Le caratteristiche meccaniche finali di un materiale trasformato attraverso additive manufacturing sono influenzate da molti parametri e fattori, a partire dalla tecnologia di stampa. Una delle più utilizzate, grazie all’ampio ventaglio di soluzioni offerto dal mercato, al costo contenuto dei sistemi di stampa e alla semplicità di utilizzo, è la tecnologia FDM (Filament Deposition Modeling) o FFF (Free Filament Fabrication). In questo ambito, la numerosità di costruttori e produttori di materiali, le differenti architetture dei sistemi di stampa e i diversi software di slicing sono fattori che rendono difficile se non impossibile una standardizzazione della qualità di produzione. Materiali nominalmente uguali, trasformati attraverso processi nominalmente identici per realizzare lo stesso componente portano a risultati qualitativamente, esteticamente e meccanicamente anche molto differenti fra loro. È quanto è emerso dall’analisi dei dispositivi di protezione individuale realizzati da Makers4Parma, una rete di makers e professionisti di Parma e della Provincia – coordinata da Fablab Parma – nata lo scorso marzo per rispondere all’emergenza sanitaria legata alla pandemia da Covid-19.
L’osservazione è stata il pretesto per dare il via al Progetto Round-Robin for Additive Manufacturing (RRAM), finalizzato a quantificare, a parità di tipologia di materiale e parametri di stampa, le differenze nelle proprietà meccaniche di produzioni additive realizzate da diverse realtà. È appunto quest’ultimo aspetto l’originalità della sperimentazione, perché la letteratura finora esistente si riferisce esclusivamente a ricerche relative alle variazioni delle prestazioni di un materiale, stampato su una singola unità di produzione, in funzione dei parametri di processo. Non sono infatti disponibili studi che mettano a confronto diretto macchine e/o materiali di produttori diversi.
Analisi delle proprietà dei materiali
Le proprietà meccaniche (trazione, compressione, flessione…) dei materiali trasformati tramite processo FDM sono state oggetto di studio fin al 1996 [1] e da allora sono state analizzate per diversi polimeri e in relazione a specifici set di parametri di processo. I parametri/fattori che più influenzano le caratteristiche meccaniche di un prodotto per FDM, illustrati nella figura 1, sono numerosi e di molteplice natura.
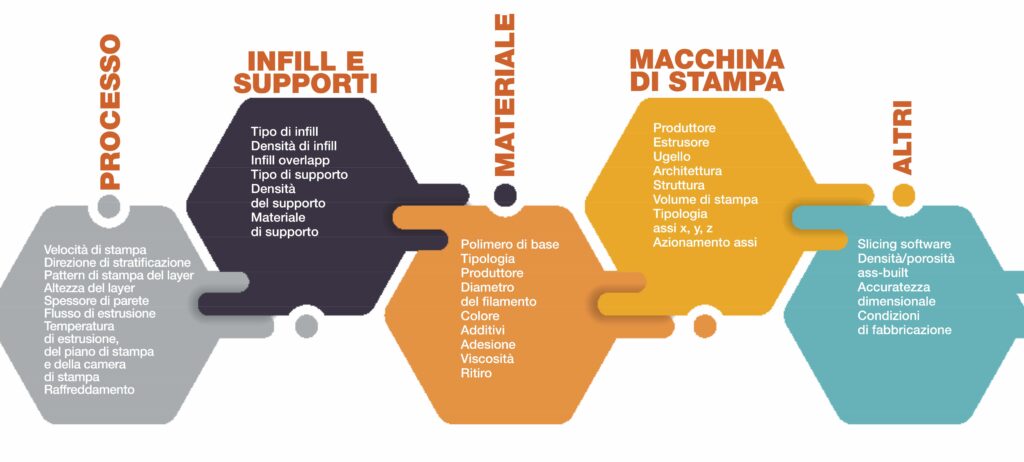
attraverso il processo FDMCiascuno di essi, in modi differenti, influisce sulle proprietà meccaniche risultanti: è noto, ad esempio, come l’orientazione e il pattern di stampa generino proprietà anisotrope nel materiale finale [2], mentre la presenza di gap ne riduca la resistenza [3], che è invece massimizzata da una minore altezza di layer e una minore larghezza di deposizione [4]. Ulteriori studi dimostrano che anche la colorazione del filamento esercita una certa influenza [5]. L’aspetto fondamentale che emerge dall’analisi della letteratura è che uno stesso materiale trasformato in massa (bulk material) o mediante additive possiede caratteristiche meccaniche differenti, non necessariamente le une maggiori delle altre, e che la meccanica di un polimero trasformato in modo additivo è completamente diversa da quella di un materiale in massa.
Le fasi della sperimentazione
Il primo round pilota del Progetto RRAM si è svolto tra luglio e settembre 2020, seguendo una procedura strutturata in cinque fasi: call-to-action, produzione, consegna, test e diffusione. La call-to-action, riservata ai membri della rete Makers4Parma, proponeva l’adesione spontanea al progetto, che consisteva nell’impegno a produrre almeno uno e fino a un massimo di cinque lotti di tre provini ciascuno, di geometria data e prestando attenzione a seguire accuratamente le istruzioni e i parametri di produzione.
Nella fase di produzione, sono stati condivisi con i partecipanti i file STL del provino e le istruzioni di produzione dettagliate. Il job di stampa consisteva in un batch di tre provini da prodursi con i parametri di stampa riportati nella tabella 1.
Parametro | Valore |
---|---|
Materiale | PLA |
Altezza layer | 0,2 mm |
Numero provini per job | 3 |
Numero pareti al contorno | 2 |
Numero layer top/bottom | 0 |
Infill overlap | 15% |
Pattern di stampa | lines/rectangular (±45°) |
Temperatura di stampa | 220 °C (costante) |
Temperatura del piano | 0-40 °C |
Velocità di stampa | 40 mm/s |
Adesione al piatto | Skirt o assente |
Orientazione | Sul piano XY, lungo Y |
Tabella 1 Parametri di stampa imposti nel Progetto RRAM per la produzione dei provini e orientamento dei provini sul piano di stampa (immagine in alto)
Relativamente al materiale da utilizzare, l’unico vincolo era l’impiego di PLA, senza restrizioni su produttore e colore. La consegna prevedeva una registrazione on-line del lotto, attraverso un form per la raccolta di informazioni specifiche del lotto, della macchina di stampa e del filamento di partenza. La registrazione assegnava un codice univoco anonimo al lotto e generava una lettera di consegna da accompagnare al lotto stesso.
L’esperimento ha coinvolto ventidue makers, di cui tredici hanno prodotto ventisei lotti per un totale di settantotto provini. Il campione sperimentale raccolto è rappresentativo di undici produttori di materia prima (3DJake, Amazon, Eolas, Filoalfa, Makerbot, Prusa Research, Raise3D, RS Components, Smart Material, Sunlu, Formfutura), nove colori (arancione, bianco, blu, ciano, giallo, grigio, nero, rosa, verde) e tre tipologie di filamento (FDA, neo, shiny e standard).
Per quanto riguarda le stampanti sono stati utilizzati undici modelli di sette costruttori (Anycubic/I3 Mega, Bq/Witbox 1, Creality/CR-10S, Creality/Ender 3, Creality/Ender 3 Pro, Geetech/I3 Pro B, Prusa/I3-MK2, Prusa/I3-MK3, Wasp/4070, 3DPR/Cubo), operanti a quattro diverse temperature del piano di stampa (ambiente, 40 °C, 50 °C e 60 °C), e tre differenti software di slicing (Cura, Prusa e Simplify 3D). Tutte le varianti rappresentate hanno carattere commerciale e non è stata considerata nessuna soluzione autoprodotta.
Il set up delle prove
Le proprietà meccaniche dei materiali trasformati sono state determinate attraverso prove di trazione condotte secondo lo standard ASTM D638 [6]. Le misure sono state effettuate su una macchina di trazione MaCh5 formato desktop (figura 2) prodotta da MaCh3D, capace di un carico massimo di 5 kN e una corsa complessiva di 110 millimetri.
2 Macchina di trazione MaCh5 per la determinazione delle proprietà meccaniche dei provini stampati in 3D
L’apparecchiatura sfrutta una forma proprietaria degli afferraggi che si accoppia alla forma dei provini, con il vantaggio di ridurre i tempi di realizzazione dei test, eliminare gli effetti degradanti delle ganasce tradizionali sul provino e minimizzare l’errore dell’operatore escludendo l’influenza di fattori soggettivi nella preparazione del test [7]. I carichi sono stati registrati con una cella di carico da 5kN (con accuratezza 5×10-3 N), mentre la deformazione del provino è stata misurata con un estensometro commerciale, con base di misura 50 millimetri, direttamente acquisito dal sistema MaCh3D.
Le prove di trazione sono state effettuate in controllo di spostamento, con una velocità di prova di 5 mm/min e una frequenza di campionamento di 5 Hz.
Variazione delle proprietà meccaniche del materiale
Ogni provino è stato sottoposto a test di trazione, generando le curve tensione-deformazione riportate nella figura 3. Da ogni grafico si sono ricavati i parametri meccanici del materiale: modulo elastico (E), tensione di scostamento dalla proporzionalità allo 0,2% (σp02), tensione massima (σmax), deformazione alla tensione massima (ε*), tensione di rottura (σf) e deformazione a rottura (εf). Per ciascun lotto di provini sono stati calcolati i valori medi e la deviazione standard di ogni proprietà. Nella tabella 2 sono riportati i valori medi, le deviazioni standard e la variabilità sull’intero esperimento, insieme ai valori del provino in PLA stampato a iniezione presi come riferimento.
Modulo di elasticità, E (MPa) | Sollecitazione scost. prop., σp02 (MPa) | Sollecitazione massima, σmax (MPa) | Deformazione alla σmax, ε* (mm/mm) | Sollecitazione a rottura, σf (MPa) | Deformazione a rottura, εf (mm/mm) | |
---|---|---|---|---|---|---|
Valori di riferimento (1) | 3.500,00 | 70 | 60 | - | 60 | 0,07 |
Valore medio | 2.428,90 | 35,8 | 40,8 | 0,0284 | 38,6 | 0,0412 |
Massimo | 3.521,80 | 53,1 | 54,2 | 0,0904 | 50,6 | 0,0903 |
Minimo | 997,8 | 10,5 | 13,2 | 0,0158 | 12,7 | 0,0161 |
Deviazione std | 874,8 | 13,3 | 11 | 0,0187 | 9,7 | 0,0238 |
Variabilità (CV%) | 36,00% | 37,20% | 27,00% | 65,80% | 25,00% | 57,90% |
Tabella 2 Proprietà meccaniche determinate sperimentalmente nel corso del Progetto RRAM
L’analisi dei risultati rivela che i campioni ottenuti attraverso un processo additivo di tipo FDM, a partire da filamenti in PLA di diversi produttori e diversi sistemi di stampa, mostrano proprietà meccaniche molto disperse e in generale inferiori rispetto a quelle del provino stampato a iniezione [8]. Modulo elastico e tensione di scostamento dalla proporzionalità presentano una dispersione attorno al 35%, valore che si riduce a circa il 25% per la sollecitazione massima.
I dati di allungamento, invece, sono notevolmente dispersi, con variabilità anche superiore al 60%. La ripetibilità all’interno di ogni singolo lotto è decisamente migliore, e solo in pochi casi la variabilità supera il 5% sui parametri di elasticità e di sollecitazione.
Correlazione tra proprietà meccaniche e peso del provino
Le curve tensione-deformazione (figura 3a), analogamente disperse, permettono di individuare una regione del piano tensione-deformazione (σ, ε) nella quale si collocano le risposte meccaniche dei provini, quindi identificative del comportamento del PLA (figura 3b).
3 Curve tensione-deformazione delle prove di trazione: grafico cumulativo di tutti i provini testati (a) e definizione di regioni di risposta meccanica del PLA (b)
Dai risultati si distinguono due eccezioni. La prima si riferisce all’unico lotto relativo a un materiale con colorazione “shiny” (ID N20-218), per il quale si evidenzia una curva tensione-deformazione leggermente al di sotto della regione principale, mostrando una maggiore elasticità e una maggiore tenacità del materiale, caratteristiche potenzialmente indotte dalla colorazione. La seconda eccezione è invece legata a filamenti di diversi produttori trasformati con la stessa macchina di stampa (lotti ID J9-81, K8-80 e L7-80); la regione tensione-deformazione individuata da questi materiali è molto schiacciata e notevolmente inferiore alla regione principale. Dall’analisi dei pesi di questi provini emerge un minor peso rispetto alle medie, indicativo di una sotto-estrusione nel processo FDM, che quindi è causa di proprietà meccaniche notevolmente inferiori.
Le proprietà meccaniche dei singoli lotti sono state confrontate due a due, individuando una proporzionalità tra modulo elastico (E), tensione di scostamento dalla proporzionalità allo 0,2% (σp02) e tensione di rottura (εf), e la tensione massima (σmax); in particolare la proporzione tra σp02 e σmax è costante, pari a 0,96 (figura 4).
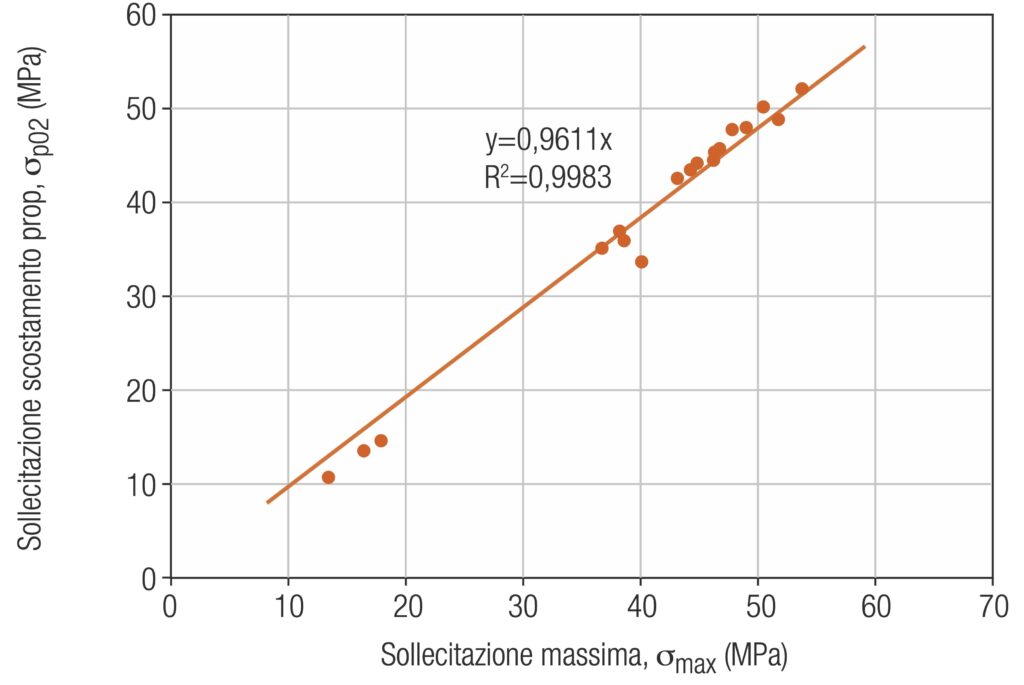
Dal confronto tra le proprietà meccaniche e il peso del provino si osserva una correlazione di natura esponenziale (figura 5).
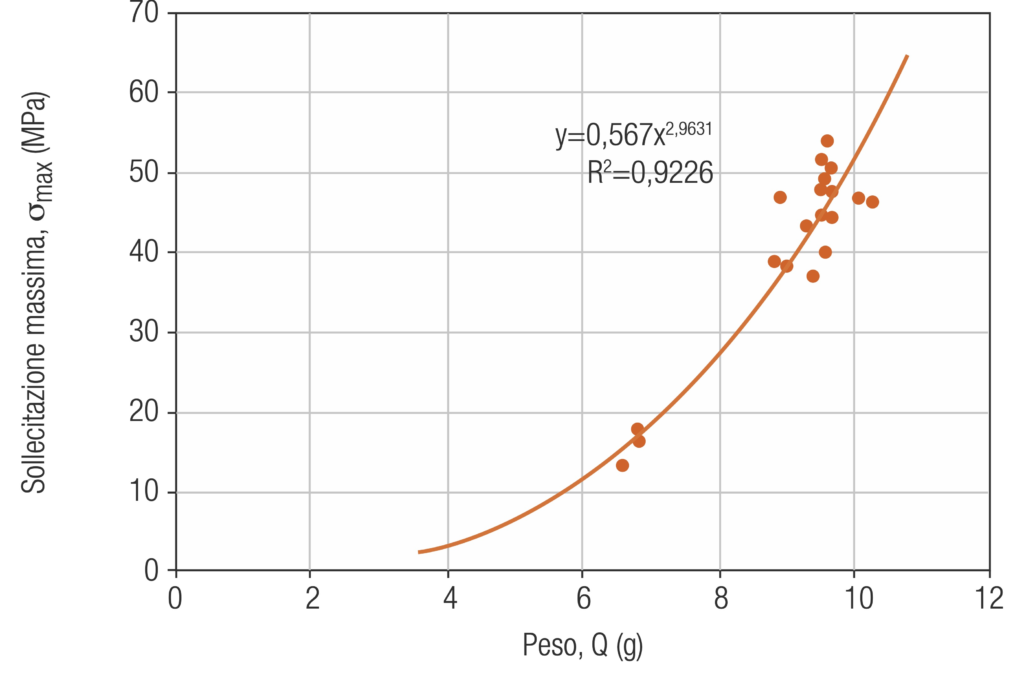
Attraverso un fattore U – definito coefficiente di estrusione – pari al rapporto tra peso effettivo e peso nominale del componente è possibile stimare le proprietà meccaniche reali del materiale stampato a partire da quelle nominali del materiale additivo. Il parametro U è quindi adatto per valutare in via preliminare la qualità meccanica dei materiali trasformati.
Un valido indicatore
Il primo esperimento pilota del Progetto RRAM ha evidenziato una notevole influenza del grado del filamento e del sistema di stampa sulle proprietà meccaniche di un provino in PLA prodotto attraverso tecnologia FDM. Da processi nominalmente identici si possono ottenere proprietà meccaniche molto differenti, con variazioni anche superiori a ±30%. Un valido indicatore per una prima stima della qualità meccanica di un componente stampato è il rapporto tra peso effettivo e peso nominale.
La buona partecipazione all’esperimento, in relazione all’estensione e ai tempi di apertura della call-to-action, dimostra l’interesse verso il reperimento di informazioni sulle proprietà meccaniche dei materiali trasformati mediante additive manufacturing da parte dei professionisti come dei makers, che in entrambi i casi hanno sottolineato anche difficoltà di accesso a dati attendibili.
Bibliografia
1 E. Fodran et al, International Solid Freeform Fabrication Symposium, 1996
2 I. Durgun e R. Ertan, Rapid Prototyping Journal, 20(3), 228-235, 2014
3 G. C. Onwubolu G e F. Rayegani, Journal of Manufacturing Engineering, November 2014
4 S. Ahn et al, Rapid Prototyping Journal, 8, 248-257, 2002
5 B. Wittbrodt e J.M. Pearce, Additive Manufacturing, 8 110-116, 2015
6 ASTM D638-14 2014 Standard Test Method for Tensile Properties of Plastics (West Conshohocken, PA: ASTM International)
7 L. Bergonzi et al, Procedia Structural Integrity, 12, 392-403, 2018
8 S. Farah et al, Advanced Drug Delivery Reviews, 107, 367-392, 2016