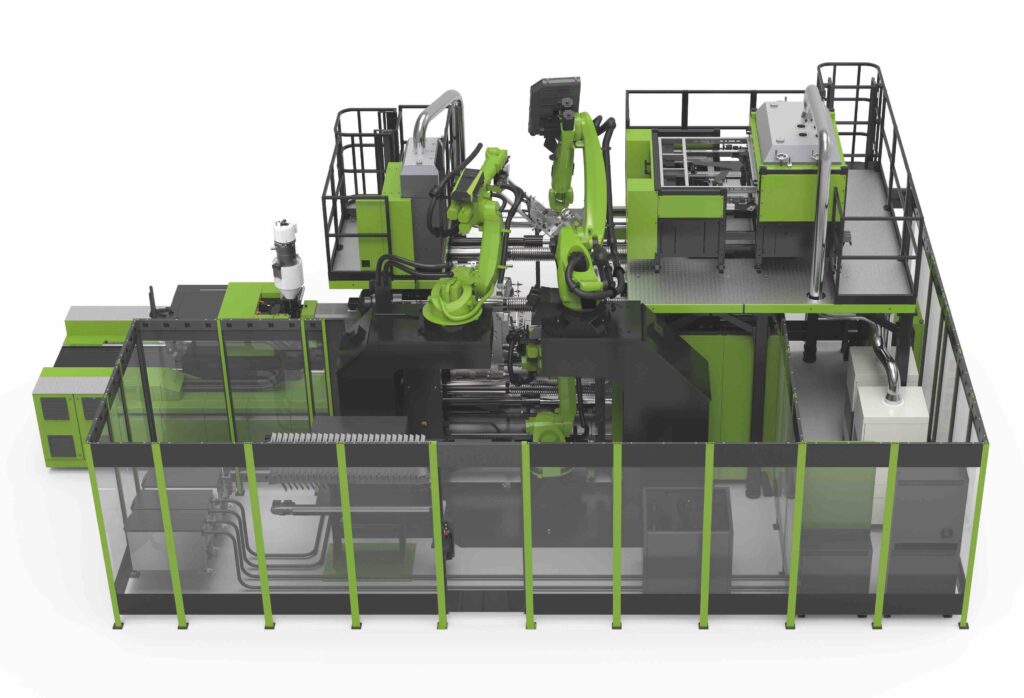
L’alleggerimento delle auto, una strada obbligata per la riduzione delle emissioni climalteranti e per l’e-mobility, sta trainando la richiesta di parti in compositi termoplastici. Le ragioni sono principalmente due. In primo luogo, l’impiego sistematico di questi materiali consente di integrare in maniera efficiente la formatura e la funzionalizzazione dei semilavorati fibrorinforzati, abbattendo i costi unitari. In secondo luogo, l’uso esclusivo di polimeri termoplastici facilita il processo di riciclo. Aspetto, quest’ultimo, particolarmente interessante per l’industria automobilistica, che tra i principali obiettivi da raggiungere nello sviluppo di nuovi modelli si è posta la reintroduzione dei componenti in composito nel ciclo dei materiali al termine della loro vita utile.
Processi ottimizzati e tempi ciclo ridotti
Nell’ormai consolidato processo di produzione in un unico ciclo dei manufatti in composito termoplastico, i semilavorati, sotto forma di lastre, vengono inizialmente collocati in appositi magazzini. Da qui, vengono prelevati da un robot e trasportati verso un forno a raggi infrarossi (IR). Una volta riscaldato, il semilavorato in composito, ora malleabile, viene di nuovo prelevato dal robot e depositato nello stampo della pressa a iniezione, dove viene formato nella forma desiderata durante la chiusura dello stampo; subito dopo vengono sovrastampati i particolari geometrici desiderati. Una volta terminato il raffreddamento, necessario soprattutto per le aree stampate a iniezione, il manufatto viene prelevato dallo stampo, finito. Uno dei principali vantaggi offerti dai compositi termoplastici consiste nel fatto che il tempo ciclo necessario a produrre un componente tecnico corrisponde a soli 40-80 secondi, laddove una soluzione in composito termoindurente richiederebbe invece almeno qualche minuto.
La configurazione del sistema di riscaldamento
Durante la sequenza che ha inizio con l’introduzione dei semilavorati nello stampo e termina con il sovrastampaggio, il tempo rappresenta un fattore cruciale. Non appena il semilavorato in composito riscaldato viene estratto dal forno IR, infatti, inizia a raffreddarsi. Tuttavia, in fase di sovrastampaggio dei particolari geometrici, occorre che il materiale conservi una quantità di calore sufficiente a garantire una buona adesione tra il composito e la resina termoplastica che viene iniettata su di esso. La movimentazione a caldo del semilavorato deve pertanto essere ben studiata, testata e implementata con precisione con l’ausilio di soluzioni di automazione adeguate.
Un ruolo altrettanto fondamentale è svolto dalla configurazione e dalla posizione del forno IR. Engel Austria progetta e costruisce forni a infrarossi in configurazione orizzontale e verticale, con la possibilità di scegliere, per ciascuna versione, se installare i pannelli radianti soltanto su un lato o su entrambi i lati. In presenza di lastre organiche termoplastiche sottili, un forno IR verticale posizionato sul piano portastampo fisso della pressa a iniezione rappresenta spesso la soluzione più vantaggiosa. Più è sottile la lastra, più rapidamente si raffredda. La vicinanza tra il forno a infrarossi e lo stampo abbatte le distanze da percorrere e, di conseguenza, riduce i tempi di movimentazione. Spesso, per riscaldare parti sottili con pareti fino a 1 millimetro è sufficiente un forno a infrarossi con pannelli radianti su un solo lato, una disposizione che contribuisce ad agevolare l’accesso e l’estrazione rapida del semilavorato.
Forno IR: la soluzione migliore per le lastre organiche
Il motivo per cui le radiazioni infrarosse, caratterizzate da un’elevata densità energetica, rappresentano una soluzione eccellente per riscaldare i semilavorati in composito termoplastico risiede nella struttura dei semilavorati stessi. Questi sono generalmente costituiti da lastre formate da una serie di strati privi di cavità intermedie, grazie anche all’impilaggio e alla pressatura. Ciò garantisce una rapida propagazione del calore dalla superficie al nucleo della lastra. Dal momento che la radiazione infrarossa agisce velocemente e, al contempo, non richiede alcun contatto fisico, è possibile riscaldare semilavorati di vario spessore, superando ampiamente il punto di fusione della matrice in polimero, senza provocare problemi di adesione.
La profondità fino alla quale vengono eccitati gli elettroni dipende dalla lunghezza d’onda della radiazione infrarossa e dal comportamento di assorbimento del materiale. I normali materiali a matrice termoplastica presentano fasce di assorbimento che si aggirano attorno a una lunghezza d’onda di 2-3 micron [1]. I radiatori IR a onde medie raggiungono un’intensità di radiazione elevata in questo range, e rappresentano la scelta privilegiata per il riscaldamento dei compositi termoplastici dal momento che consentono di raggiungere profondità di penetrazione fino a 0,5 millimetri. Lo strato appena al di sotto della superficie si riscalda quindi molto velocemente. Tuttavia, soprattutto nelle lastre organiche termoplastiche più spesse può accadere che, sebbene la superficie abbia raggiunto la temperatura desiderata, il nucleo non risulti ancora sufficientemente caldo. Il calore necessario a fondere l’area attorno al nucleo può essere trasmesso al materiale esclusivamente mediante conduzione termica. La plastica e le fibre di vetro si caratterizzano per le scarse proprietà conduttive: per questo motivo occorre del tempo per riscaldare completamente tutto lo spessore della lastra fino al centro. Al fine di garantire che quest’ultima raggiunga la temperatura necessaria, quindi, la superficie viene mantenuta a una temperatura predefinita per un determinato lasso di tempo calcolato in modo empirico.
La radiazione infrarossa si è dimostrata la tecnologia più efficiente per riscaldare le lastre organiche. In termini di conduzione termica, infatti, lo strato più vicino alla superficie rappresenta una sorta di fonte di calore interna, che non deve più superare la resistenza del materiale al trasferimento di calore, come nel caso del riscaldamento per contatto o per convezione. Messa a confronto con il riscaldamento a convezione, in particolare, la tecnologia a infrarossi offre tempi di riscaldamento sensibilmente ridotti. In linea di massima, i forni IR si prestano alla lavorazione di tutti i polimeri matrice, comprese le materie plastiche ad alta resistenza al calore come PAI, PPS, PEKK e PEEK.
Massima omogeneità termica e protezione del materiale
Quando si opta per il riscaldamento a infrarossi, la sfida consiste nell’ottenere una combinazione ottimale tra efficienza elevata e una buona omogeneità termica, senza danneggiare il materiale esponendolo a surriscaldamenti localizzati. La temperatura desiderata o impostata, che generalmente supera abbondantemente quella di fusione, ammette in ogni caso solo superamenti minimi. Al fine di garantire ciò, la temperatura superficiale viene monitorata mediante pirometri durante l’intera fase di riscaldamento. I valori misurati vengono poi acquisiti dal sistema di controllo del processo.
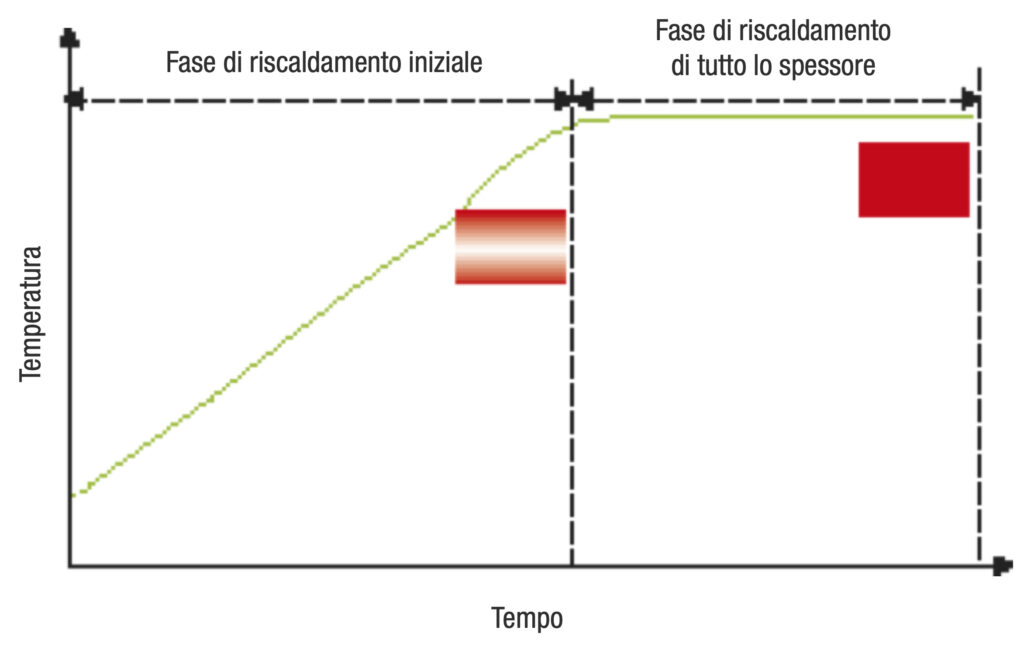
La figura 1 mostra l’andamento della temperatura di un singolo punto di misura durante la fase di riscaldamento iniziale e a riscaldamento completato di un materiale termoplastico semicristallino (ad esempio, polipropilene o poliammide). Caratteristico è l’andamento pressoché lineare della temperatura fino al raggiungimento del punto di fusione dei cristalliti. La velocità di riscaldamento è determinata dalla densità di potenza della radiazione, dal coefficiente di assorbimento, dalla capacità e conducibilità termica del composito termoplastico. In prossimità del punto di fusione dei cristalliti, che per la poliammide 6 corrisponde a circa 223 °C, la velocità di riscaldamento diminuisce, poiché parte dell’energia rilasciata viene utilizzata per fondere le sferuliti. Una volta che il materiale della matrice è stato fuso, la velocità di riscaldamento riprende a crescere, acquisendo addirittura maggiore dinamicità rispetto a quanto osservato al di sotto del punto di fusione dei cristalliti. Il polimero fuso presenta una densità e una capacità termica inferiori e, di conseguenza, risponde con un riscaldamento più rapido. In prossimità della temperatura impostata interviene il sistema di regolazione, che limita il successivo incremento della temperatura al fine di evitare picchi eccessivi. L’andamento lievemente irregolare della curva attorno al punto di fusione dei cristalliti è da ricondursi ai processi coinvolti nella fusione della matrice termoplastica. La distribuzione del processo sull’intera sezione trasversale della lastra e la dipendenza del coefficiente di assorbimento dalla temperatura fanno sì che gli effetti risultino spalmati su una fascia più ampia di tempi e temperature.
Al fine di ottenere una fase di riscaldamento totalmente lineare è possibile limitare la velocità di riscaldamento a un valore predefinito, e quindi regolarla mediante un parametro prescelto. Tuttavia, è nell’interesse dell’efficienza del processo e della protezione del materiale sfruttare al massimo, in fase di riscaldamento, la potenza termica del radiatore a infrarossi, purché non si verifichino deviazioni di temperatura significative o surriscaldamenti locali sulla superficie del materiale composito.
Controllo su un ampio numero di stati operativi
I forni IR possono essere impostati per assicurare un’omogeneità termica ottimale per un determinato punto di funzionamento, ad esempio nel caso in cui venga trattato il 70% della superficie utile complessiva in una forma rettangolare. Dal momento che, tuttavia, il punto di funzionamento effettivo tende a deviare anche sensibilmente dal valore nominale, questa strategia ha poco senso. Maggiormente utile allo scopo è invece optare per un sistema dotato già di base di buone caratteristiche in termini di omogeneità termica. A questo fine, il software dei forni IR costruiti da Engel è in grado di controllare ottimamente un ampio numero di stati operativi e di variabili al fine di assicurare un’eccellente omogeneità termica in una vasta gamma di applicazioni. I forni IR sono perlopiù concepiti per operare a pieno regime, sfruttando l’intera superficie radiante bordi esclusi. Il forno a infrarossi illustrato nella figura 2, ad esempio, presenta una superficie radiante pari a 1.250 x 750 millimetri e una superficie utile nominale di 1.100 x 600 millimetri.
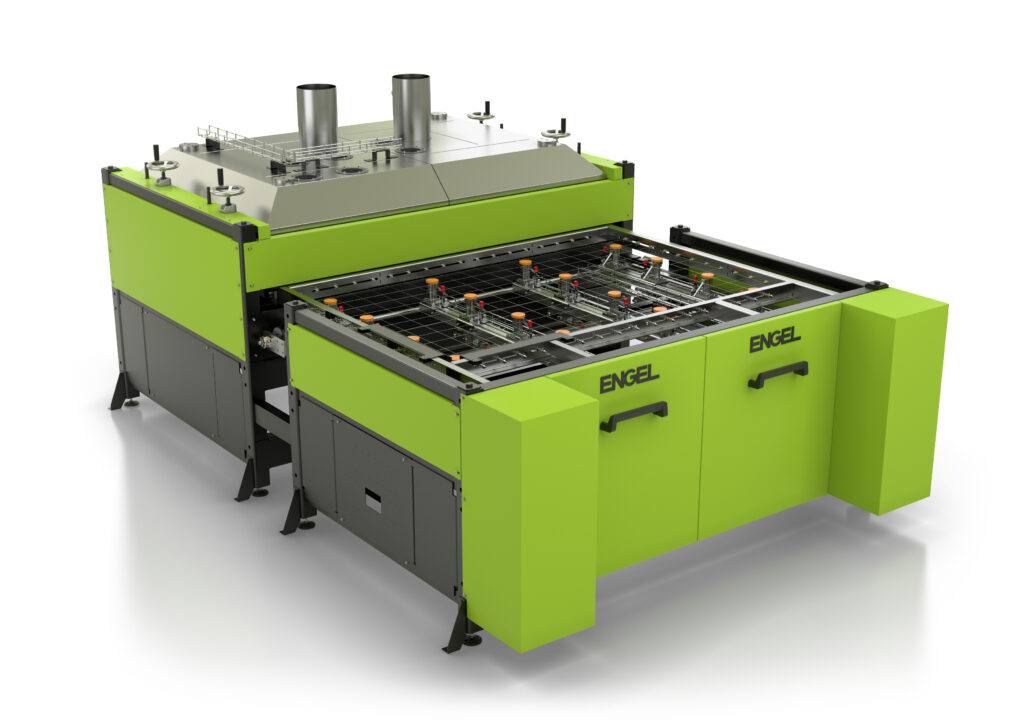
I radiatori non necessari possono essere spenti individualmente. Inoltre, solitamente, i radiatori vengono riuniti in gruppi in modo da poter controllare l’intero gruppo in base a uno specifico valore di misura della temperatura. Una disomogeneità termica può nascere da cause complesse. Tra gli altri, svolgono un ruolo fondamentale l’influenza reciproca esercitata dalle diverse zone di regolazione, il carico della superficie utile, le condizioni ambientali e il comportamento transitorio del forno IR. Una regolazione precisa della fase di riscaldamento a infrarossi rappresenta una parte cruciale del controllo di processo nella produzione di manufatti in composito termoplastico. È per questo motivo che, nelle soluzioni di sistema Engel, la regolazione del forno IR è integrata nell’unità di controllo della pressa a iniezione. Ciò consente di documentare i parametri di processo e i valori di misura relativi al forno a infrarossi insieme ai dati di produzione che riguardano il processo di stampaggio a iniezione.
Ottimizzazione automatica della curva di riscaldamento
Data la varietà di possibili cause che possono provocare una disomogeneità termica, nelle applicazioni pratiche ogni zona di regolazione presenta caratteristiche di riscaldamento differenti. Durante un esperimento, sono state create condizioni di disomogeneità termica mirate (figura 3). È emerso che una situazione simile genera differenze significative in termini di velocità di riscaldamento. La temperatura impostata viene raggiunta in momenti diversi e la stabilizzazione della temperatura superficiale al valore desiderato richiede tempi più lunghi. Questa situazione ha rappresentato il punto di partenza per l’elaborazione di un sistema di ottimizzazione automatica della curva di riscaldamento. La curva ottimizzata è riportata nella figura 4. Il sistema di regolazione si basa su un confronto tra le temperature effettive nelle singole zone di regolazione. Le curve di riscaldamento mostrano ora un andamento uniforme, pressoché lineare. La stabilizzazione nella fascia della temperatura impostata è sensibilmente migliorata rispetto alla situazione di partenza. In presenza di una zona di regolazione che, a piena potenza radiante, raggiunge la temperatura prevista prima del tempo, occorre ridurre tale potenza già durante la fase di riscaldamento.
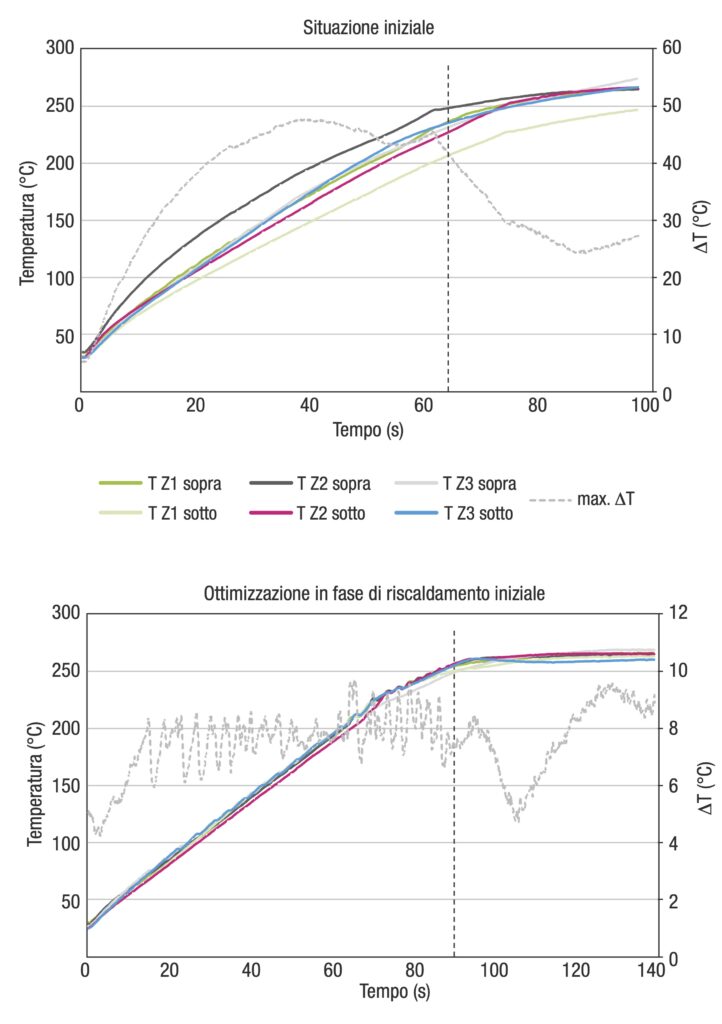
4 (in basso) L’ottimizzazione automatica della curva di riscaldamento iniziale genera un incremento di temperatura più uniforme, pressoché lineare
L’ottimizzazione e il coordinamento automatico delle zone di regolazione si traducono in un adeguamento continuo della potenza radiante in tutte le zone interessate, in modo tale da mantenere eventuali deviazioni entro un margine di tolleranza ristretto e regolabile. Ciò consente di ottenere una velocità di riscaldamento uniforme in tutte le zone di regolazione affinché raggiungano la temperatura impostata nello stesso momento. Particolarmente interessante è il fatto che il sistema di controllo del processo non richiede l’impostazione di una zona di regolazione di riferimento. Il sistema tiene costantemente conto dei valori misurati da tutti i pirometri e implementa in tutte le zone di regolazione un processo di riscaldamento altamente dinamico, che si adatta al comportamento specifico della matrice durante la fusione, attraverso le fasi di riscaldamento iniziale, fusione e ulteriore riscaldamento del materiale.
Come evitare i picchi termici
Quando la temperatura superficiale si avvicina al valore impostato, occorre un ulteriore aggiustamento dei parametri di controllo del processo, al fine di impedire eventuali picchi termici in superficie. Un’uniformità ottimale della temperatura durante la fase di riscaldamento in profondità fa sì che l’area del nucleo raggiunga la temperatura desiderata in un determinato momento calcolabile. In seguito, il riscaldamento del composito termoplastico può essere terminato dopo un intervallo di tempo ben definito, che sia il più breve possibile, a protezione del materiale. Soprattutto in fase di riscaldamento in profondità, è fondamentale limitare al massimo le deviazioni di temperatura allo scopo di evitare surriscaldamenti localizzati e il deterioramento del materiale. A tal fine, occorre impostare in modo ottimale i parametri di regolazione.
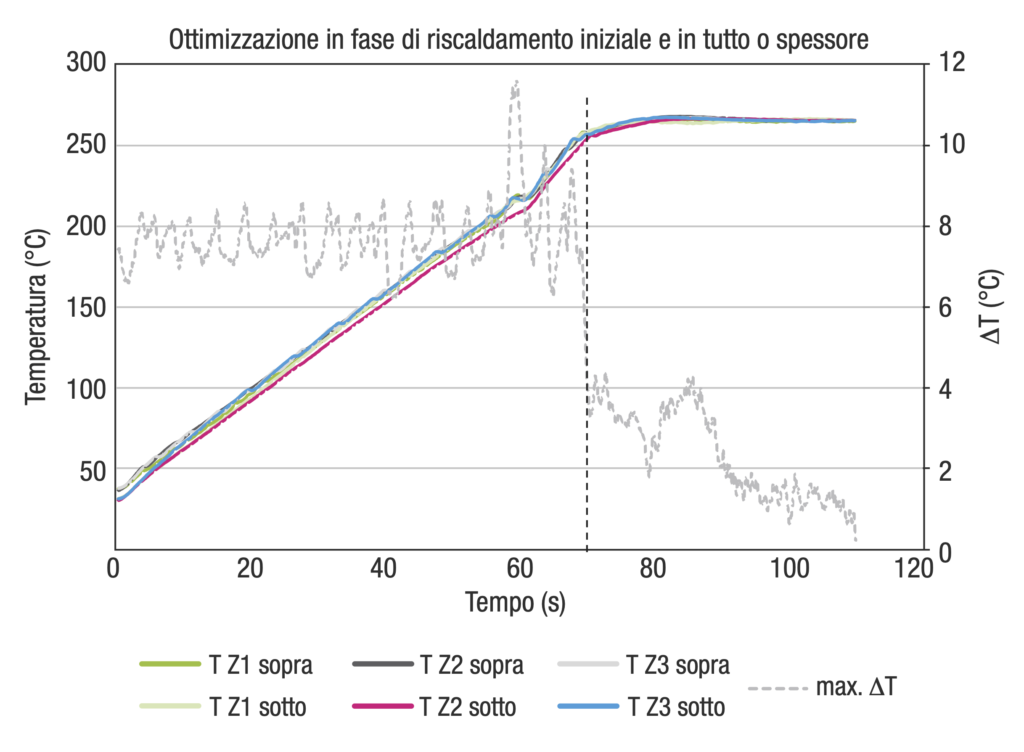
Se, ad esempio, il materiale, le dimensioni del semilavorato o lo spessore della lastra subiscono variazioni, è necessario reimpostare anche i parametri di regolazione per la fase di riscaldamento in profondità. Per un’ottimizzazione automatica dei parametri, è possibile effettuare un ciclo di misurazione separato. Ciò consente di ottenere informazioni sulle modifiche effettuate, sulla base delle quali i parametri di regolazione vengono poi ricalcolati e reimpostati. Il risultato consiste in un controllo di processo eccellente, come illustrato nella figura 5.

Riscaldamento di semilavorati di spessore diverso
L’immagine riportata in apertura raffigura l’isola di produzione completamente automatizzata allestita per fabbricare un componente strutturale per portiere (figura 6) costituito da tre lastre organiche di diverso spessore. I semilavorati spessi 1,0 e 2,5 millimetri vengono riscaldati insieme in un forno a infrarossi orizzontale (figura 7). In condizioni standard, la lastra organica più sottile si riscalderebbe molto più rapidamente di quella più spessa. La limitazione della differenza di temperatura massima consentita tra le zone di regolazione assicura tuttavia una curva di temperatura costante e uniforme. I due semilavorati raggiungono la temperatura impostata contemporaneamente. Per la lastra organica da 0,6 millimetri viene invece utilizzato un forno verticale con pannelli radianti installati su un solo lato. Qui, tutto dipende dalla rapidità della movimentazione a caldo, poiché il sottile semilavorato si raffredda molto velocemente. I tre semilavorati vengono quindi trasferiti tutti insieme nello stampo dove, entro un tempo di ciclo di 70 secondi, vengono processati dando origine a un manufatto composito concepito per garantire una distribuzione ottimale dei carichi.
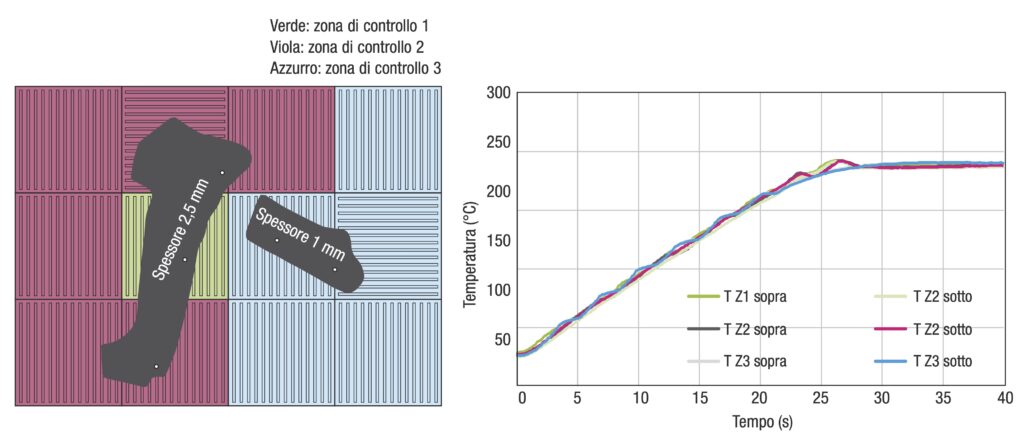
Una procedura digitalizzata
Lo studio riportato dimostra che la tecnologia di riscaldamento a raggi infrarossi, in combinazione con l’automazione, rappresenta la chiave per una lavorazione ottimale dei semilavorati in composito termoplastico. Strategie innovative per la regolazione del processo di riscaldamento consentono di ottenere un riscaldamento rapido e preciso, al fine di poter processare lastre organiche di spessori diversi in un unico passaggio. A tale scopo, durante la regolazione di precisione dei parametri, l’operatore può contare su procedure di ottimizzazione automatica. Il calcolo assistito da software di parametri di regolazione idonei garantisce temperature superficiali costanti in fase di riscaldamento. Eventuali interferenze esterne vengono automaticamente escluse prima che possano provocare deviazioni di processo critiche.
Bibliografia
1 G.W. Ehrenstein “Handbuch Kunststoff-Verbindungstechnik (Manuale di tecnologia dei compositi plastici)” Hanser, 2004, pag. 223