La transizione verso una mobilità “zero emission” è ormai avviata e, a meno di eventuali proroghe, ha un traguardo fissato al 2035. Tra le soluzioni tecnologiche disponibili, l’Unione Europea sembra aver puntato sull’elettrificazione: una scelta che impone all’industria automobilistica del Vecchio continente nuovi modelli di business da implementare con urgenza per non perdere ulteriori quote di mercato.
Il passaggio dal motore a combustione a quello elettrico, con il radicale cambiamento del mix della componentistica dei veicoli, creerà nuove opportunità per i produttori di batterie, motori elettrici, cablaggi e sistemi elettronici avanzati. I fornitori di componenti tradizionali dovranno quindi evolversi per restare competitivi, integrando le loro competenze con nuove tecnologie e, soprattutto, trovando soluzioni per rendere i processi produttivi più efficienti e cost-effective.
Batteria, un componente critico
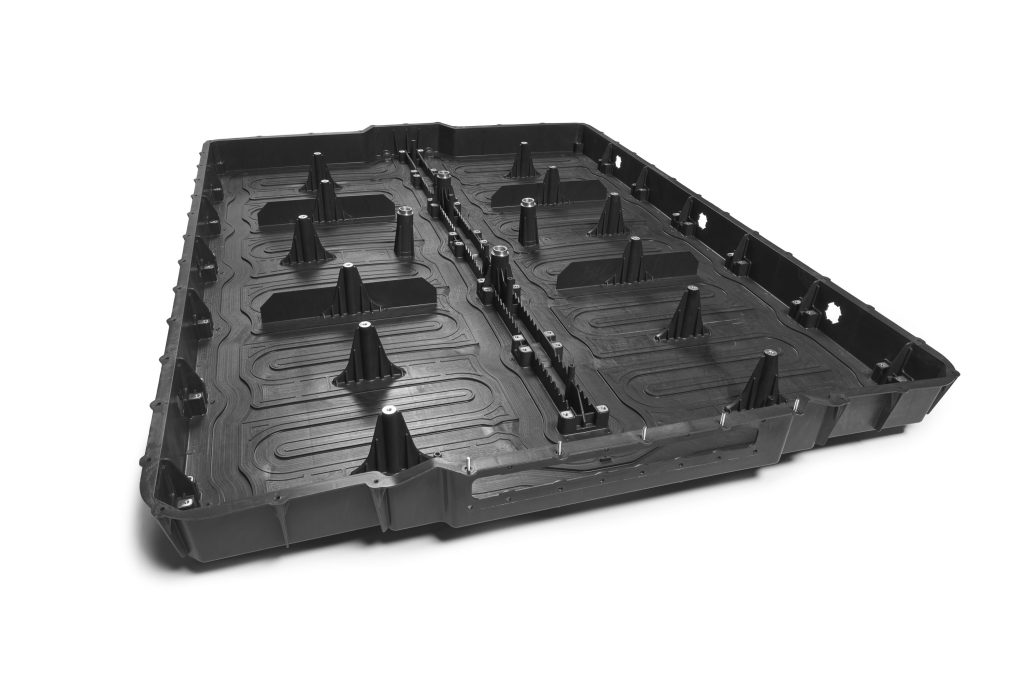
Uno dei componenti critici dei veicoli elettrici (EV) è la batteria, perché, oltre a soddisfare elevati requisiti tecnici e prestazionali (densità di carica, autonomia, durata e velocità di ricarica), deve garantire la sicurezza dei passeggeri prevenendo il rischio d’incendio. Anche se numerosi studi hanno dimostrato che il rischio di prendere fuoco di un veicolo full-electric non è superiore a quello di uno tradizionale, resta il fatto che i tempi di spegnimento sono molto più lunghi a causa del thermal runaway. Per prevenire questo fenomeno vengono adottate misure di sicurezza, come sistemi di gestione della batteria (BMS), dispositivi di spegnimento automatici, sistemi di raffreddamento adeguati e involucri ignifughi realizzati con materiali progettati per resistere alle temperature elevate.
Nello sviluppo di contenitori per il pacco batterie le resine termoplastiche giocano un ruolo particolarmente rilevante, forti del contributo in termini di alleggerimento e della possibilità di essere trasformate in modo efficiente su vasta scala tramite stampaggio a iniezione. Su questo aspetto si focalizzerà la presentazione “The next generation of battery box: potential for plastics” di Matteo Terragni, amministratore delegato di Engel Italia, al prossimo Congresso nazionale delle materie plastiche. L’evento, organizzato dall’Associazione italiana dei Tecnici delle Materie Plastiche (TMP) e dalla rivista Plastix, si terrà il 21 novembre 2024 presso l’NH Hotel di Milanofiori (Assago, Milano).
I vantaggi dell’inietto-compressione
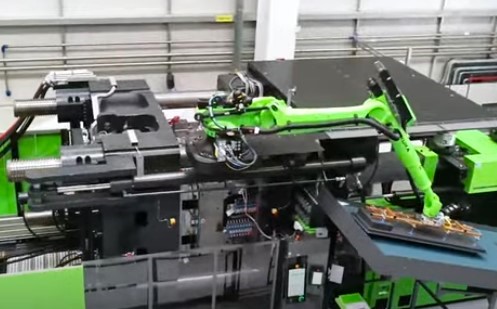
Peso e dimensioni sono due aspetti critici da affrontare quando si stampano gli involucri delle batterie per EV. Ad esempio, in funzione del modello del veicolo, la superficie del coperchio della batteria può variare da 1,5 a 3 metri quadrati, con spessori relativamente ridotti (da 3,5 a 7 mm). La produzione di pezzi di queste proporzioni richiede la capacità di gestire le tolleranze dimensionali e, al contempo, di ridurre le deformazioni e di ottimizzare lo “stress” all’interno del componente.
In queste applicazioni l’inietto-compressione si è rivelata promettente. La tecnologia prevede l’iniezione della massa fusa a stampo parzialmente aperto e la successiva formatura del pezzo attraverso una compressione omogenea, che si ottiene mediante la chiusura dello stampo utilizzando solo i quattro cilindri di pressione della pressa a iniezione. Inserendo i sensori di pressione nella cavità dello stampo in prossimità dell’iniezione e nelle zone più lontane, si osserva che nell’inietto-compressione la pressione ha un andamento costante. Inoltre, la temperatura del pezzo stampato è pressoché identica in ogni punto. Ne derivano tensioni interne ridotte e ritiro omogeneo e, di conseguenza, deformazioni minime, a fronte di migliori proprietà meccaniche e resistenza all’urto. Un altro vantaggio importante dell’inietto-compressione è la possibilità di utilizzare presse con forza di chiusura inferiore rispetto allo stampaggio tradizionale, perché iniettando a stampo aperto sono necessarie pressioni minori.
Le tecnologie Engel per lo stampaggio dei battery box
Oltre a un’elevata produttività su vasta scala, i vantaggi dello stampaggio a iniezione sono legati alla possibilità di realizzare forme complesse con una precisione molto elevata, riducendo la necessità di assemblaggio di più componenti. In particolare, la tecnologia Engel combimelt consente di combinare materiali plastici diversi in un unico processo produttivo, inserendo ad esempio sezioni flessibili o rinforzate in punti critici dell’involucro, migliorando le proprietà funzionali del prodotto finale senza necessità di ulteriori lavorazioni. L’inserimento di inserti metallici, inoltre, permette di integrare direttamente nell’involucro funzionalità aggiuntive, come lamelle o supporti per cavi, ottimizzando lo spazio e migliorando la gestione complessiva della batteria.
Nella produzione di componenti che richiedono leggerezza e resistenza meccanica superiore, ad esempio il vassoio porta-batteria, la tecnologia Engel organomelt rappresenta un’alternativa efficiente rispetto ai metalli. Il processo permette infatti di realizzare in un’unica stampata componenti in compositi termoplastici rinforzati con nastri in fibre di vetro o di carbonio preimpregnati.
I vantaggi sono evidenti. In primo luogo, l’impiego sistematico di questi materiali consente d’integrare in maniera efficiente la formatura e la funzionalizzazione dei semilavorati fibrorinforzati, abbattendo i costi unitari. In secondo luogo, l’uso esclusivo di polimeri termoplastici facilita il processo di riciclo. Aspetto, quest’ultimo, particolarmente interessante per l’industria automobilistica, che, tra i principali obiettivi da raggiungere nello sviluppo di nuovi modelli, si è posta la reintroduzione dei componenti in composito nel ciclo dei materiali al termine della loro vita utile.
L’impiego di materiali riciclati, inclusi i termoplastici, rafforza ulteriormente il profilo green dei veicoli elettrici e, in questo campo, Engel si distingue per una vasta gamma di tecnologie per lo stampaggio di riciclati. Il two-stage process, per esempio, permette di utilizzare direttamente il 100% di scaglie post consumo senza la necessità di una fase di compounding. Dal lancio al K 2022 a oggi, il processo ha migliorato le proprie performance, espandendo l’ambito di applicazione a componenti come gli alloggiamenti per le batterie degli EV.
Infine, grazie agli assistenti intelligenti del Programma Inject 4.0, le tecnologie di processo Engel possono essere gestite con la massima efficienza, ottimizzando produttività e qualità dei pezzi prodotti.