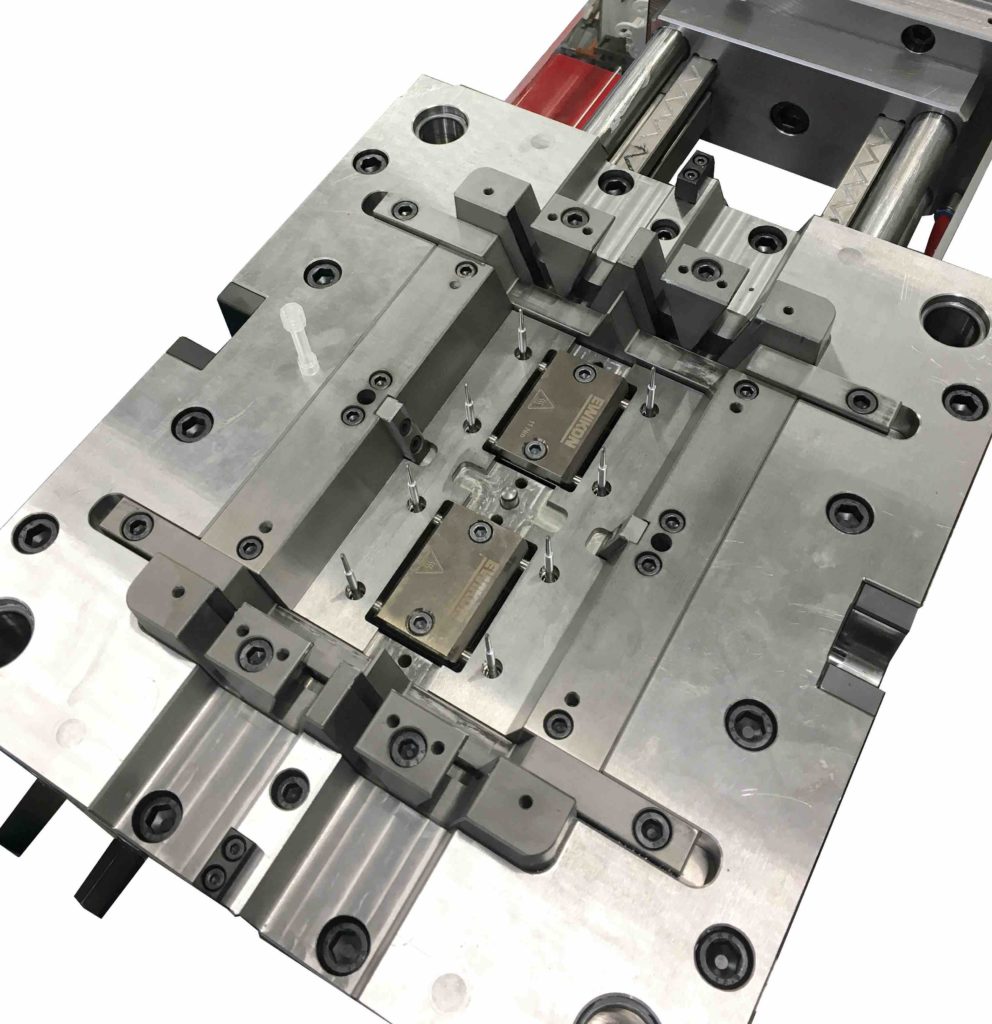
La semplicità è un valore da perseguire, nella vita come in fabbrica, ma non sempre è la strada più efficiente ed economica per raggiungere un obiettivo. Lo dimostra il caso di Euroteck di Pratola Peligna (Aquila), società attiva nello stampaggio a iniezione, alle prese con il passaggio di scala, da pochi pezzi a una produzione di serie, nella realizzazione di un nuovo connettore medicale dotato di attacco luer in policarbonato.
Da quattro a otto cavità
L’azienda aveva iniziato a produrre i connettori su uno stampo a quattro cavità alimentato a canale freddo, scontrandosi con la limitata produttività dovuta allo sfrido, consistente e non totalmente recuperabile, al tempo ciclo elevato e alla necessità di separare manualmente i prodotti dalla carota fredda.
Euroteck si è quindi rivolta a Paoltroni Stampi, con sede a Potenza Picena (Ancona), puntando a superare i limiti dello stampo utilizzato fino a quel momento, con l’obiettivo di eliminare le inefficienze e ridurre i costi unitari. Lo studio di fattibilità condotto a quattro mani ha portato a definire una nuova configurazione a otto cavità, con iniezione diretta del pezzo, con cui stampare componenti di migliore qualità in un tempo ciclo intorno a 20 secondi.
Passate da due a tre, le aziende coinvolte nel progetto si sono trovate ad affrontare un intenso lavoro di preparazione, dovendo valutare diverse configurazioni dello stampo e condurre test sul materiale per validare la qualità del punto di iniezione.
Integrazione funzionale nello stampo
Un rapporto molto stretto si è instaurato tra stampista e fornitore di canali caldi. «Per poter raggiungere le massime prestazioni, abbiamo deciso di acquistare da Ewikon il pacchetto completo di piastre e centralina di controllo temperatura» nota Lois Paoltroni, titolare di Paoltroni Stampi.
«La complessità dello stampo, con la formatura del pezzo principalmente su carrelli, ha richiesto una progettazione delle piastre specifica, che abbiamo risolto integrando funzioni stampo nella piastra porta ugelli. Su nostre indicazioni, Ewikon ha prodotto in maniera precisa la piastra, per permettere il supporto dei carrelli in modo ottimale».
Il canale caldo a otto punti di iniezione è composto da due ugelli per iniezione laterale diretta HPS III-MHL 100, ognuno equipaggiato con quattro puntali sostituibili in macchina. Soluzione standard per questa linea di prodotti – spiega Ewikon –, il distributore a due punti di iniezione sfrutta una tecnologia a elementi con canali dal flusso ottimizzato, cruciale per garantire un perfetto bilanciamento ed eliminare zone di stress e ristagno, che potrebbero danneggiare il fuso. Grazie a un’accurata progettazione, si è riusciti a limitare la caduta di pressione, mantenendo un tempo minimo di permanenza del materiale in camera. Questa soluzione a iniezione laterale diretta, in continua evoluzione dal suo lancio nel 2007, rappresenta lo stato dell’arte nelle applicazioni multicavità, diffuse ormai in ogni settore dello stampaggio a iniezione. L’ampia gamma di soluzioni disponibile consente di integrare senza difficoltà l’iniezione diretta in stampi da una a oltre 128 impronte, applicabili nella lavorazione di poliolefine, quando di tecnopolimeri caricati.
Infine, per assicurare prestazioni costanti e al massimo livello, è stata montata la nuova centralina di controllo della temperatura a sei zone proControl, dotata di touch-screen da 7”, facilmente integrabile nei moderni sistemi di produzione automatica grazie alle numerose interfacce disponibili. L’interfaccia utente è moderna, intuitiva e in lingua italiana.
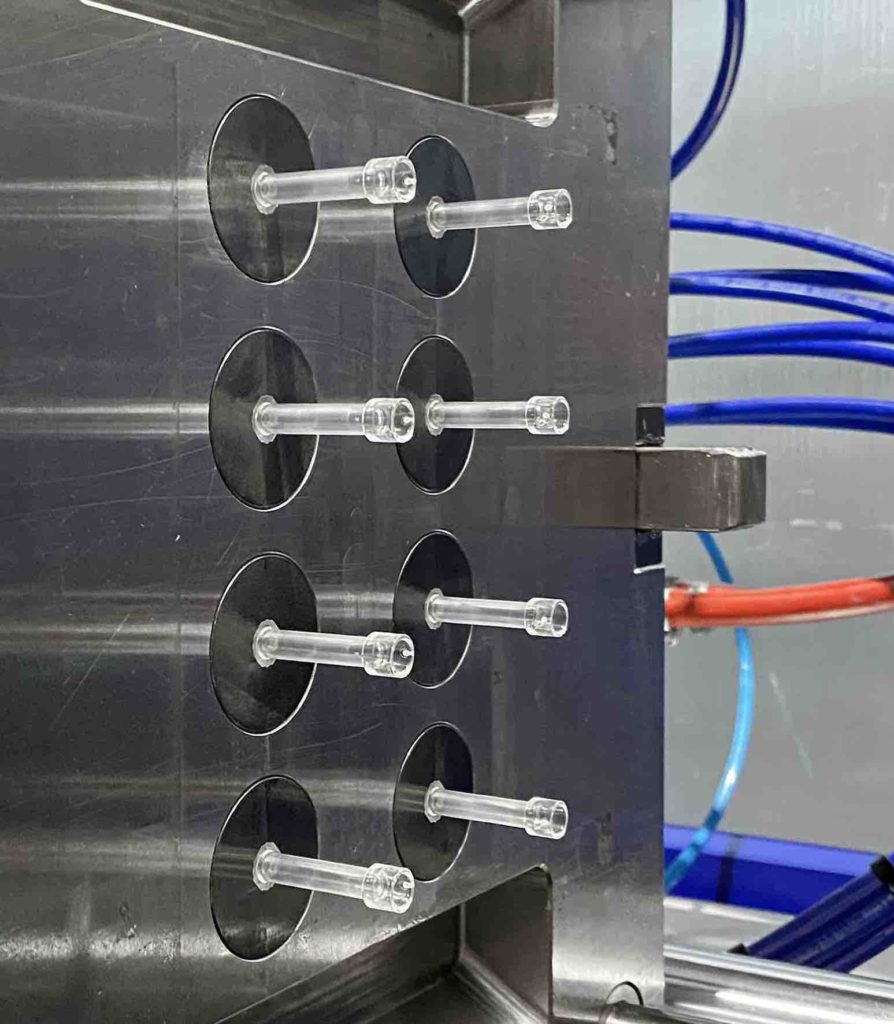
Stampo testato e approvato
La dinamica di funzionamento articolata dello stampo è gestita da due attuatori pneumatici posizionati nella parte alta. Completata l’iniezione, un attuatore libera i maschi sulla parte fissa, prima dell’apertura dello stampo, in modo da evitare trattenute e difettosità sul pezzo. Durante l’apertura dello stampo, i carrelli svincolano il pezzo, che rimane trattenuto dal maschio. Quest’ultimo, durante la corsa di apertura, viene ruotato dal secondo attuatore pneumatico per svincolare il filetto dell’attacco luer. Una volta raggiunta la posizione finale, si può procedere con l’estrazione. Tutti i movimenti sono assicurati da sensori di posizione per impedire danni accidentali dovuti a un’errata sequenza di movimento, per semplificare la produzione automatica.
Completato in modo agevole l’assemblaggio del complesso stampo, il primo test si è concluso con un risultato superiore alle aspettative: «Abbiamo riempito il canale caldo velocemente, passando direttamente alla pre-produzione in pochi minuti, già al primissimo collaudo dello stampo» commenta soddisfatto Pizzola. «Tutti gli obiettivi del progetto sono stati raggiunti: la qualità del manufatto stampato è migliorata, abbiamo eliminato gli sfridi e il tempo di ciclo si è mantenuto entro i 20 secondi; inoltre, i pezzi ora vengono inviati direttamente al cliente, senza bisogno di essere ulteriormente manipolati».
Senza anomalie
Lo stampo è in produzione dalla fine dell’anno scorso e, ad oggi, non sono state riscontrate anomalie. Tanto che l’AD di Euroteck sta già guardando avanti. «Con Paoltroni Stampi ed Ewikon stiamo già studiando nuove applicazioni, con l’obiettivo di iniettare direttamente materiali più complessi». Pizzola ha le idee chiare anche in tema di Industria 4.0: «Lo stampaggio medicale deve puntare alla massima automazione e al controllo del processo, evitando quanto più possibile il ricorso a post-lavorazioni, dato l’elevato grado di pulizia richiesto» sottolinea. «Per la stessa ragione abbiamo investito molti anni fa nel controllo di processo, installando un software MES, che si sposa perfettamente con il sistema di controllo processo smartControl di Ewikon».