale. L’assorbimento di acqua è invece leggermente superiore in confronto ad altre poliammidi a catena molecolare lunga come la PA 11 e la PA 12.
2 Elevata resistenza chimica in contatto con soluzioni di cloruro di calcio e cloruro di zinco. Pur essendo adeguata per molte applicazioni, la PA 6.10 mostra prestazioni inferiori rispetto alla PA 6.12. Quest’ultima supera i test previsti dalle normative per diversi tipi di condotti, anche in presenza di connessioni che causano forti sollecitazioni nel materiale, facilitando così la rottura per “stress cracking”. In sintesi, possiamo affermare che la PA 6.12 può sostituire agevolmente numerose applicazioni oggi realizzate in PA 12, incluse le linee per il carburante mono e multistrato.
3 Eccellente resistenza ai perossidi.
4 Resistenza termica superiore rispetto alla PA 11 e alla PA 12. Considerando l’aumento generalizzato delle temperature previste in vari compartimenti nel settore auto (circuito dell’aria, circuito di raffreddamento, alimentazione del combustibile…), la disponibilità di PA 6.10 e PA 6.12 correttamente stabilizzate al calore rappresenta un’alternativa molto interessante a causa dei limiti, in termini di resistenza termica, sia della PA 12 sia della PA 11.
5 Eccellente resistenza al contatto con i liquidi di raffreddamento del motore, che si rivela nettamente superiore alla PA 66. Possono sostituire tubi in gomma rinforzata per i circuiti di raffreddamento e riscaldamento delle auto. In alcuni casi rappresentano una valida alternativa a prodotti come la PPA.
6 Minore permeabilità ai carburanti rispetto alla PA 12.
7 Superiore resistenza all’idrolisi a contatto con acqua calda; tale proprietà, accanto alla buona stabilità dimensionale, rende queste poliammidi adatte per la produzione di componenti sostitutivi dell’ottone nel settore termo-sanitario.
8 Elevata resistenza a contatto con olio per trasmissioni. Considerando il possibile aumento delle temperature, la PA 6.10 e la PA 6.12 possono essere utilizzate come reali alternative alla PA 12 e al metallo nella produzione, per esempio, di condotti della frizione.
Proprietà ed esempi applicativi
Le poliammidi 6.10 e 6.12 sono materiali semi-cristallini, adatti per numerose applicazioni a elevato contenuto tecnico. Come per altri polimeri a base poliammidica, esistono versioni adatte allo stampaggio a iniezione e all’estrusione. Inoltre, possono essere facilmente aggiunte cariche, stabilizzanti e additivi per conferire particolari proprietà. La loro trasformazione non presenta alcuna difficoltà, tanto che possono essere considerati “facili da stampare” e “facili da estrudere” soprattutto se paragonati a materiali speciali come la PPA e la PA 46.
Stabilità dimensionale
La figura 2 mostra un confronto relativo all’assorbimento di acqua misurato su provini condizionati a 23 °C in ambiente con umidità relativa al 50% e su provini portati a saturazione.
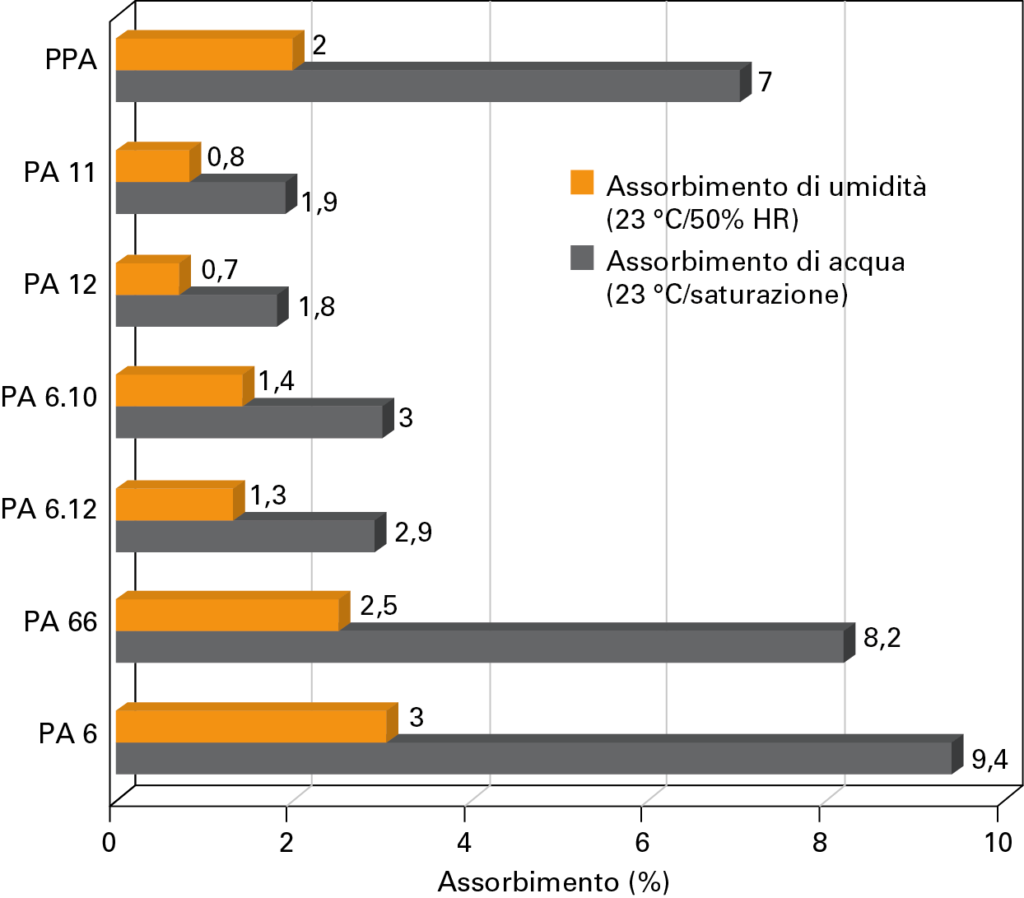
Si osserva come la PA 6.10 e la PA 6.12, a saturazione, assorbano circa un terzo dell’acqua rispetto alla PA 6 e alla PA 66, e meno della metà rispetto alla PPA. Rappresentano quindi una valida alternativa per le applicazioni che richiedono una buona stabilità dimensionale al variare delle condizioni di umidità ambientale. Questa caratteristica è particolarmente apprezzata per tutti i particolari che devono rispettare tolleranze dimensionali strette.
Temperatura di fusione e HDT
La figura 3 illustra un confronto tra le temperature di fusione e i valori di temperatura di deflessione (Heat Deflection Temperature o HDT).
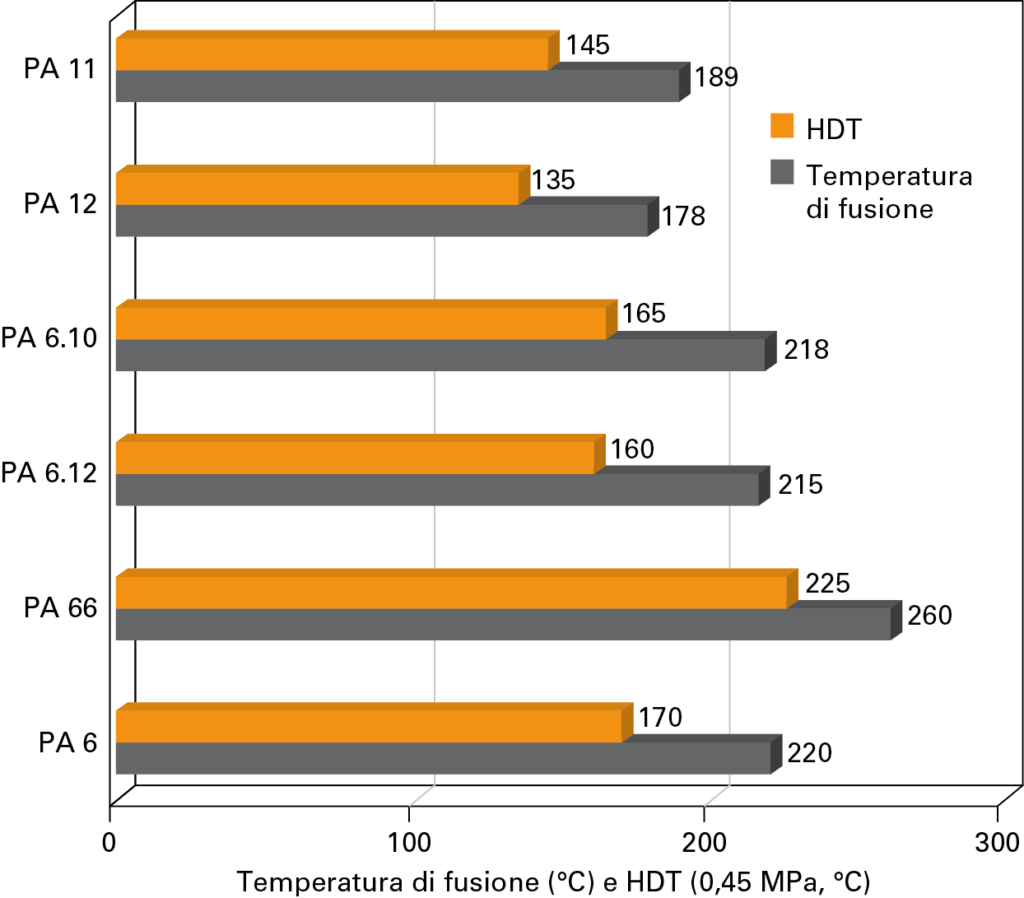
Polimeri a catena lunga, come la PA 11 e la PA 12, hanno limitazioni di impiego a causa dell’aumento delle temperature di utilizzo in vari componenti quali condotti del carburante, della frizione o dei liquidi di raffreddamento del motore. Tali limiti sono ancora più evidenti in caso di componenti sottoposti a sollecitazioni elevate. Le PA 6.10 e 6.12, grazie a valori superiori della temperatura di fusione (+40 °C) e dell’HDT (compreso tra +20 e + 25 °C), se opportunamente stabilizzate per aumentare la resistenza alla sollecitazione termica prolungata, possono effettivamente rappresentare un’alternativa tecnica eccellente a costi competitivi. Possono inoltre essere considerate valide in sostituzione alla PPA per temperature di utilizzo non troppo elevate, come nel caso delle applicazioni per particolari del circuito termo-sanitario e del circuito di raffreddamento delle auto, che devono resistere fino a 135 °C.
Resistenza a contatto con acqua-glicole
La figura 4 mostra l’andamento della resistenza a trazione a seguito di immersione in soluzioni di acqua-glicole in proporzione 50:50.
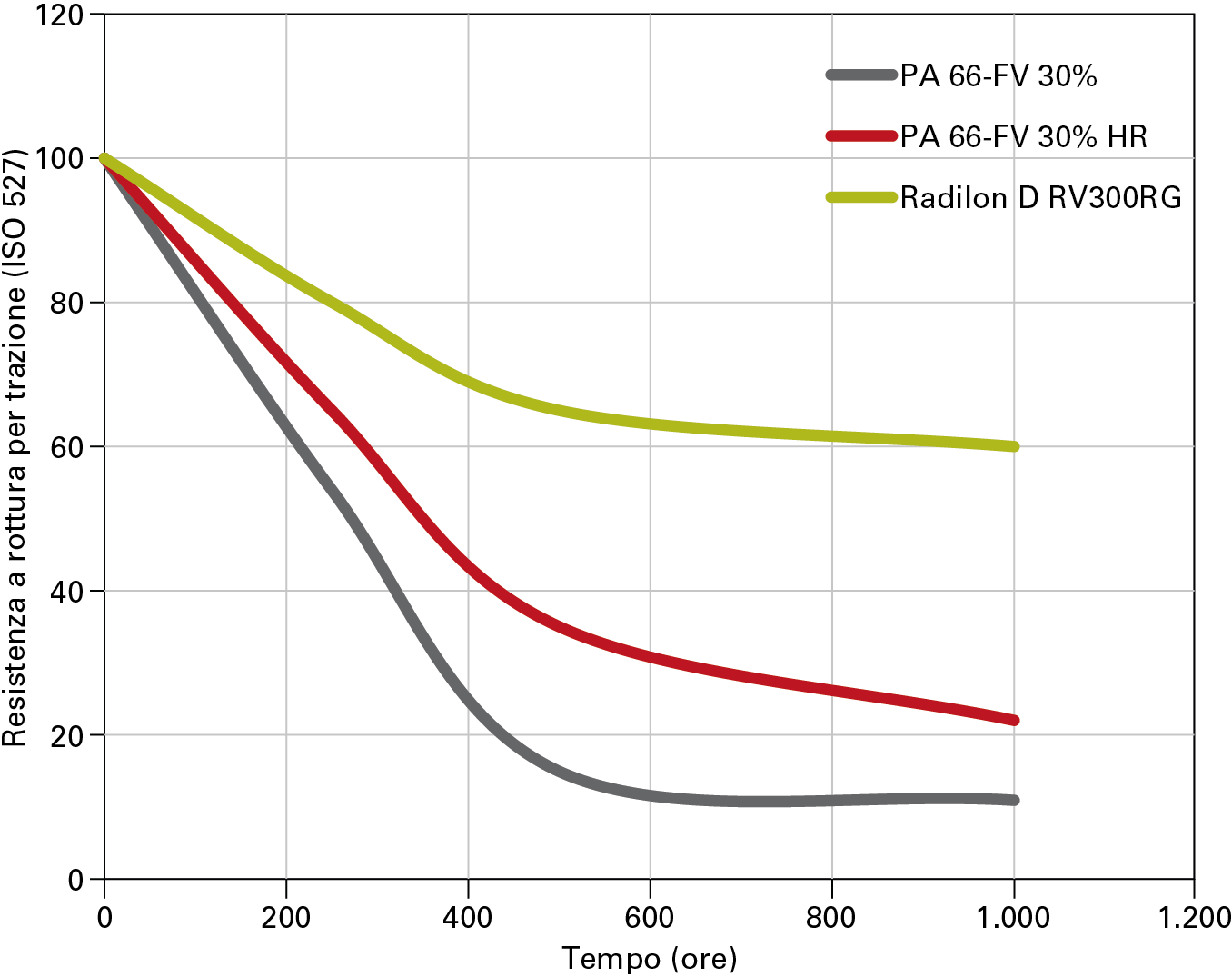
I test confermano l’ottimo comportamento della PA 6.10 caricata con fibra di vetro al 30% (Radilon® D RV300RG di RadiciGroup) rispetto alla PA 66 standard caricata con fibra di vetro al 30% e alla PA 66 caricata con fibra di vetro al 30% e stabilizzata all’idrolisi. Grazie a questa importante proprietà, la PA 6.10 viene oggi proposta per applicazioni nel settore automobilistico, dove la PA 66 non è in grado di rispettare i capitolati. Inoltre, potrebbe rappresentare una valida alternativa alla PPA, offrendo vantaggi aggiuntivi quali una maggiore facilità di trasformazione e un minor assorbimento di acqua.
Resistenza a immersione in acqua
La figura 5 riporta il confronto dei risultati ottenuti da un test di immersione in acqua relativo a una PA 6.10 caricata con fibra di vetro al 50% (Radilon D RV500RKC 106 Nat) e una PPA caricata con fibra di vetro al 40%.
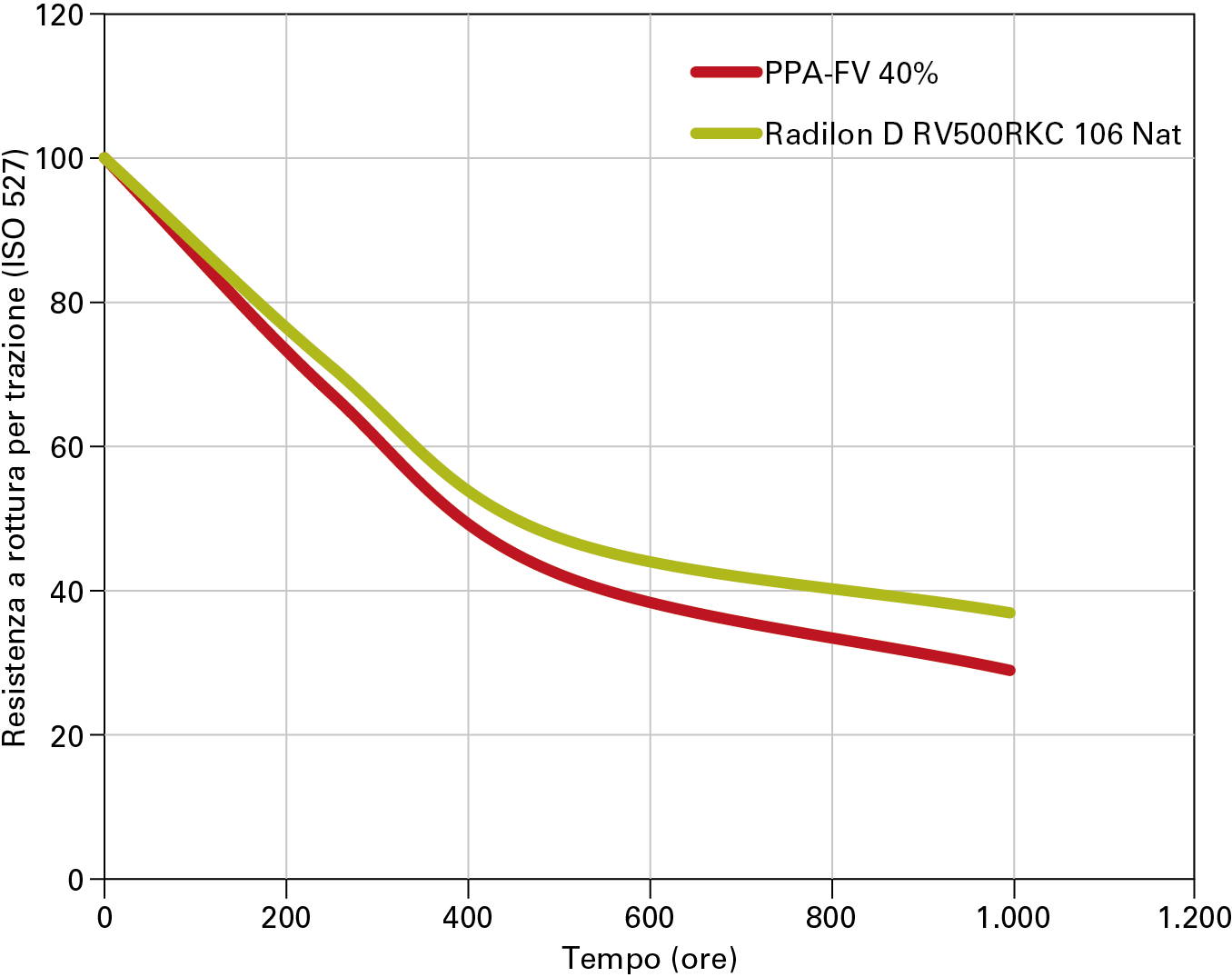
Si noti la miglior tenuta della PA 6.10. Questa linea di PA 6.10, formulata per resistere meglio alla glicolisi e con contenuto di carica variabile dal 30 al 60%, viene oggi proposta sempre di più per l’impiego nei settori termo-sanitario, delle macchine da caffè e per le applicazioni in cui la resistenza all’idrolisi e la stabilità dimensionale sono fattori chiave. Esistono versioni già omologate per il contatto con acqua potabile secondo le norme KTW e ACS.
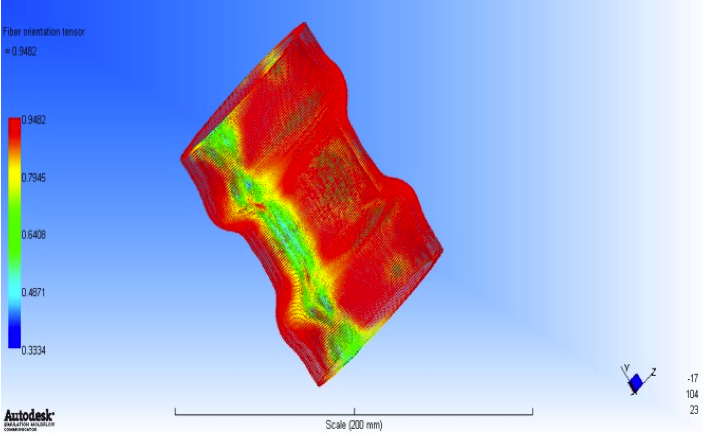
La figura 6 mostra il modello semplificato di un raccordo per circuito termo-sanitario. Il componente richiede, oltre all’eccellente resistenza all’idrolisi, elevate caratteristiche meccaniche, quali la resistenza alla rottura a trazione e al creep.
Condotti pneumatici
La PA 6.10 trova oggi impiego nella produzione di tubi per applicazioni pneumatiche industriali e per il trasporto dell’aria compressa.
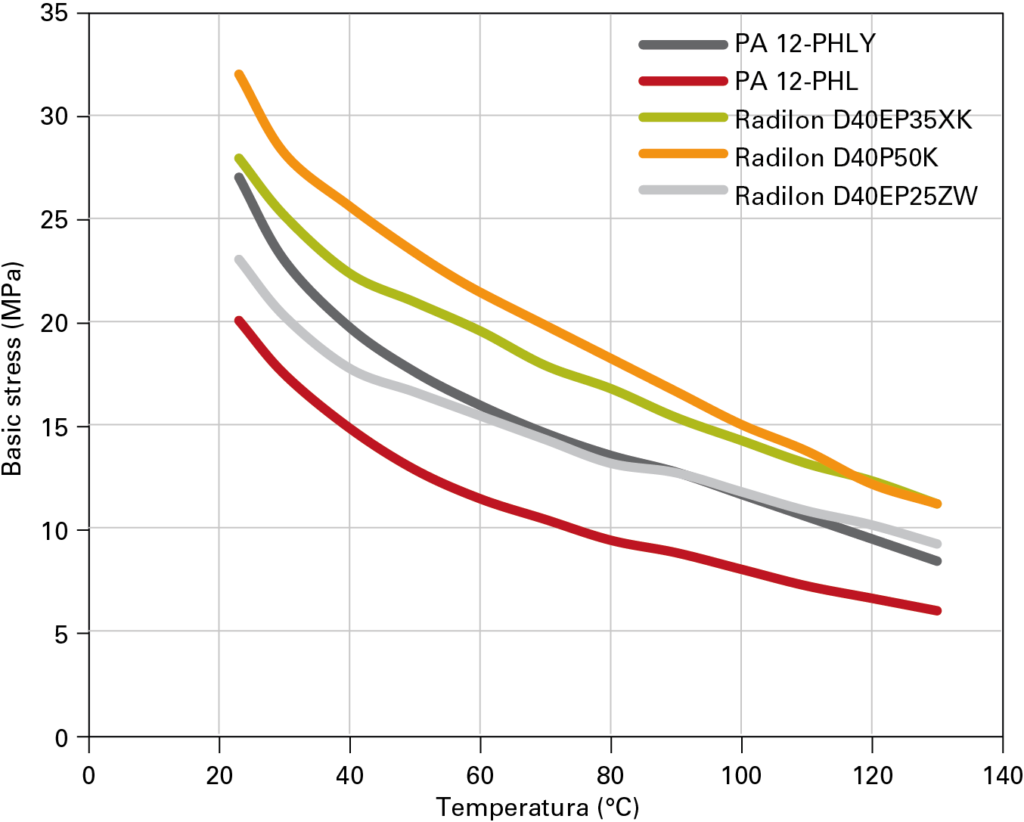
Nella figura 7 sono riportati i valori relativi alla sollecitazione calcolata secondo la norma DIN 73378 (legata alla pressione di scoppio dei condotti) per diversi materiali. I riferimenti (linee tratteggiate) sono relativi alla PA 12 flessibile (PHL) e semi-flessibile (PHLY). Nello stesso grafico viene riportato il comportamento di tre formulazioni su base PA 6.10 in grado di superare agevolmente i valori raggiunti dalla PA 12, soprattutto alle temperature elevate.
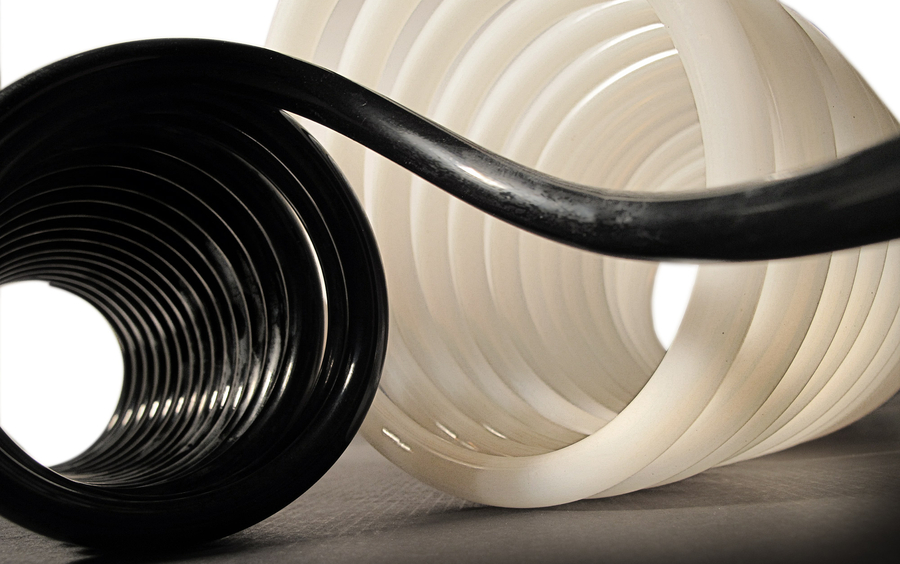
La figura 8 mostra tubi a spirale prodotti con Radilon D40P50UK, un materiale che offre buona trasparenza, resistenza agli UV, facilità di lavorazione e attitudine alla pigmentazione in una vasta gamma di colori.
Polimeri per condotti dell’aria
I condotti dell’aria per sistema frenante dei camion devono superare i capitolati più severi previsti da diverse normative. Le caratteristiche principali richieste sono: elevata pressione di scoppio, resistenza all’urto anche a basse temperature, resistenza allo “stress cracking” in presenza di soluzioni di cloruro di zinco, buona flessibilità per facilitare il montaggio. I tubi estrusi in Radilon D 40EP25ZW (figura 9) hanno superato i test secondo le normative DIN 74324, DIN 73378, ISO 7628, SAE J844 e FMVSS 106.
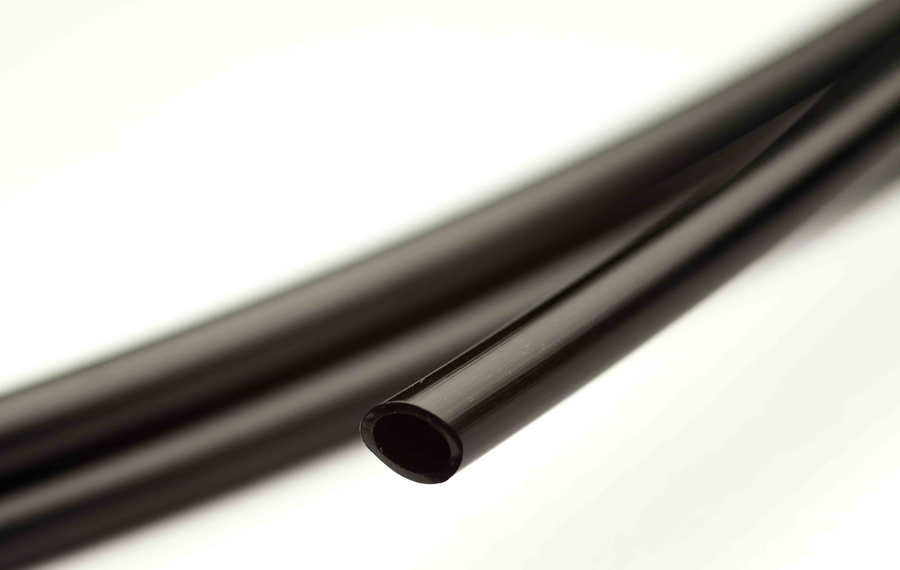
Condotti del carburante e dell’olio della frizione
Le case automobilistiche richiedono per i condotti del carburante (diesel e benzina) il superamento dei test di immersione in soluzione con cloruro di zinco, includendo la zona di contatto tra tubo e connettore dove lo sforzo indotto dal montaggio è elevato.
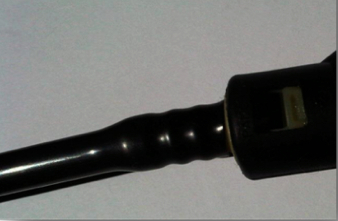
La figura 10 mostra come, dopo immersione per 200 ore in una soluzione di acqua e cloruro di zinco in proporzioni 50:50, non vi sia attacco per “stress cracking” utilizzando la PA 6.12 e anche alcuni tipi speciali di PA 6.10. Al contrario, un materiale sottoposto al medesimo test, non resistente allo “stress cracking”, presenta delle fessurazioni simili a quelle riportate nella figura 11.
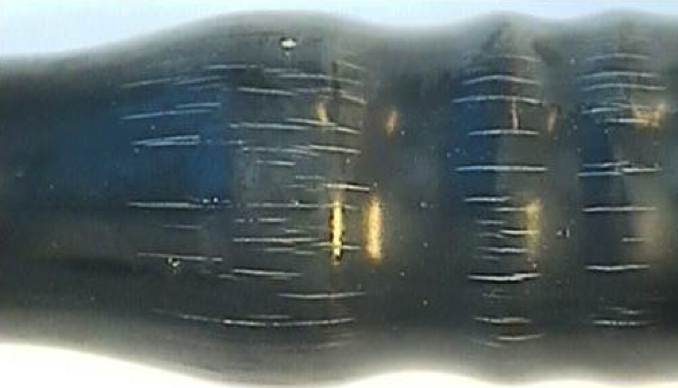
La PA 6.12 è adatta a superare questo test anche nel caso di materiali con modulo più elevato, come nel caso del materiale rigido per estrusione Radilon DT 40EP75W (figura 12).
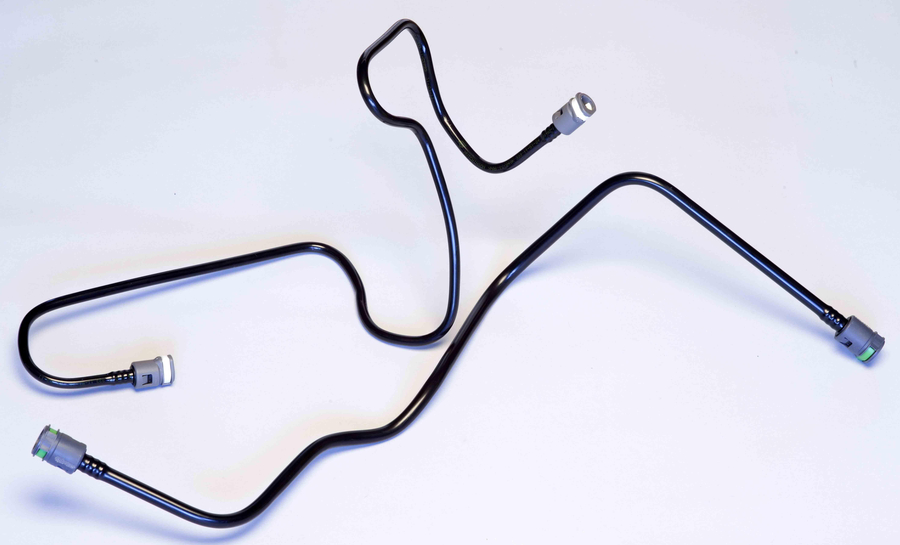
del 38% superiore rispetto alla PA 12
Le figure 13 e 14 illustrano, invece, il comportamento di una PA 6.12 per estrusione, rigida (Radilon DT 40EP75W), immersa in olio per trasmissione DOT 4 a 100 °C fino a 1.500 ore. Il mantenimento delle proprietà è migliore rispetto alla PA 12 impiegata per la stessa applicazione.
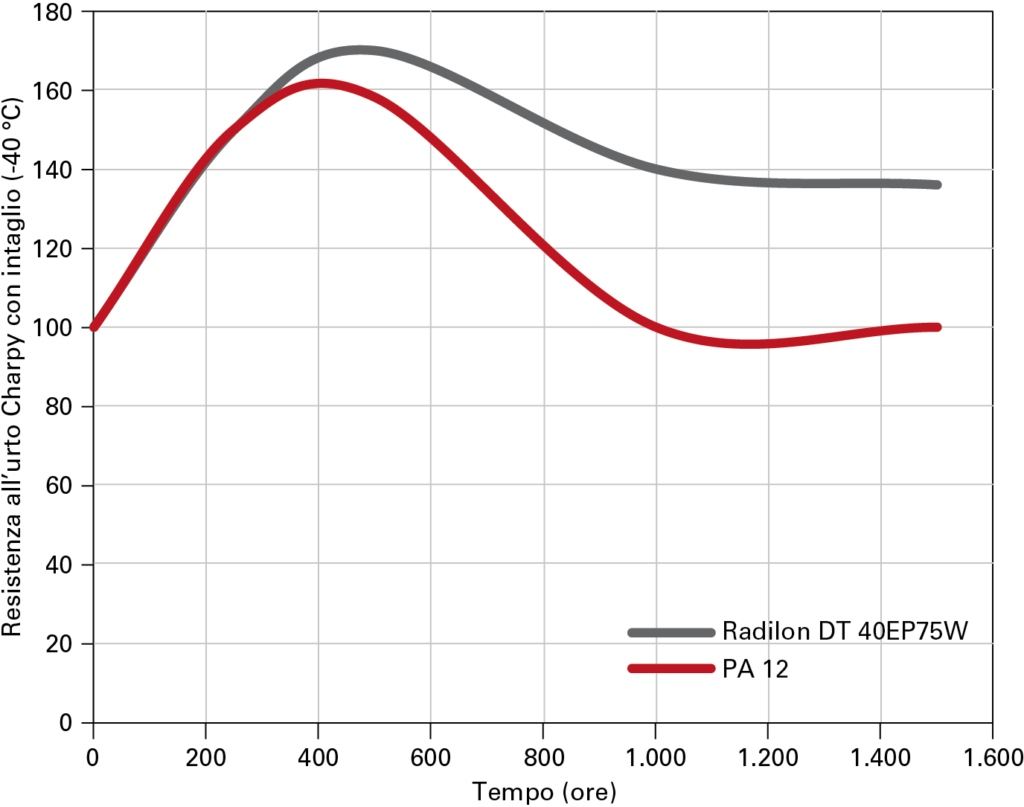
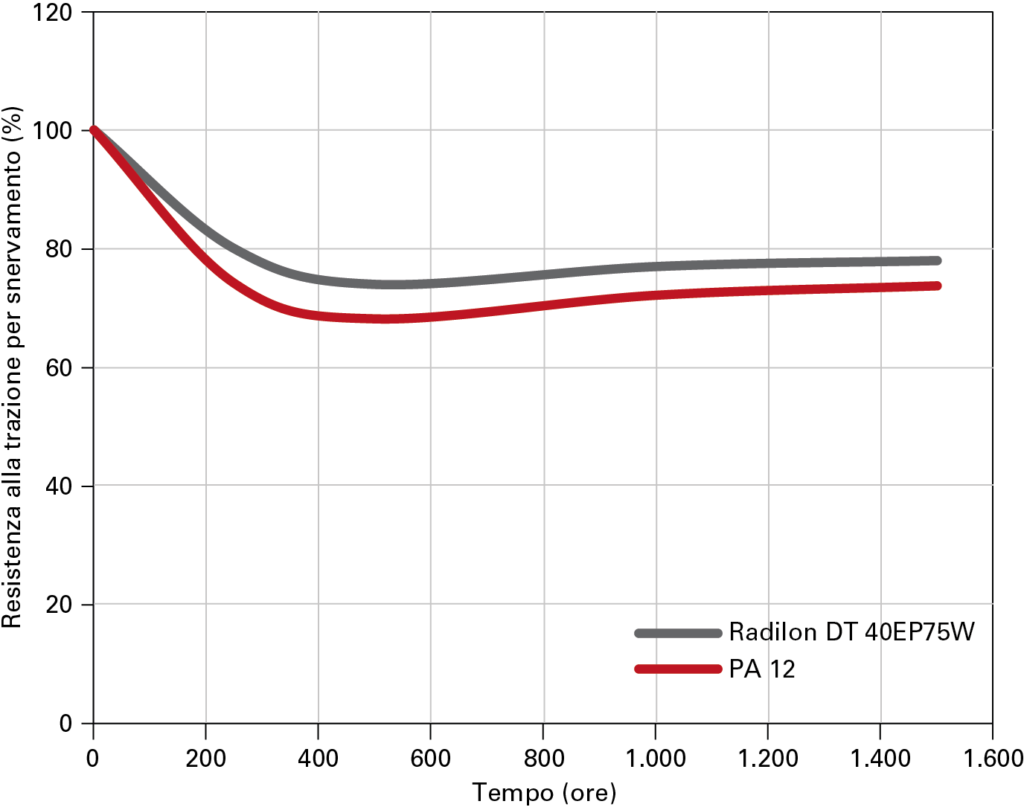
Connettori per condotti del carburante
In molti casi, i connettori per condotti del carburante (figura 15) vengono già realizzati con PA 6.10 per stampaggio a iniezione. La formulazione tipica prevede materiali con un contenuto di fibra di vetro del 30%.
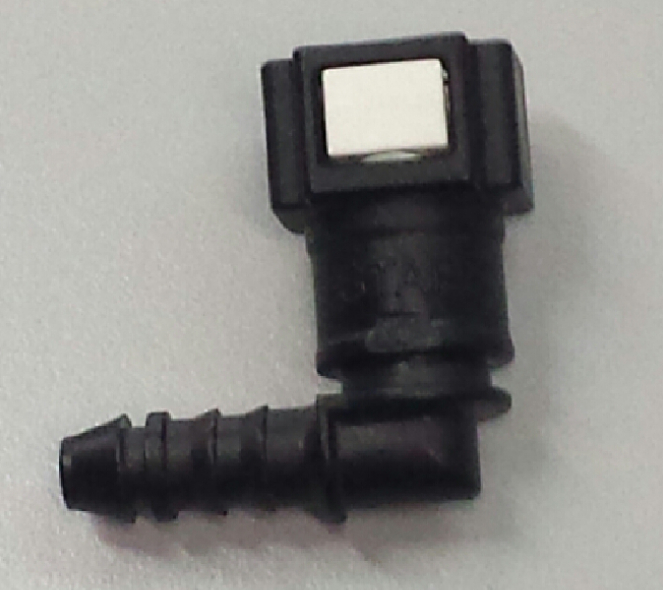
La PA 6.10 caricata con il 30% di fibre di vetro è in grado di sostituire la PA 12 con lo stesso tipo e quantità di carica grazie all’eccellente resistenza termica e alla stabilità dimensionale.
La figura 16 riporta l’andamento della resistenza a trazione a rottura e della deformazione a rottura per una PA 6.10 caricata con il 30% di fibra di vetro stabilizzata al calore (Radilon D RV300W); come si può osservare, non si rilevano variazioni significative nelle proprietà dopo invecchiamento termico in aria fino a 2.000 ore a 130 °C.
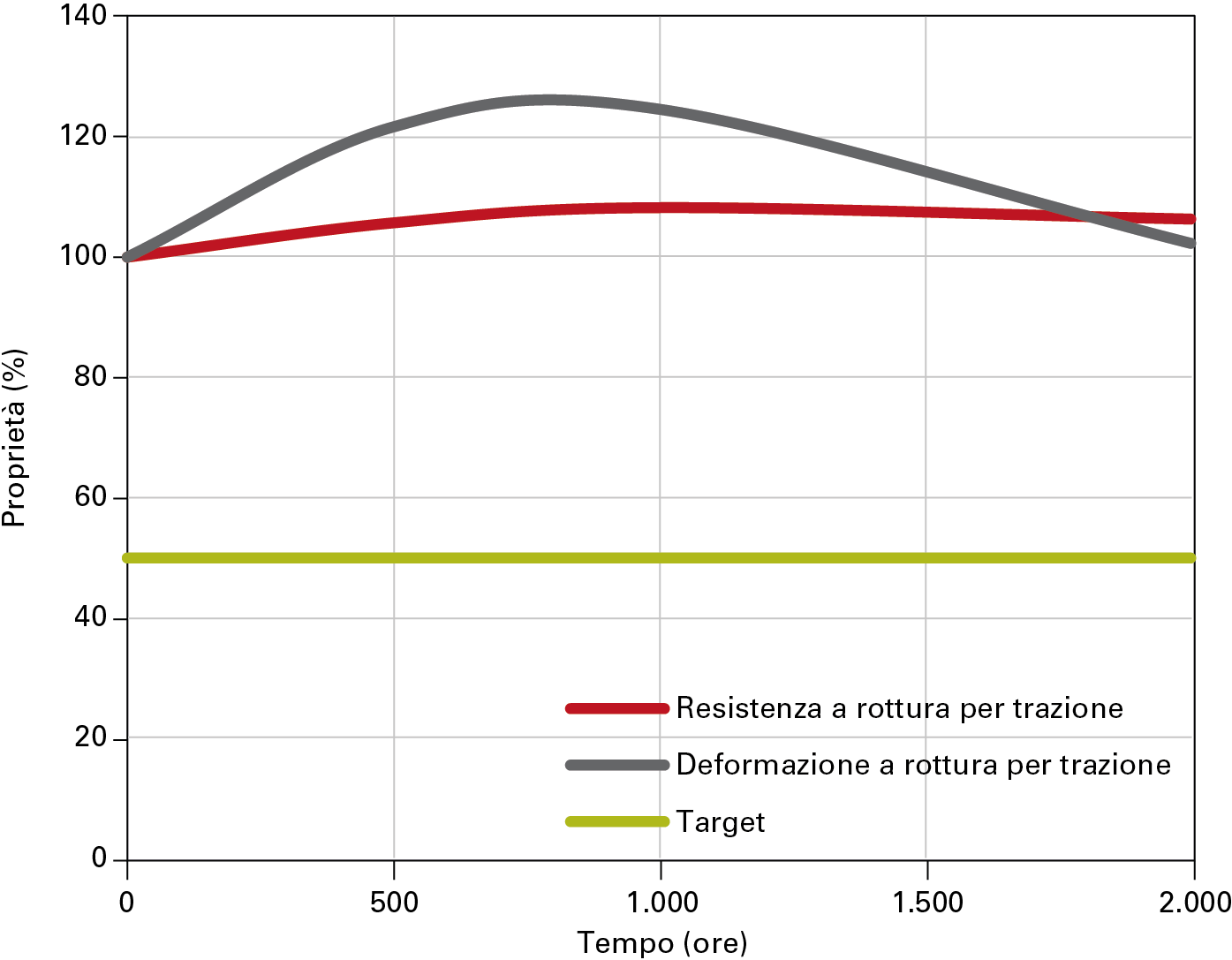
Fattori decisivi
Negli ultimi anni abbiamo assistito all’introduzione progressiva di polimeri a base di PA 6.10 e PA 6.12 in sostituzione di materiali metallici e di altre poliammidi a catena lunga. Questo è stato possibile grazie ad alcune caratteristiche peculiari di tali materiali, particolarmente interessanti per la loro eccellente resistenza chimica, stabilità dimensionale, facilità di trasformazione. Se confrontate con altri polimeri a catena lunga, come la PA 12 e la PA 11, possono offrire notevoli vantaggi grazie alla maggiore resistenza termica, e rispondere meglio alle nuove esigenze prestazionali legate all’aumento delle temperature di utilizzo.
Caratteristiche come l’eccellente resistenza all’idrolisi potrebbero, in breve tempo, aprire nuove prospettive nel settore termo-sanitario e automobilistico in sostituzione di metalli e di polimeri speciali difficili da trasformare. L’impiego di PA 6.10 di origine parzialmente biologica, inoltre, permette di realizzare soluzioni a impatto ambientale sempre più ridotto, un fattore sempre più importante e decisivo nella scelta dei materiali del futuro.