
Guarnizioni, ammortizzatori di vibrazioni, connettori e altri componenti in gomma sono fondamentali in molte applicazioni per la sicurezza e il funzionamento affidabile di sistemi, apparecchiature e autoveicoli. Fattori economici e ambientali costringono i produttori a integrare sempre più funzioni in questi componenti e al contempo a ridurre il consumo di risorse [1, 2]. In questo contesto, la raccolta e l’interpretazione dei dati di processo rappresenta un valido strumento per ottenere una qualità costante ed elevata [3-5].
Il sistema di assistenza iQ Clamp Control di Engel, insieme al “polmonamento dello stampo”, fornisce segnali utili che consentono l’ottimizzazione automatica della forza di chiusura. Inoltre, facilita il monitoraggio del processo di produzione e l’ottimizzazione manuale dei parametri importanti per la qualità, come il punto di commutazione e il tempo di mantenimento della pressione. Il software è stato sviluppato per i termoplastici, dove è utilizzato con successo da anni [6, 7], ma l’applicazione nel campo degli elastomeri presenta delle criticità legate soprattutto alla reticolazione.
Come rilevare le non conformità
Il tema è stato affrontato in un progetto di ricerca congiunto tra Engel, il Centro di Competenza Polimeri (PCCL) di Leoben e l’Università Montan (MUL) di Leoben, in Austria. L’obiettivo era quello di rilevare in tempo reale le parti in gomma non conformi già in fase di produzione, senza la necessità di implementare un ulteriore controllo di qualità manuale.
Per simulare le deviazioni di processo, la temperatura dello stampo è stata deliberatamente aumentata durante lo stampaggio senza però regolare il tempo di reticolazione. Tale variazione ha indotto modifiche inaccettabili nelle proprietà dinamico-meccaniche dei pezzi, classificandole come non conformi.
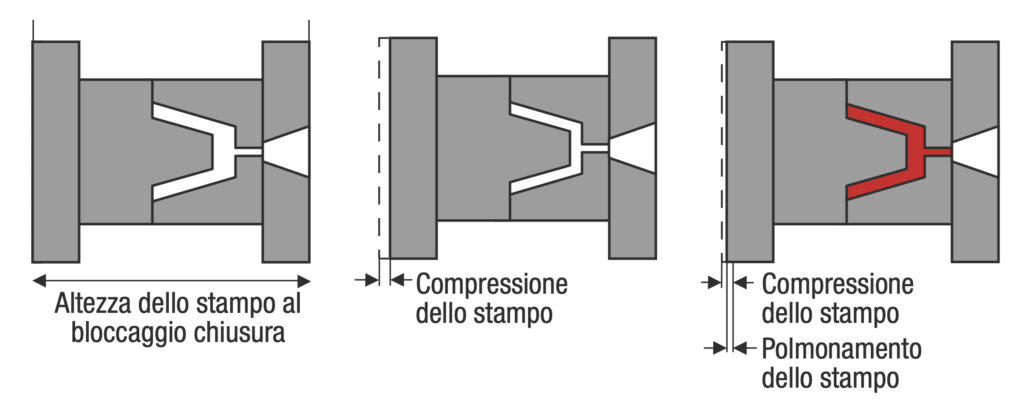
Il processo è stato monitorato mediante metodi basati sull’analisi PCA (Principal Component Analysis, cioè analisi delle componenti principali), ovvero metodi di machine learning in grado di utilizzare e definire le correlazioni tra diversi segnali emessi nel corso del processo, come ad esempio il polmonamento dello stampo (figura 1). Ciò consente di migliorare significativamente il rilevamento degli errori rispetto ai metodi tradizionali e di visualizzare le alterazioni del processo associate alla temperatura. Per consentire l’esecuzione dell’analisi PCA, e quindi la correlazione tra i dati di processo e di qualità della produzione, è necessario estrarre un set di dati di esercitazione (training dataset) dai dati di processo delle parti conformi. Questo set di dati di esercitazione, utilizzato come base per la successiva identificazione in linea degli errori, viene determinato sperimentalmente.
Esercitazione per l’identificazione degli errori in linea
I test sono stati eseguiti nel centro tecnico Engel, in Austria, su una pressa a iniezione e-victory 740/220 con forza di chiusura massima di 220 tonnellate. Per la regolazione della temperatura dello stampo sono stati utilizzati piani portastampo dotati di elementi riscaldanti elettrici integrati, i cui valori impostati potevano essere modificati attraverso il sistema di controllo della pressa. Le prove sperimentali sono state effettuate stampando provini in gomma nitrile-butadiene caricata con nerofumo, tipica delle applicazioni industriali, fornita da SKF Sealing Solutions (Austria).
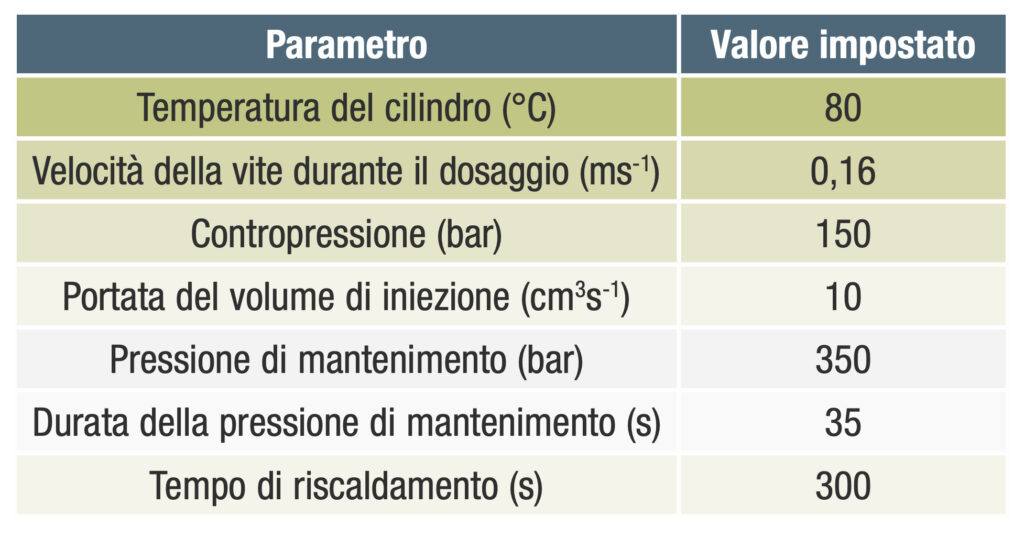
Nei test preliminari sono state identificate le impostazioni di tutti i parametri di lavorazione, garantendo così la stabilità del processo di produzione (tabella 1). Il tempo di riscaldamento è stato impostato in modo che, al punto di estrazione a una temperatura dello stampo di 160 °C, le parti abbiano raggiunto un grado di reticolazione del 90%. Le impostazioni sono state mantenute costanti su 20 cicli, al fine di generare dati di esercitazione validi dal ciclo 5 al ciclo 15 dopo una breve oscillazione transitoria. È stata quindi fissata una temperatura costante di 163 °C, misurata con il sensore di temperatura dello stampo (figura 2). Dal ciclo 21, il valore impostato per gli elementi riscaldanti è stato portato a 180 °C, causando anche l’aumento della temperatura massima misurata sullo stampo. Dal ciclo 52, la temperatura di controllo degli elementi riscaldanti è stata abbassata a 160 °C. In coincidenza con l’aumento della temperatura impostata sono state simulate deviazioni di temperatura impreviste, derivanti da possibili malfunzionamenti degli elementi riscaldanti o termici. Su questa base, sono stati studiati i valori di soglia per le variazioni di qualità non consentite, nonché la risposta dei metodi di monitoraggio del processo.
Definizione del comportamento dinamico del materiale
Le proprietà dinamico-meccaniche delle parti sono state studiate con un’apparecchiatura per test elettrodinamici Instron ElectroPuls E3000 di Illinois Tool Works. La procedura utilizzata è in grado di individuare il comportamento caratteristico del materiale nel range del carico oscillante di pressione.
La risposta del materiale al carico è definita come valore caratteristico della tangente dell’angolo di perdita tan(δ), che descrive il rapporto tra il comportamento plastico e il comportamento elastico del materiale, e che fornisce quindi informazioni utili sul grado di reticolazione.
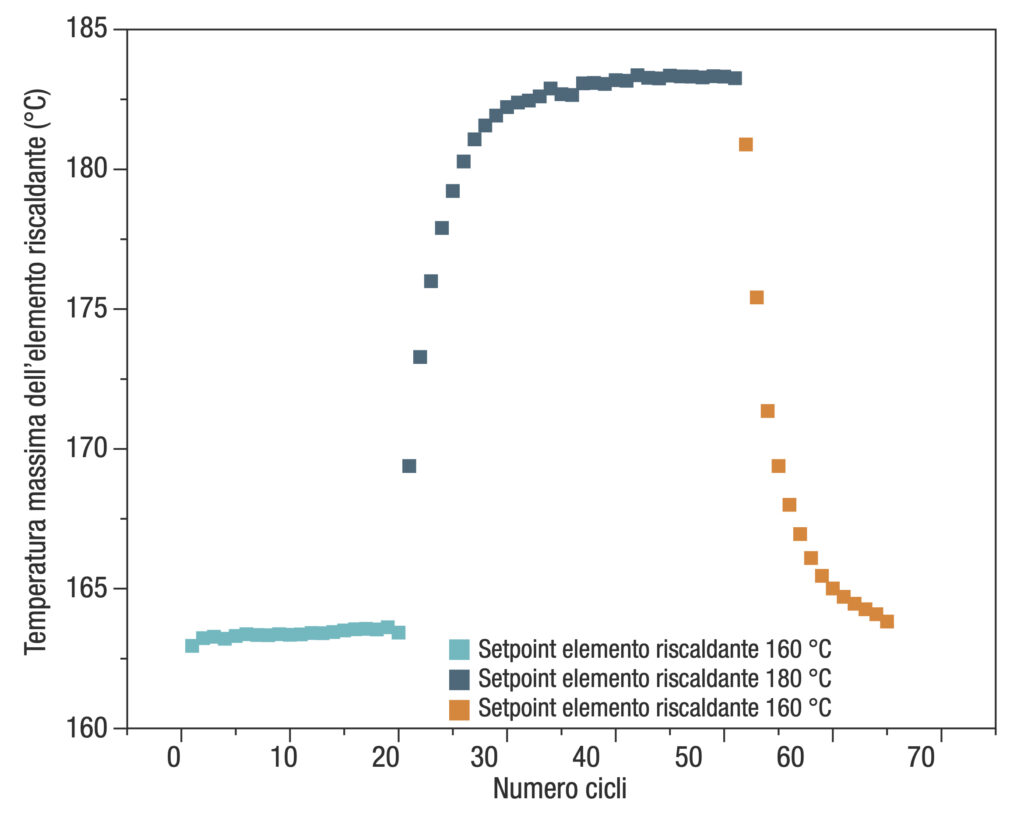
I valori di tan(δ) determinati nelle prove dinamiche, come previsto, sono correlati con la temperatura dello stampo misurata (figura 2). Un incremento di tan(δ) corrisponde a un aumento della componente plastica, ad esempio a causa di una minore reticolazione causata da un cambiamento delle condizioni di reticolazione. In fase di addestramento (cicli da 5 a 15), tan(δ) evidenzia un valore medio di 0,209 con una deviazione standard (δ) di 0,002. Su questa base, viene definita una tolleranza di ±3 δ. Se su un pezzo si misura un valore fuori tolleranza, viene considerato non conforme. Nella sequenza temporale dei cicli di prova, questa tolleranza viene rilevata a partire dal ciclo 23 e mantenuta stabilmente solo a partire dal ciclo 58. L’oggetto dei sistemi di monitoraggio statistico (in questo caso l’analisi PCA) avviene in tempo reale, mentre il processo è in esecuzione, per utilizzare i parametri utili a identificare se la qualità del pezzo è nei limiti di tolleranza consentiti. Per valutare i diversi metodi di monitoraggio studiati, i singoli cicli sono stati contrassegnati come parti conformi o non conformi in funzione dei limiti di controllo.
Polmonamento dello stampo e pressione nell’impronta
A conferma che il polmonamento dello stampo rappresenta un parametro adatto per il riconoscimento degli errori, nelle prove pratiche è stata studiata la correlazione tra il segnale di polmonamento e la pressione nell’impronta (figura 3). È evidente che il segnale di polmonamento dello stampo mostra deviazioni significative solo quando lo stampo è quasi pieno, mentre la pressione nell’impronta inizia ad aumentare non appena il fronte del flusso raggiunge il sensore (figura 3a). Questo comportamento può essere previsto poiché, oltre alla pressione, il pomonamento dello stampo tiene conto anche della superficie proiettata già riempita. Nel punto di commutazione, invece, i picchi di entrambi i segnali sono ugualmente intensi e possono quindi venire valutati con precisione. Se i picchi dei due segnali vengono tracciati l’uno sopra l’altro in tutti i cicli (figura 3b), è chiaramente possibile riconoscere una relazione lineare.
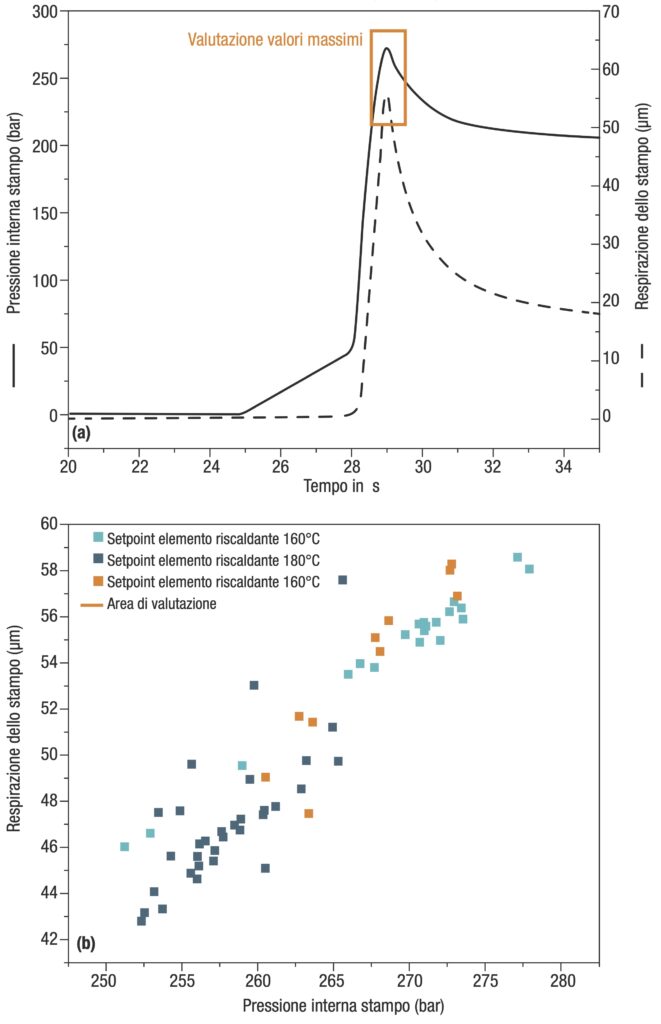
Monitoraggio dei processi mediante analisi PCA
I processi con più variabili possono essere opportunamente monitorati utilizzando metodi statistici multivariati [8, 9]. Per i test, è stato scelto un approccio basato su analisi PCA (vedi riquadro) con l’obiettivo di individuare in modo affidabile le fluttuazioni del processo e quindi della qualità. Le variabili di processo registrate, a eccezione della temperatura dello stampo, sono quindi state elaborate mediante l’analisi delle componenti principali (PCA). Inoltre, sono state calcolate le statistiche SPE (Squared Predictive Error, errore predittivo al quadrato) per ciascun ciclo di prova (figura 4b). I cicli da 5 a 15 sono stati utilizzati per produrre il set di dati di esercitazione, sulla base dei quali è stato calcolato un limite di intervento comune e univoco utilizzando il metodo PCA. Se le statistiche SPE di un ciclo si trovano all’esterno del limite di intervento, la parte viene identificata come probabilmente non conforme. Come risultato si è visto che la valutazione comune delle variabili di processo rende visibile la variazione della temperatura dello stampo in modo statisticamente significativo, senza che vi sia la necessità di misurarla direttamente. La variazione della temperatura dello stampo viene identificata rapidamente; solo a partire dal ciclo 55 il sistema ritorna al funzionamento normale.
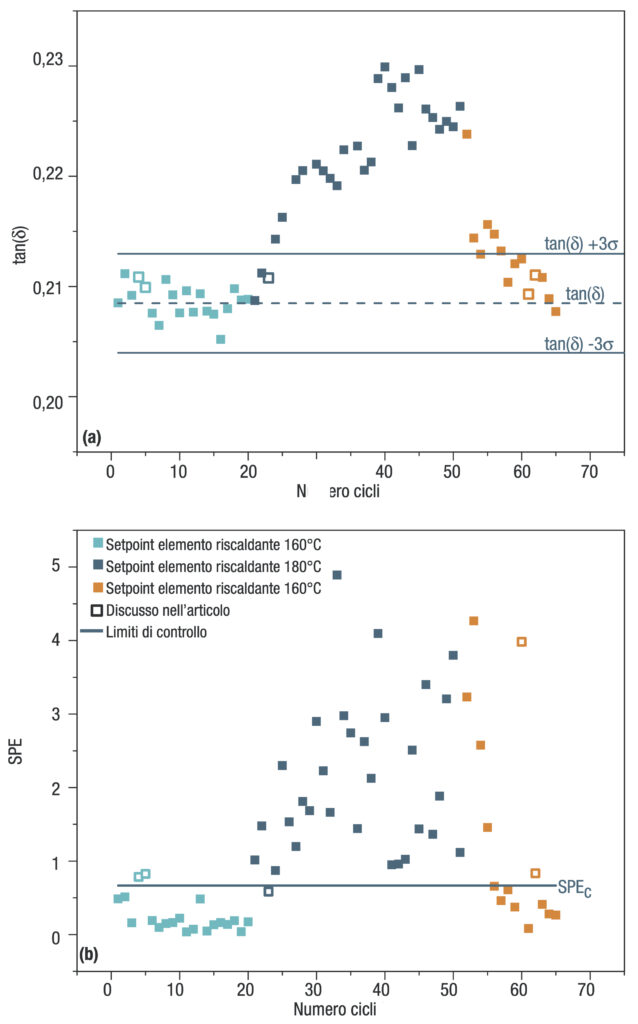
Un processo difficilmente prevedibile
In generale, gli esempi indicano che, nonostante la forte correlazione, nessuno dei segnali di processo valutati è in assoluto in grado di rappresentare il processo di reticolazione. Tutte le variabili registrate negli esperimenti descrivono i cambiamenti delle proprietà fisiche della gomma, in particolare il comportamento del flusso. Tuttavia, se le proprietà della reticolazione chimica non sono in relazione lineare con le proprietà fisiche, le proprietà della parte che sono determinate principalmente dal grado di reticolazione non possono essere previste in modo univoco. Se tutti i segnali di processo e il monitoraggio multivariato indicano che le proprietà di flusso sono cambiate, anche se la tan(δ) prevista, determinata principalmente dalla reazione di polimerizzazione, rientra nei limiti di intervento, sarà necessario eseguire un controllo approfondito delle parti. Solo allora si potrà valutare se le fluttuazioni impreviste del processo non comportano criticità o scarti.
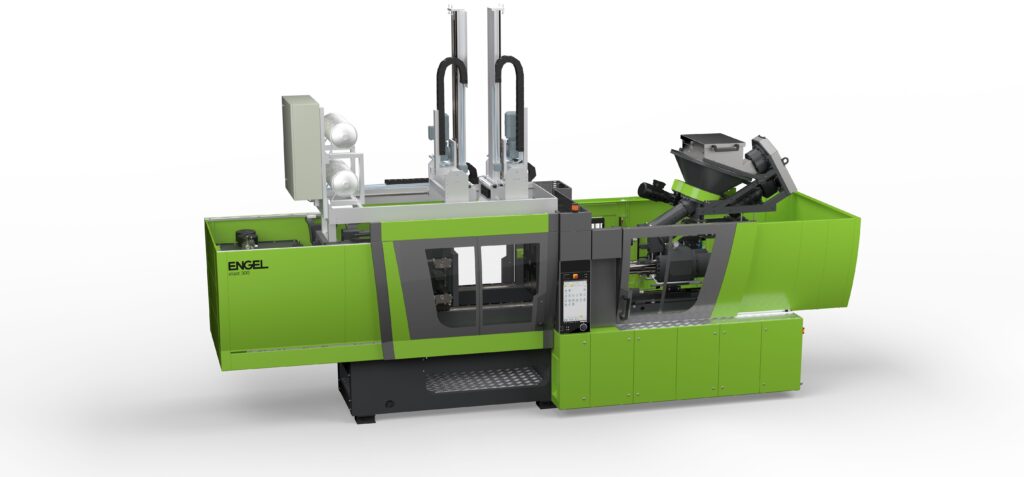
Nuove opportunità nella lavorazione della gomma
Sulla base del sistema di assistenza intelligente IQ Clamp Control, grazie all’analisi delle componenti principali (PCA) è stato possibile impostare un sistema di monitoraggio multivariato del processo di stampaggio a iniezione della gomma che identifica immediatamente i cambiamenti nelle condizioni di processo e classifica le parti stampate come non conformi. I vantaggi di questo sistema consistono nel basso sforzo necessario per l’estrazione dei dati di addestramento e nella possibilità di elaborare contemporaneamente più variabili di processo. La sfida dello stampaggio a iniezione degli elastomeri consiste nel fatto che la maggior parte dei segnali di processo disponibili è fortemente correlata alle proprietà di fluidità dei materiali, ma solo debolmente alla reattività chimica, il che stabilisce ulteriori limiti all’individuazione dei guasti basata sui segnali di processo. Il sistema sviluppato evidenzia le tendenze delle fluttuazioni di processo ancor prima che inizino a influire sulla qualità delle parti. Ciò schiude un grande potenziale per l’ottimizzazione dei processi di serie nell’industria della lavorazione degli elastomeri, per la quale Engel propone le macchine delle linee elast (figura 5) e flexseal.
Bibliografia
1 J.A. Lindsay, Practical guide to rubber injection moulding. Smithers Rapra, Shawbury, Shrewsbury, Shropshire 2012
2 M. Fasching et al., Advanced Mold Concepts to Improve Part Quality and Productivity in Rubber Injection Molding. In: Proceedings of the Re-gional Conference of the Polymer Processing Society, Graz 2015, pp. 49
3 Z. Chen, Data-Driven Fault Detection for Industrial Processes: Canonical Correlation Analysis and Projection Based Methods. Springer Fachmedien, Wiesbaden 2017
4 Y. Yang et al., Injection molding process control, monitoring, and optimiza-tion. Hanser, München 2016
5 M. Zeppenfeld et al., Wireless Life Cycle Monitoring in the Injection Molded Part. Kunststoffe international 109 (2019) 3, pp. 11-16
6 G. Pillwein et al., Breathing Exercises for Process Optimization. Kunststoffe international 105 (2015) 10, pp. 81-84
7 G. Pillwein et al., Using Breathing Signals for Process Optimization. Kunststoffe international 110 (2020) 1, pp. 26-31
8 T. Hutterer et al., Fault detection in rubber injection molding with multivariate statistics. Rubber World (2019), pp. 40-44
9 T. Hutterer et al., Rubber injec-tion molding: Applying multivariate statistics to identify quality issues solely from process sig-nals. Polymer Engineering & Science (2020), https://onlineli-brary.wiley.com/doi/full/10.1002/pen.25604
10 Y. Yang e F. Gao, Injection molding product weight: Online prediction and control based on a nonlinear principal component regression model. Polymer Engineering & Science 46 (2006) 4, pp. 540-548
11 S. Wold et al., Multi-Way Principal Components and PLS-Analysis. Journal of Chemometrics (1987) 1, pp. 41-56
12 E.L. Russell et al., Data-driven Methods for Fault Detection and Diagnosis in Chemical Processes. Springer, London 2000. URL: http://dx.doi.org/10.1007/978-1-4471-0409-4
13 Y. Yang, Y e F. Gao, Injection molding product weight: Online prediction and control based on a nonlinear principal component regression model. Polymer Engineering & Science 46 (2006) 4, pp. 540-548