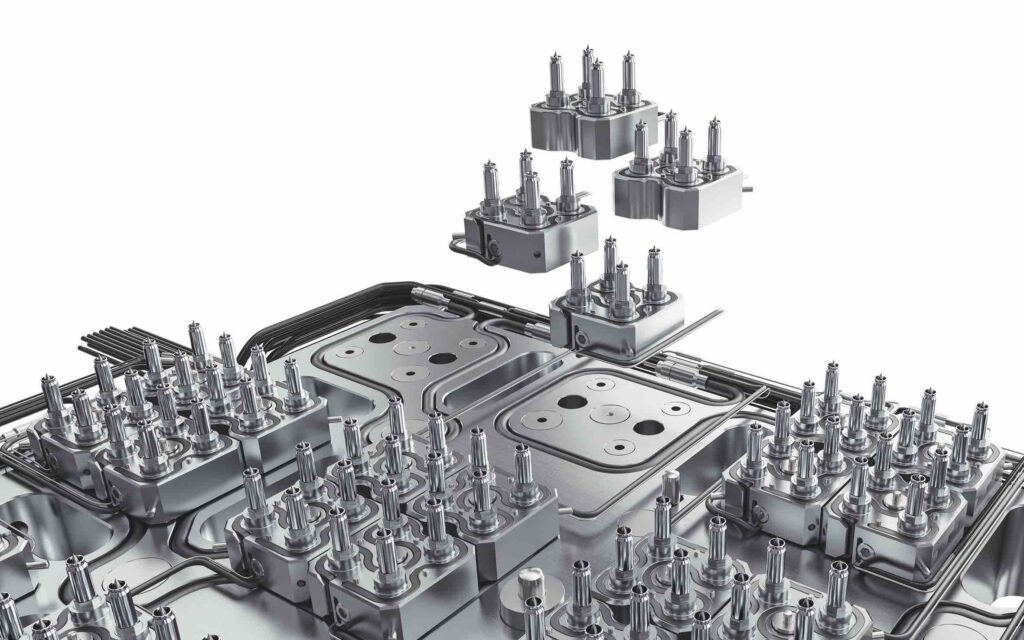
Da molti anni l’industria europea dello stampaggio a iniezione è sottoposta a forti pressioni per migliorare costantemente produttività ed efficienza, con l’obiettivo di non perdere competitività sui mercati globali. L’esplosione della recente pandemia ha mostrato le debolezze dell’industria di settore, spesso incapace di soddisfare con una risposta immediata l’accelerazione della domanda di molti componenti plastici, imballaggi, erogatori per disinfettanti e detergenti, dispositivi medici come siringhe, pipette e provette.
Conciliare prestazioni e investimento
Tra le diverse strategie volte a migliorare l’efficienza del processo di stampaggio a iniezione, intesa come riduzione del tempo ciclo, risparmio energetico ed elevata automazione, la più semplice e immediata – e anche la più “antica” – è l’aumento delle cavità dello stampo. La soluzione, nel tempo, ha permesso lo sviluppo di tecnologie come i sistemi a canali caldi, che ne hanno sostituite altre più inefficienti e limitate come i canali freddi, trasformando gli stampi moderni in attrezzature compatte in grado di produrre 16, 32, 48 o più componenti per ciclo.
L’evoluzione delle presse a iniezione, oggi molto veloci e precise, ha reso ancora più interessante l’idea di concentrare il maggior numero di impronte possibile in un singolo stampo, operazione che può avvenire anche quando è necessario scendere a compromessi, soprattutto in termini di bilanciamento naturale del canale caldo e di stabilità dello stampo, ma anche di investimento.
I vantaggi dell’iniezione laterale diretta
Ewikon offre diverse soluzioni per gli stampi multi cavità. Quella probabilmente più nota ed apprezzata è l’HPS III-MH (nell’immagine in alto) che, dal suo lancio sul mercato nel 2008, ha definito nuovi standard globali nella trasformazione di una gamma sempre più ampia di materiali plastici e nella semplicità e velocità di manutenzione. Sviluppata in origine per le applicazioni medicali, HPS III-MH è stata la prima serie di ugelli in grado di convincere l’esigente mercato dello stampaggio tecnico, alle prese con la trasformazione di tecnopolimeri avanzati, e anche il settore dell’elettronica grazie all’eccellente controllo di temperatura.
Basandosi sulla piattaforma degli ugelli MH, Ewikon ha sviluppato una speciale soluzione a otturazione, con l’alimentazione del fuso laterale all’otturatore, che permette di costruire stampi a elevato numero di impronte, di ottenere interassi tra i punti di iniezione a partire da soli 9 millimetri e quindi di iniettare in zone molto difficilmente raggiungibili. Negli anni, le soluzioni a iniezione laterale diretta e otturazione HPS III-MH hanno contribuito positivamente allo sviluppo di stampi che spesso hanno superato la barriera delle 48 impronte, spingendosi addirittura fino a 192.
La tecnologia a “micro collettori”
La disponibilità sul mercato di un’ampia gamma di ugelli individuali compatti permette di concentrare un numero elevato di punti di iniezione in un’area limitata, ma complica alcuni aspetti critici: il bilanciamento del sistema e la stabilità dello stampo. Oltre all’esigenza di concentrare questi aspetti, gli end user sono spesso alla ricerca di soluzioni per una produzione efficiente su larga scala, anche di componenti di piccole dimensioni (con pesi spesso inferiori a un grammo), oppure per trattare resine termosensibili, definendo importanti restrizioni nel tempo di residenza del sistema.
La tecnologia a “micro collettori” – sul mercato dal 2015 – è la risposta di Ewikon a queste problematiche: permette di realizzare stampi robusti, con sistemi naturalmente bilanciati ed estremamente compatti in configurazioni standard da 16 a 192 impronte, mantenendo al contempo un investimento contenuto. Il sistema, ideale per chiusure dal diametro ridotto, prevede puntali termoconduttivi avvitati a distributori molto compatti, con un interasse tra i punti di iniezione di soli 30 millimetri. Uno dei vantaggi primari è la riduzione del numero di zone di controllo, con la significativa eliminazione dei cablaggi e quindi dell’importante spazio necessario per dirigerli verso la scatola di connessione. Questo risparmio – che si traduce in oltre 600 metri lineari di cavi in meno su stampi a 192 cavità – permette di compattare ulteriormente gli stampi e di utilizzare i volumi recuperati per stabilizzare gli stampi con piloni di supporto nelle piastre.
Ugelli per la produzione di massa di micro componenti
Il lancio di L2X-Mikro nel 2017 ha visto l’introduzione di una nuova e più potente serie di ugelli riscaldati direttamente. Sempre mantenendo il bilanciamento naturale del sistema, la stabilità dello stampo e gli interassi di 30×30 millimetri tra le cavità, introduce la possibilità di trattare resine tecniche e caricate. L’anno scorso, la gamma è stata ampliata introducendo una versione a otturazione studiata per soddisfare il forte aumento della domanda di imballaggi (soprattutto farmaceutici e medicali). Grazie a un sistema a otturazione compatto e sincrono, il dispositivo apre le porte alla produzione di massa anche di micro componenti, con pesi da 0,05 a 5 grammi per punto di iniezione.
Controllo sempre più efficiente
La capacità di installare un numero sempre maggiore di cavità sulla pressa a iniezione e di utilizzare macchine di tonnellaggio inferiore per soddisfare le medesime esigenze produttive è uno degli ingredienti primari per ottenere la massima efficienza e conciliare l’aspetto economico, oggi più che mai afflitto dallo shortage e dai prezzi crescenti delle materie prime. La combinazione dei moderni sistemi di controllo della temperatura pro CONTROL e specialmente la digitalizzazione degli stampi a iniezione, possibile grazie alle unità smart CONTROL, permette di progettare stampi moderni, compatti, modulari e ben controllati, elementi che rappresentano la chiave per il successo nel cambiamento nell’industria dello stampaggio.