Il PET e il PBT sono polimeri versatili caratterizzati da eccellenti proprietà termiche e meccaniche, ampiamente utilizzati in applicazioni che spaziano dalle fibre tessili al packaging, fino ai componenti strutturali ingegneristici
di Giovanni Lucchetta (Università di Padova) e Andrea Cavalet (Sipa)
I poliesteri rappresentano una classe di polimeri caratterizzati dalla presenza del gruppo funzionale degli esteri lungo la loro catena principale (vedi figura 1). Poliestere è il nome di un ampio gruppo di materie plastiche che possono essere sia termoindurenti che termoplastiche e il poliestere termoplastico può essere a sua volta amorfo o semicristallino. Tra i semicristallini troviamo i tecnopolimeri PET e PBT, ma anche plastiche più avanzate come i polimeri a cristalli liquidi (LCP), su cui torneremo in seguito. In questo articolo ci concentreremo sui poliesteri termoplastici semicristallini PET e PBT.
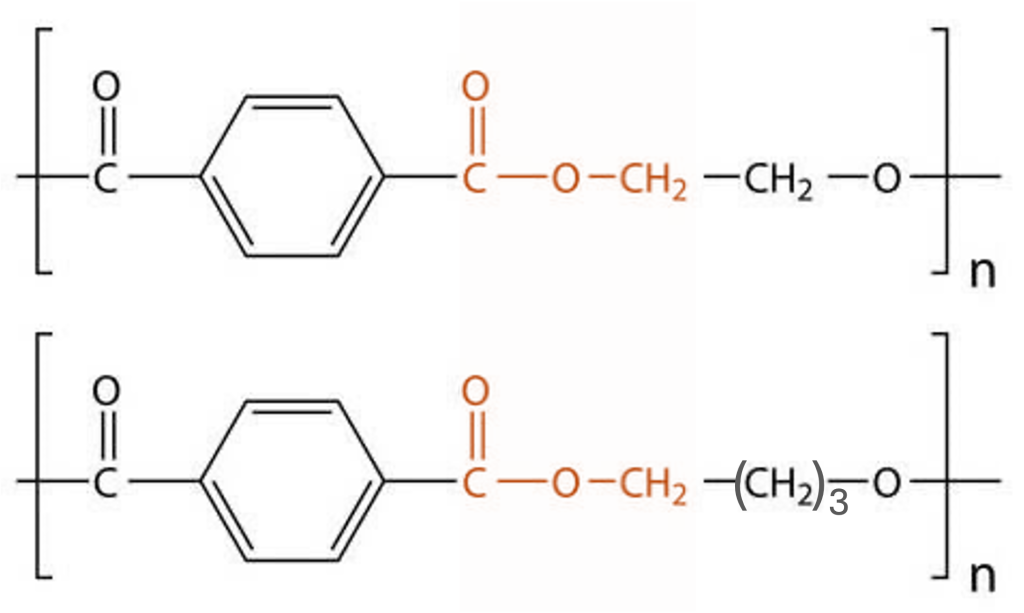
Fu Wallace Carothers, lo scienziato che in seguito inventò il Nylon, a scoprire per la prima volta il poliestere alla fine degli Anni Venti nei laboratori DuPont degli Stati Uniti. Tuttavia, DuPont non lanciò il materiale sul mercato e solo nel 1940 l’azienda tedesca Agfa lo introdusse come fibra sintetica. Il primo grado commerciale adatto allo stampaggio a iniezione fu lanciato a metà degli Anni Sessanta da Akzo, nei Paesi Bassi, ma la vera svolta come polimero tecnico arrivò solo negli Anni Ottanta.
Il poliestere combina elevata rigidità, resistenza alle alte temperature e buone proprietà elettriche e, per questo, è molto utilizzato nell’industria elettrica ed elettronica e nell’industria automobilistica. Tuttavia, solo una minima parte di tutti i poliesteri prodotti viene utilizzata per lo stampaggio a iniezione e l’estrusione, perché il suo utilizzo maggiore è per le fibre, il packaging e i film.
Le fibre di poliestere per tessuti e nontessuti sono disponibili in diverse forme: come fiocchi, come filo e anche come microfibra. Sono ampiamente usate nell’abbigliamento, negli arredi per la casa e come ovatta per l’imbottitura di vestiti, mobili e oggetti per la casa. Essendo il poliestere un materiale idrofobo, permette di realizzare tessuti molto resistenti alle macchie, oltre che alle pieghe e al restringimento.
Il polietilentereftalato (PET)
Il PET domina il mercato del poliestere grazie alla facilità di accesso alle materie prime, alla semplicità del processo di sintesi e alle sue eccezionali proprietà meccaniche e chimiche, oltre alla sua riciclabilità. Nel 2022, il valore del mercato globale del PET era stimato in 33 miliardi di dollari e si prevede che crescerà fino a raggiungere i 43 miliardi di dollari entro il 2029, con un tasso di crescita annuo composto (CAGR) del 3,2%.
Il PET possiede eccellenti proprietà meccaniche e termiche, ma è estremamente fragile se non essiccato adeguatamente al di sotto dello 0,02% di umidità prima della lavorazione. A confronto, il PBT richiede un’umidità residua dello 0,04% e la poliammide dello 0,2%. Inizialmente, questo ha creato difficoltà, in quanto erano pochi i produttori disponevano delle competenze tecniche e delle attrezzature adeguate per un corretto processo di essiccazione. Tuttavia, con l’evoluzione e il miglioramento delle tecnologie di essiccazione, attualmente la maggior parte dei produttori è in grado di processarlo correttamente.
Il PET è caratterizzato da una struttura molecolare non ramificata, composta da catene lineari lunghe. Questo polimero si forma attraverso una reazione di condensazione reversibile, il che porta a una distribuzione relativamente semplice delle lunghezze delle catene molecolari. Per gli utilizzatori finali, la struttura chimica di uno specifico grado di PET può essere efficacemente descritta utilizzando solamente due parametri: la viscosità intrinseca (IV), che è legata al peso molecolare, e il contenuto di copolimeri.
Il PET è un polimero semicristallino, il che significa che allo stato solido presenta regioni cristalline circondate da zone amorfe. Dato che la forma cristallina è energeticamente più stabile, il PET tenderebbe a cristallizzare se fosse lasciato raffreddare lentamente. Tuttavia, a causa della lunghezza e dell’intreccio delle sue molecole, può anche rimanere in uno stato amorfo se viene raffreddato rapidamente nel processo di trasformazione (ad es. a contatto con uno stampo condizionato a bassa temperatura).
La cristallizzazione del PET può avvenire a temperature in cui le catene polimeriche sono abbastanza mobili da riorganizzarsi. La rapidità con cui avviene la cristallizzazione dipende da vari fattori, come la temperatura, la viscosità del polimero e il grado di copolimerizzazione. Mentre temperature più elevate facilitano la cristallizzazione, l’aumento di viscosità e la presenza di copolimeri ottengono l’effetto contrario.
L’intervallo di temperatura necessario per la cristallizzazione del PET si colloca tra la temperatura di transizione vetrosa (Tg, varia tra 67 e 81°C) e la temperatura di fusione (Tm, varia tra 245 e 260°C). Sotto la Tg, la resina è definita “vetrosa” in quanto la mobilità delle sue catene polimeriche è fortemente limitata, rendendole quasi immobili, sia che si trovino in uno stato amorfo che cristallino. Superata la temperatura di fusione, le catene polimeriche acquisiscono troppa energia per potersi organizzare in strutture ordinate e stabili, risultando così in una resina fusa e amorfa. Nell’intervallo tra la Tg e la Tm, invece, le catene polimeriche dispongono di sufficiente energia per riorganizzarsi in una struttura più stabile e termodinamicamente favorevole, permettendo così alla resina di cristallizzare.
Per capire meglio come il PET possa cristallizzare in modi diversi, esaminiamo il suo percorso attraverso il processo bistadio comunemente usato nella produzione di bottiglie e contenitori a partire dal pellet.
Dal pellet alla bottiglia
Nella granulazione del PET, il materiale subisce una cristallizzazione termica che lo porta a raggiungere un livello di cristallinità tra il 50% e il 70%. Durante questo processo, i cristalli formati durante il raffreddamento si organizzano in strutture sferiche note come “sferuliti”. Queste strutture iniziano a svilupparsi da un punto centrale chiamato sito di nucleazione e crescono radialmente in tutte le direzioni, formando un modello sferico. Le sferuliti hanno la capacità di riflettere la luce, motivo per cui i pellet di PET hanno un colore bianco.
Il processo bistadio si compone di due fasi separate:
1) inizialmente, si stampano a iniezione delle preforme, che assomigliano a piccole fiale o provette con i colli già formati, ma con diametro e lunghezza molto ridotti rispetto alla dimensione finale della bottiglia (figura 2);
2) successivamente le preforme subiscono un processo di riscaldamento e formatura mediante stiro-soffiaggio (RSBM, Reheat Stretch Blow Moulding) per ottenere la complessa geometria della bottiglia.
Durante il processo di stampaggio a iniezione delle preforme, i cristalli presenti nei pellet sono distrutti per formare una massa fusa amorfa. Questa massa è poi iniettata nelle cavità di uno stampo per preforme, condizionato a circa 15°C per impedire che ricristallizzi. Dopo pochi secondi, la preforma appena realizzata viene estratta dallo stampo e subisce un processo di raffreddamento accelerato in un sistema appositamente progettato, fino a quando la sua temperatura non scende al di sotto della temperatura di transizione vetrosa.
In questa fase amorfa, le catene molecolari del PET non sono orientate e non mostrano cristallinità, il che rende il materiale trasparente. Pertanto, il processo di raffreddamento dello stampo è cruciale e gioca un ruolo determinante nella qualità finale della preforma. Tuttavia, in questo stato, il PET possiede proprietà meccaniche e di barriera relativamente scarse, che saranno migliorate nel successivo processo di formatura della bottiglia mediante stiro-soffiaggio.
Il riscaldamento delle preforme al di sopra della temperatura di transizione vetrosa è la prima fase del processo RSBM (figura 3), essenziale per permettere la deformazione della preforma all’interno dello stampo (figura 4a). Durante la fase di stiro-soffiaggio, le catene molecolari amorfe presenti nella preforma riscaldata sono stirate e orientate, formando una nuova struttura cristallina. Questo avviene sotto l’azione combinata dell’asta di stiro e dell’aria soffiata (figura 4b), che costringono le catene del polimero ad allinearsi in direzione sia longitudinale che circonferenziale, generando piccoli cristalli causati dalla deformazione (in fondo i cristalli sono, per definizione, strutture molecolari ordinate).
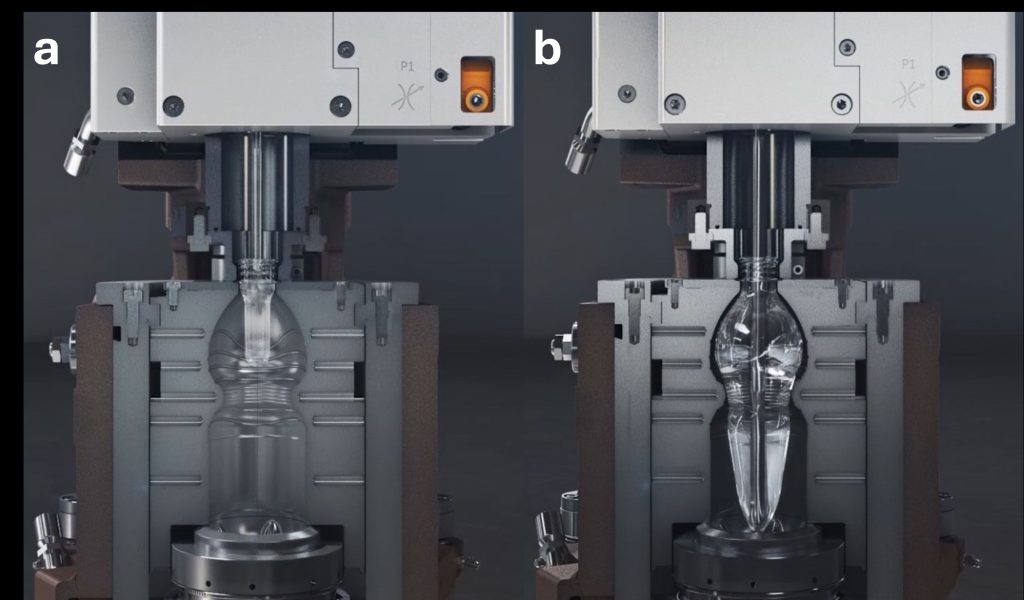
Le catene molecolari si dispongono parallelamente alla direzione della deformazione applicata, creando una struttura ordinata e lineare nell’area interessata dalla tensione. Questi cristalli, essendo non riflettenti, mantengono la bottiglia trasparente, ma migliorano significativamente le sue proprietà di resistenza e di barriera, grazie alla loro disposizione ordinata e compatta. Con un’adeguata progettazione della preforma e un accurato controllo delle condizioni di processo, si può raggiungere una cristallizzazione fino al 25% nella parete laterale della bottiglia.
La bottiglia finita avrà zone amorfe nel collo e nell’imboccatura, dove non è avvenuto lo stiramento, e zone orientate nelle pareti laterali; a volte, si possono formare zone cristallizzate termicamente intorno al punto d’iniezione della preforma (lo possiamo notare sul fondo della bottiglia), un comune difetto che non si può correggere durante il processo di soffiaggio.
Per le bottiglie destinate al riempimento a caldo, usate per alimenti che richiedono pastorizzazione come succhi di frutta, latte e passata di pomodoro, si cerca di ottenere livelli più elevati di cristallinità. Le temperature di riempimento variano da 82°C per i succhi fino a 95°C per i prodotti a base di pomodoro. Per resistere al carico termico, le bottiglie per il riempimento a caldo sono significativamente più spesse rispetto a quelle per l’acqua o le bevande gassate. Poiché è necessario un alto livello di cristallinità nelle pareti laterali, ma si deve mantenere la trasparenza, è fondamentale modificare i parametri di processo per formare solo cristalli abbastanza piccoli da non interferire con la luce. I cristalli indotti dalla deformazione misurano solo 0,5-0,7 μm di diametro e non alterano in alcun modo la trasmissione della luce.
Il polibutilentereftalato (PBT)
La produzione commerciale di PBT è iniziata nel 1970 negli Stati Uniti, da Celanese, principalmente per applicazioni che richiedevano performance più elevate (le cosiddette plastiche tecniche o ingegneristiche). È rapidamente diventato popolare in settori come l’automobilistico, l’elettrico e l’elettronico, grazie alla sua rapida cristallizzazione e facile lavorazione, distinguendosi dagli altri poliesteri.
Il PBT è noto per la sua elevata resistenza al calore, rigidità, durezza, eccellenti proprietà elettriche e buona resistenza ambientale. È utilizzato principalmente nello stampaggio a iniezione per formare componenti funzionali e parti strutturali. Le varietà di PBT disponibili includono gradi non caricati, modificati per l’impatto, rinforzati con vetro, caricati con minerali e ritardanti di fiamma, oltre a blend come PBT/PC, PBT/PET e PBT/ABS, permettendone la personalizzazione per applicazioni specifiche.
Circa il 75% del PBT prodotto è rinforzato con fibra di vetro o altri materiali per migliorarne le caratteristiche meccaniche, come il modulo, la resistenza e la temperatura di deflessione termica (HDT). I rinforzi comuni includono fibre di vetro corte trattate superficialmente, che migliorano la rigidità e la resistenza al calore. Le cariche usate includono invece vetro macinato e vari riempitivi minerali, mirati a migliorare la rigidità e la stabilità dimensionale, riducendo il ritiro e migliorandone l’isotropia.
La bassa viscosità e l’elevata velocità di cristallizzazione del PBT ne facilitano la lavorazione usando metodi convenzionali come la filatura, l’estrusione e, in particolare, lo stampaggio a iniezione. Il PBT è ampiamente utilizzato nel settore automobilistico, elettrico, elettronico, delle telecomunicazioni, dell’ingegneria di precisione e dell’ingegneria meccanica generale. Le sue caratteristiche di resistenza al calore e alle sostanze chimiche, insieme a proprietà elettriche stabili in un ampio intervallo di temperature, lo rendono adatto per un’ampia gamma di applicazioni, da piccole parti come i connettori a grandi componenti utilizzati in applicazioni automobilistiche (figura 5). Il PBT compete spesso con altri termoplastici come la poliammide e il policarbonato, specialmente quando è personalizzato con additivi come fibre di vetro, modificanti d’impatto e ritardanti di fiamma per soddisfare requisiti specifici.
(Articolo tratto dalla rivista Plastix n. 8, novembre 2024)